- お役立ち記事
- The cutting edge of composite materials and new materials that R&D leaders should know about
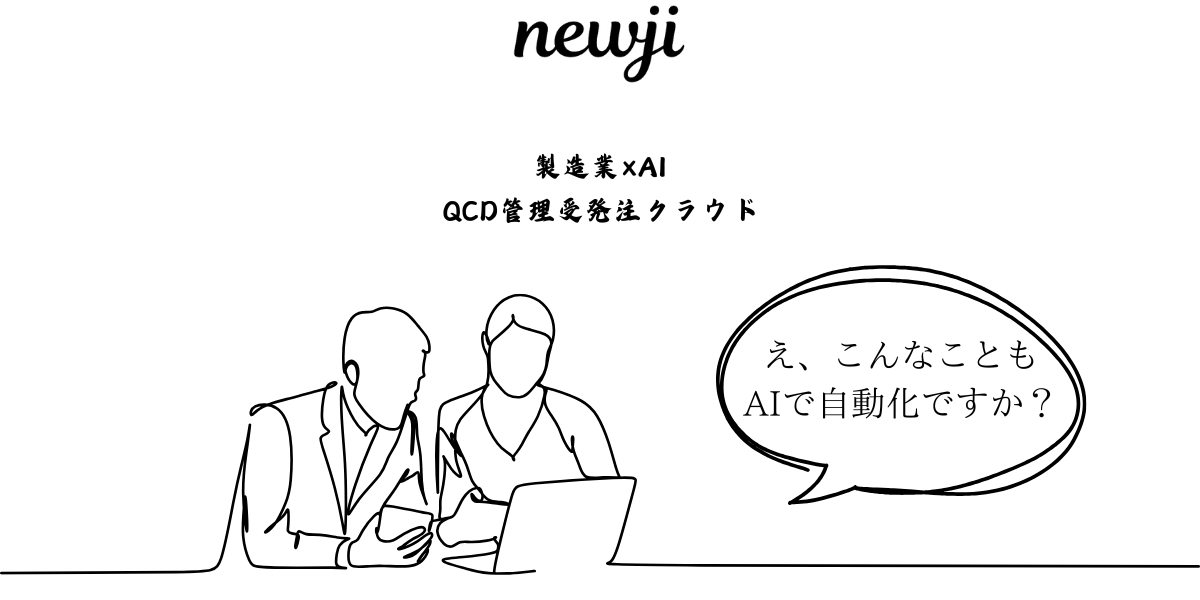
The cutting edge of composite materials and new materials that R&D leaders should know about
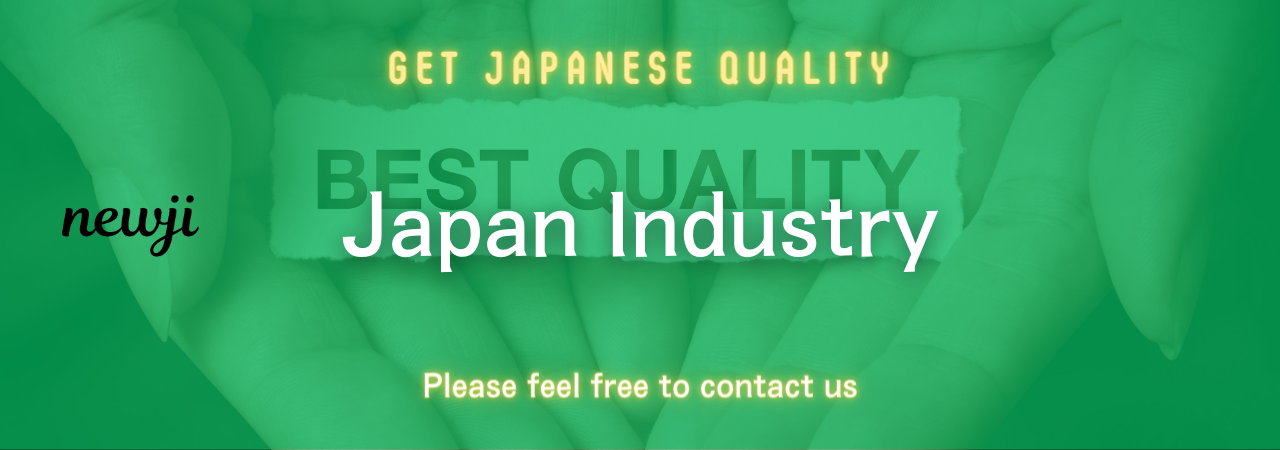
目次
Introduction to Composite Materials
Composite materials have long been at the forefront of innovation in various industries.
They are engineered materials made by combining two or more constituent materials with significantly different physical or chemical properties.
The result is a product that possesses unique attributes, often surpassing those of its individual components.
Composite materials are celebrated for their lightweight nature, high strength-to-weight ratio, and versatility, making them essential in sectors such as aerospace, automotive, and renewable energy.
Understanding the cutting-edge developments in composite materials is crucial for R&D leaders to unlock new possibilities and maintain a competitive edge.
The Basics of Composite Materials
Before delving into the latest advancements, it’s essential to grasp the fundamental aspects of composite materials.
These materials typically consist of a matrix and a reinforcement phase.
The matrix, often a polymer, metal, or ceramic, surrounds and supports the reinforcement, contributing to the integrity and stability of the composite.
The reinforcement generally consists of fibers, particles, or flakes and is responsible for providing strength and rigidity.
A classic example of a composite material is fiberglass, where glass fibers are embedded within a polymer matrix.
