- お役立ち記事
- The difference between Defective Products and Non-conforming Products
The difference between Defective Products and Non-conforming Products
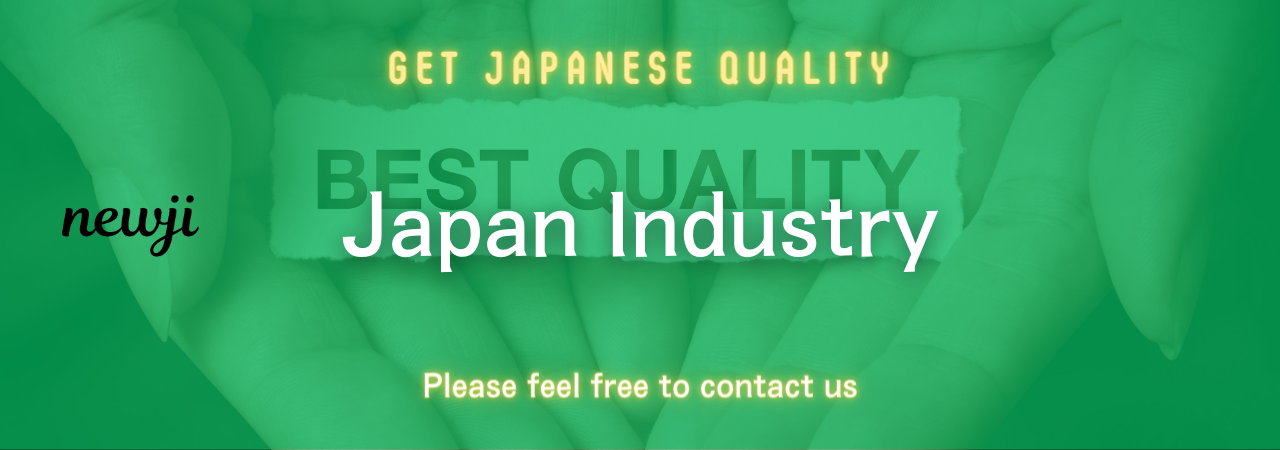
When discussing manufacturing, quality control, and supply chain management, the terms “defective products” and “non-conforming products” often come up.
While they might seem similar at first glance, there are distinct differences between these two categories.
Understanding these differences is crucial for businesses to maintain quality, comply with standards, and keep customers satisfied.
目次
What are Defective Products?
Defective products are items that fail to work as intended.
They may have structural flaws, do not perform their function, or are dangerous to use.
Customers who purchase defective products usually notice the issue almost immediately or after short-term use.
Typically, a defective product cannot be repaired and needs to be replaced or refunded.
For businesses, defective products can lead to recalls, customer dissatisfaction, and potential legal issues.
Types of Defective Products
Various factors can make a product defective.
These include manufacturing defects, design defects, and marketing defects.
1. **Manufacturing Defects:** These occur during the production process.
For example, a batch of smartphones might leave the factory with faulty batteries.
2. **Design Defects:** These flaws are inherent in the product’s design.
For instance, a piece of furniture might be unstable due to poor engineering.
3. **Marketing Defects:** These arise from incorrect labeling, insufficient instructions, or improper safety warnings.
For example, a chemical product without proper usage guidelines could be dangerous.
What are Non-conforming Products?
Non-conforming products do not meet the specified standards or requirements but are not necessarily defective in function or safety.
They do not align with the parameters set out by the manufacturing protocols, industry standards, or customer specifications.
In many cases, non-conforming products can still be used but may not be suitable for their intended purpose or market.
These products often undergo rework, repair, or reclassification to meet the necessary standards.
Examples of Non-conforming Products
Non-conforming products come in various forms.
Here are a few examples to illustrate:
1. **Dimensional Deviation:** A mechanical part might be a few millimeters off the specified size, affecting its fit and function in an assembly.
2. **Material Non-conformity:** A product made from a different material than specified could affect its durability or appearance.
For example, a metal part might be constructed from aluminum instead of stainless steel.
3. **Color Variation:** If a batch of clothing comes in a different shade than ordered, it is non-conforming but not necessarily defective.
