- お役立ち記事
- The difference between Extrusion Molding and Injection Molding
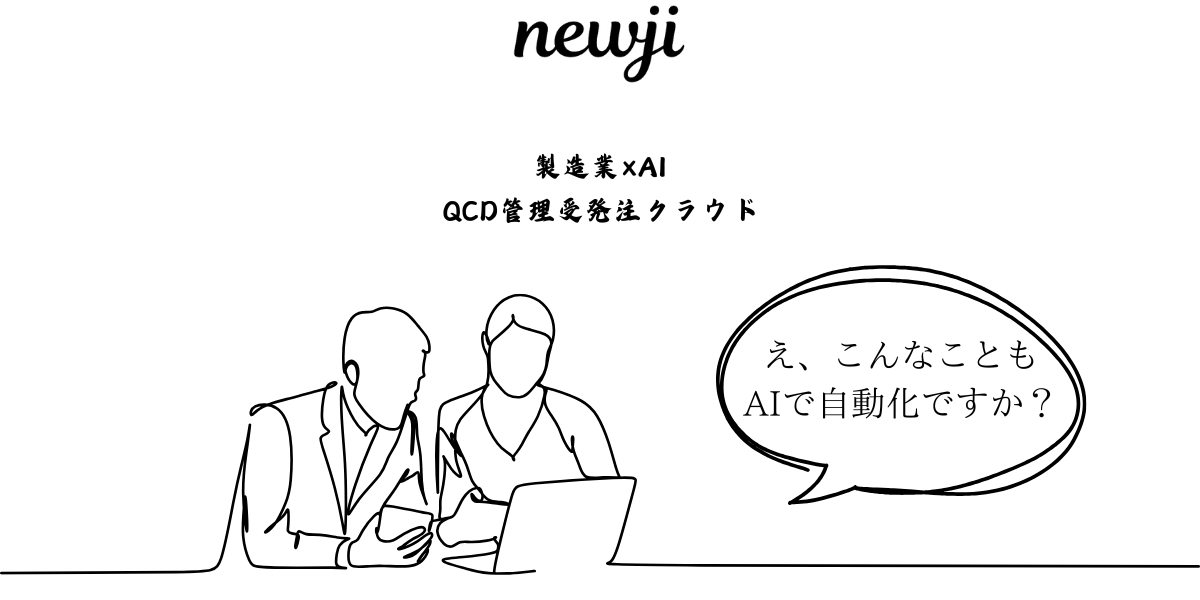
The difference between Extrusion Molding and Injection Molding
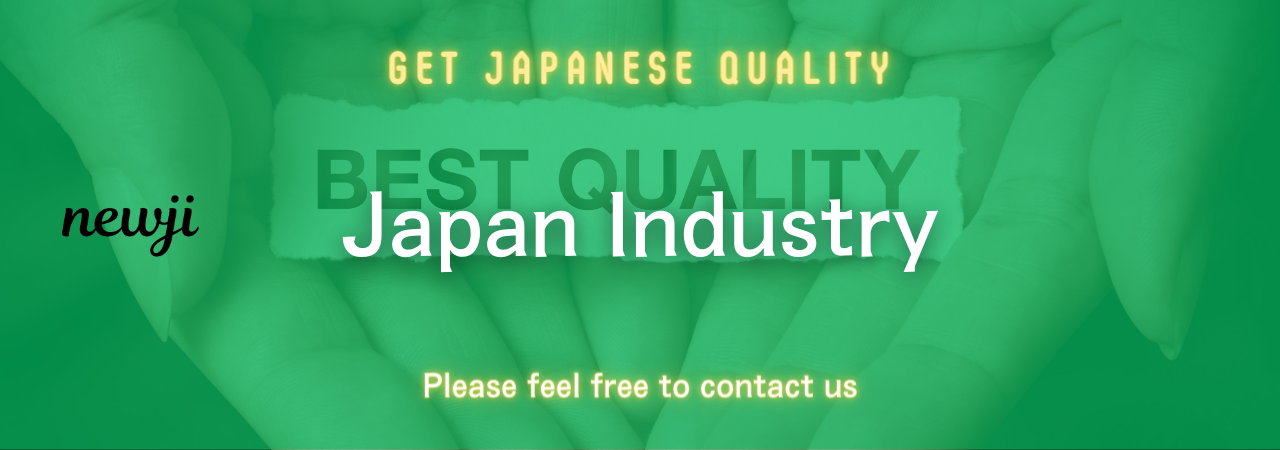
When it comes to manufacturing plastic parts, two common methods are often employed: extrusion molding and injection molding. Both techniques are widely used in the industry. However, they serve different purposes and are suitable for different types of products.
Understanding the distinctions between these methods is crucial for manufacturers to select the most appropriate process for their needs.
目次
What is Extrusion Molding?
Extrusion molding is a continuous process used to create long products with a uniform cross-section. The basic concept involves pushing molten material through a die to form the desired shape.
How Does Extrusion Molding Work?
The extrusion process begins with raw plastic material, typically in the form of small pellets or granules. These materials are fed into an extruder, which consists of a heated barrel and a rotating screw.
As the screw rotates, it melts the plastic, which is then forced through a die to shape it into a continuous profile.
Once the plastic exits the die, it is cooled and solidified using water quenching or air cooling methods.
