- お役立ち記事
- The difference between Die Casting and Continuous Casting
月間76,176名の
製造業ご担当者様が閲覧しています*
*2025年3月31日現在のGoogle Analyticsのデータより
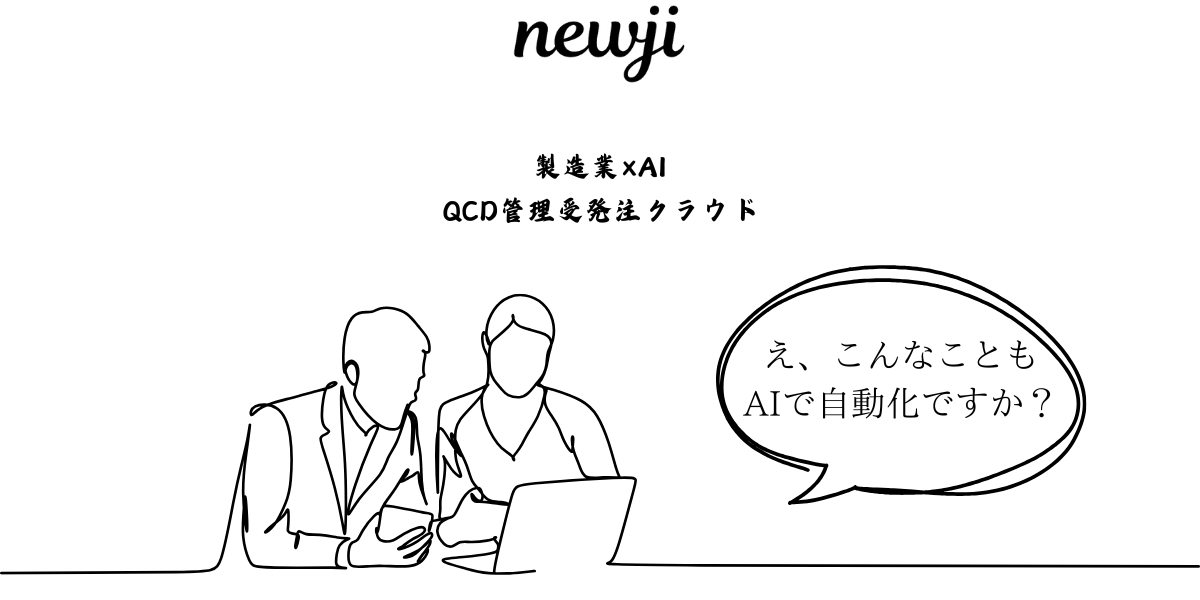
The difference between Die Casting and Continuous Casting
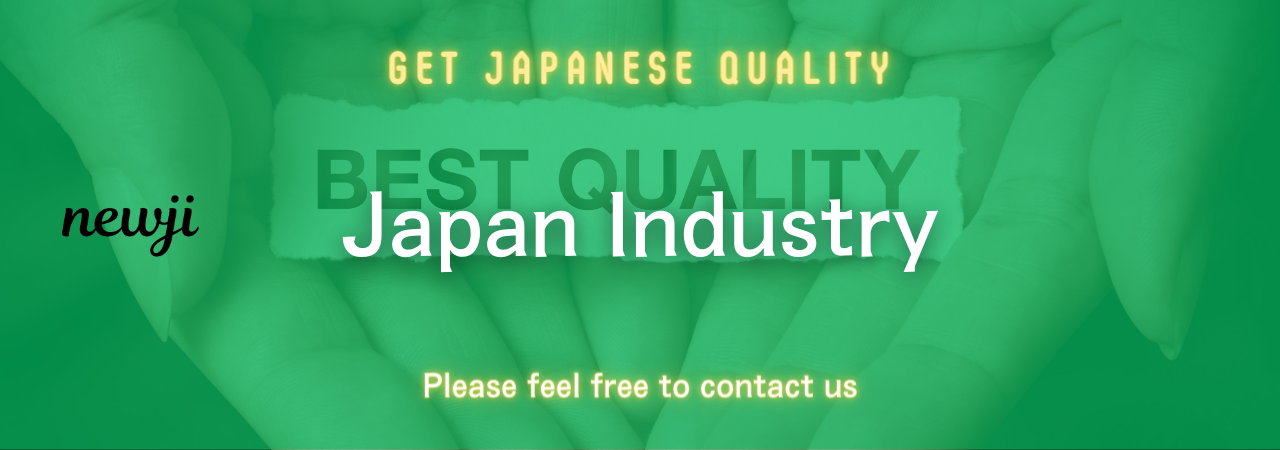
Die casting and continuous casting are two important methods used in the manufacturing industry to create metal products.
While both processes focus on molding and shaping metals, they are fundamentally different in terms of their methods, applications, and benefits.
Understanding these differences can help industries choose the right process for their specific needs.
Let’s dive into the details of both processes and explore what sets them apart.
目次
What is Die Casting?
Die casting is a manufacturing process where molten metal is injected into a mold cavity under high pressure.
The molds, also known as dies, are usually made from durable metal materials like steel.
Die casting is widely used to create complex geometries, and it is particularly effective for mass production.
Steps Involved in Die Casting:
Firstly, prepare the die by lubricating it to facilitate easy removal of the cast part.
This lubrication also helps to extend the lifespan of the die.
Secondly, molten metal is injected into the mold cavity under high pressure.
