- お役立ち記事
- The difference between Honing and Lapping
月間76,176名の
製造業ご担当者様が閲覧しています*
*2025年3月31日現在のGoogle Analyticsのデータより
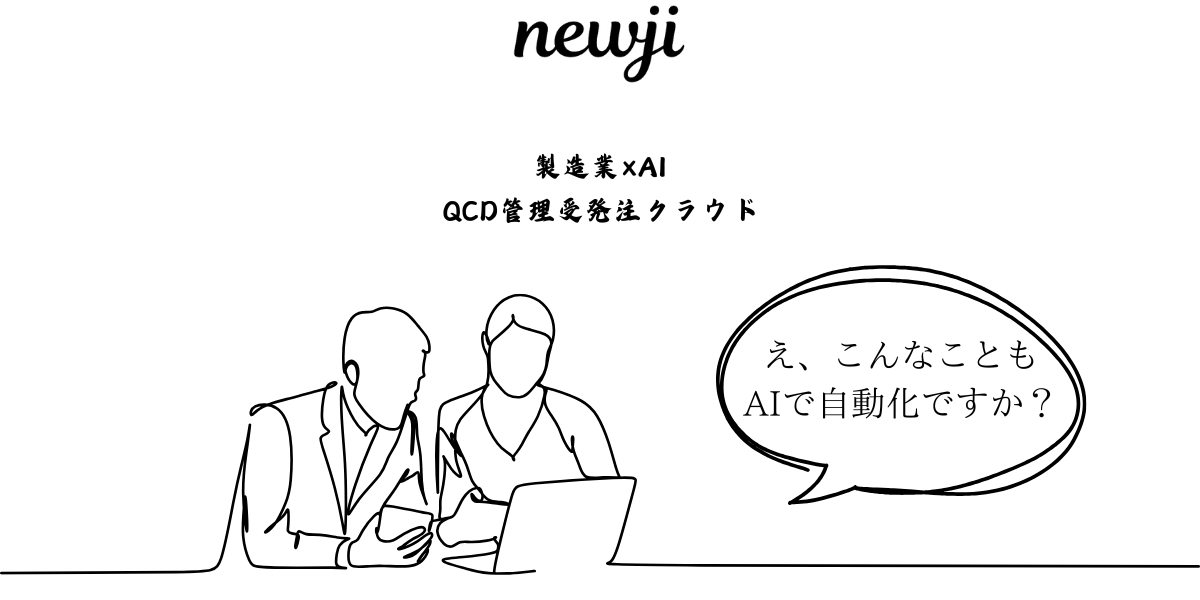
The difference between Honing and Lapping
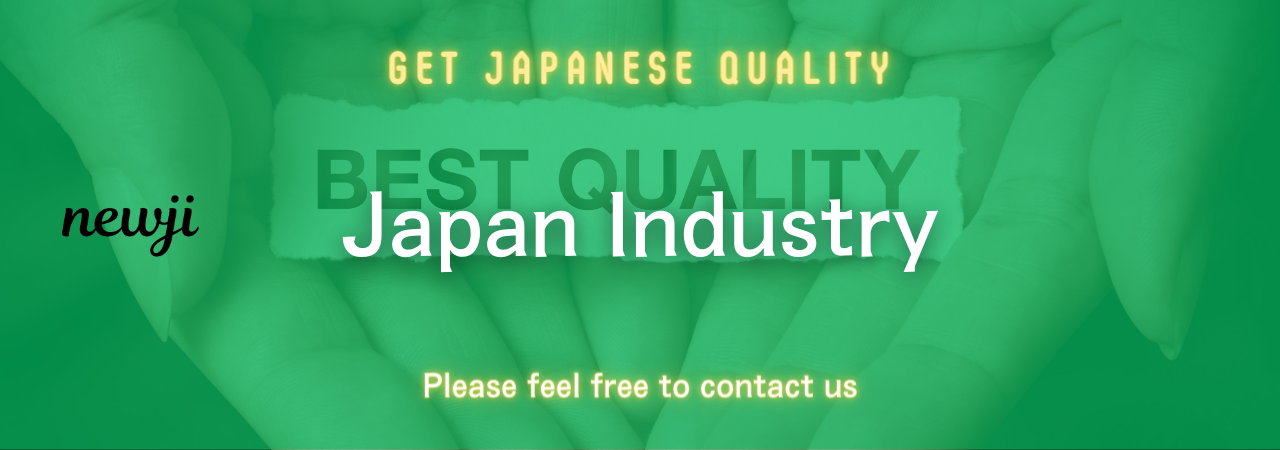
Honing and lapping are both finishing processes used to achieve high levels of surface smoothness and precision in various materials.
Although these terms are often used interchangeably, honing and lapping have distinct differences.
Understanding these differences can help in selecting the appropriate method for a specific application.
目次
What is Honing?
Honing is an abrasive machining process that involves the use of a honing stone or abrasive stick.
The goal is to improve the geometric form of a surface, as well as its texture.
Honing is commonly used to refine the bore of cylinders, such as those in engines.
