- お役立ち記事
- The cost reduction effect and realization process that parts standardization has on the manufacturing industry
月間76,176名の
製造業ご担当者様が閲覧しています*
*2025年3月31日現在のGoogle Analyticsのデータより
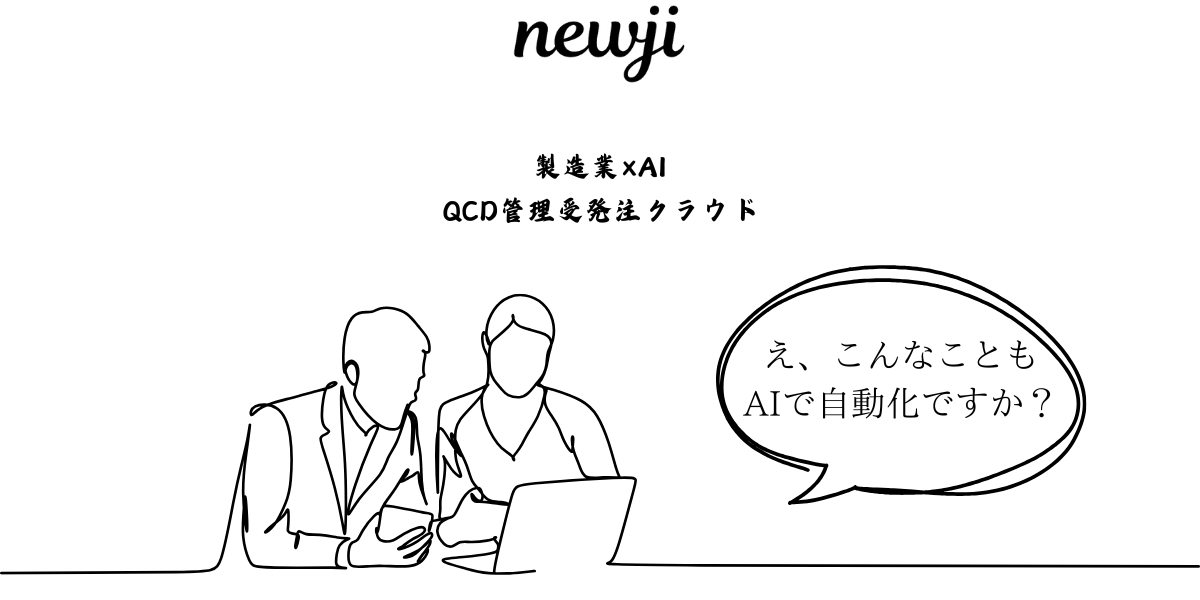
The cost reduction effect and realization process that parts standardization has on the manufacturing industry
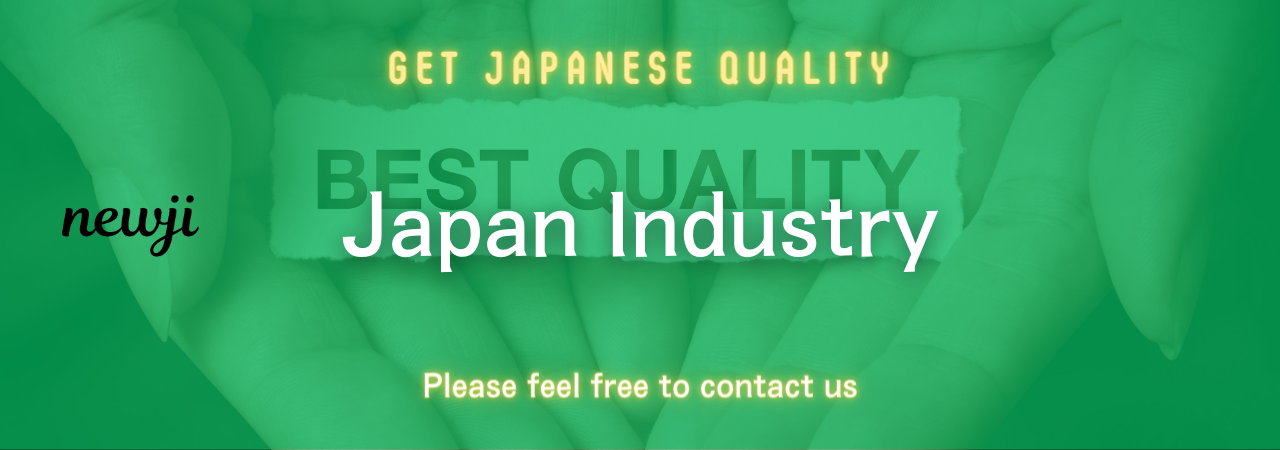
目次
Understanding Parts Standardization
Parts standardization in the manufacturing industry refers to the practice of using uniform and interchangeable components across different products.
This strategy streamlines the production process, ensuring consistency and compatibility.
By adopting standardized parts, manufacturers can significantly reduce costs and improve efficiency across various stages of production.
Why Standardize Parts?
The first and most compelling reason to standardize parts is cost reduction.
When manufacturers use standardized components, they can order in bulk, which often leads to discounts and reduced purchase prices.
Moreover, it minimizes the complexity of inventory management.
Fewer unique parts mean less time and resources spent on tracking and storing these components.
Additionally, standardization can accelerate production times.
