- お役立ち記事
- The difference between Impact Extrusion and Cold Extrusion
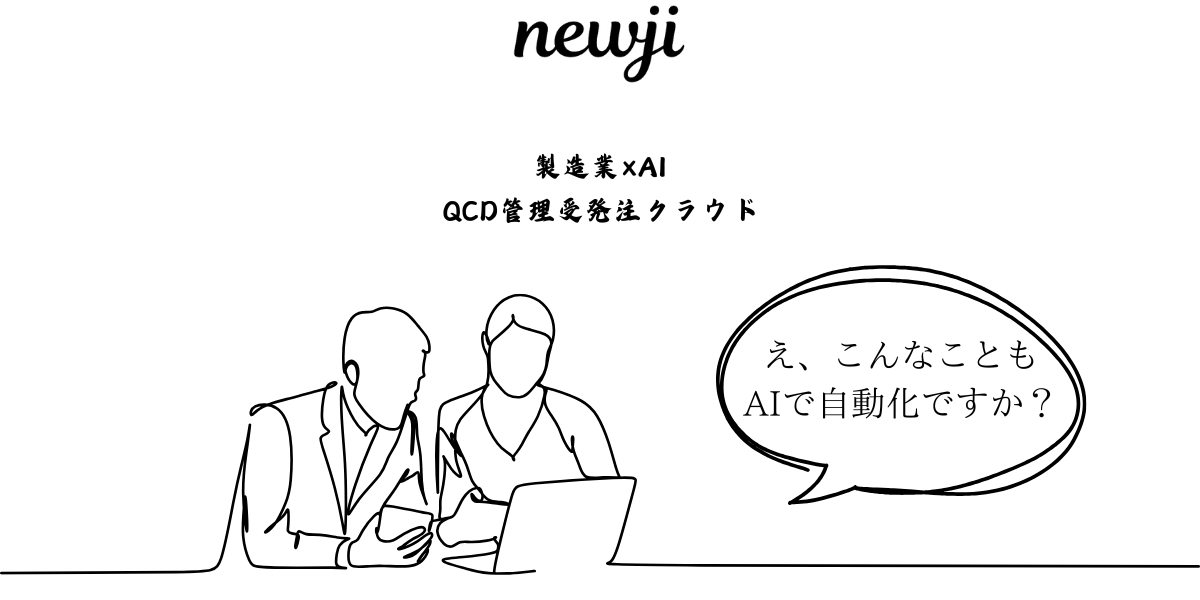
The difference between Impact Extrusion and Cold Extrusion
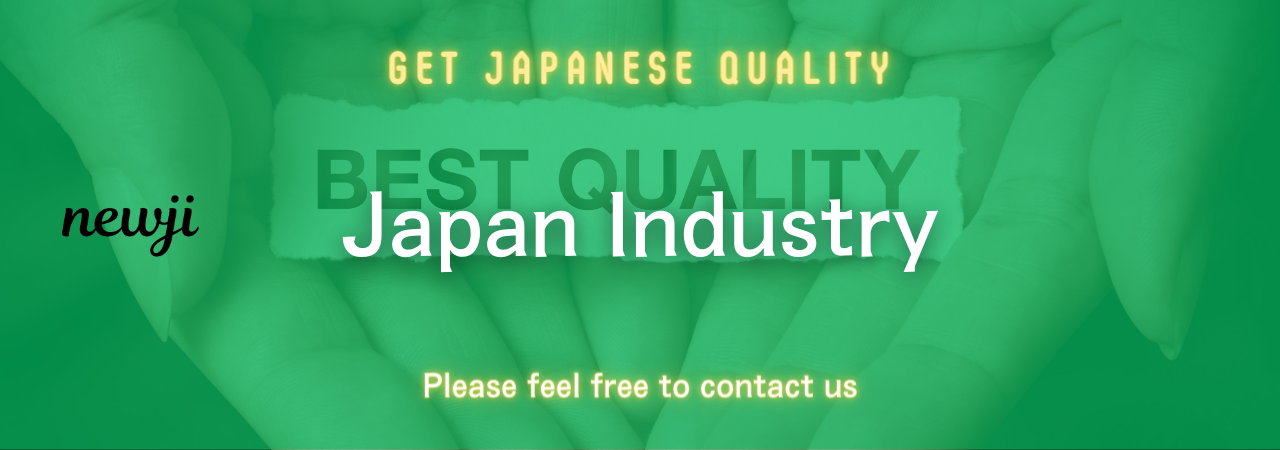
Understanding the process of creating metal parts is fascinating, particularly when comparing different methods such as impact extrusion and cold extrusion.
