- お役立ち記事
- The difference between Equipment Maintenance and Equipment Replacement
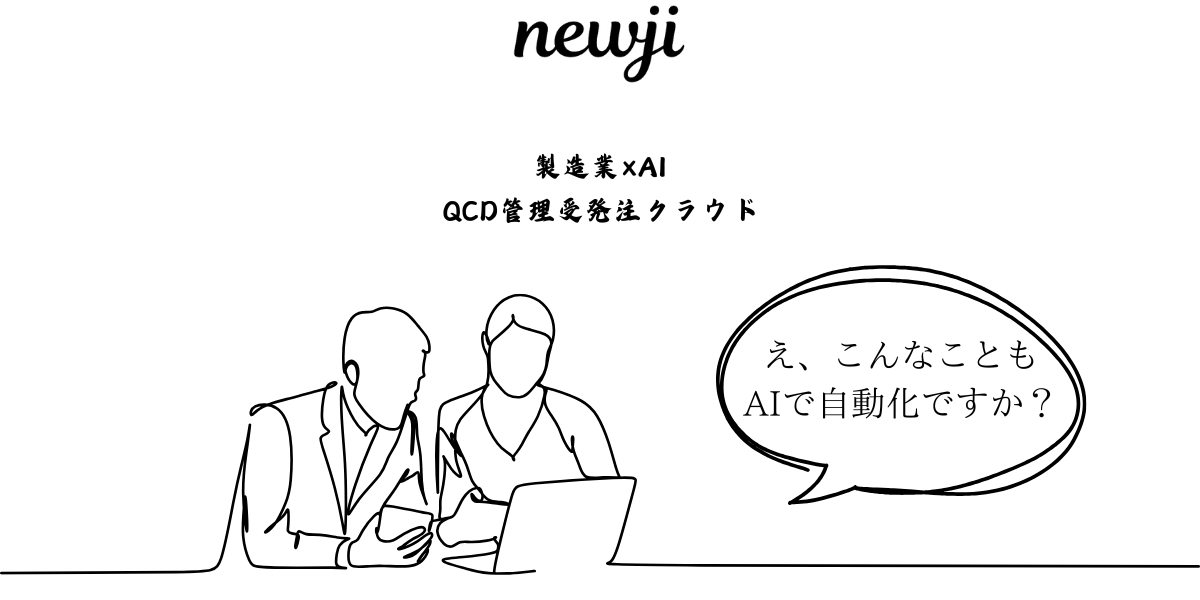
The difference between Equipment Maintenance and Equipment Replacement
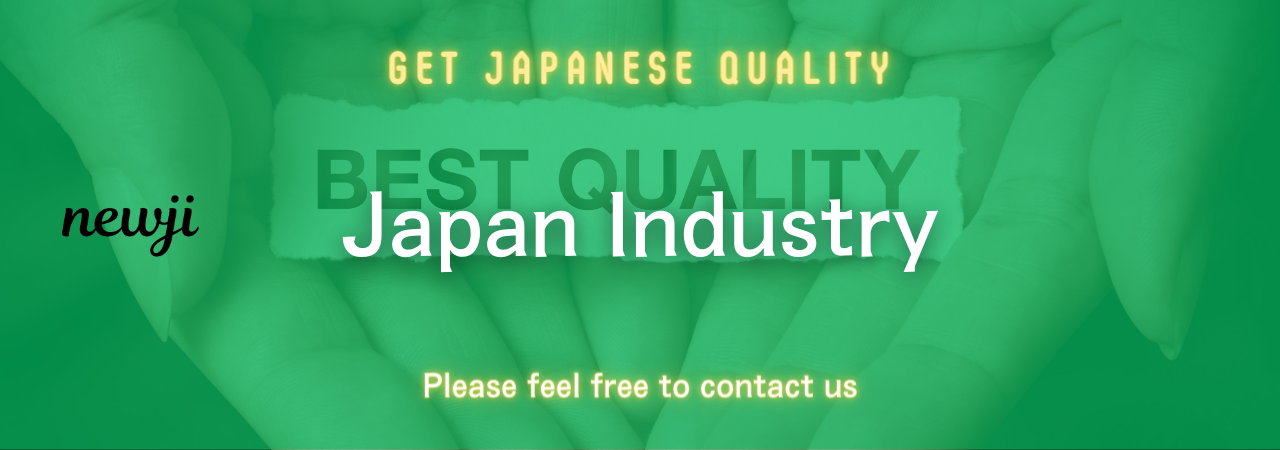
In the world of machinery and tools, knowing when to maintain and when to replace can save both time and money.
Understanding the difference between equipment maintenance and equipment replacement is crucial for running any operation smoothly.
This guide will help break down these concepts so that anyone can make informed decisions.
目次
Understanding Equipment Maintenance
Equipment maintenance refers to the routine actions taken to keep machines and tools in good working condition.
Regular maintenance includes tasks like cleaning, lubricating, inspecting, and testing.
