- お役立ち記事
- The difference between Equipment Inspection and Equipment Diagnosis
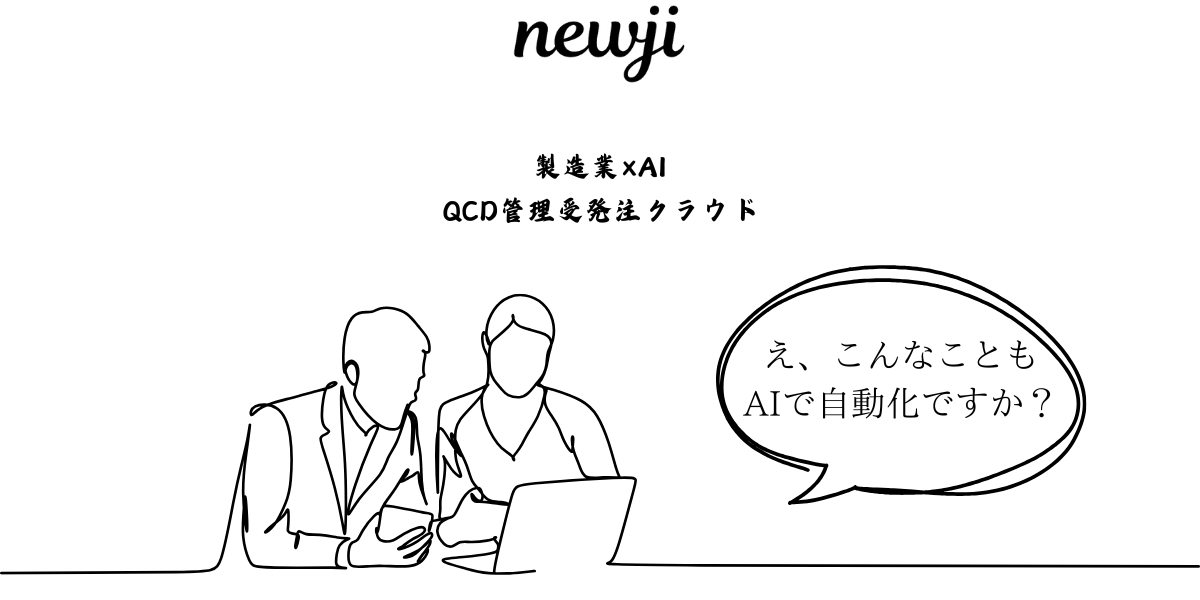
The difference between Equipment Inspection and Equipment Diagnosis
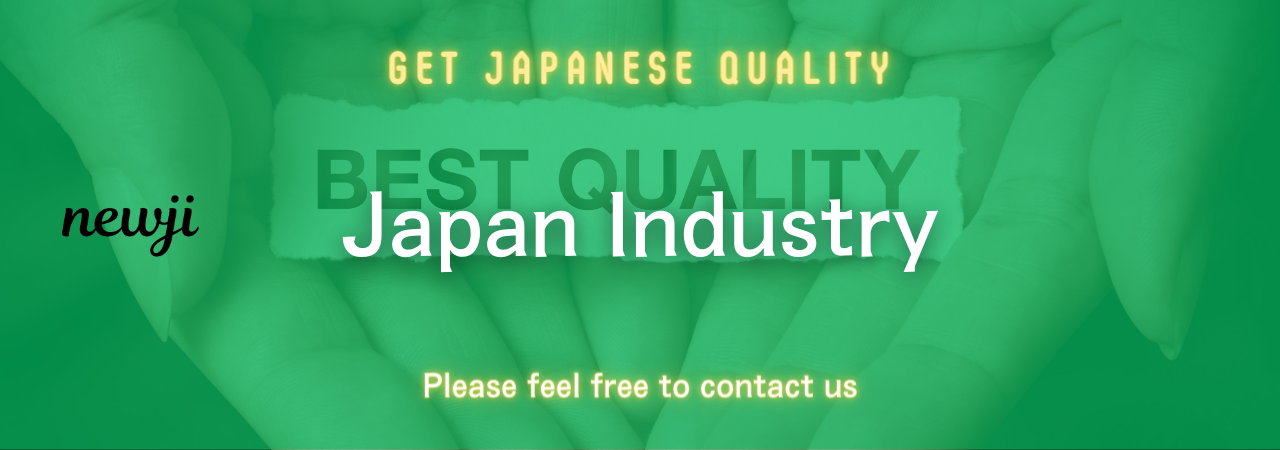
In any industrial setting, keeping machinery running smoothly is crucial to maintaining productivity and safety.
To achieve this goal, businesses must regularly assess their equipment.
While terms like “equipment inspection” and “equipment diagnosis” are often used interchangeably, they refer to different processes.
Understanding the differences between these two procedures can help companies optimize their maintenance strategies.
This article will explore both concepts in detail.
目次
What is Equipment Inspection?
Equipment inspection is a systematic process of evaluating the condition of machinery and other industrial equipment.
Typically performed on a periodic basis, it involves visual checks, measurements, and testing to assess the current state of the equipment.
Main Objectives
The primary goals of equipment inspection are to ensure operational efficiency and safety.
Inspections help identify wear and tear, corrosion, alignment issues, and other potential problems before they escalate into major faults.
By catching these issues early, businesses can save on costly repairs and avoid unplanned downtime.
Types of Inspections
There are several different types of equipment inspections, each tailored to specific needs:
– **Visual Inspections**: Involves examining the equipment with the naked eye to identify obvious signs of damage or wear.
