- お役立ち記事
- The difference between FMEA and FMECA
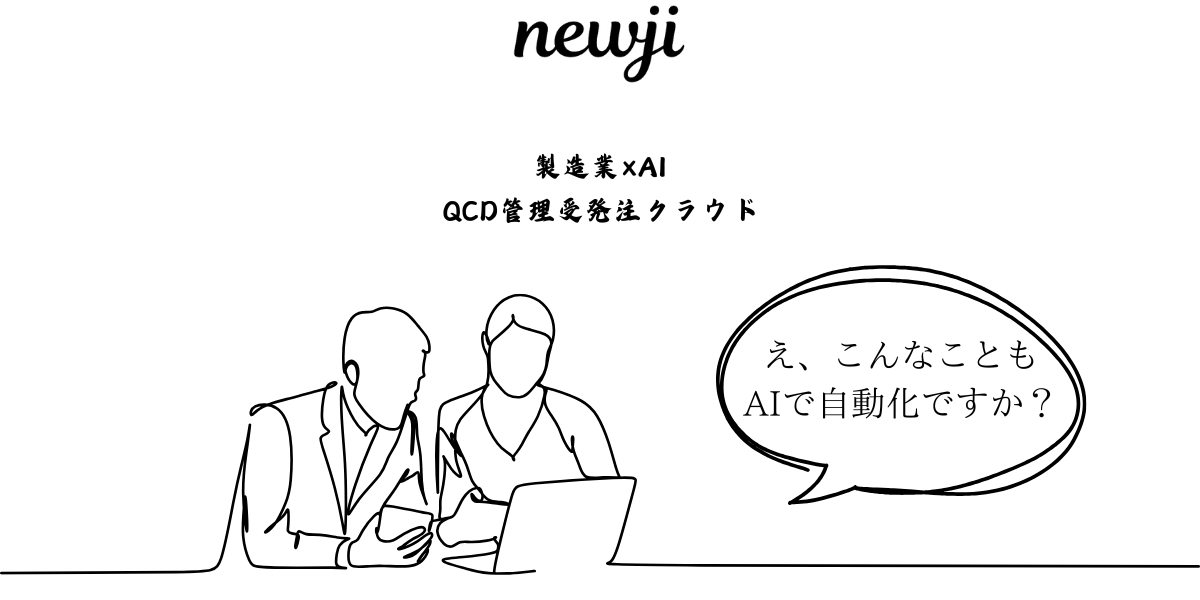
The difference between FMEA and FMECA
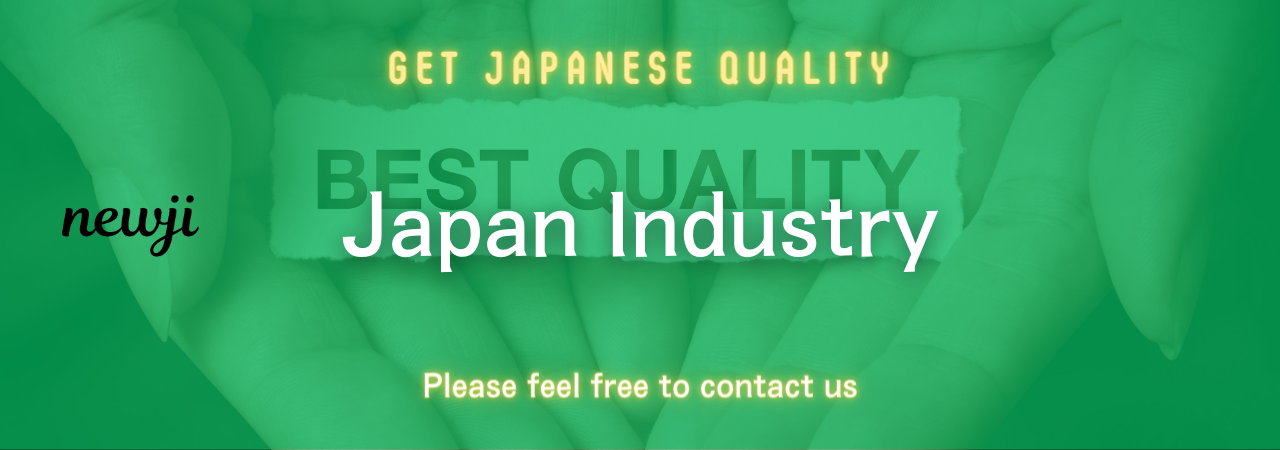
Failure Modes and Effects Analysis (FMEA) and Failure Modes, Effects, and Criticality Analysis (FMECA) are two essential methods used to identify potential issues in products and processes.
They help in improving reliability and safety.
Understanding these methodologies is crucial for industries like automotive, aerospace, and healthcare.
目次
What is FMEA?
Failure Modes and Effects Analysis, commonly known as FMEA, is a systematic approach for identifying potential failure modes in a product or process.
Its goal is to assess the impact of these failures and prioritize them for corrective actions.
FMEA ensures early identification and mitigation of risks.
Components of FMEA
An FMEA usually consists of several key components:
1. **Failure Modes**: These are the various ways in which a component, subsystem, or system can fail to perform its intended function.
