- お役立ち記事
- The difference between Bill of Materials (BOM) and Material List
月間76,176名の
製造業ご担当者様が閲覧しています*
*2025年3月31日現在のGoogle Analyticsのデータより
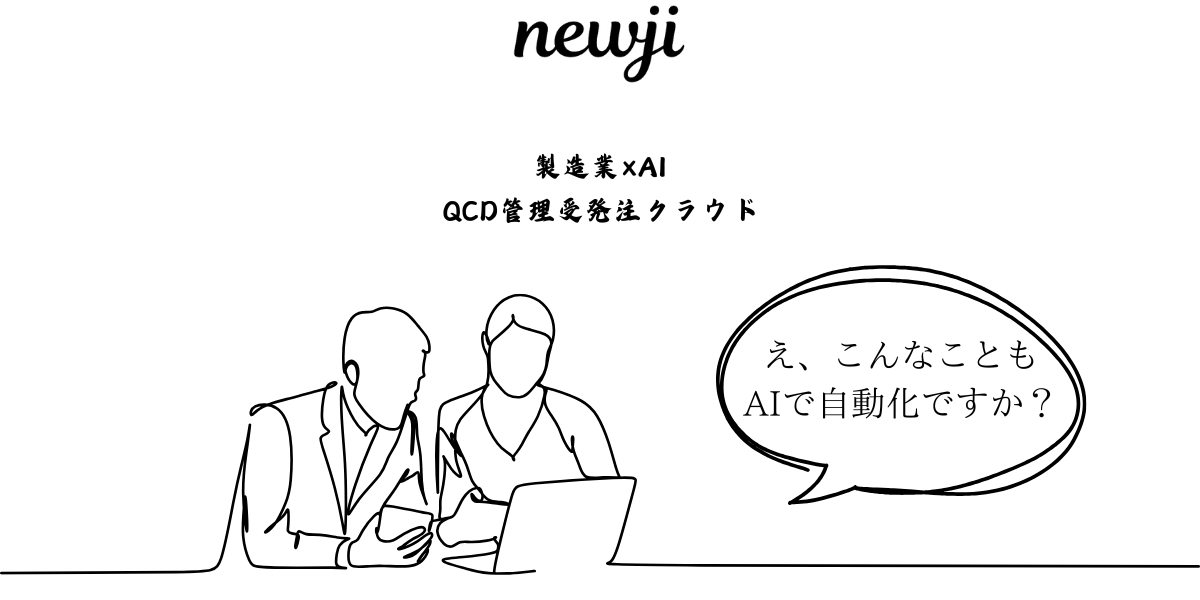
The difference between Bill of Materials (BOM) and Material List
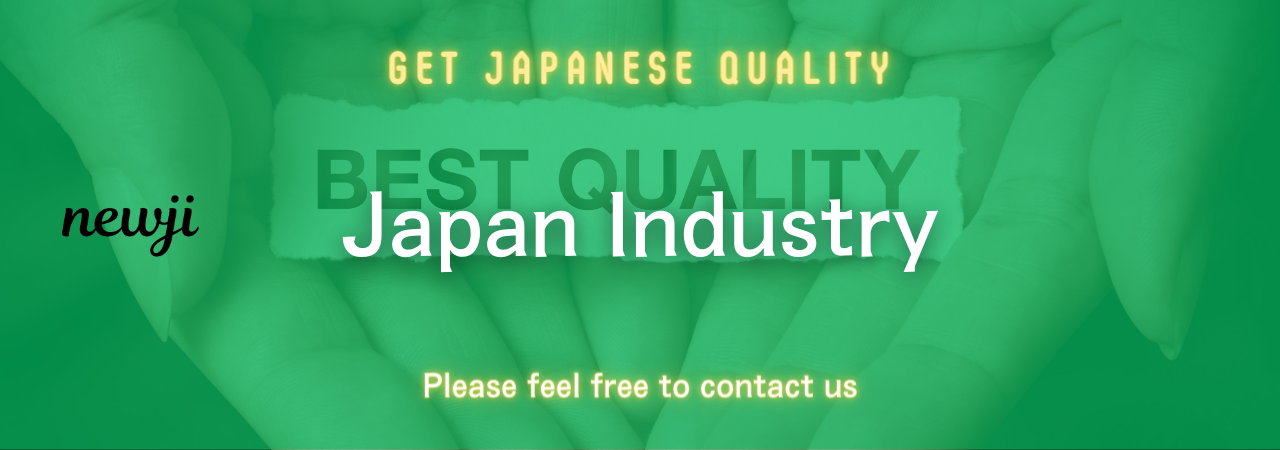
Understanding the difference between a Bill of Materials (BOM) and a Material List is crucial for anyone involved in manufacturing, project management, or sourcing.
Though the terms are often used interchangeably, they serve different purposes in the production process.
Let’s break down each term to understand their unique roles and how they complement each other.
目次
What is a Bill of Materials (BOM)?
