- お役立ち記事
- The difference between Friction Stir Welding and Friction Welding
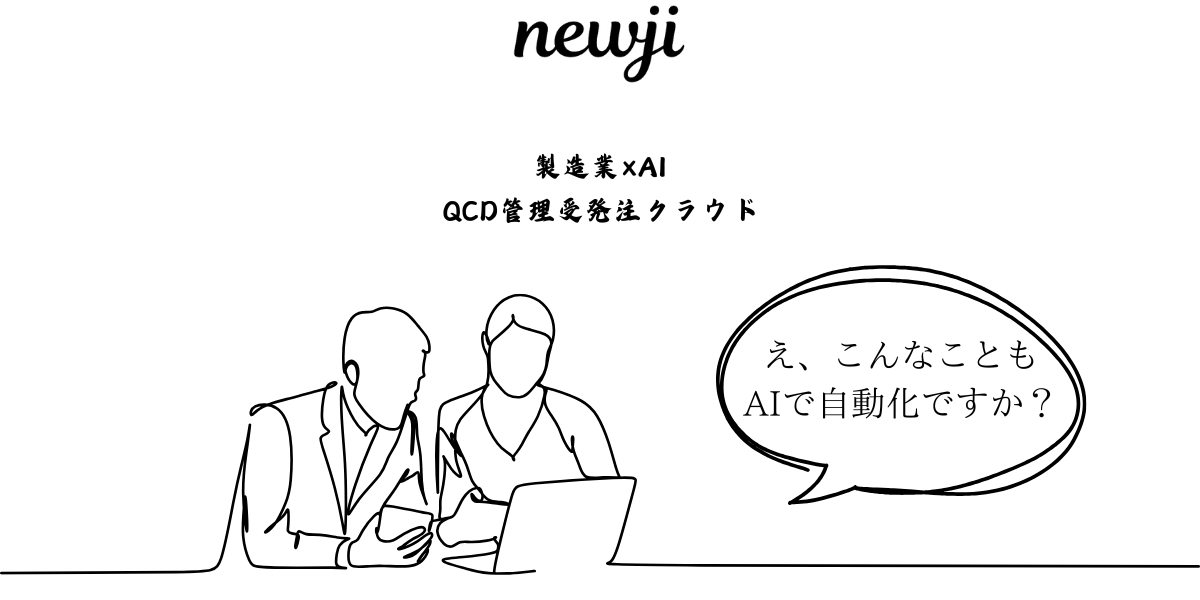
The difference between Friction Stir Welding and Friction Welding
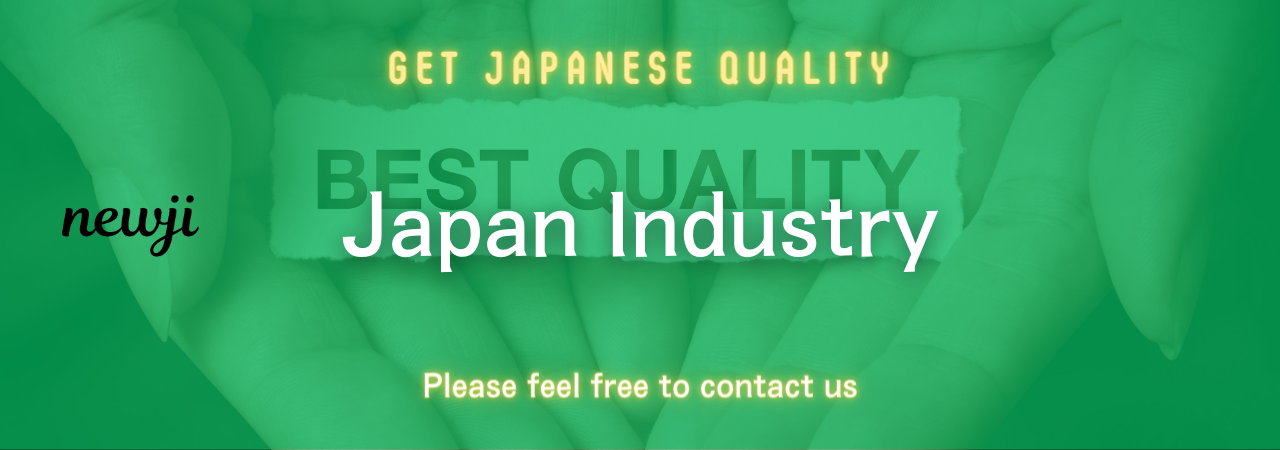
Friction Stir Welding (FSW) and Friction Welding (FW) are two innovative joining processes widely used in various industries. Knowing the differences between these two methods can help you select the right technique for your specific application.
目次
Understanding Friction Stir Welding
What is Friction Stir Welding?
Friction Stir Welding (FSW) is a solid-state joining process that uses a non-consumable tool to join two facing workpieces without melting the material. Initially developed by The Welding Institute (TWI) in 1991, FSW is particularly useful for joining aluminum and other non-ferrous materials.
How Does Friction Stir Welding Work?
In Friction Stir Welding, a rotating cylindrical tool with a specially designed pin and shoulder is inserted into the workpieces to be joined. The tool creates frictional heat, which softens the material without reaching its melting point.
Under the pressure of the tool, the softened material is stirred and mechanically mixed, forming a solid-state weld upon cooling. The process results in a high-quality joint with excellent mechanical properties and minimal distortion.
Applications of Friction Stir Welding
Friction Stir Welding is widely used in aerospace, automotive, shipbuilding, and railway industries. The process is ideal for fabricating large panels, such as aircraft wings, automotive body panels, and ship hulls, where traditional welding techniques may be challenging to implement.