The primary goal of maintenance is to ensure the equipment operates efficiently and safely.
It aims to prevent unexpected breakdowns, which can disrupt operations and lead to costly repairs or downtime.
Types of Equipment Maintenance
There are various types of maintenance strategies.
Here are some popular ones:
Preventive Maintenance
Preventive maintenance involves performing regular inspections and servicing at scheduled intervals.
The idea is to catch problems before they become serious issues.
This could involve checking for wear and tear, replacing parts, and ensuring everything runs smoothly.
Predictive Maintenance
Predictive maintenance uses data and sensors to predict when equipment might fail.
By analyzing data trends, you can anticipate when a machine needs servicing.
This approach can be more cost-effective as it reduces unplanned downtime.
Corrective Maintenance
Corrective maintenance is performed when something goes wrong.
It involves fixing the issue promptly to get the equipment back to its operational state.
This type of maintenance can be more expensive due to the urgency and potential for more extensive damage.
Understanding Equipment Replacement
Equipment replacement is when you decide that an existing piece of equipment is no longer worth maintaining.
This means purchasing new equipment to take its place.
The decision to replace equipment often depends on several factors, including cost, efficiency, and the potential for future breakdowns.
When to Consider Equipment Replacement
Determining the right time to replace equipment is essential for optimizing operations.
Here are some situations where replacement should be considered:
Frequent Breakdowns
If a piece of equipment constantly breaks down, it might be more cost-effective to replace it.
Frequent repairs can add up quickly and cause significant downtime.
High Repair Costs
Sometimes, the cost of repairing old equipment can get close to or even exceed the cost of new equipment.
In such cases, replacement might be the smarter choice.
Outdated Technology
With advancements in technology, older equipment might not be as efficient or safe as newer models.
Upgrading to newer technology can enhance productivity and safety, often justifying the investment.
Factors to Consider Before Maintenance or Replacement
Before deciding whether to maintain or replace equipment, it’s crucial to consider several factors.
These can help make a well-informed decision that saves both time and money.
Cost Analysis
Evaluate the costs involved in both maintaining and replacing the equipment.
Consider the long-term benefits and savings that new equipment might offer.
Sometimes, spending more upfront can save money in the long run.
Life Expectancy
Consider the remaining life expectancy of the equipment.
If a machine is nearing the end of its useful life, it might be better to replace it rather than invest in costly repairs.
Operational Impact
Think about how the decision will impact your operations.
Will maintenance cause significant downtime?
Or will replacement cause disruptions?
Weigh these factors carefully.
Environmental Impact
The environmental impact of your decision is also essential.
Replacing equipment often comes with disposal issues.
On the other hand, new equipment might be more energy-efficient and environmentally friendly.
Best Practices for Maintenance and Replacement
Adopting best practices can help streamline the decision-making process.
Here are some tips:
Keep Detailed Records
Maintain detailed records of all maintenance activities and costs.
These records can offer valuable insights into the equipment’s performance and help in decision-making.
Regular Inspections
Conduct regular inspections to stay ahead of any potential issues.
This helps in catching problems early and making timely decisions about maintenance or replacement.
Employee Training
Ensure that your team is well-trained in operating and maintaining equipment.
Proper use can extend the life of machinery and reduce the need for frequent maintenance.
Consult Experts
When in doubt, consult with experts.
Whether it’s a maintenance professional or a financial advisor, expert opinions can provide valuable guidance.
Conclusion
Knowing the difference between equipment maintenance and equipment replacement can make a significant impact on your operations.
Both have their pros and cons, and the decision should be based on a thorough evaluation of various factors.
By understanding these concepts and following best practices, you can ensure that your equipment remains in optimal condition, thereby saving time, money, and resources.
資料ダウンロード
QCD調達購買管理クラウド「newji」は、調達購買部門で必要なQCD管理全てを備えた、現場特化型兼クラウド型の今世紀最高の購買管理システムとなります。
ユーザー登録
調達購買業務の効率化だけでなく、システムを導入することで、コスト削減や製品・資材のステータス可視化のほか、属人化していた購買情報の共有化による内部不正防止や統制にも役立ちます。
NEWJI DX
製造業に特化したデジタルトランスフォーメーション(DX)の実現を目指す請負開発型のコンサルティングサービスです。AI、iPaaS、および先端の技術を駆使して、製造プロセスの効率化、業務効率化、チームワーク強化、コスト削減、品質向上を実現します。このサービスは、製造業の課題を深く理解し、それに対する最適なデジタルソリューションを提供することで、企業が持続的な成長とイノベーションを達成できるようサポートします。
オンライン講座
製造業、主に購買・調達部門にお勤めの方々に向けた情報を配信しております。
新任の方やベテランの方、管理職を対象とした幅広いコンテンツをご用意しております。
お問い合わせ
コストダウンが利益に直結する術だと理解していても、なかなか前に進めることができない状況。そんな時は、newjiのコストダウン自動化機能で大きく利益貢献しよう!
(Β版非公開)