- お役立ち記事
- The difference between Accuracy Management and Quality Standards
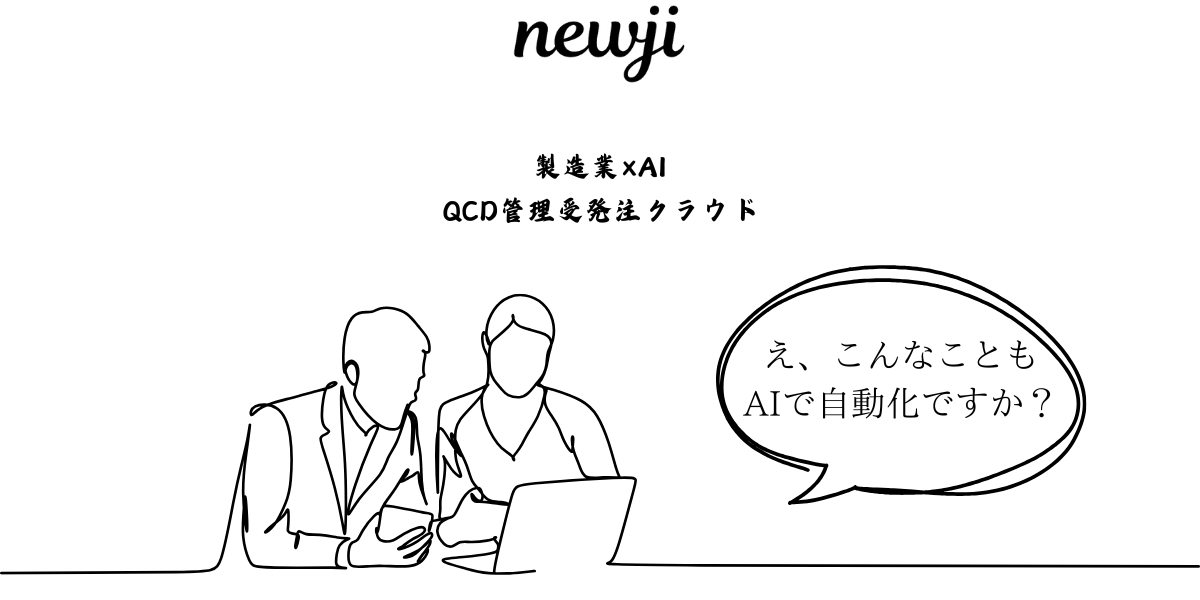
The difference between Accuracy Management and Quality Standards
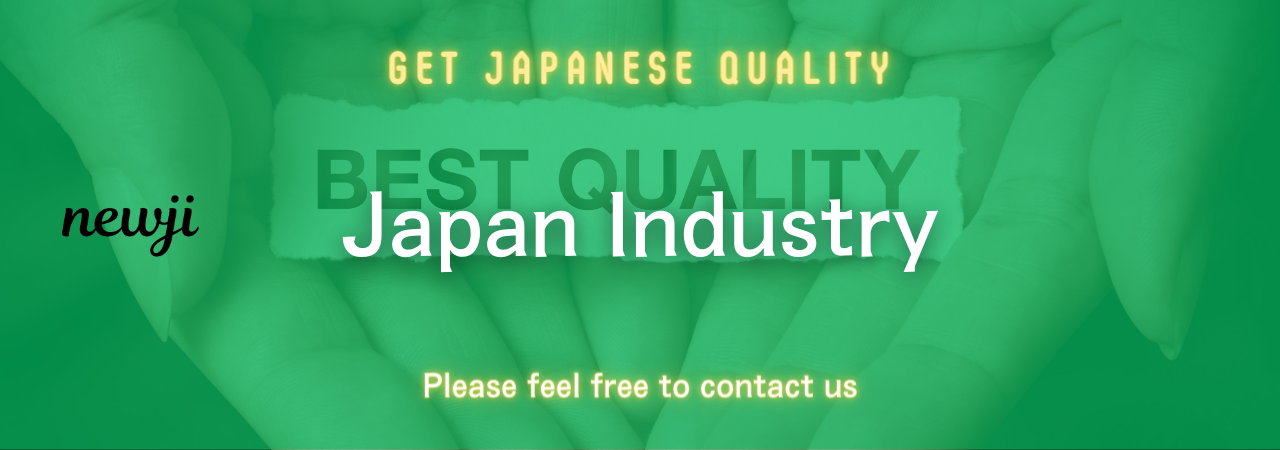
When it comes to delivering products and services, two terms that often come up are accuracy management and quality standards.
These concepts are crucial for businesses aiming to provide top-notch results, but they aren’t quite the same thing.
Let’s dive deep into the differences between accuracy management and quality standards, helping clarify these essential aspects.
目次
What is Accuracy Management?
Accuracy management focuses on the precision and correctness of data, measurements, and processes.
It’s about making sure that everything aligns perfectly with a specified benchmark or criterion.
Mistakes or deviations can lead to significant problems, whether in manufacturing, healthcare, finance, or any other industry.
Key Components of Accuracy Management
1. **Data Verification:**
This involves checking and cross-referencing data to ensure its correctness.
For example, data entry errors can cause big issues, so ensuring accuracy is vital.
2. **Measurement Calibration:**
Keeping equipment and tools calibrated ensures they provide accurate measurements.
