- お役立ち記事
- The basics of “why why analysis” using logical thinking and points to prevent recurrence of defects
The basics of “why why analysis” using logical thinking and points to prevent recurrence of defects
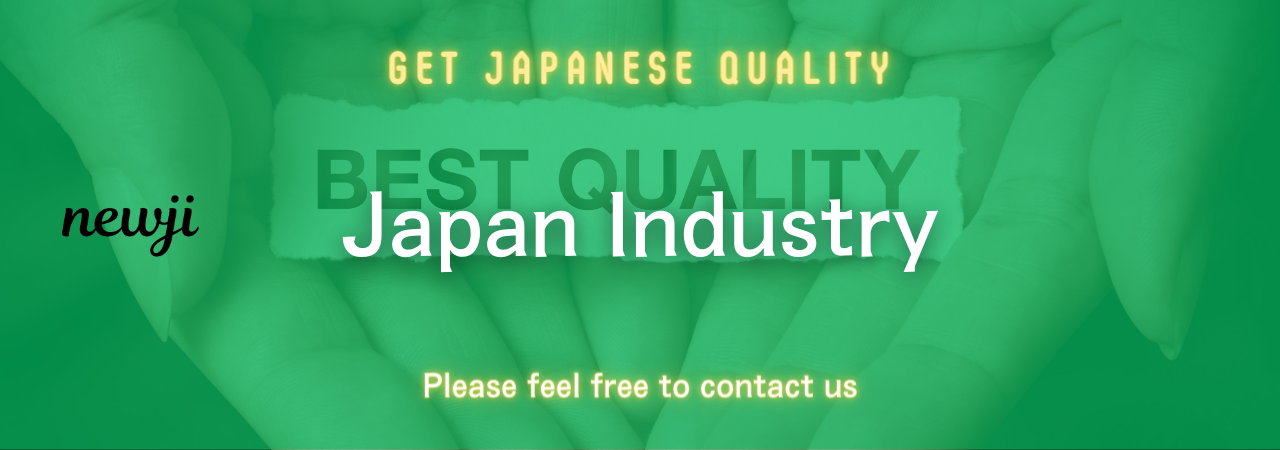
目次
Understanding Why Why Analysis
Why Why Analysis is a simple yet powerful method used to identify the root causes of a problem.
This technique involves repeatedly asking the question “why” to uncover the underlying issues contributing to a defect or problem.
It encourages logical thinking and helps organizations prevent the recurrence of defects by addressing issues at their core.
Originating from the manufacturing sector, Why Why Analysis has since found application in various industries, including healthcare, software development, and service sectors.
The ultimate goal is not just to solve the surface-level problem but to implement solutions that will prevent it from happening again.
The Importance of Root Cause Analysis
Root causes are the fundamental reasons behind a problem.
Addressing these issues ensures that a problem doesn’t recur, leading to more sustainable and efficient operations.
By dedicating time to understanding why an issue has arisen, organizations can devise ways to prevent its recurrence, thus saving resources and improving service quality.
Using logical thinking is crucial during this analysis as it helps in systematically moving from one stage to the next, ensuring that nothing is overlooked.
Every “why” asked should be meaningful and lead to a plausible answer or further questioning, gradually paving the way to the root cause.
How to Conduct a Why Why Analysis
Conducting a successful Why Why Analysis involves a systematic approach.
Here’s a step-by-step guide:
Step 1: Define the Problem Clearly
Understanding and defining the issue properly is the first step.
Avoid vague statements and ensure that the problem is expressed in specific terms.
For example, instead of saying “the system is crashing,” specify when it crashes, how often, and any other details that are known.
Step 2: Ask the First “Why”
Begin by asking why the problem is occurring.
It’s important to rely on actual data and observations instead of assumptions.
Ensure that each answer is based on factual evidence.
Step 3: Keep Asking “Why”
Continue asking “why” until the root cause is identified.
Typically, it takes about five iterations, but this can vary depending on the complexity of the issue.
Each “why” should bring the team closer to understanding the underlying cause.
Step 4: Identify the Root Cause
Once you have drilled down to the root cause, it should be clear that addressing this issue will prevent the defect from recurring.
The root cause should be actionable and within the organization’s control to change or mitigate.
Step 5: Develop Corrective Measures
With the root cause identified, it’s time to devise strategies to address it.
This can involve changes in processes, employee training, policy modifications, or new technology implementations.
The focus should be on solutions that will have a lasting impact.
Points to Prevent Recurrence of Defects
Even post-analysis, there are essential considerations to ensure solutions are effective over the long term.
Implementing Effective Solutions
Ensure that solutions are thoroughly documented and communicated to all relevant stakeholders.
This might involve developing new procedures, updating manuals, or creating new training materials.
The key is to ensure that everyone understands not only what changes are being made but also why these changes are necessary.
Monitoring and Feedback
After implementation, regular monitoring is crucial to ensure the solutions are working as intended.
Gather feedback from employees and analyze any new data that arises.
It is essential to remain vigilant and ready to tweak the solution if any issues are observed.
Cultivate a Culture of Continuous Improvement
Why Why Analysis should not be seen as a one-time fix, but rather as part of a broader commitment to continuous improvement.
Establishing a learning culture where employees are encouraged to report and analyze problems can pave the way for future innovation and efficiency.
Challenges and Overcoming Them
While Why Why Analysis is straightforward, there can be challenges.
Avoiding Assumptions
Always base “why” questions on facts rather than assumptions.
Making assumptions can steer the analysis off course, leading to incorrect conclusions.
Stopping Too Soon
Sometimes teams might stop asking “why” too early, resulting in only treating symptoms rather than the root cause.
Persevere until the actual reason behind the problem is uncovered.
Actionability of Root Causes
Ensure that the root causes identified are within reach.
If the analysis points to issues beyond the organization’s control, you may need to reevaluate and identify a more actionable cause.
Conclusion
Why Why Analysis is a potent tool for problem-solving and defect prevention.
By fostering logical thinking and encouraging a deep dive into issues, organizations can identify sustainable solutions that contribute to long-term stability and efficiency.
Embracing this method as part of a broader strategy of continuous improvement can lead to a more proactive and resilient organization.
資料ダウンロード
QCD調達購買管理クラウド「newji」は、調達購買部門で必要なQCD管理全てを備えた、現場特化型兼クラウド型の今世紀最高の購買管理システムとなります。
ユーザー登録
調達購買業務の効率化だけでなく、システムを導入することで、コスト削減や製品・資材のステータス可視化のほか、属人化していた購買情報の共有化による内部不正防止や統制にも役立ちます。
NEWJI DX
製造業に特化したデジタルトランスフォーメーション(DX)の実現を目指す請負開発型のコンサルティングサービスです。AI、iPaaS、および先端の技術を駆使して、製造プロセスの効率化、業務効率化、チームワーク強化、コスト削減、品質向上を実現します。このサービスは、製造業の課題を深く理解し、それに対する最適なデジタルソリューションを提供することで、企業が持続的な成長とイノベーションを達成できるようサポートします。
オンライン講座
製造業、主に購買・調達部門にお勤めの方々に向けた情報を配信しております。
新任の方やベテランの方、管理職を対象とした幅広いコンテンツをご用意しております。
お問い合わせ
コストダウンが利益に直結する術だと理解していても、なかなか前に進めることができない状況。そんな時は、newjiのコストダウン自動化機能で大きく利益貢献しよう!
(Β版非公開)