- お役立ち記事
- The difference between FMEA and FTA
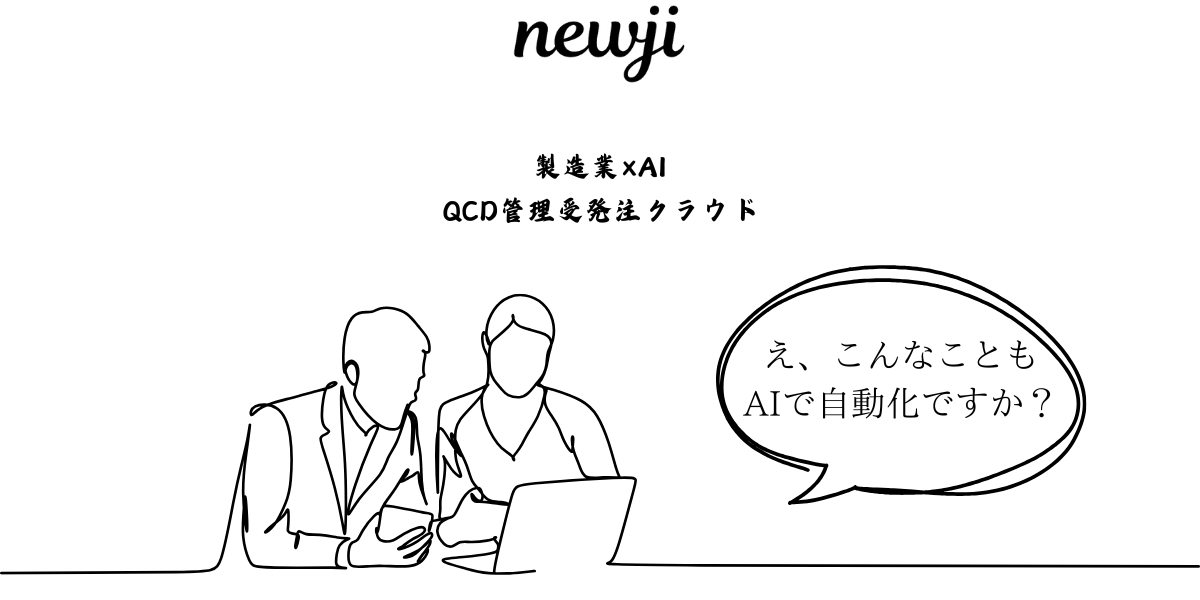
The difference between FMEA and FTA
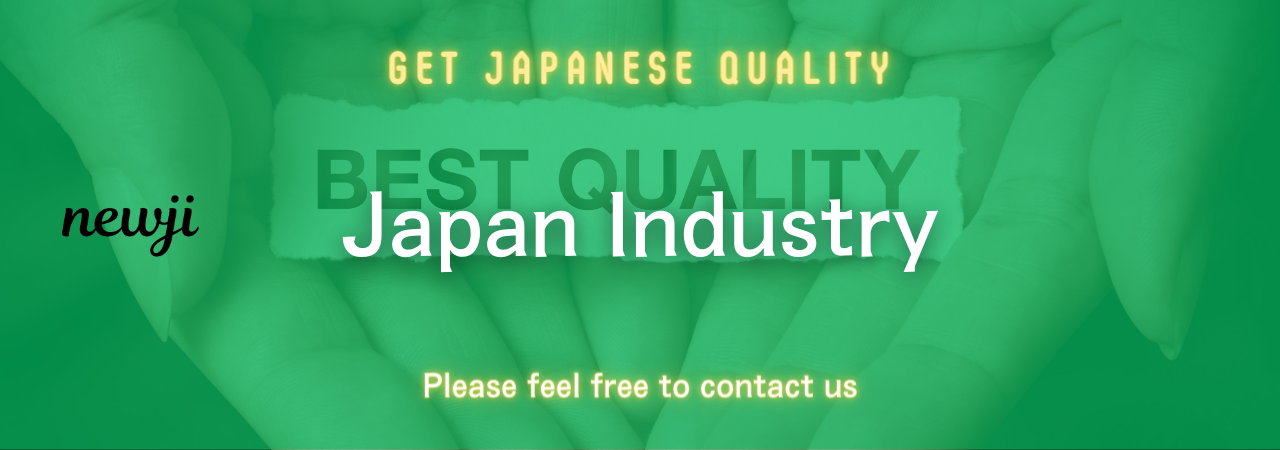
When it comes to analyzing and managing risks in engineering and manufacturing processes, two common methods are often discussed: Failure Mode and Effects Analysis (FMEA) and Fault Tree Analysis (FTA).
Both techniques aim to prevent problems before they occur, but they do so in different ways.
Understanding the difference between FMEA and FTA is essential for choosing the right tool for your specific needs.
Let’s explore these differences.
目次
What is FMEA?
FMEA stands for Failure Mode and Effects Analysis.
It is a systematic approach used to identify potential failure modes in a system, product, or process.
Originally developed for the aerospace industry, FMEA is now widely used across various sectors including automotive, healthcare, and electronics.
