- お役立ち記事
- The difference between High-temperature Forming and Low-temperature Forming
月間76,176名の
製造業ご担当者様が閲覧しています*
*2025年3月31日現在のGoogle Analyticsのデータより
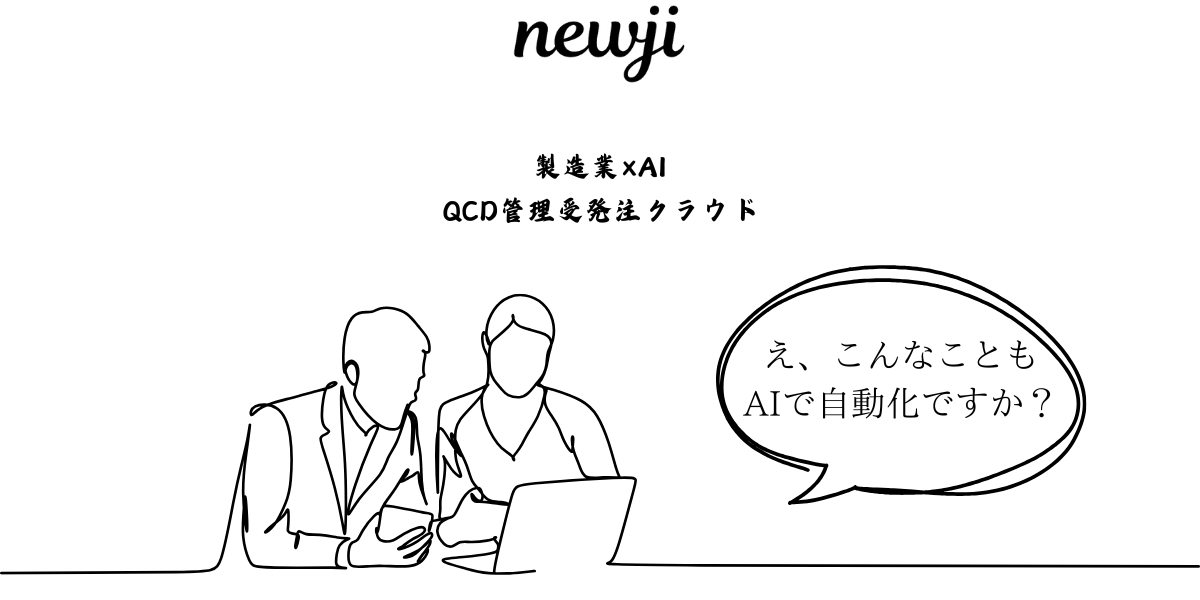
The difference between High-temperature Forming and Low-temperature Forming
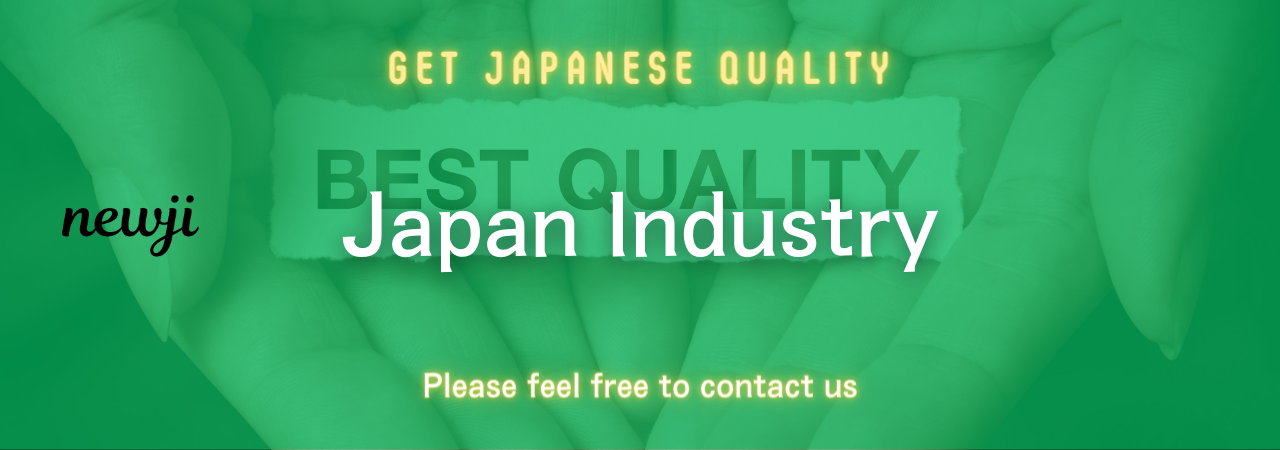
Forming is a fundamental aspect of material science and manufacturing where materials are modified into specific shapes through various processes.
Understanding the difference between high-temperature forming and low-temperature forming is crucial for selecting the appropriate method for your project.
In this article, we will delve into these two forming methods while discussing their unique properties, advantages, and applications.
目次
What is High-Temperature Forming?
High-temperature forming involves manipulating materials at elevated temperatures to achieve desired shapes and properties.
This technique is essential for materials that are difficult to form at room temperature, such as metals and certain polymers.
How Does High-Temperature Forming Work?
During high-temperature forming, the temperature of the workpiece is increased substantially.
This helps in reducing the strength and hardness of the material, making it more malleable and easier to shape.
Common methods of high-temperature forming include forging, hot rolling, and hot extrusion.