Understanding Friction Welding
What is Friction Welding?
Friction Welding (FW) is another solid-state joining process that joins materials by generating heat through mechanical friction between workpieces, combined with an applied axial force. Unlike conventional welding, Friction Welding does not melt the workpieces. Instead, it relies on pressure and high rotational speeds to create a strong bond.
How Does Friction Welding Work?
In Friction Welding, one of the workpieces is fixed while the other is rotated at high speeds. The contact between the surfaces generates frictional heat, softening the materials at the interface. Once sufficient heat is generated, rotation is stopped, and the workpieces are pressed together under high pressure. The softened materials forge a bond, creating a strong, homogenous joint.
Applications of Friction Welding
Friction Welding is commonly used in the aerospace, automotive, and oil and gas industries. Typical applications include joining dissimilar metals, such as steel to aluminum, creating engine components, and assembling drill pipes. The method is efficient and versatile, making it suitable for various industrial applications.
Key Differences Between Friction Stir Welding and Friction Welding
Process Fundamentals
The primary difference lies in the fundamental mechanism of the processes. Friction Stir Welding uses a non-consumable tool to generate frictional heat and mechanically stir the materials, while Friction Welding relies on rotational or linear motion and pressure to produce heat and forge the joint.
Tooling and Equipment
Friction Stir Welding requires a rotating tool with a specially designed pin and shoulder, and a rigid clamping system to hold the workpieces in place. On the other hand, Friction Welding typically uses a lathe or similar rotary machine to spin one of the workpieces and apply axial pressure.
Material Compatibility
Friction Stir Welding is particularly effective for joining aluminum and other non-ferrous materials. Although it can be used with some ferrous materials, the tool wear tends to be higher. Friction Welding, however, is suitable for a broader range of materials, including various metals, plastics, and even ceramics. It is also ideal for joining dissimilar materials, which is often challenging with traditional welding methods.
Joint Quality
Both methods produce high-quality joints, but friction stir welded joints generally have superior mechanical properties, such as higher tensile and shear strength, due to the homogeneous mixing of the material. Friction Welding can also produce strong joints, but the quality may vary depending on the materials and process parameters used.
Applications
Friction Stir Welding is used for large, continuous welds, such as those found in aerospace and automotive panels. Friction Welding is commonly employed for smaller, rotationally symmetrical parts, such as drive shafts, valves, and bushings. The choice between the two methods often depends on the specific application and the materials involved.
Heat Affected Zone (HAZ)
The Heat Affected Zone (HAZ) is the region in the workpiece that experiences temperature changes during welding, which can affect its mechanical properties. Friction Stir Welding produces a smaller HAZ, resulting in minimal distortion and improved joint quality. Friction Welding also creates a relatively small HAZ compared to traditional welding methods, but the size and impact may vary depending on the specific process and materials used.
Benefits and Limitations
Benefits of Friction Stir Welding
One of the key benefits of Friction Stir Welding is the ability to join materials without melting, resulting in high-quality, defect-free welds with minimal distortion.
The process is energy-efficient and environmentally friendly, producing minimal fumes and emissions.
Additionally, FSW is suitable for a wide range of material thicknesses and joint configurations, offering versatility in various applications.
Limitations of Friction Stir Welding
Despite its advantages, Friction Stir Welding has some limitations. The required tooling can be expensive, and the process may not be suitable for very thin materials or complex joint geometries. High tool wear can also be a concern, particularly when welding harder materials.
Benefits of Friction Welding
Friction Welding offers several benefits, including the ability to join dissimilar materials and create strong, reliable joints without filler materials. The process is relatively fast and efficient, making it suitable for high-volume production. It also produces minimal distortion and a small HAZ, maintaining the integrity of the workpieces.
Limitations of Friction Welding
Friction Welding has some limitations, including the need for precise alignment of the workpieces and the requirement for rotationally symmetrical parts. The process may also be less suitable for very large or irregularly shaped components.
Conclusion
Understanding the key differences between Friction Stir Welding and Friction Welding is essential for selecting the right technique for your application. Both methods offer unique advantages and are widely used in various industries. By considering factors such as material compatibility, joint quality, and process limitations, you can make an informed decision and achieve optimal results in your welding projects.
資料ダウンロード
QCD調達購買管理クラウド「newji」は、調達購買部門で必要なQCD管理全てを備えた、現場特化型兼クラウド型の今世紀最高の購買管理システムとなります。
ユーザー登録
調達購買業務の効率化だけでなく、システムを導入することで、コスト削減や製品・資材のステータス可視化のほか、属人化していた購買情報の共有化による内部不正防止や統制にも役立ちます。
NEWJI DX
製造業に特化したデジタルトランスフォーメーション(DX)の実現を目指す請負開発型のコンサルティングサービスです。AI、iPaaS、および先端の技術を駆使して、製造プロセスの効率化、業務効率化、チームワーク強化、コスト削減、品質向上を実現します。このサービスは、製造業の課題を深く理解し、それに対する最適なデジタルソリューションを提供することで、企業が持続的な成長とイノベーションを達成できるようサポートします。
オンライン講座
製造業、主に購買・調達部門にお勤めの方々に向けた情報を配信しております。
新任の方やベテランの方、管理職を対象とした幅広いコンテンツをご用意しております。
お問い合わせ
コストダウンが利益に直結する術だと理解していても、なかなか前に進めることができない状況。そんな時は、newjiのコストダウン自動化機能で大きく利益貢献しよう!
(Β版非公開)