- お役立ち記事
- The difference between Friction Stir Welding and Friction Welding
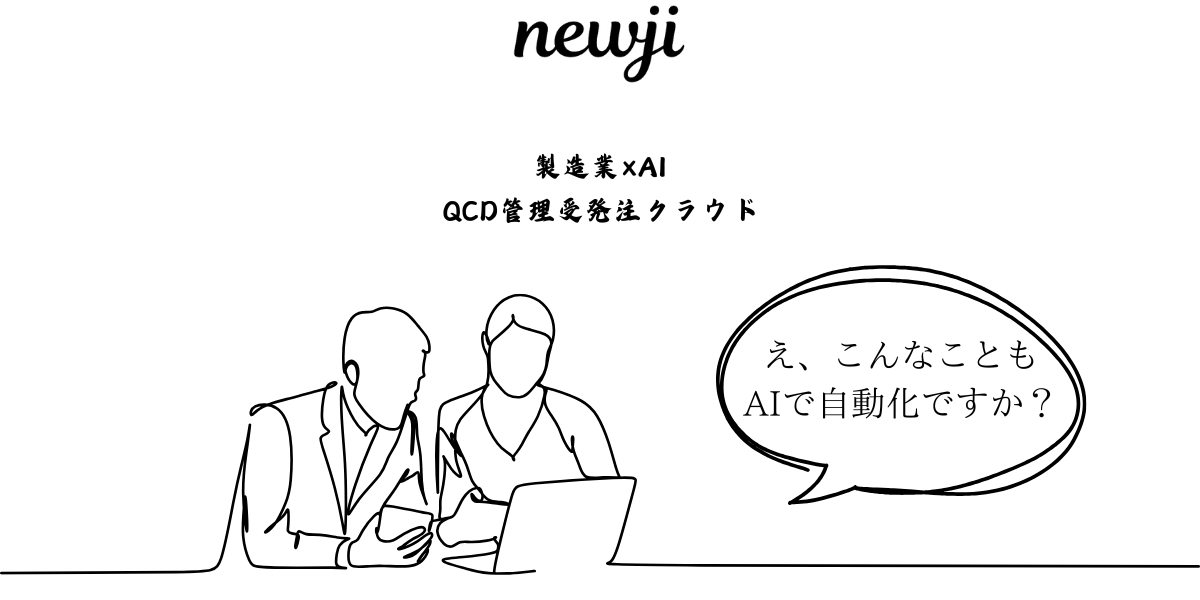
The difference between Friction Stir Welding and Friction Welding
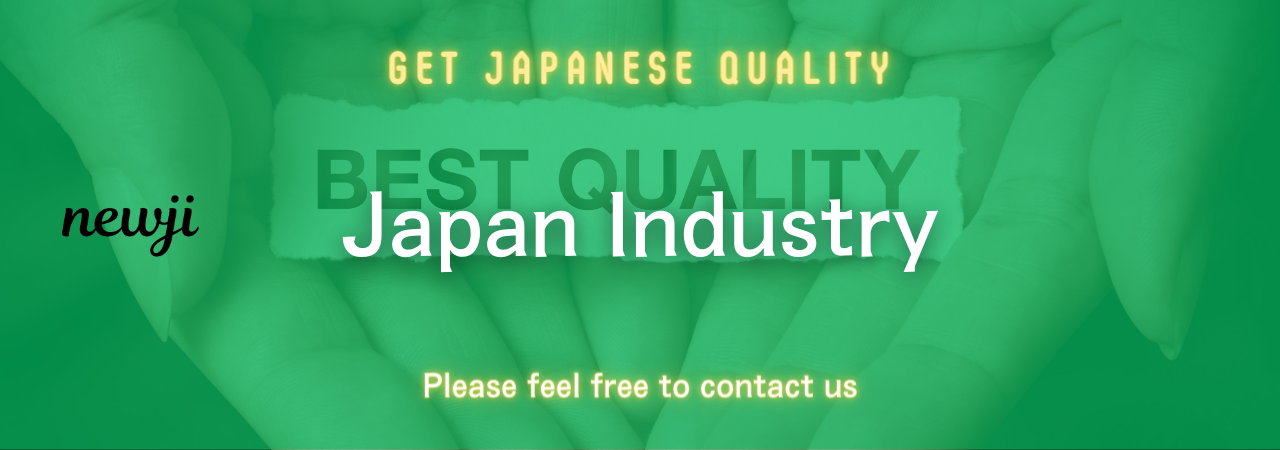
Friction Stir Welding (FSW) and Friction Welding (FW) are both popular welding techniques used in various industries today.
Though they may sound quite similar, they actually have distinct differences in process and application.
Understanding these differences is crucial in selecting the right method for a specific project.
目次
Understanding Friction Stir Welding
What is Friction Stir Welding?
Friction Stir Welding (FSW) is a solid-state joining process.
It uses a non-consumable rotating tool to join two facing workpieces without melting the material.
The process involves placing a specially designed tool between the two pieces of metal and rotating it at a high speed.
The friction from the rotating tool generates heat, softening the material and effectively stirring it together.
How Does Friction Stir Welding Work?
FSW begins with clamping the workpieces onto a fixture to hold them in place.
A rotating tool with a specific pin and shoulder design, then pierces the metal at the joint interface.
