- お役立ち記事
- The difference between Drawing and Rolling
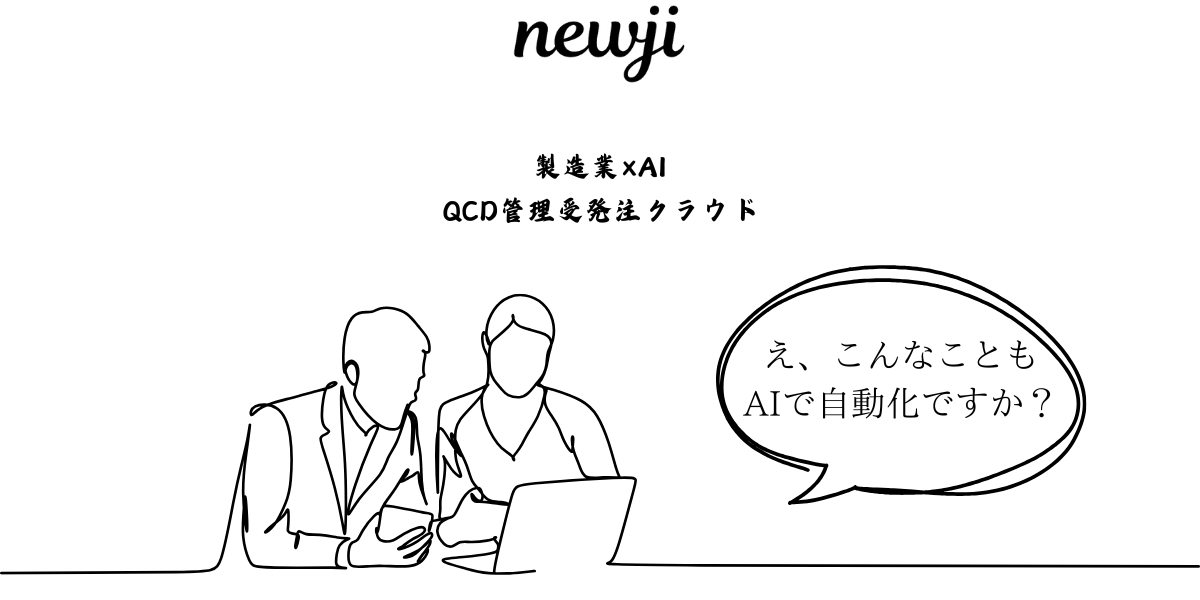
The difference between Drawing and Rolling
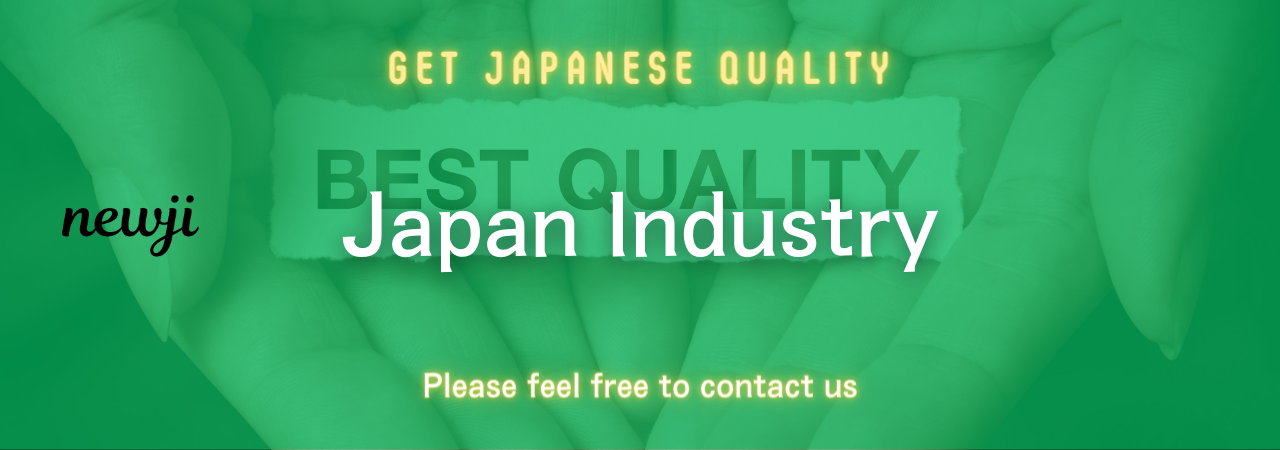
Drawing and rolling are two fundamental metalworking processes that play vital roles in shaping and forming metals for various applications.
Understanding the differences between these two methods can help individuals appreciate how metals transform from raw materials into finished products.
目次
What is Drawing?
Drawing is a metalworking process that involves pulling a metal piece through a die to reduce its diameter and increase its length.
The force applied in the drawing process is tensile, meaning it pulls the metal in a specific direction to achieve the desired shape.
