- お役立ち記事
- The difference between Forecast-based Production and Planned Production
The difference between Forecast-based Production and Planned Production
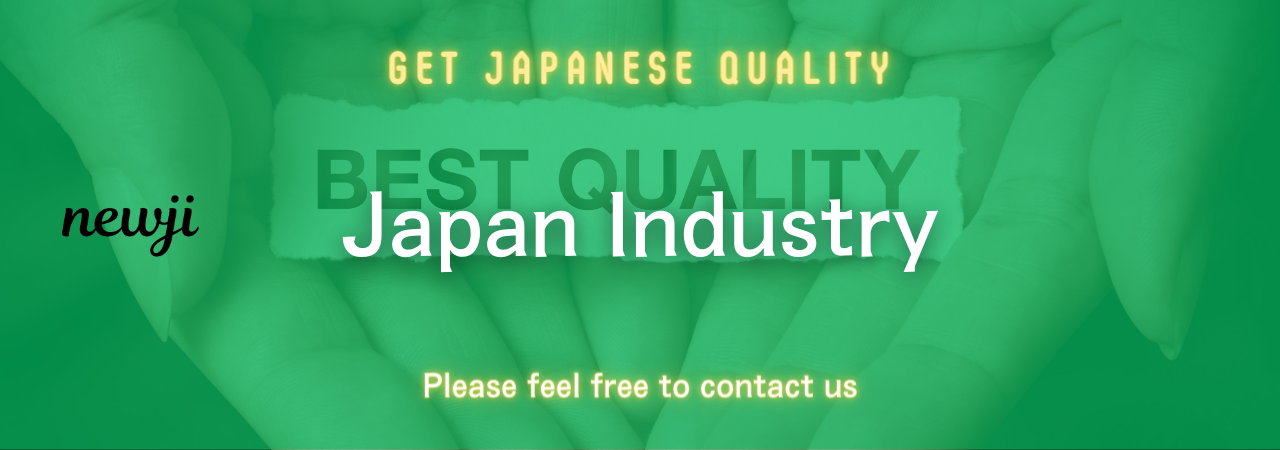
Understanding the difference between forecast-based production and planned production is critical in the manufacturing industry.
While both approaches guide how products are made, they each have their unique benefits and challenges.
This article will explain these production methods in a straightforward way so that anyone can grasp their basic concepts.
目次
What is Forecast-based Production?
Forecast-based production is a method used by manufacturers to predict future product demand.
By analyzing historical data and market trends, companies can estimate how much of a product will be needed in the future.
This information is then used to determine production schedules.
Advantages of Forecast-based Production
One of the significant advantages of forecast-based production is that it allows companies to be proactive.
By anticipating demand, manufacturers can produce goods ahead of time.
This ensures that products are ready for customers when they need them.
Another benefit of this approach is the potential for reduced lead times.
When products are made in advance, delivery to customers is quicker.
This can significantly improve customer satisfaction.
Forecast-based production can also help in better inventory management.
Companies can avoid overproduction and stock shortages by aligning production closely with predicted demand.
This balance helps reduce storage costs and the risk of unsold inventory.
Challenges of Forecast-based Production
Despite its advantages, forecast-based production has its challenges.
The biggest challenge is the reliance on accurate forecasts.
If the predictions are wrong, companies may face either an excess of unsold products or a shortage that cannot meet customer demand.
Another challenge is the potential rigidity in the production process.
Because the production is based on forecasts, it can be difficult to adjust quickly to unexpected changes in demand.
This inflexibility can be costly, especially in fast-paced markets.
What is Planned Production?
Planned production, on the other hand, relies on specific customer orders.
In this approach, manufacturers produce goods only when a confirmed order is received.
This method is also known as make-to-order (MTO).
Advantages of Planned Production
One of the primary benefits of planned production is the reduction of wasted resources.
Since products are made only when there is an order, there is no risk of overproduction.
This leads to more efficient use of materials and labor.
Planned production also offers greater flexibility.
Manufacturers can easily adapt to changes in customer requirements, as production starts only after an order is confirmed.