The Process
In honing, a rotating tool carrying an abrasive material is used to remove small amounts of material from the interior surface of a cylinder.
This tool moves in a specific pattern to ensure even and precise abrasion.
The process is typically lubricated to reduce heat and friction and to wash away debris.
Materials Used
Honing tools are usually made of aluminum oxide, silicon carbide, or diamond.
These materials are selected based on the hardness of the workpiece material and the required level of precision.
Applications
Honing is frequently used in the automotive industry.
Engine cylinders, hydraulic cylinders, and gears are often honed to achieve the required level of precision.
Other common applications include manufacturing tools and machine parts where high precision is crucial.
What is Lapping?
Lapping is another abrasive process, but it focuses more on achieving extreme flatness and smoothness.
The process involves using loose abrasives between two surfaces that are rubbing together.
The Process
Lapping involves placing a mixture of abrasive material and a liquid lubricant between the workpiece and a lapping plate.
The workpiece and the plate are then pressed together and moved in a controlled manner.
This causes the abrasive particles to grind against the material, smoothing it and bringing it to the desired thickness and flatness.
Unlike honing, lapping does not involve a rotating tool but rather relies on relative motion between surfaces.
Materials Used
The abrasives used in lapping can include aluminum oxide, silicon carbide, and diamond.
The selection of abrasive depends on the material being worked on and the required finish.
Applications
Lapping is commonly used in industries where a high degree of surface smoothness and flatness is essential.
Optics, semiconductors, and some areas of precision manufacturing regularly use lapping.
It’s ideal for products like lenses, mirrors, and mechanical seals.
Key Differences Between Honing and Lapping
While both honing and lapping are finishing processes, they have several key differences:
Purpose
Honing is primarily used for refining the geometry of a hole or cylindrical surface.
In contrast, lapping is used mainly for achieving extreme flatness and smoothness on flat or slightly curved surfaces.
Abrasive Material
Honing uses a fixed abrasive material attached to a tool, whereas lapping employs loose abrasive particles suspended in a fluid medium.
Motion
Honing involves rotational motion combined with a reciprocating or oscillating action.
Lapping relies on relative motion between two surfaces with the abrasive in between.
Surface Finish
Honing typically achieves a finish that is suitable for many mechanical applications.
Lapping, however, can achieve a much finer finish, often in the nanometer range, suitable for optics and precision components.
Advantages and Disadvantages
Honing Advantages
– High Precision: Honing can achieve high levels of dimensional accuracy.
– Material Flexibility: Suitable for a wide range of materials, including metals and ceramics.
– Versatility: Effective for various shapes, especially cylindrical surfaces.
Honing Disadvantages
– Not Ideal for Flat Surfaces: Honing is not suited for achieving flatness.
– Equipment Costs: Honing machines and tools can be expensive.
Lapping Advantages
– Exceptional Surface Finish: Achieves extremely smooth and flat surfaces.
– Precision: High levels of precision make it ideal for critical applications.
– No Rotational Tool: Fewer constraints on the shape of the workpiece.
Lapping Disadvantages
– Time-Consuming: The lapping process can be slow, especially for larger surfaces.
– Limited to Flat Surfaces: Lapping is not effective for refining cylindrical or highly contoured surfaces.
Choosing Between Honing and Lapping
The choice between honing and lapping depends on various factors, including the required surface finish, material type, and geometric requirements.
For instance, if you need to achieve a highly smooth and flat surface on a small optical component, lapping may be the better option.
On the other hand, if your goal is to refine the internal geometry of an engine cylinder, honing would be more suitable.
Conclusion
Understanding the differences between honing and lapping is essential for making informed decisions in manufacturing processes.
Each has its unique advantages and limitations, making them suitable for different applications.
By knowing when to use honing or lapping, you can achieve the desired level of precision and surface quality in your specific work piece.
資料ダウンロード
QCD管理受発注クラウド「newji」は、受発注部門で必要なQCD管理全てを備えた、現場特化型兼クラウド型の今世紀最高の受発注管理システムとなります。
ユーザー登録
受発注業務の効率化だけでなく、システムを導入することで、コスト削減や製品・資材のステータス可視化のほか、属人化していた受発注情報の共有化による内部不正防止や統制にも役立ちます。
NEWJI DX
製造業に特化したデジタルトランスフォーメーション(DX)の実現を目指す請負開発型のコンサルティングサービスです。AI、iPaaS、および先端の技術を駆使して、製造プロセスの効率化、業務効率化、チームワーク強化、コスト削減、品質向上を実現します。このサービスは、製造業の課題を深く理解し、それに対する最適なデジタルソリューションを提供することで、企業が持続的な成長とイノベーションを達成できるようサポートします。
製造業ニュース解説
製造業、主に購買・調達部門にお勤めの方々に向けた情報を配信しております。
新任の方やベテランの方、管理職を対象とした幅広いコンテンツをご用意しております。
お問い合わせ
コストダウンが利益に直結する術だと理解していても、なかなか前に進めることができない状況。そんな時は、newjiのコストダウン自動化機能で大きく利益貢献しよう!
(β版非公開)