- お役立ち記事
- The difference between High-pressure Casting and Low-pressure Casting
月間76,176名の
製造業ご担当者様が閲覧しています*
*2025年3月31日現在のGoogle Analyticsのデータより
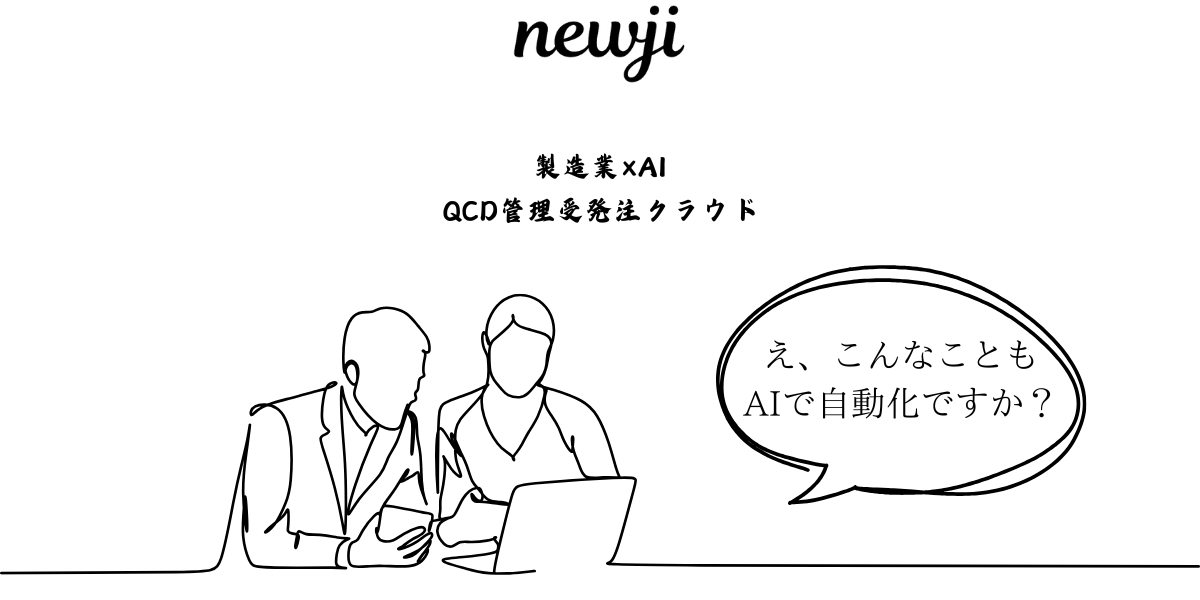
The difference between High-pressure Casting and Low-pressure Casting
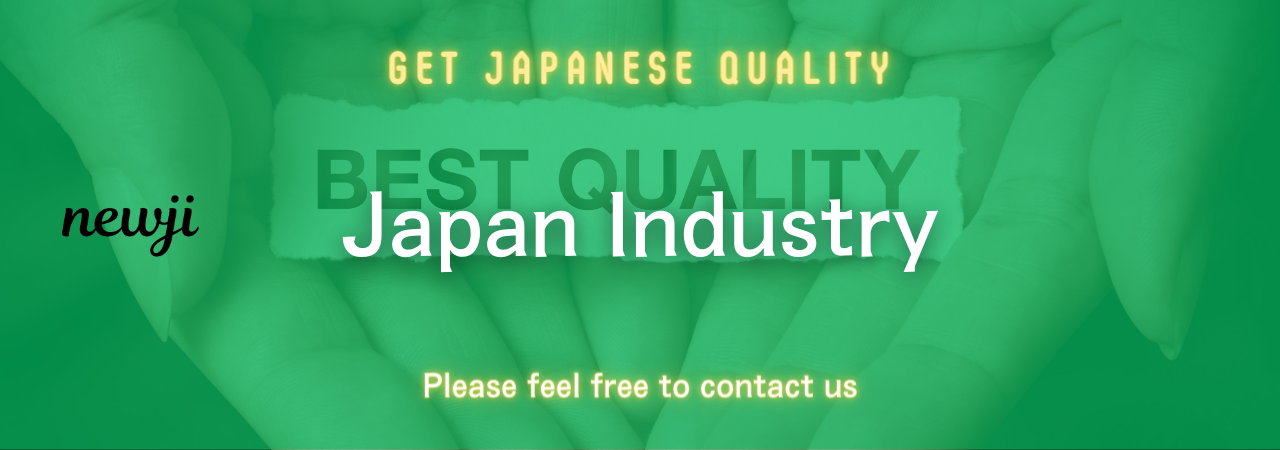
Casting is a manufacturing process where a liquid material is poured into a mold and allowed to solidify.
Casting is used in a variety of industries to create complex shapes and structures from metals and other materials.
Two common types of casting are high-pressure casting and low-pressure casting.
Although both methods aim to produce high-quality castings, they differ significantly in terms of process, equipment, and applications.
This article explores the differences between high-pressure casting and low-pressure casting in detail.
目次
What is High-Pressure Casting?
High-pressure casting, often referred to as die casting, is a manufacturing process where molten metal is forced into a steel mold or die at high pressure.
The pressure can range from 1,500 to 25,000 psi (pounds per square inch), depending on the type of metal and the complexity of the part.
This high pressure ensures that the molten metal fills every detail of the mold cavity, resulting in a highly precise and smooth finish.