2. **Effects Analysis**: This involves assessing the consequences of each failure mode on the system or end-user.
3. **Risk Priority Number (RPN)**: This is a numerical score calculated by multiplying the severity, occurrence, and detection ratings of a failure mode. It helps in prioritizing which issues to address first.
Types of FMEA
There are two main types of FMEA:
1. **Design FMEA (DFMEA)**: Focuses on potential failure modes in product design.
2. **Process FMEA (PFMEA)**: Focuses on potential failure modes in manufacturing and assembly processes.
What is FMECA?
Failure Modes, Effects, and Criticality Analysis (FMECA) takes FMEA a step further by incorporating a criticality analysis component.
It does everything an FMEA does, but also evaluates the significance or “criticality” of the failure modes.
This additional step helps in prioritizing failure modes based on their severity and likelihood of occurrence.
Components of FMECA
FMECA consists of the same components as FMEA, with an additional criticality assessment:
1. **Criticality Analysis**: This involves ranking the failure modes based on their criticality, often using a criticality index or matrix.
It helps in identifying the most severe and probable failure modes that require immediate attention.
Types of FMECA
Similar to FMEA, FMECA can be categorized into:
1. **Design FMECA**: Focuses on assessing the criticality of potential failure modes in the design phase.
2. **Process FMECA**: Focuses on assessing the criticality of potential failure modes in the process phase.
The Main Differences
Both FMEA and FMECA aim to identify and mitigate potential failures, but they have some key differences.
Depth of Analysis
FMEA is generally simpler and quicker to perform.
It identifies possible failure modes and prioritizes them based on their impact.
FMECA, on the other hand, adds an extra layer of analysis by evaluating the criticality of each failure mode.
This makes FMECA more comprehensive, but also more time-consuming.
Complexity and Resource Requirements
Due to the criticality analysis component, FMECA requires more resources, including time and expertise.
It often involves more detailed data collection and analysis compared to FMEA.
Usage Scenarios
FMEA is typically used during the initial design and development stages of a product or process.
It helps in early identification and mitigation of potential issues.
FMECA is often used in high-risk industries where the cost of failure is extremely high, such as aerospace and defense.
It’s also used for critical systems where reliability and safety are paramount.
When to Use FMEA and FMECA
Understanding when to use FMEA or FMECA depends on the specific needs and constraints of your project.
Use FMEA When:
– You need a quick and straightforward method to identify and prioritize potential failure modes.
– Resource constraints limit the depth of your analysis.
– Early stages of product or process design where initial risk identification is crucial.
Use FMECA When:
– The product or process has critical safety or reliability requirements.
– You need a more comprehensive analysis to understand the impact of failure modes.
– High-risk scenarios where the cost of failure is extremely high.
Advantages and Disadvantages
Advantages of FMEA
– **Simplicity**: Easier and quicker to perform.
– **Cost-Effective**: Requires fewer resources for execution.
– **Early Identification**: Helps in early stages to identify potential issues.
Disadvantages of FMEA
– **Limited Scope**: May not provide a comprehensive analysis for high-risk scenarios.
– **Less Detailed**: Lacks the criticality assessment component.
Advantages of FMECA
– **Comprehensive Analysis**: Provides a detailed evaluation of failure modes and their criticality.
– **Better Prioritization**: Helps in prioritizing high-risk failure modes effectively.
– **Suitable for High-Risk Industries**: Ideal for sectors where reliability and safety are paramount.
Disadvantages of FMECA
– **Resource-Intensive**: Requires more time, effort, and expertise.
– **Complexity**: More complex to perform and analyze.
Conclusion
Both FMEA and FMECA are invaluable tools in the realm of risk management.
FMEA is ideal for quick, initial assessments, while FMECA is better suited for in-depth analyses in high-risk scenarios.
Understanding the differences between these methodologies will help you choose the right approach for your project, ensuring safer and more reliable products and processes.
資料ダウンロード
QCD調達購買管理クラウド「newji」は、調達購買部門で必要なQCD管理全てを備えた、現場特化型兼クラウド型の今世紀最高の購買管理システムとなります。
ユーザー登録
調達購買業務の効率化だけでなく、システムを導入することで、コスト削減や製品・資材のステータス可視化のほか、属人化していた購買情報の共有化による内部不正防止や統制にも役立ちます。
NEWJI DX
製造業に特化したデジタルトランスフォーメーション(DX)の実現を目指す請負開発型のコンサルティングサービスです。AI、iPaaS、および先端の技術を駆使して、製造プロセスの効率化、業務効率化、チームワーク強化、コスト削減、品質向上を実現します。このサービスは、製造業の課題を深く理解し、それに対する最適なデジタルソリューションを提供することで、企業が持続的な成長とイノベーションを達成できるようサポートします。
オンライン講座
製造業、主に購買・調達部門にお勤めの方々に向けた情報を配信しております。
新任の方やベテランの方、管理職を対象とした幅広いコンテンツをご用意しております。
お問い合わせ
コストダウンが利益に直結する術だと理解していても、なかなか前に進めることができない状況。そんな時は、newjiのコストダウン自動化機能で大きく利益貢献しよう!
(Β版非公開)