- お役立ち記事
- The difference between Electrical Discharge Machining (EDM) and Electron Beam Machining (EBM)
月間76,176名の
製造業ご担当者様が閲覧しています*
*2025年3月31日現在のGoogle Analyticsのデータより
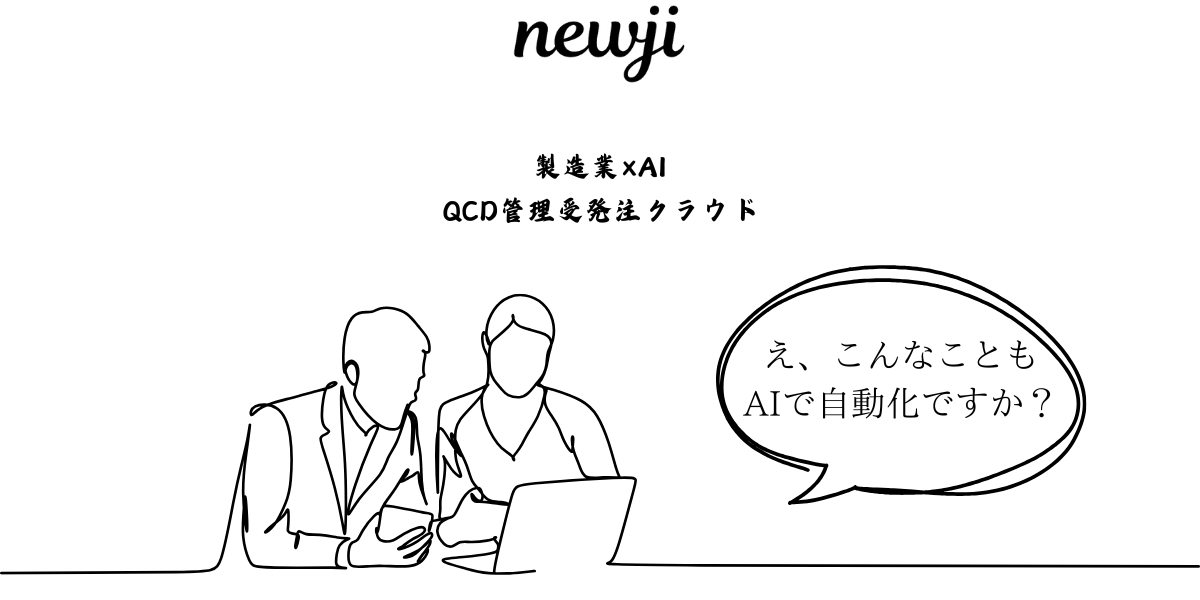
The difference between Electrical Discharge Machining (EDM) and Electron Beam Machining (EBM)
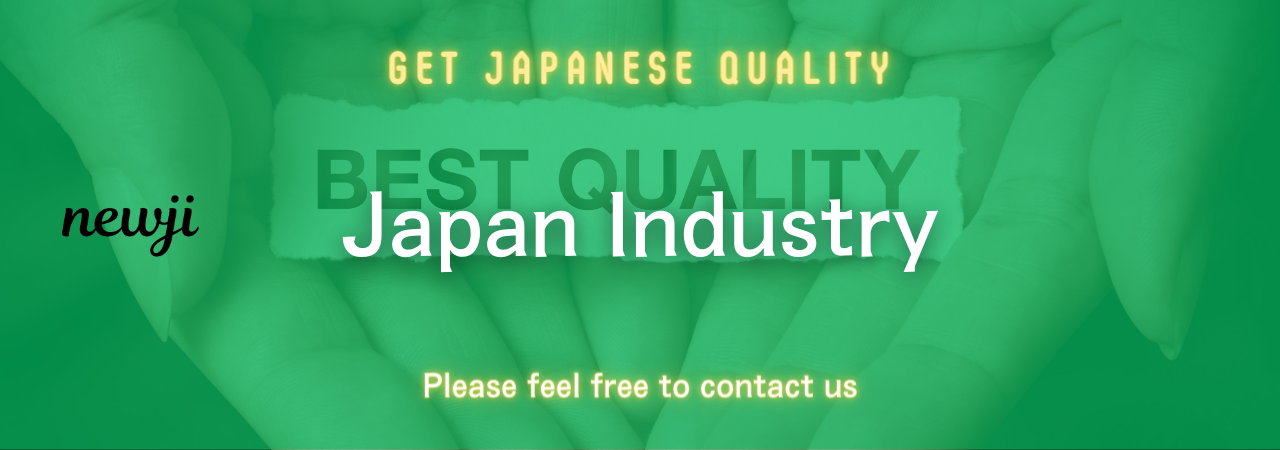
Electrical Discharge Machining (EDM) and Electron Beam Machining (EBM) are two advanced and distinct manufacturing processes used in precision machining.
Both of these methods are non-traditional, meaning they do not rely on mechanical cutting tools but rather on energy-based techniques.
Despite serving similar purposes of high-precision material removal, they operate on fundamentally different principles.
In this article, we’ll explore what makes EDM and EBM unique and how they differ from each other.
目次
What is Electrical Discharge Machining (EDM)?
Electrical Discharge Machining, commonly known as EDM, is a process that uses electrical discharges or sparks to erode material.
This method is particularly useful for working with hard materials like titanium or tungsten.