– **Operational Inspections**: These inspections focus on the functioning of the equipment, such as how it performs under normal operating conditions.
– **Safety Inspections**: Aimed at identifying hazards that could pose a risk to workers or the environment.
– **Regulatory Inspections**: Required to comply with industry standards and legal requirements.
Inspection Tools
Various tools and techniques are used during equipment inspections:
– **Thermal Imaging Cameras**: Detect temperature variations to identify overheating components.
– **Ultrasonic Testing**: Uses high-frequency sound waves to detect internal flaws.
– **Vibration Analysis Tools**: Monitor vibrations to pinpoint issues like imbalance or misalignment.
– **Precision Measuring Instruments**: Include calipers, micrometers, and other tools to measure physical dimensions.
What is Equipment Diagnosis?
Equipment diagnosis, on the other hand, is a more focused and detailed process.
It aims to identify specific faults and underlying issues that affect the performance and reliability of machinery.
This procedure is usually initiated when an equipment inspection indicates potential problems.
Diagnosis involves using advanced tools and techniques to pinpoint the exact cause of the problem.
Main Objectives
The primary goal of an equipment diagnosis is to understand the root cause of a malfunction or deficiency.
This allows technicians to recommend appropriate repairs and preventive measures.
Diagnosing equipment issues not only resolves current problems but also helps to prevent similar issues in the future.
Diagnostic Techniques
Diagnostic techniques are more sophisticated compared to inspection methods:
– **Computerized Tomography (CT) Scans**: Provide detailed internal images of machinery components.
– **Oil Analysis**: Examines the condition of lubricants to identify contamination or wear particles.
– **Electrical Testing**: Measures parameters like voltage, current, and resistance to diagnose electrical issues.
– **Nondestructive Testing (NDT)**: Methods like radiography and magnetic particle testing that do not cause damage to the equipment but reveal internal flaws.
Diagnostic Tools
Advanced diagnostic tools are crucial for accurate fault detection:
– **Oscilloscopes**: Used to analyze electrical signals and waveform patterns.
– **Data Loggers**: Record operational data over time to then analyze performance trends.
– **Endoscopes**: Allow for internal inspections without disassembly.
– **Specialized Simulation Software**: Models equipment behavior under various conditions to predict failures.
Key Differences Between Inspection and Diagnosis
Though both equipment inspection and diagnosis aim to maintain the health of machinery, they serve distinct functions.
Inspections are broader and more general, focusing on the overall condition and safety of equipment.
They are scheduled processes, often part of a preventive maintenance plan.
In contrast, diagnosis is a targeted approach initiated in response to specific issues identified during inspections or operational anomalies.
Scope
– **Inspection**: Broad, covering multiple aspects of the equipment.
– **Diagnosis**: Specific, focusing on identified issues.
Timing
– **Inspection**: Regular intervals, often as part of scheduled maintenance.
– **Diagnosis**: Ad-hoc, initiated when problems are suspected or observed.
Tools and Techniques
– **Inspection**: Basic to intermediate tools and techniques.
– **Diagnosis**: Advanced, specialized tools and techniques.
Outcomes
– **Inspection**: Identifies potential issues, safety hazards, and areas needing attention.
– **Diagnosis**: Pinpoints root causes and provides detailed solutions.
When to Use Each
Knowing when to use each process is vital for efficient equipment management.
Regular inspections should be part of any maintenance plan to ensure ongoing operational safety and efficiency.
However, when inspections or operational data point to problems, a more thorough diagnosis is required to address the underlying issues.
For example, an inspection might reveal that a machine is vibrating excessively.
A subsequent diagnosis could determine that the root cause is a misaligned shaft that requires precise adjustment.
In this way, both processes complement each other to maintain the overall health of the machinery.
Conclusion
Understanding the difference between equipment inspection and equipment diagnosis is essential for proper equipment maintenance.
While inspections provide a broad overview of equipment condition and identify potential problems, diagnoses delve deeper to pinpoint and resolve specific issues.
Using both processes in tandem allows businesses to enhance equipment reliability, safety, and efficiency.
By doing so, companies can reduce downtime, save on repair costs, and ensure a safe working environment for their employees.
資料ダウンロード
QCD調達購買管理クラウド「newji」は、調達購買部門で必要なQCD管理全てを備えた、現場特化型兼クラウド型の今世紀最高の購買管理システムとなります。
ユーザー登録
調達購買業務の効率化だけでなく、システムを導入することで、コスト削減や製品・資材のステータス可視化のほか、属人化していた購買情報の共有化による内部不正防止や統制にも役立ちます。
NEWJI DX
製造業に特化したデジタルトランスフォーメーション(DX)の実現を目指す請負開発型のコンサルティングサービスです。AI、iPaaS、および先端の技術を駆使して、製造プロセスの効率化、業務効率化、チームワーク強化、コスト削減、品質向上を実現します。このサービスは、製造業の課題を深く理解し、それに対する最適なデジタルソリューションを提供することで、企業が持続的な成長とイノベーションを達成できるようサポートします。
オンライン講座
製造業、主に購買・調達部門にお勤めの方々に向けた情報を配信しております。
新任の方やベテランの方、管理職を対象とした幅広いコンテンツをご用意しております。
お問い合わせ
コストダウンが利益に直結する術だと理解していても、なかなか前に進めることができない状況。そんな時は、newjiのコストダウン自動化機能で大きく利益貢献しよう!
(Β版非公開)