With a set range of parts, assembly processes become more predictable and less prone to error, thus increasing overall production speed.
This uniformity also facilitates easier training for employees, as they deal with familiar components daily, decreasing the learning curve and boosting productivity.
Standardization not only aids the production line but also enhances product quality.
Consistency in parts results in consistent product performance, which leads to higher customer satisfaction and fewer returns.
Moreover, standardized parts simplify the repair and maintenance processes, as replacements are more readily available and fit without additional modifications.
The Cost Reduction Benefits of Parts Standardization
Cost savings from parts standardization are realized through multiple channels.
Bulk ordering reduces the per-unit cost of components, leading to direct savings.
Furthermore, storage and handling costs decrease, as inventory becomes more streamlined.
This efficiency reduces the need for extensive storage facilities and lowers overhead costs associated with inventory management.
Transportation costs also benefit from standardization.
Fewer unique parts mean shipments can be consolidated, leading to fewer deliveries and lower transportation fees.
This consolidation not only reduces costs but also minimizes the environmental impact of transportation.
On the production floor, fewer errors and less rework result in cost savings.
Standardized components reduce the likelihood of assembly mistakes, as the parts fit exactly as intended.
This precision lowers the incidence of defects and associated costs, such as re-manufacturing and waste disposal.
Ultimately, the cumulative effect of these cost savings enhances the competitive advantage of manufacturers.
Lower production costs translate to more competitive pricing and improved profitability, enabling businesses to thrive in a competitive industry.
Implementing Parts Standardization in Manufacturing
The process of implementing parts standardization involves a series of strategic steps aimed at optimizing production processes.
First, it is essential to conduct a thorough review of current products and components.
Identifying parts that can be standardized without compromising product functionality or quality is crucial.
Once suitable parts are identified, manufacturers should analyze supply chains for potential adjustments.
Establishing partnerships with suppliers who offer standardized parts can ensure a smooth transition.
This collaboration is vital for maintaining quality and ensuring the consistent availability of parts.
Design teams also play a significant role in parts standardization.
Engineers should revamp product designs to accommodate standardized components.
This redesign often involves innovative thinking to maintain product uniqueness while integrating interchangeable parts.
Communication across departments is vital during the implementation phase.
Manufacturers should ensure that every team, from purchasing to assembly, is on board with the new standardization strategy.
This alignment ensures a cohesive transition and maximizes the benefits of standardization.
Testing is another crucial step in the process.
Manufacturers must rigorously test new standardized parts within their production lines to identify potential issues.
Resolving these issues early ensures a smoother transition and helps in maintaining product quality.
Overcoming Challenges in Standardization
While the benefits are substantial, parts standardization poses its challenges.
The initial shift can be resource-intensive, requiring investment in redesign and retraining efforts.
Manufacturers might face resistance from teams accustomed to long-standing practices, emphasizing the need for effective change management strategies.
Balancing standardization with innovation can also be challenging.
Manufacturers must ensure that standardization does not stifle product differentiation or technological advancement.
Therefore, flexibility within standardization is key, allowing for adjustments when necessary to stay competitive.
Additionally, there might be hesitance from suppliers regarding altering existing contracts or processes.
Building strong relationships and clear communication with suppliers is essential to navigating these obstacles successfully.
The Future of Parts Standardization
With the rapid advancement of technology, parts standardization in manufacturing is poised to evolve further.
Automation and artificial intelligence can enhance standardization efforts by optimizing production processes and managing inventory with minimal human intervention.
Real-time data analytics allows manufacturers to identify further areas for standardization, driving additional cost savings.
Furthermore, the trend towards globalization in supply chains will press manufacturers to adopt increasingly standardized parts to maintain competitiveness.
Global standardization helps ensure that parts are readily available worldwide, aiding in seamless international operations.
In summary, parts standardization is a powerful strategy for cost reduction and operational efficiency in the manufacturing industry.
While it requires careful planning and execution, the rewards far outweigh the initial investment.
Manufacturers that embrace this approach stand to benefit from significant cost savings, improved product quality, and enhanced competitiveness in a rapidly evolving market.
資料ダウンロード
QCD管理受発注クラウド「newji」は、受発注部門で必要なQCD管理全てを備えた、現場特化型兼クラウド型の今世紀最高の受発注管理システムとなります。
ユーザー登録
受発注業務の効率化だけでなく、システムを導入することで、コスト削減や製品・資材のステータス可視化のほか、属人化していた受発注情報の共有化による内部不正防止や統制にも役立ちます。
NEWJI DX
製造業に特化したデジタルトランスフォーメーション(DX)の実現を目指す請負開発型のコンサルティングサービスです。AI、iPaaS、および先端の技術を駆使して、製造プロセスの効率化、業務効率化、チームワーク強化、コスト削減、品質向上を実現します。このサービスは、製造業の課題を深く理解し、それに対する最適なデジタルソリューションを提供することで、企業が持続的な成長とイノベーションを達成できるようサポートします。
製造業ニュース解説
製造業、主に購買・調達部門にお勤めの方々に向けた情報を配信しております。
新任の方やベテランの方、管理職を対象とした幅広いコンテンツをご用意しております。
お問い合わせ
コストダウンが利益に直結する術だと理解していても、なかなか前に進めることができない状況。そんな時は、newjiのコストダウン自動化機能で大きく利益貢献しよう!
(β版非公開)