- お役立ち記事
- The difference between Cast Iron Machining and Steel Machining
月間76,176名の
製造業ご担当者様が閲覧しています*
*2025年3月31日現在のGoogle Analyticsのデータより
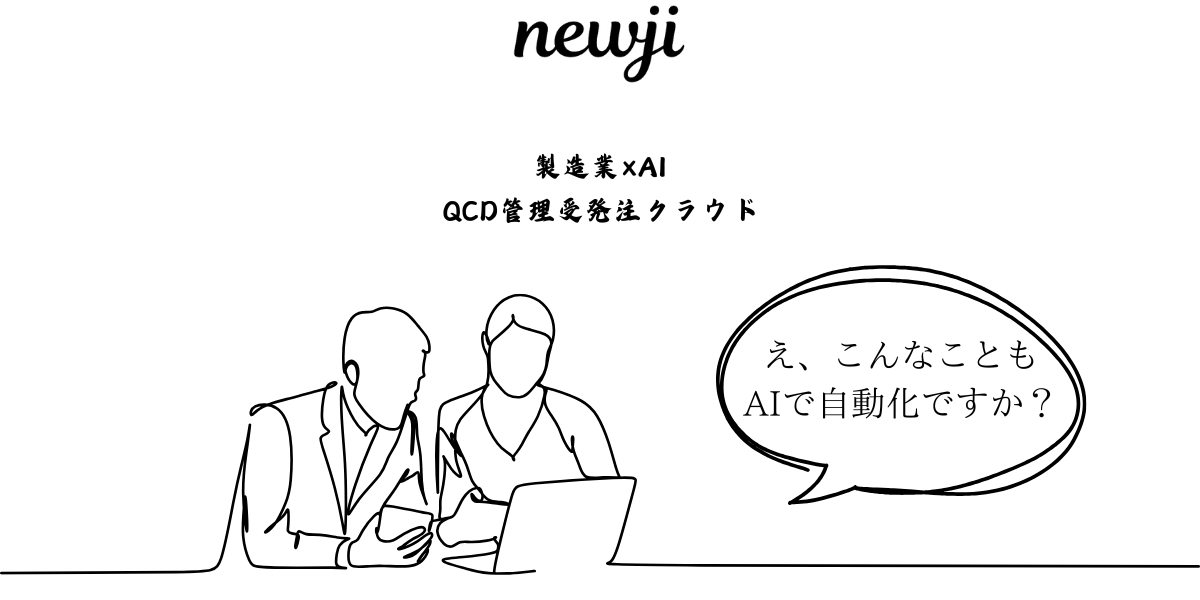
The difference between Cast Iron Machining and Steel Machining
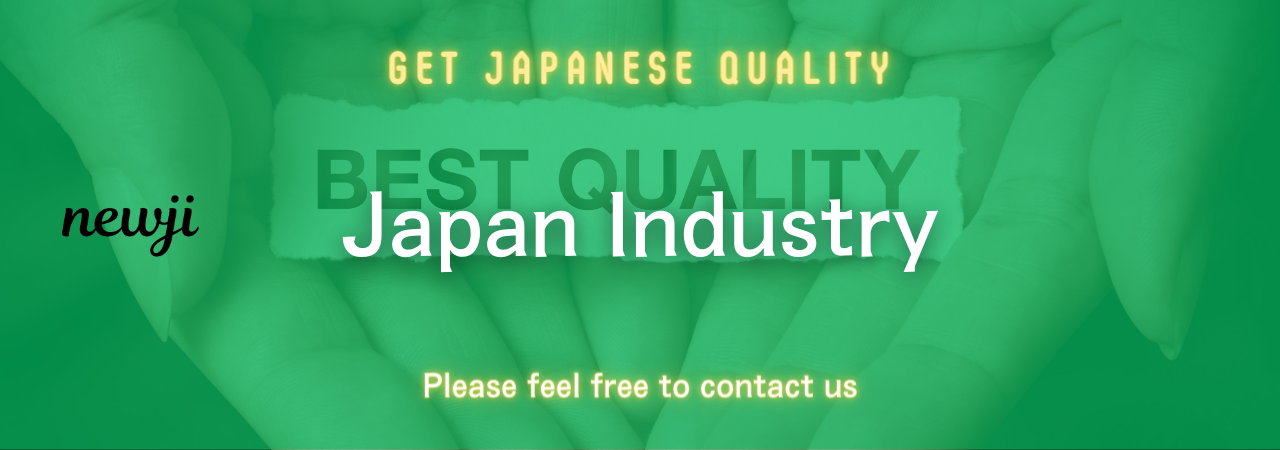
Understanding the process and key differences between cast iron machining and steel machining is crucial for anyone involved in the metalworking industry. Whether you’re a beginner or an experienced professional, having a clear grasp of how these materials behave under machining processes can save you time, money, and effort.
Here, we will dive into the distinct characteristics and machining techniques for both cast iron and steel. By the end of this article, you’ll have a clearer understanding of how to approach each material for optimal results.
