- お役立ち記事
- The basics of why-why analysis and how to use it for effective problem solving
月間76,176名の
製造業ご担当者様が閲覧しています*
*2025年3月31日現在のGoogle Analyticsのデータより
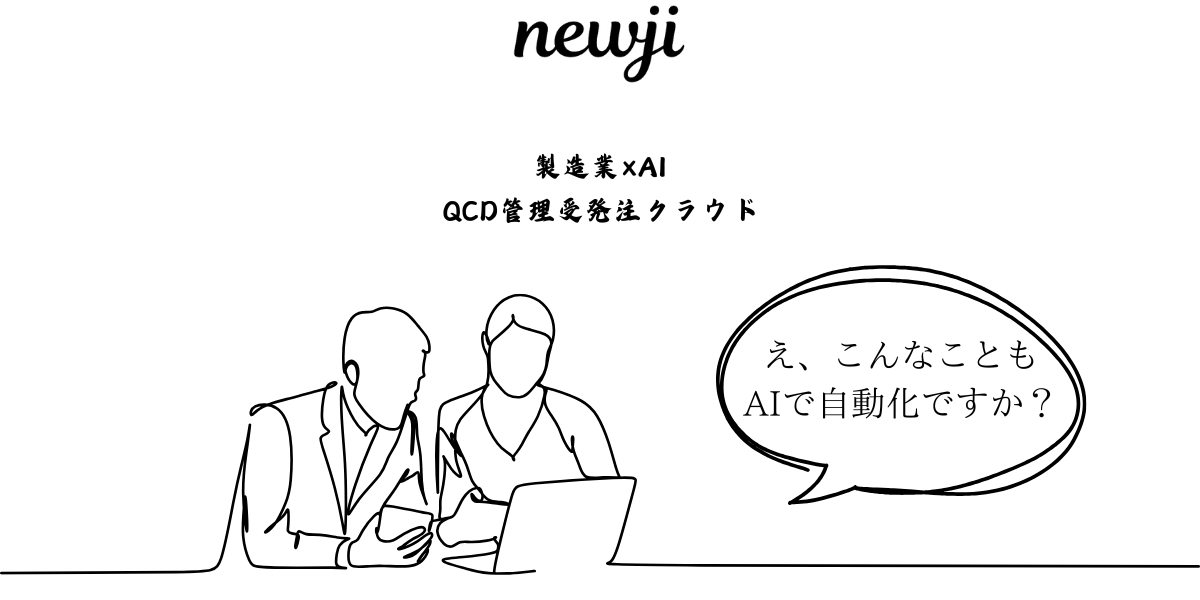
The basics of why-why analysis and how to use it for effective problem solving
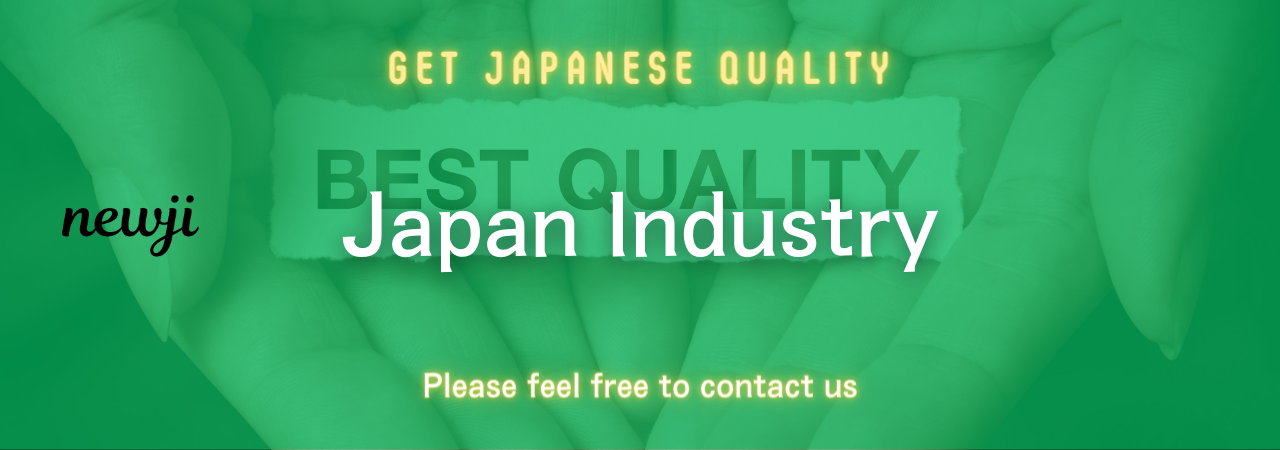
目次
Understanding Why-Why Analysis
Why-why analysis, also known as the five whys, is a problem-solving technique designed to delve into the core of an issue.
By repeatedly asking “why,” you can explore various levels of a problem, which often leads to identifying the root cause.
