- お役立ち記事
- The difference between Fused Deposition Modeling (FDM) and Selective Laser Sintering (SLS)
The difference between Fused Deposition Modeling (FDM) and Selective Laser Sintering (SLS)
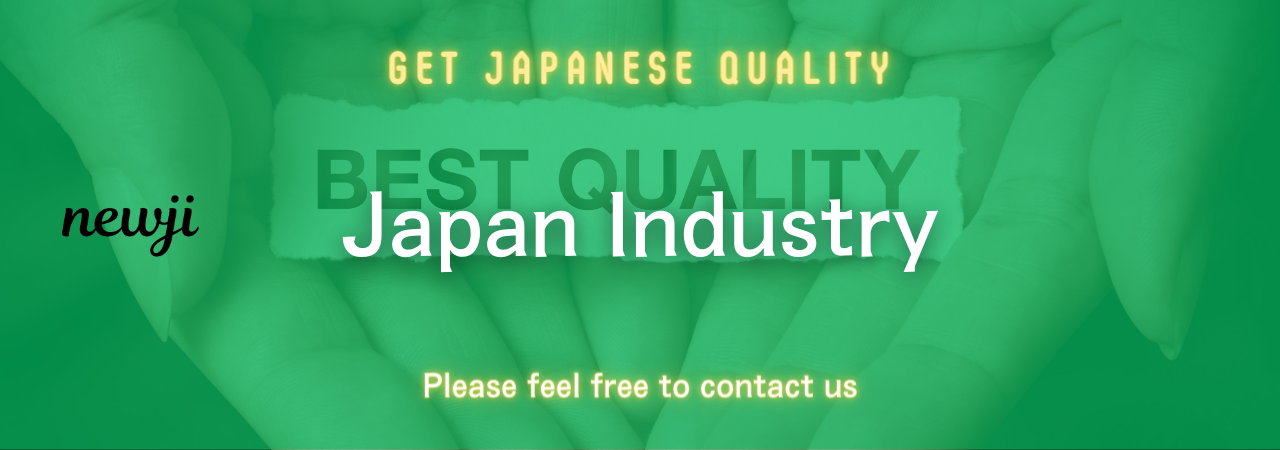
When it comes to 3D printing, two common methods you might come across are Fused Deposition Modeling (FDM) and Selective Laser Sintering (SLS).
Each of these techniques offers unique advantages and is suitable for different applications. Knowing the differences between them can help you decide which one is best suited to your needs.
目次
What is Fused Deposition Modeling (FDM)?
Fused Deposition Modeling (FDM) is a popular 3D printing technology known for its simplicity and affordability.
In FDM, a thermoplastic filament is fed into an extruder, where it is heated and then deposited layer by layer to build a 3D object.
The process is straightforward and is widely used in both consumer and industrial 3D printing.
How Does FDM Work?
In FDM, the 3D printer follows these steps:
1. The filament, usually made of plastic like ABS or PLA, is loaded into the extruder.
2. The filament is heated to melt it.
3. The melted filament is then extruded through a nozzle.
4. The print head moves according to the design, depositing the material in layers to create the object.
Advantages of FDM
FDM has several benefits:
– Cost-Effective: FDM printers are relatively inexpensive compared to other 3D printing technologies.
– Versatile Material Options: FDM can use a variety of materials, including ABS, PLA, and PETG.
– Ease of Use: The technology is user-friendly and widely accessible, making it ideal for beginners and hobbyists.
– Good for Prototyping: FDM is excellent for creating prototypes and functional parts quickly.
What is Selective Laser Sintering (SLS)?
Selective Laser Sintering (SLS) is another 3D printing method, but it is quite different from FDM.
SLS uses a laser to sinter powdered material, bonding it together to form a solid structure.
It is a more complex and typically more expensive process, but it offers high precision and strength.
How Does SLS Work?
In SLS, the process involves these steps:
1. A thin layer of powdered material is spread across the build platform.
2. A laser selectively heats and fuses the powdered material based on the design.
3. The build platform lowers, and a new layer of powder is spread over the previous layer.
4. This process repeats until the entire object is formed.
Advantages of SLS
Here are some advantages of SLS:
– High Precision: SLS produces very detailed and complex parts with high accuracy.
– Strong and Durable: Parts created with SLS are often stronger and more durable than those made with FDM.
– No Support Structures Needed: Since the powder supports the part during printing, there’s no need for additional support structures.
– Wide Material Range: SLS can use various materials, including nylon, glass-filled nylon, and metals.
Comparing FDM and SLS
While both FDM and SLS are used for 3D printing, they have distinct differences that make them suitable for different applications.
Cost
FDM is generally more cost-effective than SLS.
FDM printers and materials are cheaper, making it a popular choice for hobbyists and small businesses.
SLS, on the other hand, is more expensive due to the sophisticated machinery and materials required.
Print Quality
SLS offers superior print quality compared to FDM.
It produces highly detailed and complex parts with better mechanical properties.
FDM prints may have visible layer lines and may require post-processing to achieve a smooth finish.
Material Properties
SLS materials are usually stronger and more durable than those used in FDM.
FDM materials are limited to thermoplastics, while SLS can use a broader range of materials, including metals and composites.
Design Flexibility
SLS provides greater design freedom.
You can create intricate and complex geometries without worrying about support structures.
FDM may require support materials for overhangs and complex shapes, which can limit design possibilities.
Application Areas
FDM is widely used for prototyping, educational purposes, and hobbyist projects.
It’s fantastic for creating simple parts quickly and affordably.
SLS, however, is more suited for industrial applications where high precision and durability are critical.
It’s often used in aerospace, automotive, and medical fields.
Speed
FDM can be faster than SLS for printing simple and small objects.
SLS, though more complex and time-consuming, is faster for producing detailed and high-quality parts.
Which One Should You Choose?
Choosing between FDM and SLS depends on your specific needs and budget.
If you are a hobbyist or need to create simple prototypes quickly and affordably, FDM is likely the best choice.
On the other hand, if you require high precision, durability, and can afford the higher cost, SLS might be the better option.
Consider factors such as print quality, material properties, design complexity, cost, and application areas when making your decision.
Both FDM and SLS have their unique strengths and can be excellent tools for creating 3D printed objects.
Understanding their differences will help you make an informed choice and achieve the best results for your projects.
資料ダウンロード
QCD調達購買管理クラウド「newji」は、調達購買部門で必要なQCD管理全てを備えた、現場特化型兼クラウド型の今世紀最高の購買管理システムとなります。
ユーザー登録
調達購買業務の効率化だけでなく、システムを導入することで、コスト削減や製品・資材のステータス可視化のほか、属人化していた購買情報の共有化による内部不正防止や統制にも役立ちます。
NEWJI DX
製造業に特化したデジタルトランスフォーメーション(DX)の実現を目指す請負開発型のコンサルティングサービスです。AI、iPaaS、および先端の技術を駆使して、製造プロセスの効率化、業務効率化、チームワーク強化、コスト削減、品質向上を実現します。このサービスは、製造業の課題を深く理解し、それに対する最適なデジタルソリューションを提供することで、企業が持続的な成長とイノベーションを達成できるようサポートします。
オンライン講座
製造業、主に購買・調達部門にお勤めの方々に向けた情報を配信しております。
新任の方やベテランの方、管理職を対象とした幅広いコンテンツをご用意しております。
お問い合わせ
コストダウンが利益に直結する術だと理解していても、なかなか前に進めることができない状況。そんな時は、newjiのコストダウン自動化機能で大きく利益貢献しよう!
(Β版非公開)