- お役立ち記事
- The difference between Fault Tree Analysis (FTA) and Failure Mode and Effects Analysis (FMEA)
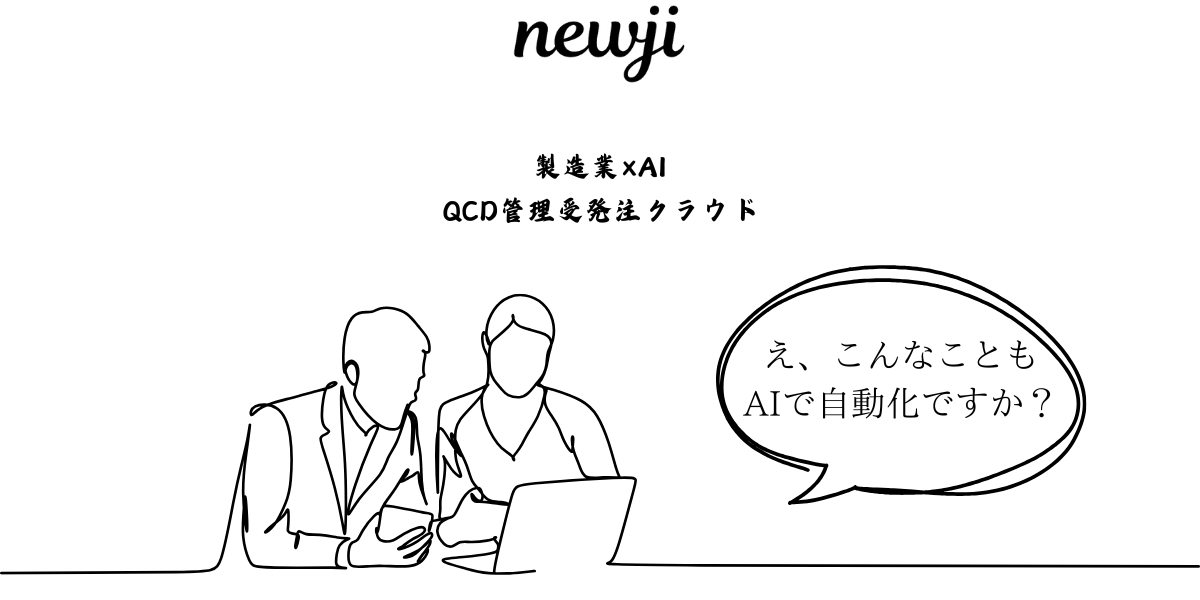
The difference between Fault Tree Analysis (FTA) and Failure Mode and Effects Analysis (FMEA)
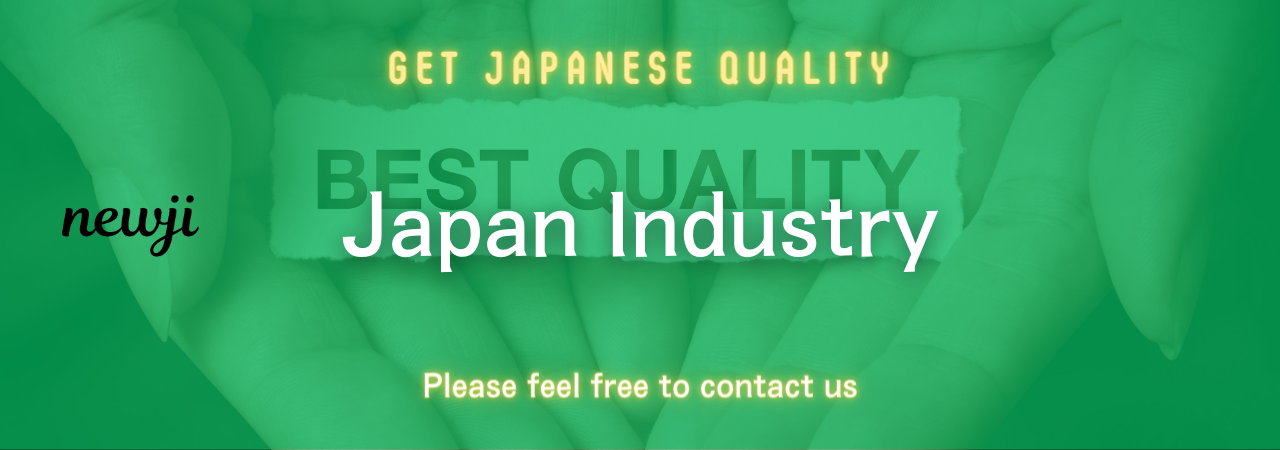
目次
Understanding Fault Tree Analysis (FTA)
Fault Tree Analysis, commonly abbreviated as FTA, is a systematic method used to identify the root causes of a system failure.
It employs a top-down approach, starting from the primary undesirable event, often termed as the “top event,” and working downwards to recognize all possible causes leading to that event.
This method is designed to find the possible ways things can go wrong in a system.
FTA is widely used in industries, including aerospace, manufacturing, and nuclear power, to evaluate the safety and reliability of complex systems.
The technique uses a graphic model that visually depicts the logical relationships between different subsystems and components, highlighting how multiple smaller failures can result in a major system breakdown.
The Process of FTA
The process begins by defining the top event clearly.
For example, in an aerospace application, the top event might be an aircraft engine failure.
Next, the analyst constructs a fault tree diagram, identifying and linking the immediate potential causes that could lead to the top event.
These causes are linked through logical gates such as “AND” and “OR” to show their relationship.
Once the fault tree is complete, the subsequent step is to analyze the diagram to determine minimal cut sets.
These are the smallest combinations of failures that can cause the top event.