The Importance of Differentiating Between the Two
Recognizing the difference between defective and non-conforming products helps businesses manage quality control effectively.
Each type of issue requires different corrective actions and strategies.
Quality Control and Assurance
Implementing quality control measures ensures that products meet certain standards before reaching the customer.
By distinguishing between defects and non-conformities, a business can better allocate resources to address specific problems.
For example, defective products may necessitate recalls and refunds, while non-conforming products might just require adjustments or rework.
Reducing Costs
Addressing non-conformities early in the production process can prevent costly mistakes down the line.
By identifying and correcting these issues before the product reaches the market, businesses can save money on returns, repairs, and damaged reputation.
Customer Satisfaction and Trust
Customers expect high-quality products that work as intended.
Delivering defective products can result in dissatisfaction, negative reviews, and loss of trust.
On the other hand, addressing non-conformities ensures that the products meet customer specifications, maintaining customer satisfaction.
Regulatory Compliance
Many industries have strict regulations regarding product quality and safety.
Non-conforming products might not breach regulations but could still fall short of customer expectations.
Defective products, however, can lead to severe consequences like fines, legal actions, and loss of certifications.
By distinguishing between the two, businesses can better navigate regulatory landscapes.
Strategies for Managing Defective and Non-conforming Products
To effectively manage defective and non-conforming products, businesses can adopt several strategies.
Implementing Rigorous Testing
Regular testing during and after production can help identify issues early.
This approach ensures that products meet the necessary standards and specifications before they reach the market.
Continuous Improvement
Adopting a culture of continuous improvement can help businesses enhance their production processes, reducing the likelihood of defects and non-conformities.
Techniques like Lean Manufacturing and Six Sigma can be incredibly effective.
Supplier Quality Management
Working closely with suppliers to ensure the quality of raw materials and components can prevent non-conformities.
Regular audits and performance reviews can maintain high standards across the supply chain.
Effective Feedback Loops
Creating channels for customer feedback can help businesses quickly identify and rectify issues.
Hearing directly from customers provides invaluable insights into product performance in real-world conditions.
Training and Skill Development
Investing in employee training ensures that everyone involved in the production process understands quality standards, best practices, and the importance of distinguishing between defective and non-conforming products.
Conclusion
In summary, while defective and non-conforming products might seem similar, they are distinct issues that require different management strategies.
Defective products fail to work as intended and often necessitate recalls or refunds.
Non-conforming products do not meet specified standards but may still function adequately.
Understanding these differences is essential for maintaining quality control, reducing costs, ensuring customer satisfaction, and complying with regulations.
By implementing rigorous testing, continuous improvement, supplier quality management, and effective feedback loops, businesses can better manage product quality and minimize the occurrence of defects and non-conformities.
資料ダウンロード
QCD調達購買管理クラウド「newji」は、調達購買部門で必要なQCD管理全てを備えた、現場特化型兼クラウド型の今世紀最高の購買管理システムとなります。
ユーザー登録
調達購買業務の効率化だけでなく、システムを導入することで、コスト削減や製品・資材のステータス可視化のほか、属人化していた購買情報の共有化による内部不正防止や統制にも役立ちます。
NEWJI DX
製造業に特化したデジタルトランスフォーメーション(DX)の実現を目指す請負開発型のコンサルティングサービスです。AI、iPaaS、および先端の技術を駆使して、製造プロセスの効率化、業務効率化、チームワーク強化、コスト削減、品質向上を実現します。このサービスは、製造業の課題を深く理解し、それに対する最適なデジタルソリューションを提供することで、企業が持続的な成長とイノベーションを達成できるようサポートします。
オンライン講座
製造業、主に購買・調達部門にお勤めの方々に向けた情報を配信しております。
新任の方やベテランの方、管理職を対象とした幅広いコンテンツをご用意しております。
お問い合わせ
コストダウンが利益に直結する術だと理解していても、なかなか前に進めることができない状況。そんな時は、newjiのコストダウン自動化機能で大きく利益貢献しよう!
(Β版非公開)