This combination yields a material that is strong, lightweight, and corrosion-resistant.
Such composites are employed in diverse applications, from boat hulls to wind turbine blades.
Advanced Composite Materials
Carbon Fiber Reinforced Polymers (CFRP)
Carbon fiber reinforced polymers have gained immense popularity due to their exceptional properties.
Carbon fibers exhibit high tensile strength, low weight, and resistance to thermal expansion, making them ideal for high-performance applications.
CFRP is extensively used in aerospace for building aircraft components, as well as in automotive engineering for manufacturing lightweight, fuel-efficient cars.
Graphene-Based Composites
Graphene, a single layer of carbon atoms arranged in a two-dimensional lattice, has garnered significant interest due to its extraordinary mechanical, electrical, and thermal properties.
When integrated into composite materials, graphene can impart enhanced electrical conductivity, thermal conductivity, and mechanical strength.
These graphene-based composites show promise in a range of applications, from flexible electronics to high-strength structural components.
Bio-Composites
With increasing focus on sustainability, bio-composites are an exciting area of research and development.
These materials are derived from renewable sources, such as plant fibers and biodegradable polymers.
Bio-composites offer a sustainable alternative to traditional composites by reducing the environmental footprint.
Industries like packaging, construction, and automotive are exploring bio-composites for their potential to create eco-friendly products without compromising performance.
Innovations in Composite Manufacturing
3D Printing of Composites
Additive manufacturing, commonly known as 3D printing, has revolutionized the way composite materials are produced.
3D printing allows for intricate designs that were previously impossible or cost-prohibitive to manufacture with traditional methods.
This technology facilitates rapid prototyping and customization of composite parts, especially beneficial in industries that demand swift innovation cycles.
3D printing of composites is paving the way for creating tailored components with complex geometries and optimized properties.
Automated Fiber Placement (AFP)
Automated fiber placement is a cutting-edge technique used in the production of composite materials.
This advanced process involves robotically controlled placement of fiber tapes or tows onto a mold to create a precise composite structure.
AFP provides exceptional control over fiber orientation, which is crucial for achieving the desired mechanical properties.
Aerospace and defense sectors extensively utilize AFP for manufacturing large-scale components, such as aircraft wings and fuselage sections.
Applications of Composite Materials
Aerospace Industry
The aerospace industry is a significant driver of innovation in composite materials.
The demand for lightweight, high-strength materials has propelled the use of composites in aircraft structures, such as wings, tails, and fuselages.
Composites reduce the overall weight of the aircraft, leading to improved fuel efficiency and increased payload capacity.
As aviation continues to evolve, composite materials will play a pivotal role in developing next-generation aircraft.
Automotive Sector
The automotive sector is embracing composite materials to meet stringent environmental regulations and consumer demands for fuel-efficient vehicles.
By incorporating lightweight composites into vehicle design, manufacturers can enhance performance, reduce emissions, and improve safety features.
Car components, such as body panels, hoods, and suspension systems, are increasingly made from composites.
Renewable Energy
Composite materials are integral to the growth of renewable energy industries, particularly wind and solar power.
Wind turbine blades, for instance, require materials that can withstand harsh environmental conditions while maintaining minimal weight.
Composite materials, such as fiberglass and carbon fiber, are ideal for this purpose.
In solar energy, composites are used in the manufacturing of support structures and panel frames, optimizing durability and performance in various climates.
Future Directions and Challenges
The future of composite materials is promising, with ongoing research focused on enhancing their properties and expanding their applications.
However, challenges remain in terms of high production costs, recyclability, and standardization.
R&D leaders must address these issues to unleash the full potential of composite materials.
Advancements in nanotechnology and molecular engineering hold the key to unlocking novel composites with unprecedented characteristics.
As technology progresses, we can expect composite materials to revolutionize industries, contributing to a more sustainable and efficient future.
Conclusion
Composite materials are at the cutting edge of innovation in material science, offering unparalleled advantages across various sectors.
Continued research and development are essential to harnessing their full potential.
R&D leaders should remain informed about the latest advancements in composite materials to drive innovation and meet the demands of a rapidly evolving world.
Whether it’s improving energy efficiency, enhancing product performance, or minimizing environmental impact, the next generation of composite materials holds the key to unlocking new possibilities.
資料ダウンロード
QCD調達購買管理クラウド「newji」は、調達購買部門で必要なQCD管理全てを備えた、現場特化型兼クラウド型の今世紀最高の購買管理システムとなります。
ユーザー登録
調達購買業務の効率化だけでなく、システムを導入することで、コスト削減や製品・資材のステータス可視化のほか、属人化していた購買情報の共有化による内部不正防止や統制にも役立ちます。
NEWJI DX
製造業に特化したデジタルトランスフォーメーション(DX)の実現を目指す請負開発型のコンサルティングサービスです。AI、iPaaS、および先端の技術を駆使して、製造プロセスの効率化、業務効率化、チームワーク強化、コスト削減、品質向上を実現します。このサービスは、製造業の課題を深く理解し、それに対する最適なデジタルソリューションを提供することで、企業が持続的な成長とイノベーションを達成できるようサポートします。
オンライン講座
製造業、主に購買・調達部門にお勤めの方々に向けた情報を配信しております。
新任の方やベテランの方、管理職を対象とした幅広いコンテンツをご用意しております。
お問い合わせ
コストダウンが利益に直結する術だと理解していても、なかなか前に進めることができない状況。そんな時は、newjiのコストダウン自動化機能で大きく利益貢献しよう!
(Β版非公開)