How FMEA Works
FMEA involves a step-by-step procedure to identify failure modes, assess their potential impact, and prioritize corrective actions.
Here is a breakdown of the key steps in FMEA:
1. **Identify Failure Modes**: The first step is to list all the possible ways in which a component or system could fail.
2. **Analyze Effects**: Next, evaluate the consequences of each failure mode.
What happens when this failure occurs?
Does it affect safety, performance, or user satisfaction?
3. **Assign Severity, Occurrence, and Detection Rankings**: Each failure mode is then rated for its severity, the likelihood of occurrence, and how easily it can be detected.
4. **Calculate Risk Priority Number (RPN)**: The rankings are combined to form an RPN, which helps prioritize which failure modes should be addressed first.
5. **Implement Corrective Actions**: Finally, actions are taken to eliminate or reduce the risks associated with the highest RPNs.
What is FTA?
FTA stands for Fault Tree Analysis.
Unlike FMEA, which is a bottom-up approach, FTA is a top-down, deductive analysis method.
It was originally developed for military and aerospace applications but has since been used in various industries such as nuclear power and chemical manufacturing.
How FTA Works
FTA starts with a top-level event, usually an undesired state (such as system failure), and works backward to identify all the possible causes usually represented in a tree diagram:
1. **Define the Top-Level Event**: Begin by identifying the undesirable event that you want to analyze.
2. **Identify Intermediate Events**: Break down the top-level event into intermediate events which represent conditions that could lead to the top-level event.
3. **Construct the Fault Tree**: Develop a tree diagram that maps out the logical connections between the intermediate events and their underlying causes.
4. **Analyze the Fault Tree**: Evaluate the fault tree to determine the probability and impact of each event leading up to the top-level failure.
5. **Implement Corrective Actions**: Based on the analysis, take actions to mitigate the risk of the top-level event occurring.
Key Differences Between FMEA and FTA
Approach
– **FMEA**: Uses a bottom-up approach. It begins with individual components and looks forward to see the impact of potential failures.
– **FTA**: Uses a top-down approach. It starts with an undesirable event and works backward to find its causes.
Scope
– **FMEA**: Typically more detailed and time-consuming, as it involves examining all possible failure modes at a granular level.
– **FTA**: Tends to be broader and more focused on key events that could lead to major failures.
Visualization
– **FMEA**: Results are usually documented in tables or spreadsheets.
– **FTA**: Results are often depicted in tree diagrams, making it easier to visualize the relationships between events.
Applications
– **FMEA**: Commonly used in product design and development, manufacturing, and service delivery.
– **FTA**: Frequently applied in safety-critical industries such as aerospace, military, and nuclear power.
Complexity and Ease of Use
– **FMEA**: Can become quite complex when dealing with large systems due to the detailed analysis required for each failure mode.
– **FTA**: Generally easier to use for high-level analysis, given its top-down approach.
When to Use FMEA
FMEA is particularly useful when you aim to:
– Improve the reliability of a product or system.
– Identify and prioritize potential failure modes during the design and development phase.
– Enhance overall product or process quality.
When to Use FTA
FTA is ideal when you need to:
– Analyze complex systems where a single failure can have significant consequences.
– Assess the root causes of critical failures.
– Visualize the relationships and interdependencies among components and subsystems.
Complementary Techniques
While FMEA and FTA have their distinct strengths, they are often used together to provide a comprehensive risk assessment.
For instance, you might start with FTA to identify the critical events and then use FMEA to dive deeper into the failure modes and their effects.
Using both techniques allows for a more robust analysis, ensuring that both high-level and detailed risks are addressed.
Understanding the difference between FMEA and FTA is crucial for effective risk management.
These tools, each with their unique strengths and applications, can significantly enhance the reliability and safety of your systems.
By choosing the right method for your specific needs, you can proactively address potential issues and achieve greater success in your projects.
資料ダウンロード
QCD調達購買管理クラウド「newji」は、調達購買部門で必要なQCD管理全てを備えた、現場特化型兼クラウド型の今世紀最高の購買管理システムとなります。
ユーザー登録
調達購買業務の効率化だけでなく、システムを導入することで、コスト削減や製品・資材のステータス可視化のほか、属人化していた購買情報の共有化による内部不正防止や統制にも役立ちます。
NEWJI DX
製造業に特化したデジタルトランスフォーメーション(DX)の実現を目指す請負開発型のコンサルティングサービスです。AI、iPaaS、および先端の技術を駆使して、製造プロセスの効率化、業務効率化、チームワーク強化、コスト削減、品質向上を実現します。このサービスは、製造業の課題を深く理解し、それに対する最適なデジタルソリューションを提供することで、企業が持続的な成長とイノベーションを達成できるようサポートします。
オンライン講座
製造業、主に購買・調達部門にお勤めの方々に向けた情報を配信しております。
新任の方やベテランの方、管理職を対象とした幅広いコンテンツをご用意しております。
お問い合わせ
コストダウンが利益に直結する術だと理解していても、なかなか前に進めることができない状況。そんな時は、newjiのコストダウン自動化機能で大きく利益貢献しよう!
(Β版非公開)