- お役立ち記事
- The difference between Aluminum Casting and Zinc Casting
月間76,176名の
製造業ご担当者様が閲覧しています*
*2025年3月31日現在のGoogle Analyticsのデータより
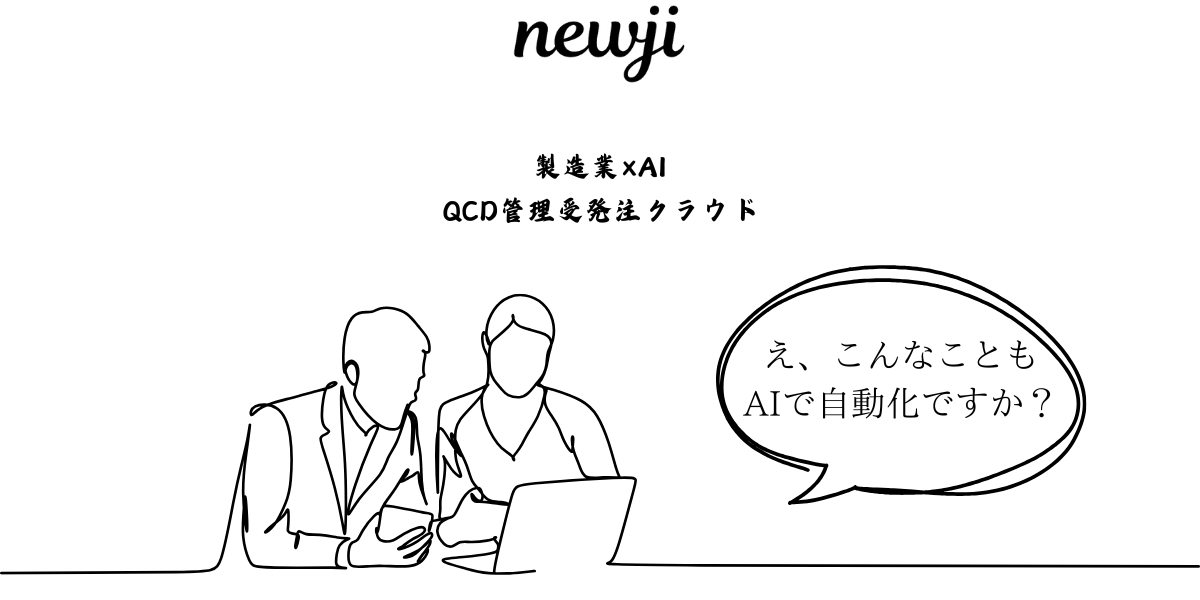
The difference between Aluminum Casting and Zinc Casting
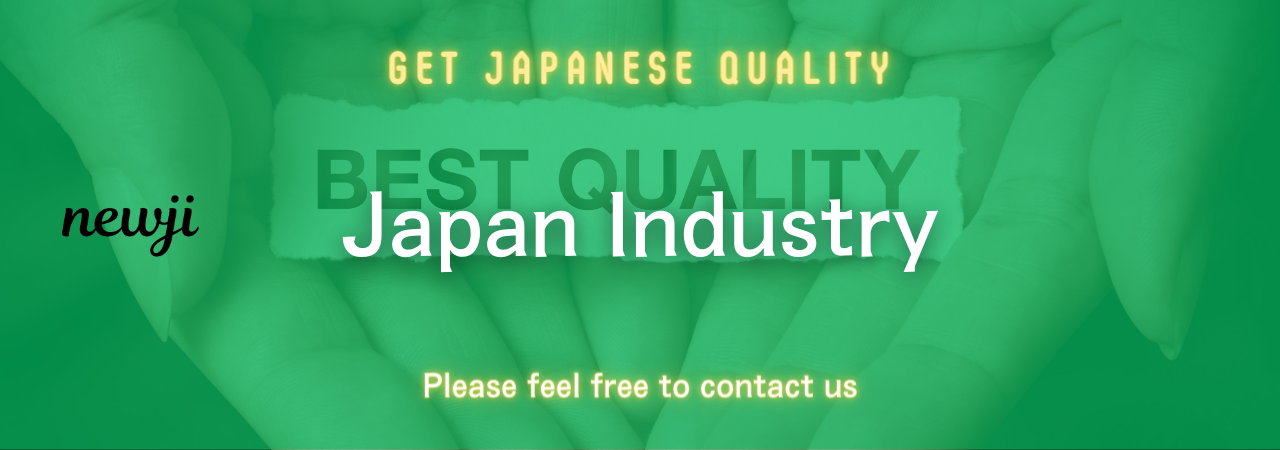
When exploring the world of metal casting, two primary materials often come up: aluminum and zinc. Both metals are popular in various industries due to their unique properties.
Understanding the differences between aluminum casting and zinc casting can help businesses and individuals make informed decisions for their projects.
目次
What is Aluminum Casting?
Aluminum casting involves creating items by pouring molten aluminum into a mold. The aluminum cools and solidifies into the desired shape.
One of the primary benefits of using aluminum in casting is its lightweight nature. This makes it ideal for applications where weight is a critical factor, such as in the aerospace and automotive industries.
Advantages of Aluminum Casting
Aluminum casting offers several advantages. These benefits make it a preferred choice for various applications:
1. **Lightweight**: Aluminum is considerably lighter than other metals, which contributes to its widespread use in industries requiring weight reduction.