The outcome of an FTA helps in understanding the system vulnerabilities and is instrumental in planning preventive measures.
Understanding Failure Mode and Effects Analysis (FMEA)
Failure Mode and Effects Analysis, abbreviated as FMEA, is another structured approach used to identify and analyze the possible ways a system might fail and the consequences of those failures.
Unlike FTA, FMEA utilizes a bottom-up approach, starting from individual components, called failure modes, and moving upward to see the effects on the entire system.
FMEA is extensively used in product development, manufacturing, and service industries.
It helps in improving the quality, safety, and reliability of products by highlighting potential problems and areas for improvement early in the design phase.
The Process of FMEA
The first step in FMEA is identifying the components or processes being analyzed.
For each major component, the analyst lists all possible failure modes.
Each failure mode is then assessed based on three criteria:
– Severity: The seriousness of the impact if the failure occurs.
– Occurrence: The likelihood of the failure happening.
– Detection: The ability to detect the failure before it reaches the customer.
These criteria are often rated on a numerical scale, and the product of these ratings gives a Risk Priority Number (RPN).
Components with high RPNs are prioritized for corrective actions to mitigate the risks.
Key Differences Between FTA and FMEA
While both FTA and FMEA aim to improve system reliability and safety, they differ significantly in their approaches and applications.
Understanding these differences can help businesses choose the right method for their specific needs.
Top-Down vs. Bottom-Up Approach
One of the primary distinctions between FTA and FMEA is their approach.
FTA adopts a top-down approach, starting from a single top event and working down to find possible causes.
This is suitable for identifying potential catastrophic failures and understanding complex system interactions.
On the other hand, FMEA uses a bottom-up approach, beginning with individual components and working up to understand the effects on the entire system.
This is useful for identifying multiple failure modes and understanding localized risks in detail.
Qualitative vs. Quantitative Analysis
FTA often involves qualitative analysis, focusing on the logical connections between failure causes and the top event.
While quantitative analysis (such as determining probability) can also be performed, the primary emphasis is on understanding the fault paths.
FMEA blends qualitative and quantitative aspects by evaluating severity, occurrence, and detection to generate an RPN.
This numeric assessment helps in prioritizing risks and focusing on the most critical failure modes.
Graphical Model vs. Tabular Format
FTA uses a graphic fault tree diagram, making it easier to visualize complex failure relationships within a system.
This visual aid helps stakeholders and decision-makers to quickly grasp how different component failures contribute to the top event.
FMEA, however, is typically documented in a tabular format.
This structured table provides a comprehensive overview of potential risks, associated effects, and current control measures, which can be very detailed and specific.
Applications and Use Cases
Both FTA and FMEA are indispensable tools in various industries for enhancing system reliability and safety.
Their applications, however, can be distinct based on the nature of the industry and the specific goals of the analysis.
Industries Utilizing FTA
FTA is heavily utilized in industries where the primary concern is the system’s overall safety and reliability.
For instance, in aerospace engineering, FTA helps in preventing catastrophic failures such as engine shutdowns or control system failures.
Similarly, in nuclear energy, it ensures the safe operation of reactors by identifying critical fault paths.
FTA is also pivotal in military systems where mission-critical reliability is a necessity.
Industries Utilizing FMEA
FMEA finds its prominence in industries focused on product development and manufacturing.
In the automotive industry, FMEA helps in ensuring the quality and safety of vehicles by analyzing components like brakes, engines, and electronic systems.
In healthcare, it is used to improve medical devices and processes, enhancing patient safety.
The methodology is also applied in the pharmaceutical industry to ensure drug quality and efficacy by assessing possible failure modes in the production process.
Complementary Use of FTA and FMEA
While FTA and FMEA have unique strengths, they can be complementary when used together.
Combining both provides a thorough assessment of a system’s reliability and safety by covering both top-down and bottom-up perspectives.
In complex projects like aircraft design or large-scale manufacturing processes, employing both methods can give a comprehensive risk analysis, ensuring all potential points of failure are addressed.
Conclusion
Understanding the differences between Fault Tree Analysis (FTA) and Failure Mode and Effects Analysis (FMEA) is crucial for selecting the appropriate method for evaluating system reliability and safety.
While FTA provides a top-down approach to identify critical failure paths, FMEA offers a bottom-up analysis focusing on individual component risks.
Both methodologies, when used effectively, can significantly contribute to the development of safe, reliable, and high-quality systems and products.
資料ダウンロード
QCD調達購買管理クラウド「newji」は、調達購買部門で必要なQCD管理全てを備えた、現場特化型兼クラウド型の今世紀最高の購買管理システムとなります。
ユーザー登録
調達購買業務の効率化だけでなく、システムを導入することで、コスト削減や製品・資材のステータス可視化のほか、属人化していた購買情報の共有化による内部不正防止や統制にも役立ちます。
NEWJI DX
製造業に特化したデジタルトランスフォーメーション(DX)の実現を目指す請負開発型のコンサルティングサービスです。AI、iPaaS、および先端の技術を駆使して、製造プロセスの効率化、業務効率化、チームワーク強化、コスト削減、品質向上を実現します。このサービスは、製造業の課題を深く理解し、それに対する最適なデジタルソリューションを提供することで、企業が持続的な成長とイノベーションを達成できるようサポートします。
オンライン講座
製造業、主に購買・調達部門にお勤めの方々に向けた情報を配信しております。
新任の方やベテランの方、管理職を対象とした幅広いコンテンツをご用意しております。
お問い合わせ
コストダウンが利益に直結する術だと理解していても、なかなか前に進めることができない状況。そんな時は、newjiのコストダウン自動化機能で大きく利益貢献しよう!
(Β版非公開)