In EDM, an electrode and the workpiece are submerged in a dielectric fluid.
When a voltage is applied, it generates a spark that erodes a tiny portion of the workpiece.
The dielectric fluid serves multiple functions: it flushes away debris, cools the material, and facilitates spark generation.
Advantages of EDM
One of the primary advantages of EDM is its precision.
It can achieve very tight tolerances and intricate shapes, making it ideal for applications like mold making, aerospace components, and medical devices.
Additionally, because no physical cutting tool comes into contact with the workpiece, there is no mechanical stress or deformation.
Disadvantages of EDM
However, EDM does have its limitations.
The process is relatively slow compared to traditional machining methods, which means it may not be suitable for high-volume production.
The wear on electrodes and the need for an efficient dielectric fluid system also add to the cost.
What is Electron Beam Machining (EBM)?
Electron Beam Machining (EBM) is another non-traditional machining process but operates on entirely different principles.
EBM uses a focused beam of high-velocity electrons to impact and erode the material.
This process takes place in a vacuum chamber because electrons can scatter when they come into contact with air molecules.
When the high-velocity electrons strike the workpiece, they generate heat that melts and vaporizes the material.
Advantages of EBM
EBM is incredibly fast and can work on extremely hard materials with ease, including metals like titanium and tungsten.
Since it can be precisely controlled, EBM is highly suited for applications that require intricate and detailed machining, such as in the aerospace or semiconductor industries.
The process also results in a very clean cut, reducing the need for subsequent finishing operations.
Disadvantages of EBM
One significant downside of EBM is the necessity for a vacuum environment, which makes the setup and maintenance more complex and expensive.
Also, the intense energy involved can lead to thermal damage, which might not be suitable for all materials or applications.
Comparing EDM and EBM
Understanding the differences between EDM and EBM can help you choose the right method for your specific needs.
Principles of Operation
The fundamental distinction lies in how each process removes material.
EDM relies on electrical discharges between an electrode and the workpiece in a dielectric fluid, while EBM uses a beam of electrons in a vacuum chamber.
Material Suitability
Both methods are suitable for hard materials, but their appropriateness can vary depending on the application and material characteristics.
For instance, EDM can work with both conductive and non-conductive materials, but it generally performs better with metals.
EBM is more versatile in terms of material hardness but can cause thermal damage, which may not be ideal for materials sensitive to heat.
Precision and Speed
When it comes to precision, both EDM and EBM are highly accurate.
However, EDM is usually slower, making it less suited for high-volume production.
EBM, on the other hand, offers faster material removal rates, which can be advantageous for high-speed manufacturing.
Applications of EDM and EBM
The choice between EDM and EBM often depends on the specific requirements of the application.
Common EDM Applications
EDM is widely used in mold making, aerospace, and medical device manufacturing.
Its ability to produce intricate shapes and tight tolerances makes it invaluable for these fields.
Moreover, because it imparts no physical stress on the material, it is ideal for delicate or brittle materials.
Common EBM Applications
EBM finds its niche in industries requiring extreme precision and high-speed material removal, such as aerospace and semiconductor fabrication.
The clean cuts and fast operation times make it suitable for complex components that require minimal post-processing.
Choosing the Right Machining Method
When deciding between EDM and EBM, consider your specific needs and constraints.
Cost Considerations
EDM setups are generally less complex and less costly than EBM systems.
However, the slower material removal rates can translate to higher overall costs for large-scale production.
EBM requires a vacuum environment, which increases the initial setup and maintenance costs but might be justified by the faster processing times.
Material and Precision Needs
If your work involves highly detailed designs and requires extreme precision, both EDM and EBM are excellent choices.
However, if you are working with heat-sensitive materials, EDM may be the better option due to its lower risk of thermal damage.
In contrast, for high-speed and high-volume production involving extremely hard materials, EBM could be more suitable.
In conclusion, both Electrical Discharge Machining (EDM) and Electron Beam Machining (EBM) are powerful, non-traditional machining methods, each with its own set of advantages and limitations.
Understanding these differences can help you make an informed decision that aligns with your project requirements and constraints.
資料ダウンロード
QCD管理受発注クラウド「newji」は、受発注部門で必要なQCD管理全てを備えた、現場特化型兼クラウド型の今世紀最高の受発注管理システムとなります。
ユーザー登録
受発注業務の効率化だけでなく、システムを導入することで、コスト削減や製品・資材のステータス可視化のほか、属人化していた受発注情報の共有化による内部不正防止や統制にも役立ちます。
NEWJI DX
製造業に特化したデジタルトランスフォーメーション(DX)の実現を目指す請負開発型のコンサルティングサービスです。AI、iPaaS、および先端の技術を駆使して、製造プロセスの効率化、業務効率化、チームワーク強化、コスト削減、品質向上を実現します。このサービスは、製造業の課題を深く理解し、それに対する最適なデジタルソリューションを提供することで、企業が持続的な成長とイノベーションを達成できるようサポートします。
製造業ニュース解説
製造業、主に購買・調達部門にお勤めの方々に向けた情報を配信しております。
新任の方やベテランの方、管理職を対象とした幅広いコンテンツをご用意しております。
お問い合わせ
コストダウンが利益に直結する術だと理解していても、なかなか前に進めることができない状況。そんな時は、newjiのコストダウン自動化機能で大きく利益貢献しよう!
(β版非公開)