2. **Corrosion Resistance**: Aluminum naturally forms an oxide layer that protects it from corrosion. This makes it suitable for use in environments where metals are exposed to moisture and other corrosive elements.
3. **High Thermal Conductivity**: Aluminum has excellent thermal conductivity, making it ideal for heat exchangers and other applications where heat dissipation is crucial.
4. **Ease of Machining**: Aluminum is relatively easy to machine, allowing for the creation of complex shapes and designs.
Applications of Aluminum Casting
Due to its unique properties, aluminum casting finds application in a variety of industries:
1. **Automotive**: Engine components, wheel rims, and other parts benefit from aluminum’s lightweight and strength.
2. **Aerospace**: Airplane parts and structural components often use aluminum to enhance performance while reducing weight.
3. **Electronics**: Housings for electronic devices take advantage of aluminum’s thermal conductivity.
What is Zinc Casting?
Zinc casting, also known as die-casting, involves the use of zinc alloys to create items by injecting molten zinc into a mold.
Zinc is a versatile metal with several beneficial properties that make it suitable for casting.
Advantages of Zinc Casting
Zinc casting offers a range of advantages that make it an excellent choice for specific applications:
1. **High Strength**: Zinc alloys typically have higher strength compared to pure aluminum, making them suitable for parts that must withstand mechanical stress.
2. **Dimensional Stability**: Zinc alloys exhibit minimal shrinkage during the cooling process. This ensures that the final product has high dimensional accuracy.
3. **Excellent Corrosion Resistance**: Like aluminum, zinc also forms an oxide layer that protects it from corrosion, extending the life of parts exposed to harsh conditions.
4. **Lower Melting Point**: Zinc’s lower melting point compared to aluminum reduces energy consumption during the casting process, making it a more cost-effective option.
Applications of Zinc Casting
The properties of zinc casting make it ideal for several applications across different industries:
1. **Automotive**: Precision components, such as door handles and intricate mechanical parts, benefit from zinc’s strength and dimensional accuracy.
2. **Consumer Goods**: Items like zippers, toys, and other small products often utilize zinc casting due to its ease of molding and strength.
3. **Hardware**: Locks, gears, and various hardware components also benefit from the advantages of zinc casting.
Comparing Aluminum Casting and Zinc Casting
When deciding between aluminum casting and zinc casting, it’s essential to consider the specific requirements of your project. Here, we compare the two to highlight their different attributes:
Weight
Aluminum is significantly lighter than zinc. This makes aluminum casting the preferred choice for applications where weight reduction is critical. On the other hand, zinc’s higher density provides more weight for parts that need it.
Strength
While aluminum is strong and lightweight, zinc alloys generally offer higher strength. This makes zinc casting more suitable for parts requiring higher mechanical strength and durability.
Cost
Aluminum casting typically requires higher energy consumption due to its higher melting point. While aluminum itself is relatively inexpensive, the casting process can be more costly compared to zinc casting.
Zinc’s lower melting point makes the casting process more energy-efficient and cost-effective.
Corrosion Resistance
Both aluminum and zinc offer excellent corrosion resistance. The natural oxide layer that forms on their surfaces acts as a protective barrier against environmental elements. This makes them both suitable for use in harsh conditions, but specific applications might favor one material over the other based on other properties.
Thermal Conductivity
Aluminum has better thermal conductivity compared to zinc, making it ideal for applications where heat dissipation is crucial. This property is particularly important in industries such as electronics and automotive manufacturing, where managing heat is vital for performance and safety.
Ease of Machining and Moldability
Aluminum is easier to machine into complex shapes, which allows for more intricate designs. However, zinc’s excellent moldability and minimal shrinkage during cooling provide high dimensional accuracy, making it ideal for precision parts.
Conclusion
Both aluminum casting and zinc casting have their unique advantages and applications. Choosing the right material for your cast parts depends on factors such as weight considerations, strength requirements, cost constraints, and specific industry needs.
By understanding the differences between the two materials, you can make informed decisions that lead to successful projects and optimal performance. Whether you opt for the lightweight and thermally conductive properties of aluminum or the strength and cost-effectiveness of zinc, each material brings valuable benefits to the table.
資料ダウンロード
QCD管理受発注クラウド「newji」は、受発注部門で必要なQCD管理全てを備えた、現場特化型兼クラウド型の今世紀最高の受発注管理システムとなります。
ユーザー登録
受発注業務の効率化だけでなく、システムを導入することで、コスト削減や製品・資材のステータス可視化のほか、属人化していた受発注情報の共有化による内部不正防止や統制にも役立ちます。
NEWJI DX
製造業に特化したデジタルトランスフォーメーション(DX)の実現を目指す請負開発型のコンサルティングサービスです。AI、iPaaS、および先端の技術を駆使して、製造プロセスの効率化、業務効率化、チームワーク強化、コスト削減、品質向上を実現します。このサービスは、製造業の課題を深く理解し、それに対する最適なデジタルソリューションを提供することで、企業が持続的な成長とイノベーションを達成できるようサポートします。
製造業ニュース解説
製造業、主に購買・調達部門にお勤めの方々に向けた情報を配信しております。
新任の方やベテランの方、管理職を対象とした幅広いコンテンツをご用意しております。
お問い合わせ
コストダウンが利益に直結する術だと理解していても、なかなか前に進めることができない状況。そんな時は、newjiのコストダウン自動化機能で大きく利益貢献しよう!
(β版非公開)