The Process of High-Pressure Casting
The high-pressure casting process starts with melting the metal in a furnace.
Once the metal reaches the required temperature, it is transferred to a shot chamber.
A piston then forces the molten metal into the die at high pressure.
After the metal solidifies, the mold is opened, and the casting is ejected.
Advantages of High-Pressure Casting
– **Precision**: High-pressure casting provides excellent dimensional accuracy, making it ideal for manufacturing parts that require tight tolerances.
– **Speed**: The high-pressure process allows for rapid production cycles, making it suitable for mass production.
– **Surface Finish**: The resulting castings have a smooth surface finish, reducing the need for further machining.
Disadvantages of High-Pressure Casting
– **Cost**: The initial setup costs for high-pressure casting are relatively high due to the expense of the die and machinery.
– **Size Limitation**: It is more suitable for smaller parts as larger parts would require more substantial equipment and energy.
What is Low-Pressure Casting?
Low-pressure casting, on the other hand, involves the slow filling of a mold with molten metal using low pressure, usually between 3 to 15 psi.
This process offers better control over the filling of the mold, reducing the risk of defects and resulting in castings with excellent mechanical properties.
The Process of Low-Pressure Casting
In low-pressure casting, the molten metal is stored in a holding furnace below the mold.
A tube extends from the furnace to the mold.
Low pressure is applied to force the molten metal up through the tube and into the mold cavity.
The pressure is maintained until the metal solidifies.
After solidification, the mold is opened, and the casting is removed.
Advantages of Low-Pressure Casting
– **Quality**: Low-pressure casting produces castings with excellent mechanical properties, such as high strength and good ductility.
– **Reduced Defects**: The slow filling process minimizes turbulence and reduces the risk of defects like porosity and misruns.
– **Versatility**: It is suitable for a wide range of metals and allows for the production of large and complex parts.
Disadvantages of Low-Pressure Casting
– **Speed**: The process is slower compared to high-pressure casting, making it less suitable for large-scale production.
– **Initial Setup**: While the cost is generally lower than high-pressure casting, the initial setup can still be relatively expensive.
Comparing High-Pressure Casting and Low-Pressure Casting
Application Areas
High-pressure casting is commonly used in industries such as automotive, aerospace, and electronics, where high precision and surface finish are critical.
Typical products include engine components, housing for electronic devices, and brackets.
Low-pressure casting is often used in the production of automotive wheels, large structural components, and valves.
It is favored in applications where the mechanical properties of the casting are more important than the production speed.
Material Suitability
High-pressure casting is generally used for non-ferrous metals like aluminum, magnesium, and zinc.
These metals have a lower melting point, making them suitable for the rapid filling and cooling cycles in high-pressure casting.
Low-pressure casting, however, is more versatile and can accommodate a wider range of metals, including both ferrous and non-ferrous materials.
This makes it useful for a broader array of applications.
Production Volume
High-pressure casting is ideal for high-volume production due to its rapid cycle time and repeatable process.
It allows manufacturers to produce thousands of identical parts quickly and efficiently.
Low-pressure casting is better suited for low to medium-volume production.
It excels in producing fewer parts with high mechanical integrity.
Cost Considerations
The initial setup and tooling costs for high-pressure casting are relatively high, but the cost per part decreases significantly with increased production volumes.
This makes it cost-effective for long production runs.
Low-pressure casting generally has lower initial setup costs and is more economical for small to medium production runs.
However, the cost per part is higher compared to high-pressure casting when scaled to large volumes.
Conclusion
Both high-pressure casting and low-pressure casting offer unique advantages and are suited to different applications.
High-pressure casting excels in precision, speed, and surface finish, making it ideal for high-volume production of smaller, intricate parts.
Low-pressure casting, on the other hand, offers superior mechanical properties and fewer defects, suitable for larger, complex parts and lower production volumes.
Understanding the differences between these two casting methods helps manufacturers choose the right process based on their specific requirements.
Whether you need high precision and rapid production or excellent mechanical properties and reduced defects, there is a casting method that meets your needs.
資料ダウンロード
QCD管理受発注クラウド「newji」は、受発注部門で必要なQCD管理全てを備えた、現場特化型兼クラウド型の今世紀最高の受発注管理システムとなります。
ユーザー登録
受発注業務の効率化だけでなく、システムを導入することで、コスト削減や製品・資材のステータス可視化のほか、属人化していた受発注情報の共有化による内部不正防止や統制にも役立ちます。
NEWJI DX
製造業に特化したデジタルトランスフォーメーション(DX)の実現を目指す請負開発型のコンサルティングサービスです。AI、iPaaS、および先端の技術を駆使して、製造プロセスの効率化、業務効率化、チームワーク強化、コスト削減、品質向上を実現します。このサービスは、製造業の課題を深く理解し、それに対する最適なデジタルソリューションを提供することで、企業が持続的な成長とイノベーションを達成できるようサポートします。
製造業ニュース解説
製造業、主に購買・調達部門にお勤めの方々に向けた情報を配信しております。
新任の方やベテランの方、管理職を対象とした幅広いコンテンツをご用意しております。
お問い合わせ
コストダウンが利益に直結する術だと理解していても、なかなか前に進めることができない状況。そんな時は、newjiのコストダウン自動化機能で大きく利益貢献しよう!
(β版非公開)