目次
What is Cast Iron Machining?
Cast iron is an alloy containing primarily iron, carbon, and silicon. This material has created a significant impact in the field of manufacturing due to its excellent machinability and durability. Cast iron is usually categorized into several types such as grey cast iron, white cast iron, ductile cast iron, and malleable cast iron.
Characteristics of Cast Iron
1. **Brittleness**: Cast iron has high brittleness, meaning it can break or crack under certain conditions.
2. **Hardness**: Cast iron is generally harder than many other metals, which makes it difficult to manipulate but excellent in wear resistance.
3. **Low Melting Point**: This makes it easier to cast various shapes compared to other ferrous metals.
4. **High Density**: This is beneficial for sound dampening applications, often used in machinery bases and engine blocks.
What is Steel Machining?
Steel is another iron-based alloy, but with greater amounts of carbon and additional elements such as chromium, nickel, and vanadium. These added elements give steel unique properties that are modified for specific applications.
Characteristics of Steel
1. **Malleability**: Steel can be shaped and reshaped without breaking, making it versatile for a wide range of applications.
2. **Strength**: Steel possesses a significant strength-to-weight ratio, making it ideal for structural applications.
3. **Corrosion Resistance**: When alloyed with elements like chromium, steel becomes resistant to oxidation and rust.
4. **Variety**: Steel comes in numerous grades and types, each designed for specific purposes.
Machining Processes for Cast Iron
Tool Selection
Selecting the right type of cutting tool is crucial for machining cast iron effectively. Carbide-tipped tools are widely used due to their hardness and ability to withstand high temperatures.
Cutting Speeds and Feeds
Cast iron typically requires moderate cutting speeds and feed rates. Using too high a speed can lead to rapid tool wear and degraded surface finish.
Coolants
The use of coolants in cast iron machining is often debated. Dry machining is popular for cast iron due to the risk of micro-cracks from thermal cycling when coolants are applied.
Machining Processes for Steel
Tool Selection
High-speed steel (HSS) and carbide tools are commonly used for steel machining. Coated carbide tools often extend tool life and provide better surface finishes.
Cutting Speeds and Feeds
Speeds and feeds for steel machining can vary greatly depending on the type of steel being machined. Alloy steels, for example, can often be machined at higher speeds and feed rates compared to carbon steels.
Coolants
Coolants are generally essential in steel machining to reduce the heat generated, minimize tool wear, and improve the surface finish. Water-based coolants and oils are typically used.
Key Differences between Cast Iron and Steel Machining
Brittleness vs. Malleability
Cast iron’s high brittleness requires more cautious handling compared to steel. Steel’s malleability allows for more aggressive machining techniques.
Tool Wear
Cast iron is more abrasive, leading to faster tool wear than steel. Tool maintenance and frequent replacements are often necessary.
Heat Management
Cast iron can often be machined without coolants, while steel typically requires substantial cooling to manage heat buildup and prolong tool life.
Surface Finish
The rough, flaky texture of cast iron often results in a less refined surface finish compared to steel. Achieving a smooth surface on cast iron often demands specific finishing techniques.
Applications of Cast Iron and Steel
Cast Iron
Cast iron is widely used in applications where strength, heat resistance, and durability are paramount. Common uses include engine blocks, pipes, and machinery bases.
Steel
Steel is used in a broader range of applications from construction beams and automotive parts to surgical instruments and household appliances. Its versatility allows it to be tailored for nearly any industrial need.
Conclusion
In summary, while both cast iron and steel are indispensable materials in machining, their distinct properties call for tailored techniques and considerations. Understanding these differences can guide you in selecting the right tools, speeds, and methods for your specific machining needs. Whether you are crafting intricate parts from steel or durable, robust components from cast iron, a well-informed approach will always yield the best results.
資料ダウンロード
QCD管理受発注クラウド「newji」は、受発注部門で必要なQCD管理全てを備えた、現場特化型兼クラウド型の今世紀最高の受発注管理システムとなります。
ユーザー登録
受発注業務の効率化だけでなく、システムを導入することで、コスト削減や製品・資材のステータス可視化のほか、属人化していた受発注情報の共有化による内部不正防止や統制にも役立ちます。
NEWJI DX
製造業に特化したデジタルトランスフォーメーション(DX)の実現を目指す請負開発型のコンサルティングサービスです。AI、iPaaS、および先端の技術を駆使して、製造プロセスの効率化、業務効率化、チームワーク強化、コスト削減、品質向上を実現します。このサービスは、製造業の課題を深く理解し、それに対する最適なデジタルソリューションを提供することで、企業が持続的な成長とイノベーションを達成できるようサポートします。
製造業ニュース解説
製造業、主に購買・調達部門にお勤めの方々に向けた情報を配信しております。
新任の方やベテランの方、管理職を対象とした幅広いコンテンツをご用意しております。
お問い合わせ
コストダウンが利益に直結する術だと理解していても、なかなか前に進めることができない状況。そんな時は、newjiのコストダウン自動化機能で大きく利益貢献しよう!
(β版非公開)