This method can be highly effective in different contexts, from manufacturing to daily life scenarios.
This technique encourages critical thinking and problem solving at a foundational level.
It’s simple, intuitive, and does not require any advanced tools or training, making it accessible for everyone.
At its best, it fosters a culture of curiosity and continuous improvement, crucial for personal development and organizational growth.
The Origin and Purpose of Why-Why Analysis
The why-why analysis technique was developed by Sakichi Toyoda, an industrialist, inventor, and founder of Toyota Industries.
He believed it was essential not just to fix problems superficially but to dig deep and address the cause.
This approach is vital because addressing only the symptoms of a problem means it can, and often will, reoccur.
By getting to the root cause, you can devise strategies to eliminate it entirely or reduce its impact significantly.
Steps to Conduct a Why-Why Analysis
Step 1: Define the Problem
The first step is to clearly define the problem you wish to analyze.
Be as precise as possible.
For example, instead of saying “the machine stopped working,” specify which machine and describe the exact issue and context.
Step 2: Ask the First ‘Why’
Ask yourself, “Why did this happen?”
The answer should provide an initial layer of understanding regarding the issue.
It’s the starting point of your investigation into potential causes.
Step 3: Ask Subsequent ‘Whys’
For each answer provided, continue asking “why” until you reach a conclusion that no longer offers a reasonable answer.
These are usually called the “Five Whys,” although it might take more or fewer than five times to uncover the true cause.
Each response should become more refined and reveal more detail.
Step 4: Understand the Root Cause
Once you’ve reached an answer that leads to no further ‘whys,’ you’ve likely identified a root cause.
It’s important to verify that this cause is actionable; meaning you can take steps to resolve it.
Step 5: Document and Address the Root Cause
Document the analysis and work on implementing solutions that tackle the root cause.
Develop clear strategies that will help prevent the problem from recurring in the future.
Tips for Effective Why-Why Analysis
Be Honest and Objective
This process requires honesty.
Only with unbiased evaluation can true causes be found.
Avoid the temptation to settle for answers that confirm existing beliefs.
Involve a Team
Gather a diverse team to help with the analysis process.
Different perspectives can provide fresh insights and help challenge assumptions, thereby uncovering the root cause more effectively.
Clarify Each Question and Answer
Ensure each “why” and its respective answer are clear and concise.
Vague responses can lead to further confusion and inhibit finding the true cause.
Advantages of Why-Why Analysis
Simplicity and Ease of Use
Why-why analysis is straightforward, which means there’s no need for special equipment or training.
This makes it easy for anyone within an organization to apply.
Uncovers Root Causes
This technique is well-regarded for its ability to identify root causes, which is essential for developing long-term solutions to persistent problems.
Encourages Critical Thinking
It promotes a culture of inquiry and critical thinking by motivating individuals to not accept superficial explanations.
Potential Drawbacks
Misleading Simplicity
While it seems simple, the effectiveness of why-why analysis heavily relies on the knowledge and skill of those conducting it.
Without a deep understanding of the processes involved, people might not reach the true root cause.
Assumptions and Bias
If the analysis is performed with preconceived notions or biases, it might lead to incorrect conclusions.
It’s important to approach this exercise with an open mind.
Conclusion
Why-why analysis is a powerful tool for problem-solving that provides a pathway to uncovering the genuine causes behind recurring issues.
It requires a critical mindset, willingness to explore deeply, and honesty to ensure success.
By continuously engaging with this inquiry-based approach, individuals and organizations can identify underlying issues and implement lasting solutions, significantly enhancing efficiency and preventing future obstacles.
資料ダウンロード
QCD管理受発注クラウド「newji」は、受発注部門で必要なQCD管理全てを備えた、現場特化型兼クラウド型の今世紀最高の受発注管理システムとなります。
ユーザー登録
受発注業務の効率化だけでなく、システムを導入することで、コスト削減や製品・資材のステータス可視化のほか、属人化していた受発注情報の共有化による内部不正防止や統制にも役立ちます。
NEWJI DX
製造業に特化したデジタルトランスフォーメーション(DX)の実現を目指す請負開発型のコンサルティングサービスです。AI、iPaaS、および先端の技術を駆使して、製造プロセスの効率化、業務効率化、チームワーク強化、コスト削減、品質向上を実現します。このサービスは、製造業の課題を深く理解し、それに対する最適なデジタルソリューションを提供することで、企業が持続的な成長とイノベーションを達成できるようサポートします。
製造業ニュース解説
製造業、主に購買・調達部門にお勤めの方々に向けた情報を配信しております。
新任の方やベテランの方、管理職を対象とした幅広いコンテンツをご用意しております。
お問い合わせ
コストダウンが利益に直結する術だと理解していても、なかなか前に進めることができない状況。そんな時は、newjiのコストダウン自動化機能で大きく利益貢献しよう!
(β版非公開)