This adaptability can help companies respond to market demands more precisely.
Another significant advantage is the improved cash flow.
Since products are made to order, companies do not tie up funds in unsold inventory.
This can be crucial for maintaining healthy financial operations.
Challenges of Planned Production
The main challenge with planned production is the potential for longer lead times.
Since production starts only after an order is received, customers may have to wait longer for their products.
This can be a disadvantage in competitive markets where quick delivery is a critical factor.
Another challenge is the complexity of managing production schedules.
Coordinating multiple orders of different products can be complicated, requiring efficient planning and execution.
Any delays or mistakes can lead to customer dissatisfaction and potential loss of business.
Choosing the Right Approach
Deciding between forecast-based production and planned production depends on several factors.
These include the nature of the products, market conditions, and customer expectations.
Market Dynamics
In markets with stable and predictable demand, forecast-based production can be very effective.
This approach allows companies to meet demand consistently and maintain high customer satisfaction.
However, in markets with volatile or uncertain demand, planned production may be more appropriate.
The ability to respond quickly to changing customer needs can be a significant advantage.
Nature of the Products
The type of products being manufactured also plays a crucial role in choosing the right approach.
For products with a long shelf life and consistent demand, forecast-based production can be ideal.
In contrast, for products that are highly customized or have a short shelf life, planned production may be better suited.
This method ensures that each product meets specific customer requirements without the risk of inventory obsolescence.
Customer Expectations
Customer expectations are another critical factor to consider.
If customers prioritize quick delivery times, forecast-based production may be necessary to maintain a competitive edge.
Conversely, if customers value customization and are willing to wait longer, planned production can offer a more tailored solution.
Combining Both Approaches
In some cases, combining both production methods can be beneficial.
For instance, a company might use forecast-based production for standard products with steady demand while employing planned production for customized or less predictable items.
By adopting a hybrid approach, manufacturers can enjoy the benefits of both methods.
They can maintain lower lead times for standard products and still offer customization options when needed.
Implementing a Hybrid Approach
Implementing a hybrid approach requires careful planning and management.
It involves setting up systems to handle both forecast-based and planned production efficiently.
Manufacturers may need to invest in advanced software solutions to manage production schedules, inventory, and customer orders seamlessly.
Training staff to adapt to this dual approach is also essential for its success.
Understanding the differences between forecast-based production and planned production helps manufacturers make informed decisions.
By considering factors such as market dynamics, product nature, and customer expectations, companies can choose the best approach to meet their needs.
In some cases, adopting a hybrid model can provide the best of both worlds, ensuring efficiency and flexibility in production.
Whichever method is chosen, the ultimate goal is to align production processes with market demand to maximize efficiency and customer satisfaction.
資料ダウンロード
QCD調達購買管理クラウド「newji」は、調達購買部門で必要なQCD管理全てを備えた、現場特化型兼クラウド型の今世紀最高の購買管理システムとなります。
ユーザー登録
調達購買業務の効率化だけでなく、システムを導入することで、コスト削減や製品・資材のステータス可視化のほか、属人化していた購買情報の共有化による内部不正防止や統制にも役立ちます。
NEWJI DX
製造業に特化したデジタルトランスフォーメーション(DX)の実現を目指す請負開発型のコンサルティングサービスです。AI、iPaaS、および先端の技術を駆使して、製造プロセスの効率化、業務効率化、チームワーク強化、コスト削減、品質向上を実現します。このサービスは、製造業の課題を深く理解し、それに対する最適なデジタルソリューションを提供することで、企業が持続的な成長とイノベーションを達成できるようサポートします。
オンライン講座
製造業、主に購買・調達部門にお勤めの方々に向けた情報を配信しております。
新任の方やベテランの方、管理職を対象とした幅広いコンテンツをご用意しております。
お問い合わせ
コストダウンが利益に直結する術だと理解していても、なかなか前に進めることができない状況。そんな時は、newjiのコストダウン自動化機能で大きく利益貢献しよう!
(Β版非公開)