- お役立ち記事
- The difference between Factory Layout and Cell Layout
The difference between Factory Layout and Cell Layout
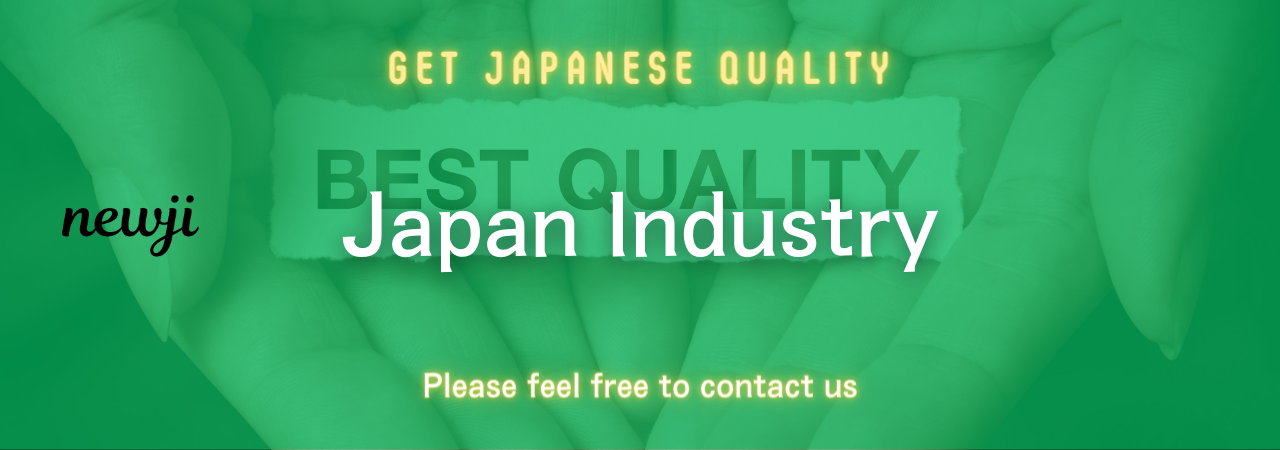
When you’re planning a factory, one of the key decisions involves choosing the right layout for the workspace.
Two common options are the factory layout and the cell layout.
Each has its own benefits and drawbacks, making them more suitable for different types of operations.
In this article, we’ll explore the differences between these two types of layouts to help you understand which one might be the best fit for your needs.
目次
Factory Layout: An Overview
Factory layout, also known as the process layout, involves grouping similar machines and equipment together.
This layout is particularly common in workshops and factories where products require different operations in a specific sequence.
Advantages of Factory Layout
One of the main advantages of a factory layout is its flexibility.
Since machines are grouped by function, it’s easier to adjust the layout for new products or processes.
This makes it ideal for manufacturers who deal with a wide variety of products.
Another benefit is efficiency.
By grouping similar machines, you can streamline operations and reduce the time spent moving materials between different areas of the factory.
Additionally, this layout can help minimize the costs of redundant equipment.
Disadvantages of Factory Layout
However, the factory layout is not without its downsides.
One major drawback is the potential for bottlenecks.
Since all similar machines are grouped together, any delay at one machine can disrupt the entire production process.
Another issue is the increased handling time.
When products need multiple operations, they must be transported back and forth between different areas, which can be time-consuming and costly.
Cell Layout: An Overview
In contrast to the factory layout, the cell layout involves arranging machines and equipment in cells.
Each cell is designed to complete a specific set of tasks, often for a particular product or product family.
This approach can help create more efficient workflows by reducing the need for transportation between different areas.
Advantages of Cell Layout
One of the primary advantages of a cell layout is improved workflow.
By placing all the necessary machines and equipment in one cell, you can significantly reduce the time and effort required to move materials.
This can result in faster production times and lower costs.
Another benefit is better quality control.
Since each cell is responsible for a specific set of tasks, workers can more easily spot and correct any defects or issues that arise.
This can help ensure a higher quality product and reduce the need for rework.
Additionally, cell layouts can help foster a sense of ownership and accountability among workers.
When employees are responsible for producing a specific product or product family, they may take greater pride in their work and strive to achieve higher levels of performance.
Disadvantages of Cell Layout
Despite its benefits, the cell layout also has some drawbacks.
One potential issue is the need for more specialized equipment.
Because each cell is designed to handle a specific set of tasks, you may need to invest in duplicate machinery to create multiple cells.
Another challenge is the potential for overproduction.
If one cell produces more than the downstream cells can handle, it can lead to excess inventory and increased storage costs.
Careful planning and coordination are essential to avoid these issues.
Choosing the Right Layout
When deciding between a factory layout and a cell layout, there are several factors to consider.
The nature of your products, the volume of production, and the flexibility required will all play a role in determining the best layout for your needs.
Product Type
If your products require a wide variety of processes and operations, a factory layout may be more suitable.
This layout can provide the flexibility needed to accommodate different production requirements.
On the other hand, if your products are more uniform and follow a similar set of steps, a cell layout may be a better fit.
Production Volume
For high-volume production, a cell layout can help streamline operations and reduce transportation times.
By placing all necessary equipment in one cell, you can achieve faster production times and lower costs.
However, if your production volume is lower and involves more specialized processes, a factory layout may be more appropriate.
Flexibility
If you need the ability to quickly adapt to new products or processes, a factory layout offers greater flexibility.
With machines grouped by function, it’s easier to reconfigure the layout as needed.
In contrast, a cell layout is more rigid and may require significant effort to change.
Conclusion
In summary, both factory layouts and cell layouts have their own unique advantages and disadvantages.
The best choice for your operations will depend on the nature of your products, the volume of production, and the level of flexibility required.
By carefully considering these factors, you can select the layout that will help you achieve the highest levels of efficiency, quality, and cost-effectiveness in your manufacturing processes.
資料ダウンロード
QCD調達購買管理クラウド「newji」は、調達購買部門で必要なQCD管理全てを備えた、現場特化型兼クラウド型の今世紀最高の購買管理システムとなります。
ユーザー登録
調達購買業務の効率化だけでなく、システムを導入することで、コスト削減や製品・資材のステータス可視化のほか、属人化していた購買情報の共有化による内部不正防止や統制にも役立ちます。
NEWJI DX
製造業に特化したデジタルトランスフォーメーション(DX)の実現を目指す請負開発型のコンサルティングサービスです。AI、iPaaS、および先端の技術を駆使して、製造プロセスの効率化、業務効率化、チームワーク強化、コスト削減、品質向上を実現します。このサービスは、製造業の課題を深く理解し、それに対する最適なデジタルソリューションを提供することで、企業が持続的な成長とイノベーションを達成できるようサポートします。
オンライン講座
製造業、主に購買・調達部門にお勤めの方々に向けた情報を配信しております。
新任の方やベテランの方、管理職を対象とした幅広いコンテンツをご用意しております。
お問い合わせ
コストダウンが利益に直結する術だと理解していても、なかなか前に進めることができない状況。そんな時は、newjiのコストダウン自動化機能で大きく利益貢献しよう!
(Β版非公開)