Once the metal enters the mold, it quickly cools and solidifies to take the shape of the cavity.
After the metal has solidified, the die is opened, and the cast part is ejected.
Finally, any excess material, known as flash, is trimmed to complete the process.
Types of Die Casting:
There are mainly two types of die casting: hot chamber and cold chamber.
**Hot Chamber Die Casting:** In this method, the metal is melted in a furnace attached to the die casting machine.
The molten metal is then injected directly into the mold under pressure.
This method is ideal for metals with low melting points like zinc and magnesium.
**Cold Chamber Die Casting:** In this method, the molten metal is poured into a separate chamber before being injected into the mold.
This is more suitable for metals with high melting points like aluminum.
Advantages of Die Casting:
Die casting allows for high-speed production, making it ideal for mass production.
It offers excellent dimensional accuracy and smooth surface finishes, reducing the need for additional machining. Complex shapes and intricate designs can be easily achieved, broadening the range of possible applications.
The process also results in strong and durable parts, making it suitable for demanding applications like automotive components.
What is Continuous Casting?
Continuous casting, also known as strand casting, is a process where molten metal is solidified into a continuous strand or slab.
This strand is then cut to the desired length, making the process highly efficient for large-scale production.
Steps Involved in Continuous Casting:
To begin with, molten metal is poured into a tundish, a reservoir that serves as an intermediary between the ladle and the mold.
The metal flows from the tundish into a water-cooled mold, where it begins to solidify.
As the metal exits the mold, it continues to cool and harden as it is pulled through a series of rollers.
Finally, the continuous strand is cut into specific lengths using a torch or mechanical saw.
Types of Continuous Casting:
The most common types of continuous casting include vertical continuous casting, horizontal continuous casting, and distributed casting.
**Vertical Continuous Casting:** In this method, the metal is cast in a vertical direction, making it ideal for producing billets and blooms.
**Horizontal Continuous Casting:** As the name suggests, this method involves casting the metal in a horizontal direction, and it is commonly used for creating slabs and thin strips.
**Distributed Casting:** It involves dividing the molten metal into multiple strands, allowing for the simultaneous production of several smaller products.
Advantages of Continuous Casting:
Continuous casting ensures a consistent and high-quality product by minimizing defects such as cracks and inclusions.
The process is highly efficient and economical for producing large quantities of metal products.
Improved metallurgical properties, such as uniform composition and grain structure, are achieved through continuous casting.
It also reduces material wastage, making it an environmentally friendly option.
Key Differences Between Die Casting and Continuous Casting:
**Process Methodology:**
Die casting involves injecting molten metal into a mold under high pressure, whereas continuous casting involves the continuous solidification of molten metal into a strand.
**Applications:**
Die casting is ideal for creating intricate shapes and complex geometries, making it suitable for automotive components, electronics, and household appliances.
On the other hand, continuous casting is better suited for producing large quantities of simple shapes like billets, slabs, and rods.
**Production Speed:**
Die casting allows for rapid production but is generally limited to smaller parts.
Continuous casting, however, can produce large quantities at a faster rate, making it ideal for steel and aluminum industries.
**Material Utilization:**
Die casting often results in some material waste due to the flashing process, whereas continuous casting minimizes material wastage.
**Strength and Durability:**
Die cast parts are usually strong and durable, ideal for high-performance applications.
Continuous cast products have excellent metallurgical properties but may require additional processing for specific applications.
Conclusion:
Both die casting and continuous casting offer unique advantages and are critical to the manufacturing industry.
Die casting excels in producing complex and intricate parts with high precision, making it ideal for various consumer products and industrial applications.
Continuous casting, on the other hand, is unparalleled in its efficiency and ability to produce large quantities of metal products, especially for the steel and aluminum industries.
Understanding the differences between these two methods can help manufacturers choose the most suitable process for their specific needs, ensuring optimal efficiency, quality, and cost-effectiveness.
Whether you’re in the automotive sector, electronics, or heavy industry, both die casting and continuous casting offer invaluable benefits that drive innovation and productivity.
By leveraging the strengths of each method, industries can achieve a higher level of performance and sustainability in their manufacturing processes.
資料ダウンロード
QCD管理受発注クラウド「newji」は、受発注部門で必要なQCD管理全てを備えた、現場特化型兼クラウド型の今世紀最高の受発注管理システムとなります。
ユーザー登録
受発注業務の効率化だけでなく、システムを導入することで、コスト削減や製品・資材のステータス可視化のほか、属人化していた受発注情報の共有化による内部不正防止や統制にも役立ちます。
NEWJI DX
製造業に特化したデジタルトランスフォーメーション(DX)の実現を目指す請負開発型のコンサルティングサービスです。AI、iPaaS、および先端の技術を駆使して、製造プロセスの効率化、業務効率化、チームワーク強化、コスト削減、品質向上を実現します。このサービスは、製造業の課題を深く理解し、それに対する最適なデジタルソリューションを提供することで、企業が持続的な成長とイノベーションを達成できるようサポートします。
製造業ニュース解説
製造業、主に購買・調達部門にお勤めの方々に向けた情報を配信しております。
新任の方やベテランの方、管理職を対象とした幅広いコンテンツをご用意しております。
お問い合わせ
コストダウンが利益に直結する術だと理解していても、なかなか前に進めることができない状況。そんな時は、newjiのコストダウン自動化機能で大きく利益貢献しよう!
(β版非公開)