- お役立ち記事
- The difference between Frame Welding and Plate Welding
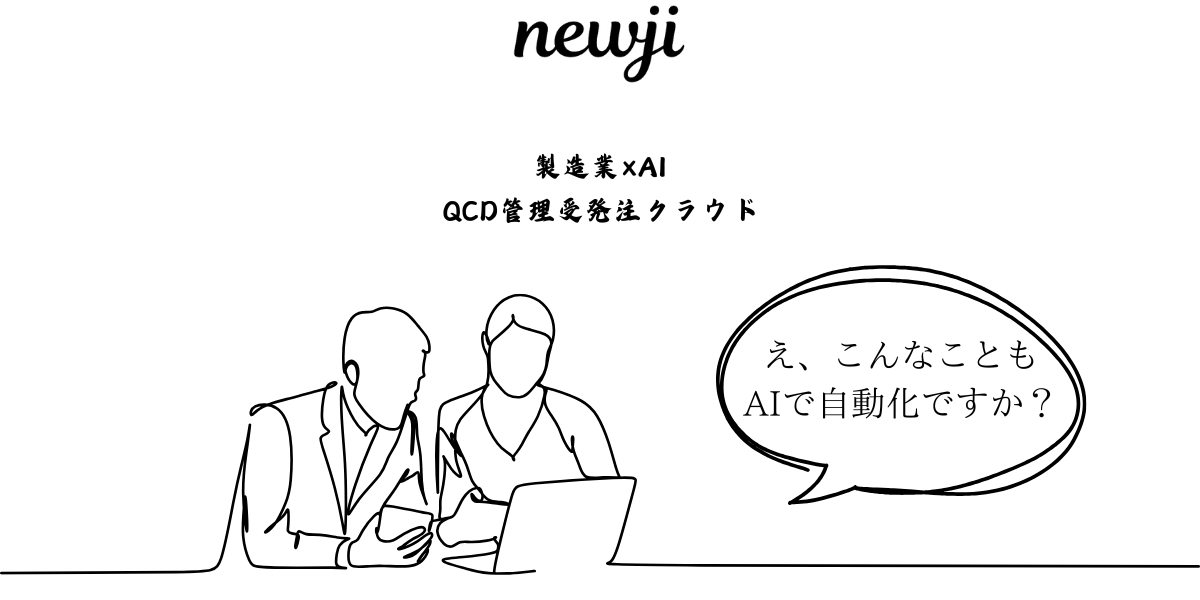
The difference between Frame Welding and Plate Welding
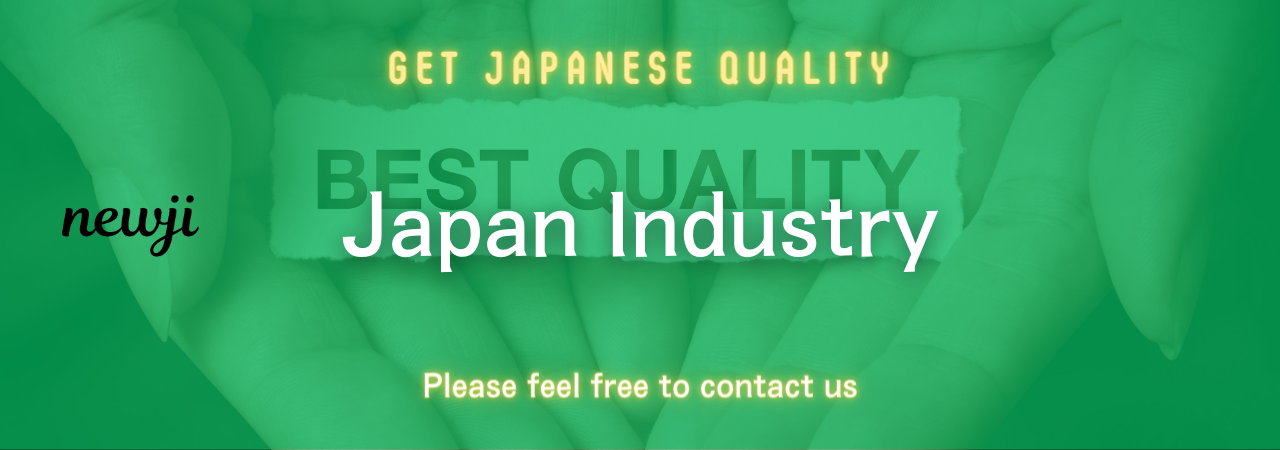
When working with metals, two common welding techniques you’ll often encounter are frame welding and plate welding.
Understanding their differences is important for anyone involved in metal fabrication, construction, or even simple DIY projects.
Here, we’ll explore what sets these two methods apart, their specific uses, and why you might choose one over the other.
目次
What is Frame Welding?
Frame welding is a technique most commonly used in the construction of frameworks and supports.
It involves joining narrow, long pieces of metal, like rods, beams, or tubes.
This type of welding is often seen in the creation of metal frameworks for buildings, vehicle chassis, and machinery.
Applications of Frame Welding
Frame welding is essential in industries where structural integrity is crucial.
For example, in the construction industry, steel frames form the backbone of skyscrapers, bridges, and residential buildings.
In the automotive industry, vehicle frames are welded to ensure the safety and performance of cars and trucks.
Farm equipment, aerospace structures, and even some furniture designs rely on the strength provided by frame welding.