Advantages of High-Temperature Forming
1. Enhanced Ductility: Increasing temperature enhances the ductility of materials, making them easier to shape without cracking.
2. Decreased Force Requirement: The reduced hardness means less force is needed to form the material.
3. Improved Properties: High-temperature forming can alter the grain structure of a material, leading to improved mechanical properties.
Applications of High-Temperature Forming
High-temperature forming is extensively used in industries such as aerospace, automotive, and construction.
For example, forging is utilized to create high-strength components like crankshafts and gears.
Hot rolling is used to produce sheets and plates of metal employed in various structural applications.
What is Low-Temperature Forming?
Low-temperature forming, or cold forming, involves shaping materials at or near room temperature.
This method is suitable for materials that exhibit sufficient plasticity and can be shaped without the need for high heat.
How Does Low-Temperature Forming Work?
In low-temperature forming, the material is deformed using mechanical forces without significantly altering its temperature.
Processes such as cold rolling, cold drawing, and stamping fall under this category.
Advantages of Low-Temperature Forming
1. No Need for Additional Heating: Eliminates the energy costs associated with heating materials, making it more cost-effective.
2. Improved Surface Finish: Since the material isn’t exposed to high temperatures, it retains a superior surface finish.
3. Increased Strength: Strain-hardening occurs during cold forming, resulting in an increase in material strength.
Applications of Low-Temperature Forming
Low-temperature forming is used widely in the manufacturing of components that require high precision and good surface quality.
For instance, cold rolling is used to produce thin metal sheets for automotive and electronics industries.
Cold drawing creates wires and tubes that meet precise dimensional tolerances.
Key Differences Between High-Temperature and Low-Temperature Forming
Temperature Conditions
The most obvious difference is the temperature at which the processes occur.
High-temperature forming operates at significantly elevated temperatures, while low-temperature forming works at ambient or near-ambient temperatures.
Material Properties
High-temperature forming affects the material’s internal structure, making it more ductile and less hard.
Low-temperature forming, on the other hand, often results in strain-hardening, increasing the material’s strength.
Surface Finish
High-temperature forming can impact the surface finish due to oxidation and scaling.
In contrast, low-temperature forming usually maintains a better surface quality as the material is not exposed to high temperatures.
Energy Consumption
High-temperature forming requires considerable energy to heat the material.
Low-temperature forming processes are generally more energy-efficient as they eliminate the need for additional heating.
Tooling and Equipment
The tools and equipment used in high-temperature forming are designed to withstand high temperatures, making them robust but also more expensive.
In contrast, low-temperature forming equipment operates under less demanding conditions, which can result in lower manufacturing costs.
Choosing the Right Forming Process
Choosing between high-temperature and low-temperature forming depends on several factors such as the material to be formed, required mechanical properties, and economic considerations.
High-temperature forming is the go-to method for creating large, high-strength components.
Low-temperature forming, however, is preferable for producing high-precision parts with excellent surface quality.
Material Suitability
Some materials are inherently better suited to specific forming methods.
For instance, high-temperature forming is typically needed for metals like titanium and certain high-performance alloys that are difficult to shape at room temperature.
Conversely, low-temperature forming is suitable for metals such as aluminum and copper that exhibit good plasticity at ambient temperatures.
End-Use Requirements
The end-use requirements, such as the desired mechanical properties and dimensional tolerances, also play a crucial role in deciding the forming method.
Components that require high ductility and toughness are better suited for high-temperature forming.
Parts that need high precision and surface finish are ideal candidates for low-temperature forming.
Cost Considerations
Finally, cost considerations often influence the decision.
While high-temperature forming can offer superior mechanical properties, it is generally more expensive due to higher energy consumption and tooling costs.
Low-temperature forming, being more energy-efficient, often presents a more cost-effective option for certain applications.
Understanding the differences between high-temperature forming and low-temperature forming enables manufacturers and engineers to select the appropriate process for their specific requirements.
Each method has its own set of advantages and is suited to different applications.
By making informed decisions, you can optimize performance, improve efficiency, and ultimately achieve better outcomes in your manufacturing endeavors.
資料ダウンロード
QCD管理受発注クラウド「newji」は、受発注部門で必要なQCD管理全てを備えた、現場特化型兼クラウド型の今世紀最高の受発注管理システムとなります。
ユーザー登録
受発注業務の効率化だけでなく、システムを導入することで、コスト削減や製品・資材のステータス可視化のほか、属人化していた受発注情報の共有化による内部不正防止や統制にも役立ちます。
NEWJI DX
製造業に特化したデジタルトランスフォーメーション(DX)の実現を目指す請負開発型のコンサルティングサービスです。AI、iPaaS、および先端の技術を駆使して、製造プロセスの効率化、業務効率化、チームワーク強化、コスト削減、品質向上を実現します。このサービスは、製造業の課題を深く理解し、それに対する最適なデジタルソリューションを提供することで、企業が持続的な成長とイノベーションを達成できるようサポートします。
製造業ニュース解説
製造業、主に購買・調達部門にお勤めの方々に向けた情報を配信しております。
新任の方やベテランの方、管理職を対象とした幅広いコンテンツをご用意しております。
お問い合わせ
コストダウンが利益に直結する術だと理解していても、なかなか前に進めることができない状況。そんな時は、newjiのコストダウン自動化機能で大きく利益貢献しよう!
(β版非公開)