As the tool moves along the joint line, the friction generates heat, causing the material to become plasticized without reaching the melting point.
The rotating tool stirs the softened material, creating a solid-state bond as it advances along the seam.
Once the tool passes, it leaves behind a high-quality weld with minimal defects.
Benefits of Friction Stir Welding
FSW offers several advantages over traditional welding methods.
One major benefit is the absence of melting, which reduces the risk of defects such as porosity and cracking.
Additionally, FSW produces minimal distortion due to the localized heating.
The process is also energy-efficient and environmentally friendly, as it requires no filler material, flux, or shielding gas.
Applications of Friction Stir Welding
FSW is widely used in various industries, including aerospace, automotive, shipbuilding, and railways.
It is particularly beneficial for joining lightweight materials such as aluminum and magnesium, which are commonly used in these sectors.
FSW is also used in manufacturing heat exchangers, fuel tanks, and even electronics enclosures.
Understanding Friction Welding
What is Friction Welding?
Friction Welding (FW) is another solid-state welding process that joins materials through the application of mechanical friction.
Unlike FSW, which uses a rotating tool, traditional FW typically uses direct friction between the workpieces to generate heat.
This heat causes the interface material to plasticize, allowing it to join when pressure is applied.
How Does Friction Welding Work?
The FW process involves holding one workpiece stationary while the other is rotated or moved back and forth at a high speed.
The friction between the contacting surfaces generates heat, which softens the material.
Once the appropriate temperature is reached, the motion stops and an axial force is applied, compressing the softened material and forming a solid-state bond.
Excess material, known as flash, is usually expelled from the joint and can be trimmed away.
Benefits of Friction Welding
FW offers several key advantages.
It can join dissimilar materials that are otherwise difficult to weld using conventional methods.
FW provides high joint strength due to the solid-state nature of the weld, which can often be stronger than the base materials.
The process is also relatively fast and can be easily automated, making it ideal for high-volume production.
Applications of Friction Welding
FW is used in various industries, such as automotive, aerospace, and construction.
It is often employed to join shafts, tubes, and other rotational components.
FW is also utilized in the production of cutting tools, where different materials need to be joined to create a single functional component.
Key Differences Between Friction Stir Welding and Friction Welding
Process and Mechanism
The primary difference between FSW and FW lies in their processes.
FSW uses a rotating tool to generate friction and stir the material, while FW relies on direct contact between the workpieces.
In FSW, the tool moves along the joint line, whereas, in FW, one workpiece is usually either rotated or subjected to linear friction against the other.
Heat Generation and Temperature
Both methods generate heat through friction, but the temperature management differs.
FSW maintains localized heating and does not reach the melting point, preventing many of the traditional welding defects.
In contrast, FW also heats the interface but can cause flash due to the axial pressure applied during the process.
Joint Configuration and Application
FSW is particularly suitable for creating long, linear joints, such as the seams in aerospace panels or automotive body parts.
It excels in welding lightweight materials like aluminum and magnesium.
FW, however, is better suited for welding components that have rotational symmetry, like axles, drive shafts, and cutting tools.
FW is also more versatile in joining dissimilar materials that might not be compatible with melting-point-based methods.
Equipment and Tooling
FSW requires a specially designed tool with a pin and shoulder to create the joint.
This tool needs to be durable and is often made from wear-resistant materials like tool steel or carbide.
In FW, specialized equipment is used to facilitate the rapid relative motion between workpieces, such as rotating spindles or reciprocating machines.
Both methods necessitate precise control systems to ensure optimal heat generation and joint quality.
Conclusion
Friction Stir Welding and Friction Welding offer unique advantages for different industrial applications.
By understanding the differences in their processes, heat generation, and equipment requirements, manufacturers can select the most suitable welding method for their needs.
Whether joining lightweight aluminum panels for aerospace or assembling durable drive shafts for automotive use, both FSW and FW provide robust, high-quality solutions for modern manufacturing challenges.
資料ダウンロード
QCD調達購買管理クラウド「newji」は、調達購買部門で必要なQCD管理全てを備えた、現場特化型兼クラウド型の今世紀最高の購買管理システムとなります。
ユーザー登録
調達購買業務の効率化だけでなく、システムを導入することで、コスト削減や製品・資材のステータス可視化のほか、属人化していた購買情報の共有化による内部不正防止や統制にも役立ちます。
NEWJI DX
製造業に特化したデジタルトランスフォーメーション(DX)の実現を目指す請負開発型のコンサルティングサービスです。AI、iPaaS、および先端の技術を駆使して、製造プロセスの効率化、業務効率化、チームワーク強化、コスト削減、品質向上を実現します。このサービスは、製造業の課題を深く理解し、それに対する最適なデジタルソリューションを提供することで、企業が持続的な成長とイノベーションを達成できるようサポートします。
オンライン講座
製造業、主に購買・調達部門にお勤めの方々に向けた情報を配信しております。
新任の方やベテランの方、管理職を対象とした幅広いコンテンツをご用意しております。
お問い合わせ
コストダウンが利益に直結する術だと理解していても、なかなか前に進めることができない状況。そんな時は、newjiのコストダウン自動化機能で大きく利益貢献しよう!
(Β版非公開)