A Bill of Materials, commonly abbreviated as BOM, is an extensive list of raw materials, components, and assemblies required to build or manufacture a product.
It serves as a blueprint for the entire production process, guiding engineers, manufacturers, and supply chain managers.
Types of BOMs
There are several types of BOMs, each tailored for specific needs:
– **Engineering BOM (EBOM):** Focuses on the design aspects and is typically used by engineers.
– **Manufacturing BOM (MBOM):** Used on the production line and includes information on how parts are assembled.
– **Sales BOM (SBOM):** Used for sales items that are often packaged together but delivered separately.
Components of a BOM
A BOM generally includes:
– **Part Number:** A unique identifier for each material or component.
– **Part Name:** The name of each part.
– **Quantity:** The required number of each item.
– **Description:** Additional details that help identify the part.
– **Unit of Measure:** The unit, such as pieces, meters, or kilograms.
– **Procurement Type:** Indicates whether the item is purchased, manufactured, or outsourced.
Purpose of a BOM
– **Project Planning:** A BOM helps in detailed project planning and scheduling.
– **Cost Estimation:** It aids in calculating the total cost of materials and production.
– **Inventory Management:** Ensures the required materials are sourced and available when needed.
– **Quality Control:** Helps maintain consistency and quality by standardizing the parts and components used.
What is a Material List?
A Material List, on the other hand, is a simpler and less detailed version compared to a BOM.
It lists the materials necessary for a project but doesn’t go into the specifics of how these materials are used in the final product.
Components of a Material List
Typically, a Material List includes:
– **Item Name:** Names of the materials needed.
– **Quantity:** How much of each material is required.
– **Description:** A brief description of each material.
Purpose of a Material List
– **Procurement:** Facilitates the purchase of materials.
– **Inventory Management:** Helps in tracking and organizing materials.
– **Simplified Planning:** Suitable for simpler projects where detailed specifications are not required.
Key Differences between BOM and Material List
Though similar at a high level, BOM and Material List serve different roles and provide varying levels of detail.
Level of Detail
A BOM is far more detailed than a Material List, containing not just materials but also assemblies and subassemblies.
A Material List is more straightforward, usually only listing the materials without detailed specifications.
Purpose
A BOM is used for complex projects requiring detailed planning and execution.
A Material List is ideal for simpler tasks where a detailed breakdown is unnecessary.
Usage in Different Phases
A BOM is utilized throughout the entire lifecycle of a product, from design to production to after-sales services.
A Material List is often used primarily during the procurement and inventory management phases.
When to Use a BOM vs. a Material List
Understanding when to use a BOM or a Material List can streamline your project and improve efficiency.
Use a BOM When:
– Working on complex projects with multiple components and assemblies.
– Detailed tracking and documentation are necessary.
– Quality control and standardization are priorities.
– There is a need to manage costs and timelines precisely.
Use a Material List When:
– The project is simple and doesn’t require extensive planning.
– You need a quick reference for procurement.
– Detailed tracking and documentation are not essential.
Integrating BOM and Material List for Efficiency
Both BOM and Material List have their place in project management and manufacturing.
Using them in conjunction can offer the best of both worlds.
Initial Planning
Start with a Material List to get a rough estimate of what’s needed.
This helps in quick procurement and initial cost estimation.
Detailed Planning and Execution
As the project progresses, switch to a BOM for detailed planning and execution.
This ensures all aspects of production are covered and helps in maintaining quality control.
Conclusion
While a Bill of Materials (BOM) and a Material List might seem similar, they serve distinct purposes in the production process.
Understanding their differences helps in choosing the right tool for your project, ensuring efficiency, cost-effectiveness, and high quality.
By integrating both, you can streamline your workflow, manage resources better, and achieve your project goals more effectively.
資料ダウンロード
QCD管理受発注クラウド「newji」は、受発注部門で必要なQCD管理全てを備えた、現場特化型兼クラウド型の今世紀最高の受発注管理システムとなります。
ユーザー登録
受発注業務の効率化だけでなく、システムを導入することで、コスト削減や製品・資材のステータス可視化のほか、属人化していた受発注情報の共有化による内部不正防止や統制にも役立ちます。
NEWJI DX
製造業に特化したデジタルトランスフォーメーション(DX)の実現を目指す請負開発型のコンサルティングサービスです。AI、iPaaS、および先端の技術を駆使して、製造プロセスの効率化、業務効率化、チームワーク強化、コスト削減、品質向上を実現します。このサービスは、製造業の課題を深く理解し、それに対する最適なデジタルソリューションを提供することで、企業が持続的な成長とイノベーションを達成できるようサポートします。
製造業ニュース解説
製造業、主に購買・調達部門にお勤めの方々に向けた情報を配信しております。
新任の方やベテランの方、管理職を対象とした幅広いコンテンツをご用意しております。
お問い合わせ
コストダウンが利益に直結する術だと理解していても、なかなか前に進めることができない状況。そんな時は、newjiのコストダウン自動化機能で大きく利益貢献しよう!
(β版非公開)