- お役立ち記事
- The difference between 5S Activities and 3S Activities
月間76,176名の
製造業ご担当者様が閲覧しています*
*2025年3月31日現在のGoogle Analyticsのデータより
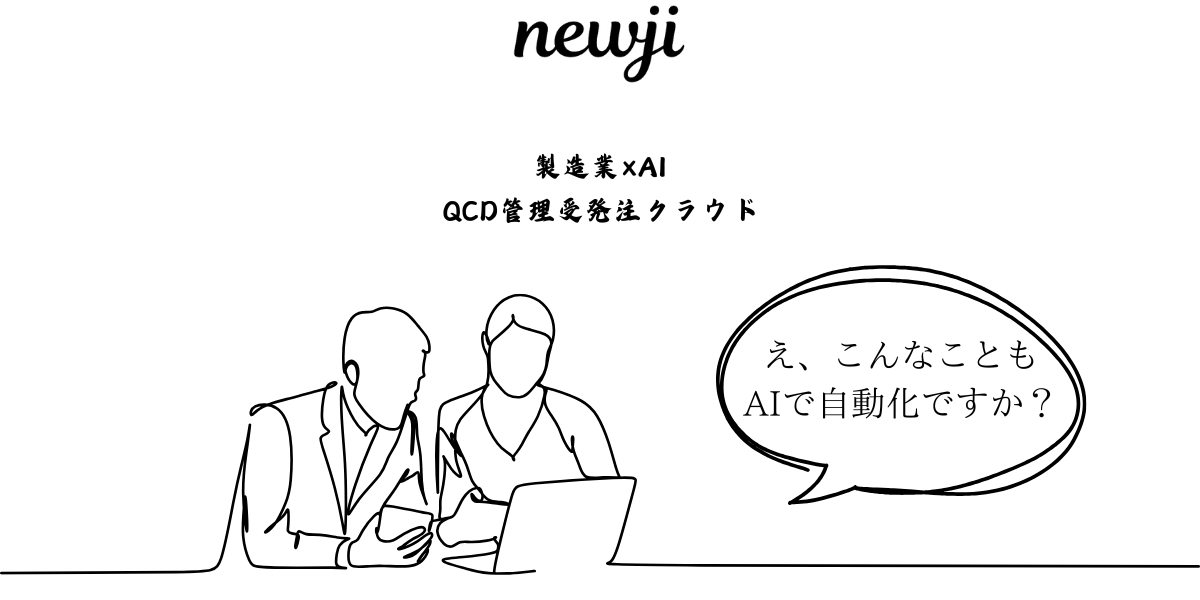
The difference between 5S Activities and 3S Activities
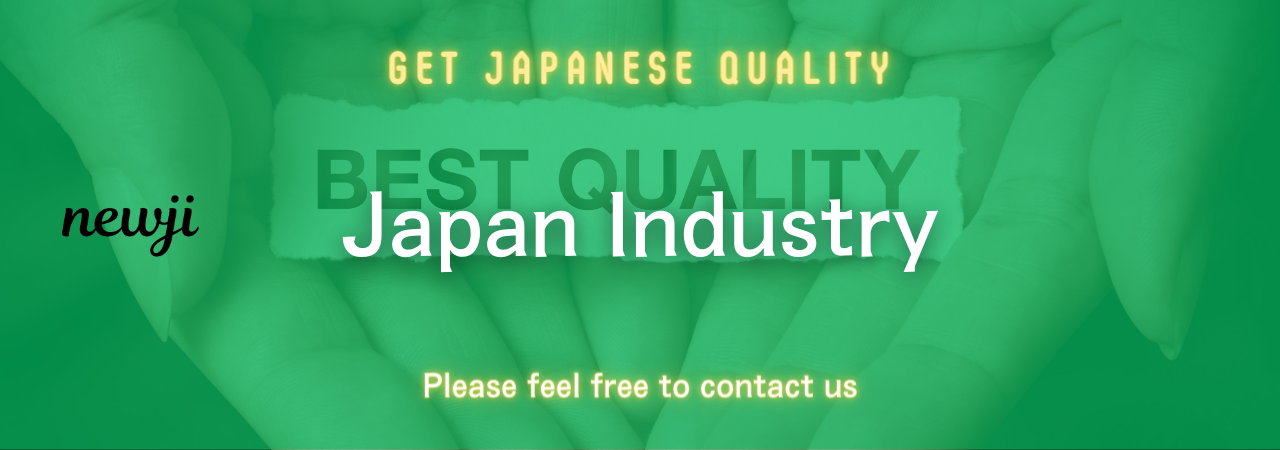
In workplaces across the world, businesses strive for efficiency, safety, and organization.
Two prominent strategies that help achieve these goals are 5S Activities and 3S Activities.
Although they share similarities, understanding their differences is key to implementing them effectively.
目次
What Are 5S Activities?
5S is a systematic approach to improving workplace efficiency and organization.
It originated in Japan and consists of five steps, each beginning with the letter “S”.
These steps are:
Sort (Seiri)
The first step involves sorting through all items in the workplace.
Unnecessary items are removed, leaving only what is needed for current operations.
This decluttering process helps in eliminating waste and creating a neat environment.
Set in Order (Seiton)
Once unnecessary items are removed, the next step is to organize the remaining items.
Tools, materials, and equipment are arranged in a way that minimizes downtime and maximizes productivity.
Each item has a designated place, making it easy to find and return after use.
Shine (Seiso)
Cleaning the workplace and maintaining cleanliness is the focus of this step.
