- お役立ち記事
- The difference between Chucking and Clamping
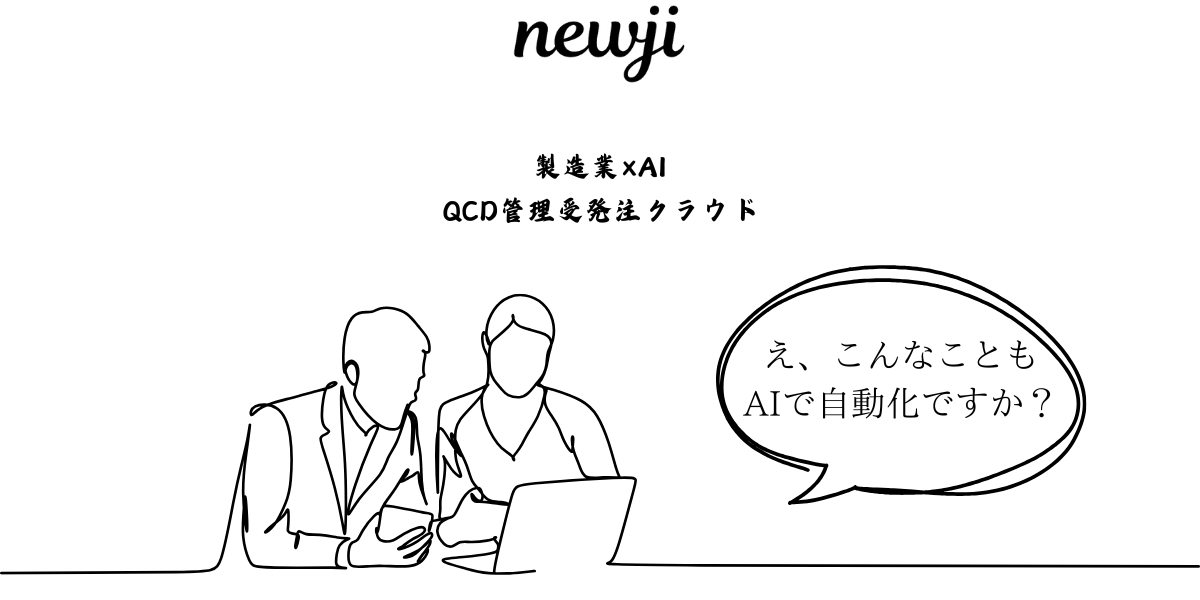
The difference between Chucking and Clamping
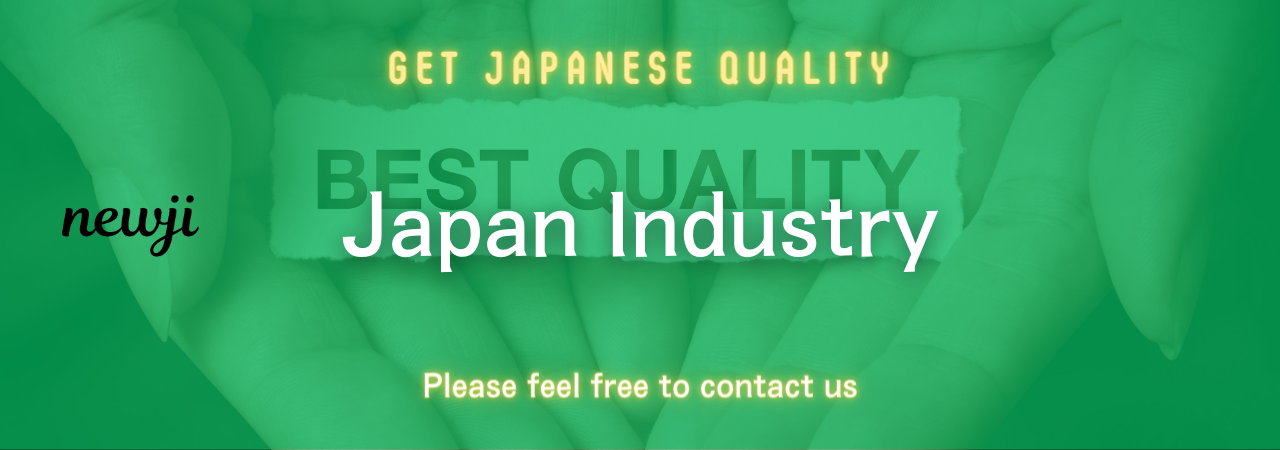
Chucking and clamping are crucial processes in the world of manufacturing and machining.
Though they might sound similar, they have distinct functions and applications.
Understanding the differences between these two can significantly impact productivity and precision in your machining projects.
目次
What is Chucking?
Chucking is a method used primarily in machining, where a component known as a chuck holds a workpiece tightly in place.
The chuck can swivel and rotate, making it ideal for projects that require high degrees of precision and rotational movements.
The most common type of chuck found in machine shops is the three-jaw chuck, which can center and grip the workpiece securely.