Techniques Used in Frame Welding
Several welding techniques can be employed in frame welding, including MIG (Metal Inert Gas), TIG (Tungsten Inert Gas), and stick welding.
Each method has its pros and cons.
MIG welding is fast and easy to learn, making it suitable for large projects.
TIG welding offers precision and control, ideal for detailed work.
Stick welding, also known as Shielded Metal Arc Welding (SMAW), is versatile and effective for heavier metals.
Selecting the appropriate technique depends on the specific needs of the project and the type of metal being used.
What is Plate Welding?
Plate welding, on the other hand, focuses on joining flat, typically larger sheets of metal.
These plates can vary in thickness but are usually significantly thicker than the long pieces used in frame welding.
Plate welding is commonly employed in the construction of ships, storage tanks, and large machinery parts.
Applications of Plate Welding
The uses of plate welding are vast and varied.
In the shipbuilding industry, plate welding is essential for crafting robust hulls that can withstand intense oceanic conditions.
Storage tanks, whether for water, chemicals, or fuels, are also often constructed using this method to ensure durability and leak-proof integrity.
In the manufacturing of large machinery parts, such as those found in industrial factories, plate welding provides the necessary strength and resilience.
Techniques Used in Plate Welding
Similar to frame welding, several methods can be used in plate welding.
Submerged Arc Welding (SAW) is popular for its deep weld penetration and high-quality outcomes, making it suitable for thick plates.
Flux-Cored Arc Welding (FCAW) is effective for thicker metals and offers high deposition rates.
Oxy-Acetylene welding is another method, valued for its versatility and portability, though it’s less common in industrial applications today.
The choice of technique is highly dependent on the thickness of the plates and the specific requirements of the weld.
Key Differences Between Frame Welding and Plate Welding
Material Shape and Size
The most obvious difference is the shape and size of the materials being welded.
Frame welding involves long, narrow pieces, while plate welding deals with larger, flat sheets.
This difference necessitates varying techniques and tools for effective welding.
Industry Applications
Although both methods can be used in similar industries, their specific applications usually differ.
Frame welding is most often associated with structural frameworks, vehicle frames, and machinery supports.
Plate welding is more likely to be found in shipbuilding, tank construction, and the manufacturing of large industrial components.
Welding Techniques
While some welding techniques can be used for both frame and plate welding, certain methods are more suited to one over the other.
For instance, Submerged Arc Welding (SAW) is highly effective for plate welding but less so for the intricate work often required in frame welding.
Conversely, TIG welding offers the precision often needed in frame welding but might not be practical for the thick, large plates used in plate welding.
Strength and Durability
Both frame and plate welding are chosen for their ability to provide strong, durable joins.
However, the kind of strength needed differs.
Frame welding provides structural integrity and support, often holding loads and stresses in buildings or vehicles.
Plate welding, particularly in applications like shipbuilding or storage tanks, focuses on creating durable, leak-proof joins that can withstand various environmental pressures.
Choosing the Right Welding Method
Project Requirements
Understanding the specific requirements of your project is the first step in choosing the right welding method.
If you’re constructing a framework for a building or vehicle, frame welding will likely be your go-to.
For projects involving large, flat pieces of metal, such as making a ship’s hull or a large storage tank, plate welding is more appropriate.
Skill Level
The skill level of the welder can also influence the choice of welding method.
Some techniques, like MIG welding, are easier to learn and more forgiving for beginners, making them suitable for both frame and some plate welding applications.
More advanced techniques, like TIG or Submerged Arc Welding, require a higher skill level and are often reserved for professionals with significant experience.
Equipment Availability
Finally, the availability of equipment and materials can also dictate your choice.
Some welding equipment is specifically designed for certain techniques and might not be suitable for both frame and plate welding.
It’s important to ensure that you have the right tools for the job to achieve the best results.
In conclusion, understanding the differences between frame welding and plate welding is crucial for making informed decisions in your welding projects.
By considering the shape and size of the materials, the industry applications, the specific techniques required, and the necessary strength and durability, you can choose the most effective welding method for your needs.
Whether you’re constructing a towering skyscraper or a sturdy ship, the right welding technique can make all the difference.
資料ダウンロード
QCD調達購買管理クラウド「newji」は、調達購買部門で必要なQCD管理全てを備えた、現場特化型兼クラウド型の今世紀最高の購買管理システムとなります。
ユーザー登録
調達購買業務の効率化だけでなく、システムを導入することで、コスト削減や製品・資材のステータス可視化のほか、属人化していた購買情報の共有化による内部不正防止や統制にも役立ちます。
NEWJI DX
製造業に特化したデジタルトランスフォーメーション(DX)の実現を目指す請負開発型のコンサルティングサービスです。AI、iPaaS、および先端の技術を駆使して、製造プロセスの効率化、業務効率化、チームワーク強化、コスト削減、品質向上を実現します。このサービスは、製造業の課題を深く理解し、それに対する最適なデジタルソリューションを提供することで、企業が持続的な成長とイノベーションを達成できるようサポートします。
オンライン講座
製造業、主に購買・調達部門にお勤めの方々に向けた情報を配信しております。
新任の方やベテランの方、管理職を対象とした幅広いコンテンツをご用意しております。
お問い合わせ
コストダウンが利益に直結する術だと理解していても、なかなか前に進めることができない状況。そんな時は、newjiのコストダウン自動化機能で大きく利益貢献しよう!
(Β版非公開)