Regular cleaning routines are established, ensuring that the area remains tidy.
A clean workspace reduces the risk of accidents and improves overall efficiency.
Standardize (Seiketsu)
Standardization ensures that the first three steps (Sort, Set in Order, Shine) are maintained consistently.
This involves creating guidelines and checklists to follow, making it easier for employees to uphold the standards.
Sustain (Shitsuke)
The final step is about discipline.
Sustain involves creating a habit of following the 5S principles.
Through continuous training and reinforcement, employees are encouraged to maintain these practices as part of their routine.
What Are 3S Activities?
3S Activities also aim to improve workplace efficiency, but they focus on three main principles.
The steps in 3S are:
Sort (Seiri)
Similar to 5S, the first step in 3S involves sorting out unnecessary items and retaining only what is needed.
This creates a streamlined workspace and reduces clutter.
Sweep (Seiso)
The second step, Sweep or Shine, is the same as in 5S.
It focuses on cleaning the workplace.
A tidy environment is maintained through regular cleaning, ensuring everything is in good condition.
Sustain (Shitsuke)
The final step in 3S maintains the progress made in the first two steps.
It’s about discipline and ensuring that the organization and cleanliness are sustained over time.
Regular checks and training help in embedding these practices into the workplace culture.
Key Differences Between 5S and 3S
While both 5S and 3S share common principles, there are key differences that set them apart.
Understanding these differences is crucial for choosing the right approach for your workplace.
Number of Steps
The most obvious difference is the number of steps involved.
5S includes five steps (Sort, Set in Order, Shine, Standardize, Sustain), while 3S includes three steps (Sort, Sweep, Sustain).
Depth of Organization
5S goes deeper into the organization process with the “Set in Order” and “Standardize” steps.
These steps ensure that items are arranged in the most efficient manner and that these arrangements are consistently followed.
3S, on the other hand, focuses more on the immediate sorting and cleaning tasks, omitting the structure and standardization steps.
Focus on Standardization
5S emphasizes the importance of standardizing practices to ensure consistency.
This is achieved through guidelines, checklists, and visual aids.
3S does not explicitly include a standardization step, focusing instead on maintaining cleanliness and organization.
Discipline and Sustainability
Both approaches highlight the importance of sustaining the improvements made.
However, 5S places a greater emphasis on creating a disciplined culture around this.
It involves continuous training and reinforcement to maintain the standards.
3S also focuses on sustainability but tends to be simpler in its approach.
Benefits of 5S Activities
Implementing 5S in the workplace can bring numerous benefits:
Improved Productivity
With everything in its place and an organized environment, employees can work more efficiently.
Time is saved by reducing the need to search for tools or materials.
Enhanced Safety
A clean and organized workplace reduces the risk of accidents.
Hazards are identified and eliminated, creating a safer environment for everyone.
Better Morale
A tidy and well-organized workplace can boost employee morale.
It creates a positive atmosphere, making it a more pleasant place to work.
Consistent Quality
Standardized practices help in maintaining consistent quality.
Employees follow set guidelines, ensuring that processes remain uniform.
Benefits of 3S Activities
Although simpler, 3S activities also offer several benefits:
Quick Implementation
With fewer steps to follow, 3S can be implemented more quickly.
It is ideal for organizations looking for immediate improvements without extensive training.
Improved Cleanliness
Regular cleaning ensures that the workplace remains tidy.
This has a direct impact on health and safety.
Cost-Effective
3S can be more cost-effective as it requires fewer resources and less training.
It is simpler to maintain, making it ideal for smaller organizations or those with limited budgets.
Choosing Between 5S and 3S
When deciding which approach to implement, consider the needs of your organization.
5S is best suited for environments that require a deep level of organization and consistency.
It is ideal for larger operations where standardization is crucial.
On the other hand, 3S is more suited for smaller environments or for those that need quick, straightforward improvements in cleanliness and organization.
Final Thoughts
Both 5S and 3S provide effective strategies for enhancing workplace efficiency and safety.
While 5S offers a more comprehensive approach with a focus on standardization, 3S offers a quicker, simpler solution.
Understanding the differences between them allows businesses to choose the approach that best fits their specific needs and goals.
Regardless of which strategy is chosen, regular training and commitment are vital to sustaining the improvements made.
資料ダウンロード
QCD管理受発注クラウド「newji」は、受発注部門で必要なQCD管理全てを備えた、現場特化型兼クラウド型の今世紀最高の受発注管理システムとなります。
ユーザー登録
受発注業務の効率化だけでなく、システムを導入することで、コスト削減や製品・資材のステータス可視化のほか、属人化していた受発注情報の共有化による内部不正防止や統制にも役立ちます。
NEWJI DX
製造業に特化したデジタルトランスフォーメーション(DX)の実現を目指す請負開発型のコンサルティングサービスです。AI、iPaaS、および先端の技術を駆使して、製造プロセスの効率化、業務効率化、チームワーク強化、コスト削減、品質向上を実現します。このサービスは、製造業の課題を深く理解し、それに対する最適なデジタルソリューションを提供することで、企業が持続的な成長とイノベーションを達成できるようサポートします。
製造業ニュース解説
製造業、主に購買・調達部門にお勤めの方々に向けた情報を配信しております。
新任の方やベテランの方、管理職を対象とした幅広いコンテンツをご用意しております。
お問い合わせ
コストダウンが利益に直結する術だと理解していても、なかなか前に進めることができない状況。そんな時は、newjiのコストダウン自動化機能で大きく利益貢献しよう!
(β版非公開)