- お役立ち記事
- The difference between CIP (Continuous Improvement Process) and QC (Quality Control)
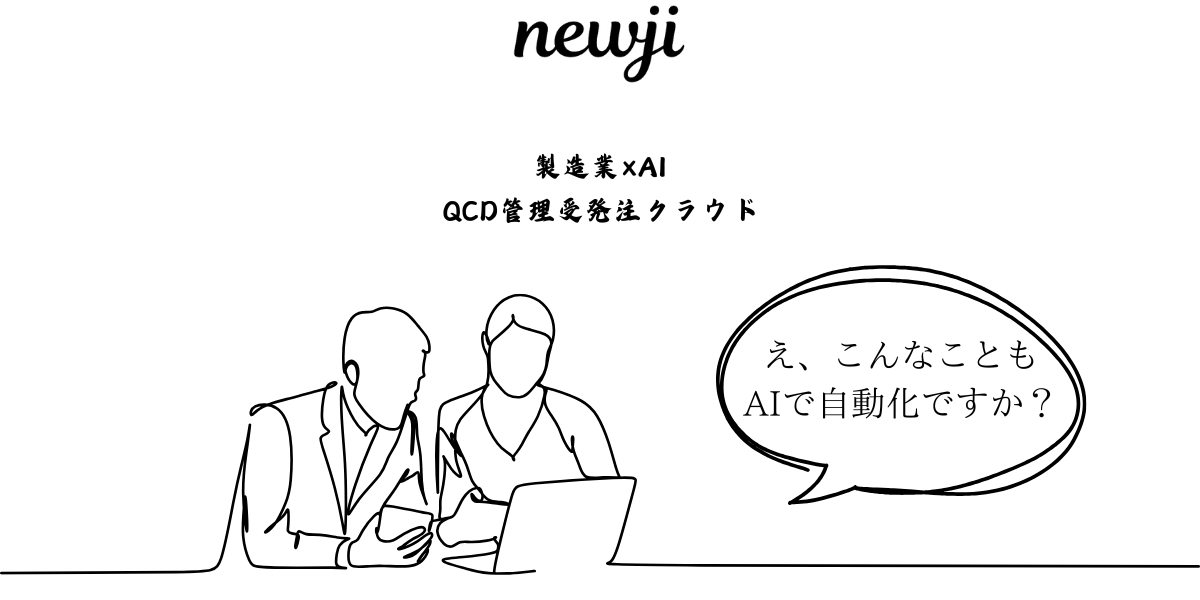
The difference between CIP (Continuous Improvement Process) and QC (Quality Control)
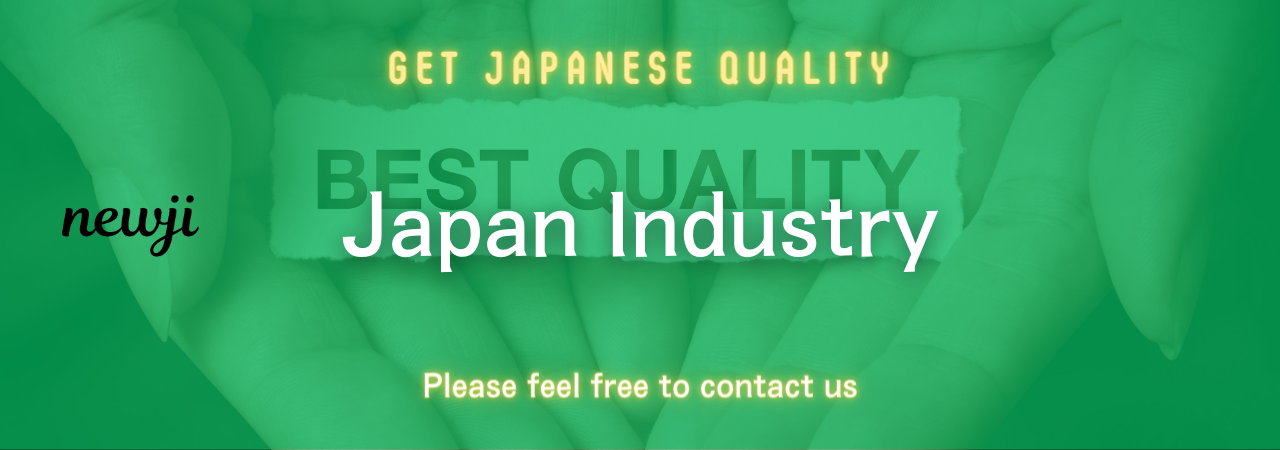
In the business world, there are many ways to ensure that products and services are of high quality and keep improving.
Two essential concepts in this regard are the Continuous Improvement Process (CIP) and Quality Control (QC).
Although both aim to enhance the quality of products and services, they have different methods and focuses.
Understanding these differences can help businesses choose the right approach for their needs.
目次
What is Continuous Improvement Process (CIP)?
The Continuous Improvement Process, often referred to as CIP, is a method used by organizations to make ongoing, incremental improvements to processes, products, or services.
It is focused on continuously enhancing every aspect of a business by encouraging regular, small changes rather than large-scale changes.