This method is often used to create wire, rods, and tubes.
The Drawing Process
In drawing, the metal is first prepped to ensure it is clean and free of any surface impurities.
It is then fed through a die, which has a specific diameter smaller than the original metal piece.
As the metal is pulled through the die, it elongates and its diameter decreases.
Depending on the desired final shape, the metal may go through multiple drawing stages.
Types of Drawing
There are several types of drawing processes, including bar drawing, tube drawing, and wire drawing.
Wire drawing is perhaps the most common, where metal rods are drawn into thin wire used in electrical and construction applications.
Tube drawing, on the other hand, involves drawing a tube through a die to achieve precise dimensions needed for various industrial applications.
Applications of Drawing
Drawing is utilized in industries requiring high precision and strength, such as aerospace, automotive, and electronics.
For example, in the automotive industry, drawn wires are used in tire cords, which need to be both flexible and strong.
In electronics, drawn wires are essential for making electrical connectors and components.
What is Rolling?
Rolling is another widely used metalworking process that involves passing metal between a pair of rollers to reduce its thickness or alter its cross-section.
Unlike drawing, the force applied in rolling is compressive, meaning it squeezes the metal to achieve the desired shape.
This process is commonly used for producing sheet metal, structural beams, and rails.
The Rolling Process
Rolling begins with a large metal slab or ingot, which is fed into the rolling mill.
The rollers apply significant pressure to compress and elongate the metal.
Depending on the desired final shape, the metal may pass through multiple sets of rollers in a process called multi-pass rolling.
The rollers can be adjusted to different gaps, which determines the final thickness of the metal.
Types of Rolling
Rolling can be classified into hot rolling and cold rolling.
In hot rolling, the metal is heated above its recrystallization temperature, making it easier to shape but less precise.
Cold rolling, performed at or near room temperature, yields a smoother surface finish and higher dimensional accuracy.
Applications of Rolling
Rolling is essential in manufacturing industries to produce sheets, strips, and plates used in construction, shipbuilding, and automotive sectors.
For instance, hot-rolled steel is often used in structural applications like I-beams and railroad tracks, while cold-rolled steel is commonly used for more precise applications like home appliances and car bodies.
Key Differences Between Drawing and Rolling
Type of Force Applied
One of the primary differences between drawing and rolling is the type of force used.
Drawing relies on tensile forces to pull the metal through a die, whereas rolling uses compressive forces to squeeze the metal between rollers.
Material Shape and Output
Drawing is typically used for producing elongated shapes like wires, rods, and tubes with smaller diameters.
In contrast, rolling is used for producing flat products like sheets and strips, as well as long structural shapes such as beams and rails.
Process Temperature
While both drawing and rolling can be done at various temperatures, rolling is often categorized into hot and cold processes.
Drawing is generally performed at room temperature, although some materials may require heating to reduce their resistance to deformation.
Precision and Surface Finish
Cold drawing and cold rolling both provide high precision and excellent surface finishes.
However, hot rolling, while essential for large structural components, is less precise and has a rougher surface finish compared to cold-rolled or cold-drawn products.
Choosing the Right Process
The choice between drawing and rolling depends on several factors, including the desired shape, material properties, and required precision.
For applications needing high precision and smaller diameters, drawing is often the go-to method.
Rolling is preferable for producing large flat sections and long structural components that require high volume and faster production rates.
In summary, both drawing and rolling are critical metalworking processes, each with its unique advantages and applications.
Understanding their differences allows manufacturers to select the most suitable process for their specific needs, ensuring optimal performance and quality in the finished metal products.
資料ダウンロード
QCD調達購買管理クラウド「newji」は、調達購買部門で必要なQCD管理全てを備えた、現場特化型兼クラウド型の今世紀最高の購買管理システムとなります。
ユーザー登録
調達購買業務の効率化だけでなく、システムを導入することで、コスト削減や製品・資材のステータス可視化のほか、属人化していた購買情報の共有化による内部不正防止や統制にも役立ちます。
NEWJI DX
製造業に特化したデジタルトランスフォーメーション(DX)の実現を目指す請負開発型のコンサルティングサービスです。AI、iPaaS、および先端の技術を駆使して、製造プロセスの効率化、業務効率化、チームワーク強化、コスト削減、品質向上を実現します。このサービスは、製造業の課題を深く理解し、それに対する最適なデジタルソリューションを提供することで、企業が持続的な成長とイノベーションを達成できるようサポートします。
オンライン講座
製造業、主に購買・調達部門にお勤めの方々に向けた情報を配信しております。
新任の方やベテランの方、管理職を対象とした幅広いコンテンツをご用意しております。
お問い合わせ
コストダウンが利益に直結する術だと理解していても、なかなか前に進めることができない状況。そんな時は、newjiのコストダウン自動化機能で大きく利益貢献しよう!
(Β版非公開)