Regular inspections and maintenance are essential in this regard.
3. **Process Monitoring:**
Continuously watching processes helps identify deviations.
Early detection of errors can prevent them from escalating and affecting the final output.
Benefits of Accuracy Management
Accuracy management offers multiple benefits.
It reduces errors, saves cost from rework, and enhances customer satisfaction.
Businesses can maintain a higher level of trust and reliability among their clients.
What are Quality Standards?
Quality standards, on the other hand, are predefined criteria that products or services must meet to be considered acceptable.
These standards are set by industry bodies, regulatory agencies, or internally within a company.
They ensure consistency and provide a benchmark against which products and services are evaluated.
Key Components of Quality Standards
1. **Compliance:**
Adhering to legal and regulatory requirements is essential.
Non-compliance can lead to penalties and legal issues, damaging a company’s reputation.
2. **Specification Adherence:**
Meeting detailed requirements such as size, material, composition, etc., is crucial.
Deviations from these specifications can lead to product failures or inefficiencies.
3. **Quality Assurance and Control:**
Implementing processes to monitor and inspect the quality of outputs.
This involves regular audits, testing, and quality control checks.
Benefits of Quality Standards
Quality standards assure that a product or service is safe, reliable, and performs as expected.
They provide a competitive edge, as consumers are more likely to trust and purchase high-quality products.
Moreover, they enhance internal efficiency and reduce waste, leading to cost savings.
Key Differences between Accuracy Management and Quality Standards
Focus
Accuracy management primarily focuses on the correctness and precision of specific elements within a process.
It’s about ensuring that individual data points and measurements are accurate.
Quality standards encompass a broader focus, evaluating the overall product or service performance.
They look at the bigger picture, ensuring that the final output meets predefined criteria.
Scope
Accuracy management usually targets specific tasks, measurements, or data points.
It involves detailed verification and calibration processes.
Quality standards, however, cover an entire process or product lifespan, from initial design to final delivery.
They ensure comprehensive quality adherence.
Implementation
Accuracy management involves precise tools and technologies for measurement and verification.
It requires continuous monitoring and adjustments to maintain accuracy.
Quality standards involve guidelines and protocols that need to be followed.
They require systematic audits, testing, and compliance checks.
Outcome
The outcome of accuracy management is pinpoint accuracy and minimized errors in specific areas.
This increases the reliability of inputs and processes.
The outcome of adhering to quality standards is a consistent, reliable, and high-quality final product or service.
This boosts consumer trust and satisfaction.
How Businesses Can Benefit from Both
Enhanced Customer Satisfaction
Combining accuracy management with quality standards ensures that not only are the products precisely made, but they also meet high-quality expectations.
This dual approach significantly enhances customer satisfaction and loyalty.
Operational Efficiency
Accuracy management helps reduce wastage and rework by eliminating errors early.
Quality standards ensure that processes are optimized for consistent and reliable output.
Together, these enhance operational efficiency and productivity.
Competitive Advantage
Incorporating accuracy management and quality standards can set a company apart from competitors.
It shows a commitment to excellence and reliability, attracting more customers and securing a strong market position.
Examples in Different Industries
Manufacturing
In the manufacturing industry, accuracy management ensures that each component fits together perfectly, reducing assembly errors.
Quality standards ensure that the final product is durable and meets safety regulations.
Healthcare
In healthcare, data accuracy is critical in diagnostics and treatment plans.
Quality standards ensure that the facilities, equipment, and services meet stringent health and safety criteria.
Finance
In finance, accuracy management ensures that all figures, reports, and transactions are precise, minimizing errors that could lead to significant financial discrepancies.
Quality standards ensure that all financial services and products are trustworthy and comply with legal requirements.
Understanding the distinction between accuracy management and quality standards equips businesses to better strategize and implement practices that will enhance both precision and quality.
These elements, while distinct, are complementary and essential for achieving excellence in any industry.
By integrating both, businesses can not only meet industry standards but exceed customer expectations, paving the way for sustained success.
資料ダウンロード
QCD調達購買管理クラウド「newji」は、調達購買部門で必要なQCD管理全てを備えた、現場特化型兼クラウド型の今世紀最高の購買管理システムとなります。
ユーザー登録
調達購買業務の効率化だけでなく、システムを導入することで、コスト削減や製品・資材のステータス可視化のほか、属人化していた購買情報の共有化による内部不正防止や統制にも役立ちます。
NEWJI DX
製造業に特化したデジタルトランスフォーメーション(DX)の実現を目指す請負開発型のコンサルティングサービスです。AI、iPaaS、および先端の技術を駆使して、製造プロセスの効率化、業務効率化、チームワーク強化、コスト削減、品質向上を実現します。このサービスは、製造業の課題を深く理解し、それに対する最適なデジタルソリューションを提供することで、企業が持続的な成長とイノベーションを達成できるようサポートします。
オンライン講座
製造業、主に購買・調達部門にお勤めの方々に向けた情報を配信しております。
新任の方やベテランの方、管理職を対象とした幅広いコンテンツをご用意しております。
お問い合わせ
コストダウンが利益に直結する術だと理解していても、なかなか前に進めることができない状況。そんな時は、newjiのコストダウン自動化機能で大きく利益貢献しよう!
(Β版非公開)