Common Applications of Extrusion Molding
Extrusion molding is particularly advantageous in producing long, continuous products. Some typical applications include:
– Pipes and Tubing: Often used in plumbing, automotive, and construction industries.
– Window Frames and Door Profiles: Common in the building sector.
– Insulation: Such as foam and coating materials for electrical wires.
– Sheets and Films: Used in packaging and various consumer goods.
What is Injection Molding?
Injection molding is a process used to produce small to medium-sized parts with complex shapes. It involves injecting molten material into a mold to form the part.
How Does Injection Molding Work?
The injection molding process starts with plastic pellets, similar to extrusion molding.
These pellets are fed into a heated barrel where they are melted by a screw.
However, unlike extrusion molding, the melted plastic is then injected into a mold at high pressure.
The mold is clamped shut during the injection process to form the material into the desired shape.
Once the plastic has cooled and solidified, the mold is opened, and the part is ejected.
Common Applications of Injection Molding
Due to its ability to produce complex shapes and high precision parts, injection molding is utilized in a wide range of industries. Typical applications include:
– Automotive Parts: Such as dashboards, bumpers, and interior components.
– Consumer Goods: Toys, kitchenware, and electronic housings.
– Medical Devices: Syringes, IV components, and surgical instruments.
– Packaging: Caps, containers, and closures.
Key Differences Between Extrusion Molding and Injection Molding
Understanding the fundamental differences between extrusion molding and injection molding can help in selecting the right manufacturing process.
Shape and Size of Products
Extrusion molding is ideal for creating long, continuous products like pipes, tubes, and profiles. The process is tailored to producing parts with a uniform cross-section. On the other hand, injection molding is better suited for smaller, intricate parts with complex geometries.
Production Volume
Extrusion molding is typically used for high-volume production of long items. It is efficient and cost-effective when producing continuous shapes in large quantities.
Injection molding is also efficient for high-volume production but is better suited for smaller parts. Once a mold is created, it can be used to produce hundreds to millions of identical pieces.
Material Usage
Both processes can use a variety of plastic materials, but the choice may depend on the specific requirements of the product. Extrusion molding usually involves materials like PVC, polyethylene, and polystyrene, which are suited for continuous shapes. Injection molding can accommodate a broader range of materials, including high-performance plastics and composites.
Tooling and Setup Costs
Extrusion dies are generally less expensive to produce compared to injection molds. However, because injection molding involves creating more complex shapes, the molds required are often more intricate and can be costly.
The setup time for extrusion molding is usually shorter, making it more favorable for continuous production runs.
Injection molding, with higher initial tooling costs, is justifiable when large quantities of parts are needed, making it cost-effective over time.
Advantages and Disadvantages
Both extrusion molding and injection molding have their pros and cons, which can influence the decision-making process.
Advantages of Extrusion Molding
– Continuous production: Ideal for high-volume production of long, uniform products.
– Lower tooling costs: Dies are generally less complex and less expensive than injection molds.
– Efficient material usage: Suitable for making long parts with minimal waste.
Disadvantages of Extrusion Molding
– Limited shapes: Mostly used for products with a constant cross-section.
– Surface finish: May require additional processing to achieve the desired surface quality.
Advantages of Injection Molding
– Complex shapes: Capable of producing intricate and detailed parts.
– High precision: Excellent for making components with tight tolerances.
– Material diversity: Can use a wide range of plastic materials.
Disadvantages of Injection Molding
– High initial cost: Tooling and molds are more expensive to create.
– Longer setup time: May take more time to prepare the mold and machinery.
Conclusion
Choosing between extrusion molding and injection molding ultimately depends on the specific requirements of the product, including shape, volume, material, and cost considerations.
Extrusion molding is ideal for producing continuous, uniform cross-section products in large quantities.
Injection molding, on the other hand, excels in creating complex, small to medium-sized parts with high precision.
By understanding the differences and advantages of each method, manufacturers can make informed decisions to best meet their production needs.
資料ダウンロード
QCD調達購買管理クラウド「newji」は、調達購買部門で必要なQCD管理全てを備えた、現場特化型兼クラウド型の今世紀最高の購買管理システムとなります。
ユーザー登録
調達購買業務の効率化だけでなく、システムを導入することで、コスト削減や製品・資材のステータス可視化のほか、属人化していた購買情報の共有化による内部不正防止や統制にも役立ちます。
NEWJI DX
製造業に特化したデジタルトランスフォーメーション(DX)の実現を目指す請負開発型のコンサルティングサービスです。AI、iPaaS、および先端の技術を駆使して、製造プロセスの効率化、業務効率化、チームワーク強化、コスト削減、品質向上を実現します。このサービスは、製造業の課題を深く理解し、それに対する最適なデジタルソリューションを提供することで、企業が持続的な成長とイノベーションを達成できるようサポートします。
オンライン講座
製造業、主に購買・調達部門にお勤めの方々に向けた情報を配信しております。
新任の方やベテランの方、管理職を対象とした幅広いコンテンツをご用意しております。
お問い合わせ
コストダウンが利益に直結する術だと理解していても、なかなか前に進めることができない状況。そんな時は、newjiのコストダウン自動化機能で大きく利益貢献しよう!
(Β版非公開)