Other common types include four-jaw chucks and collet chucks, each offering its own advantages in terms of grip and flexibility.
Types of Chucks
Chucks come in various types, each designed for specific applications. Here are a few:
– **Three-Jaw Chuck**: Ideal for holding round or hexagonal workpieces. This type is self-centering, meaning all jaws move simultaneously.
– **Four-Jaw Chuck**: Better for holding irregularly shaped objects. Each jaw moves independently, allowing for more flexibility.
– **Collet Chuck**: Provides even gripping force around the workpiece, making it ideal for smaller diameter tasks.
Applications of Chucking
Chucking is usually employed in scenarios where round or cylindrical objects need to be machined with high precision.
Common applications include turning operations on a lathe or cylindrical grinding tasks.
Industries like automotive, aerospace, and metalworking often use chucking to create intricate and precise parts.
What is Clamping?
Clamping, on the other hand, is a broader term that refers to any method used to hold a workpiece securely in place during machining.
Unlike chucking, clamping is not limited to rotational tasks and can be used for a variety of operations.
Clamps can be stationary or movable, and they often come in many shapes and sizes to accommodate different types of workpieces.
Types of Clamps
Several types of clamps are used in machining and manufacturing. Here are some of the most common types:
– **C-Clamp**: Known for its versatility, it can hold materials of various shapes and sizes.
– **Toggle Clamp**: Often used in repetitive production tasks where quick clamping and unclamping are needed.
– **Bar Clamp**: Used for large projects, where a workpiece needs to be held in place securely over a wide area.
– **Bench Vise**: A stationary clamp that is often bolted to a workbench. Ideal for tasks requiring stability.
Applications of Clamping
Clamping is used in a wide variety of scenarios, from holding wood in place during woodworking to securing metal sheets in welding operations.
In machining, clamping is essential for operations like milling, drilling, and grinding.
The primary goal of clamping is to ensure that the workpiece remains stationary and secure during the machining process.
Key Differences between Chucking and Clamping
While chucking and clamping may seem similar, they are distinct in multiple aspects.
Method of Operation
Chucking is usually associated with rotational tasks, utilizing chucks that can swivel and rotate.
Clamping, however, is a broader term that applies to various methods of holding a workpiece, usually in a stationary position.
Types of Workpieces
Chucking is commonly used for round or cylindrical objects.
Clamping is more versatile, able to secure workpieces of various shapes and sizes.
Precision and Flexibility
Chucking often offers higher precision for intricate tasks, especially in operations like turning and grinding.
Clamping provides more flexibility, suitable for a wide range of machining operations, albeit sometimes with less precision.
Choosing Between Chucking and Clamping
Your choice between chucking and clamping depends largely on the type of work you’re doing.
Consider the Workpiece Shape
If you’re working with round or cylindrical pieces, chucking is usually the better option.
For other shapes, especially irregular ones, clamping is generally more suitable.
Think About the Operation Required
For tasks requiring rotational movements and high precision, such as turning and cylindrical grinding, chucking is ideal.
For stationary tasks like drilling, milling, or welding, clamping is often the better choice.
Evaluate the Tools Available
The tools you have at your disposal also play a role in your decision.
Machining centers equipped with lathes will benefit more from chucking mechanisms.
Conversely, workshops with milling machines and drill presses will find clamping more useful.
Conclusion
Both chucking and clamping are essential techniques in the world of machining and manufacturing.
While chucking is more specialized for rotational tasks requiring high precision, clamping offers greater versatility for various operations.
Understanding the key differences between these two methods can help you choose the right approach for your specific needs, enhancing both productivity and quality in your projects.
Remember, the right tool and method can make all the difference!
資料ダウンロード
QCD調達購買管理クラウド「newji」は、調達購買部門で必要なQCD管理全てを備えた、現場特化型兼クラウド型の今世紀最高の購買管理システムとなります。
ユーザー登録
調達購買業務の効率化だけでなく、システムを導入することで、コスト削減や製品・資材のステータス可視化のほか、属人化していた購買情報の共有化による内部不正防止や統制にも役立ちます。
NEWJI DX
製造業に特化したデジタルトランスフォーメーション(DX)の実現を目指す請負開発型のコンサルティングサービスです。AI、iPaaS、および先端の技術を駆使して、製造プロセスの効率化、業務効率化、チームワーク強化、コスト削減、品質向上を実現します。このサービスは、製造業の課題を深く理解し、それに対する最適なデジタルソリューションを提供することで、企業が持続的な成長とイノベーションを達成できるようサポートします。
オンライン講座
製造業、主に購買・調達部門にお勤めの方々に向けた情報を配信しております。
新任の方やベテランの方、管理職を対象とした幅広いコンテンツをご用意しております。
お問い合わせ
コストダウンが利益に直結する術だと理解していても、なかなか前に進めることができない状況。そんな時は、newjiのコストダウン自動化機能で大きく利益貢献しよう!
(Β版非公開)