Principles of CIP
CIP is built on several key principles that guide its implementation:
1. **Incremental Improvements:** Instead of making big changes all at once, CIP stresses the importance of making small, incremental improvements over time.
These smaller changes are easier to manage and can quickly add up to significant advancements.
2. **Employee Involvement:** One of the core beliefs of CIP is that everyone in an organization should be involved in the improvement process.
Employees at all levels have valuable insights and should be encouraged to suggest and implement changes.
3. **Customer Focus:** All improvements should aim to enhance the customer experience.
Understanding the needs and wants of customers is crucial in directing efforts towards meaningful changes.
4. **Data-Driven:** Decisions regarding improvements should be based on data and factual information rather than assumptions.
Accurate data helps identify problem areas and measure the success of changes.
Benefits of CIP
Implementing CIP can bring several benefits to an organization:
– **Enhanced Efficiency:** Continuous improvements can streamline processes, reducing waste and increasing efficiency.
– **Better Quality:** By constantly refining processes and products, organizations can ensure consistent quality.
– **Employee Morale:** Involving employees in decision-making and improvement efforts can boost their morale and sense of ownership.
– **Adaptability:** CIP helps businesses stay flexible and adapt to changing market conditions and customer preferences.
What is Quality Control (QC)?
Quality Control, or QC, is a set of procedures and processes used to ensure that a product or service meets certain quality standards.
QC is typically focused on identifying defects and ensuring that the output meets the required specifications.
Principles of QC
Several key principles guide the practice of Quality Control:
1. **Inspection:** QC involves the regular inspection of products and processes to identify any defects or deviations from the standards.
2. **Testing:** Products often go through rigorous testing to ensure they meet specified criteria and perform as expected.
3. **Standards Compliance:** QC ensures that the products or services conform to predefined quality standards and regulations.
4. **Feedback Loop:** Information from inspections and tests provides a feedback loop that helps in making necessary adjustments to maintain quality.
Benefits of QC
Quality Control offers various advantages to businesses:
– **Consistent Quality:** QC helps maintain a consistent level of quality in products, ensuring customer satisfaction.
– **Error Reduction:** Through regular inspection and testing, QC minimizes the chances of errors and defects.
– **Regulatory Compliance:** Adhering to quality standards and regulations can prevent legal issues and enhance the company’s reputation.
– **Customer Trust:** Consistently high-quality products build customer trust and loyalty.
Key Differences between CIP and QC
While both CIP and QC aim to improve quality, they differ significantly in their approach and focus:
Scope and Nature of Improvements
CIP focuses on continuous, incremental improvements across all areas of a business.
It emphasizes ongoing efforts to enhance processes, products, and services.
In contrast, QC is more focused on the final output.
It aims to ensure that products meet defined standards through inspection and testing.
Employee Involvement
CIP encourages involvement from all employees at every level of the organization.
It values the insights and suggestions of everyone in the company.
QC, however, is often limited to specific departments or teams responsible for monitoring and maintaining quality.
Focus on Processes vs. Products
CIP is process-oriented, always looking for ways to make each step better.
QC is more product-oriented, concentrating on the final output to ensure it meets quality standards.
Proactive vs. Reactive Approach
CIP is proactive, aiming to prevent problems before they occur through ongoing improvements.
QC is more reactive, identifying and addressing defects after they have occurred to ensure standard compliance.
Conclusion
Both the Continuous Improvement Process (CIP) and Quality Control (QC) are essential in the business world for maintaining and improving quality.
Understanding the distinctions between them helps in selecting the right strategy for a company’s specific needs.
CIP’s focus on incremental improvements and employee involvement makes it a broader, more inclusive approach.
In contrast, QC’s concentration on product inspection and defect prevention ensures that final outputs meet the required standards.
By balancing these two approaches, businesses can achieve a harmonious blend of continuous enhancement and consistent quality.
This balance, in turn, leads to better products, greater customer satisfaction, and sustained success.
資料ダウンロード
QCD調達購買管理クラウド「newji」は、調達購買部門で必要なQCD管理全てを備えた、現場特化型兼クラウド型の今世紀最高の購買管理システムとなります。
ユーザー登録
調達購買業務の効率化だけでなく、システムを導入することで、コスト削減や製品・資材のステータス可視化のほか、属人化していた購買情報の共有化による内部不正防止や統制にも役立ちます。
NEWJI DX
製造業に特化したデジタルトランスフォーメーション(DX)の実現を目指す請負開発型のコンサルティングサービスです。AI、iPaaS、および先端の技術を駆使して、製造プロセスの効率化、業務効率化、チームワーク強化、コスト削減、品質向上を実現します。このサービスは、製造業の課題を深く理解し、それに対する最適なデジタルソリューションを提供することで、企業が持続的な成長とイノベーションを達成できるようサポートします。
オンライン講座
製造業、主に購買・調達部門にお勤めの方々に向けた情報を配信しております。
新任の方やベテランの方、管理職を対象とした幅広いコンテンツをご用意しております。
お問い合わせ
コストダウンが利益に直結する術だと理解していても、なかなか前に進めることができない状況。そんな時は、newjiのコストダウン自動化機能で大きく利益貢献しよう!
(Β版非公開)