These methods have their unique uses, advantages, and limitations.
Knowing their differences is essential for choosing the right technique for creating high-quality products.
Let’s dive into what sets these processes apart.
目次
What is Impact Extrusion?
Impact extrusion is a manufacturing process used to shape metals, particularly soft metals like aluminum, lead, steel, and copper.
In this process, a metal slug is placed inside a die and then struck with a punch, pushing the metal to flow and fill the die cavity.
The force applied is rapid and intense, resulting in quick formation of the desired shape.
How Does Impact Extrusion Work?
Impact extrusion begins by placing a metal slug in a die cavity.
A punch then strikes the slug with significant force.
This impact causes the metal to flow plastically, filling the die cavity and forming the desired shape.
Since the entire process happens very quickly, it can produce components efficiently.
Moreover, the rapid deformation of the metal results in a smooth surface finish and low dimensional tolerances.
Advantages of Impact Extrusion
Impact extrusion offers several benefits.
First, this method allows for high production speeds, making it suitable for mass production.
The process also produces components with excellent surface finishes, reducing the need for additional finishing operations.
Furthermore, it requires relatively low material waste compared to other manufacturing processes.
Disadvantages of Impact Extrusion
Despite its advantages, impact extrusion has some limitations.
The method is generally limited to softer metals, as harder metals can cause excessive die wear and require higher impact forces.
The initial cost of the tooling can also be high, making it less suitable for small production runs.
What is Cold Extrusion?
Cold extrusion is another metal forming process, but it differs significantly from impact extrusion.
In this method, a metal slug is forced through a die at room temperature.
The force applied is continuous and steady rather than a single, high-impact force.
How Does Cold Extrusion Work?
Cold extrusion involves placing a metal slug in a die and then applying a continuous and steady force using a punch.
The metal is squeezed through the die, creating the desired shape.
Unlike impact extrusion, this process relies on the steady application of pressure rather than a single high-impact force.
The metal is typically worked at room temperature, though slight heating may be applied in some cases to reduce work hardening.
Advantages of Cold Extrusion
Cold extrusion offers several benefits.
One of the key advantages is that it improves the mechanical properties of the metal, including increased strength and hardness due to work hardening.
This method also allows for greater dimensional accuracy and finer tolerances.
Additionally, cold extrusion can be used with a wider range of metals, including both soft and hard materials.
Like impact extrusion, it produces components with good surface finishes and minimal material waste.
Disadvantages of Cold Extrusion
Despite its benefits, cold extrusion has some limitations.
The process generally requires more force compared to impact extrusion, which can lead to higher operational costs.
Tool wear can also be an issue, particularly when working with harder metals.
Additionally, cold extrusion may require lubrication to reduce friction and wear on the tools.
Key Differences Between Impact Extrusion and Cold Extrusion
Understanding the key differences between these two methods can help you choose the right process for your manufacturing needs.
Force Application
The most significant difference between impact extrusion and cold extrusion lies in how the force is applied.
In impact extrusion, a single, high-impact force is used to shape the metal rapidly.
In contrast, cold extrusion relies on a continuous and steady application of force.
Working Temperature
Impact extrusion is typically performed at elevated temperatures to aid in the plastic deformation of the metal, while cold extrusion is done at room temperature.
This difference in working temperature can affect the mechanical properties of the finished product.
Material Suitability
Impact extrusion is generally limited to soft metals like aluminum, lead, and copper due to the high-impact force used in the process.
Conversely, cold extrusion can handle a broader range of materials, including both soft and hard metals.
Production Speed and Efficiency
Impact extrusion offers higher production speeds, making it ideal for mass production.
The quick formation process also results in lower cycle times.
Cold extrusion, while not as fast, provides greater dimensional accuracy and better mechanical properties.
Tooling Costs and Wear
Impact extrusion typically involves higher initial tooling costs, and the rapid force can lead to quicker die wear, particularly with harder metals.
Cold extrusion, although potentially generating higher operational costs due to the need for continuous force, may have longer tool life depending on the materials used and the process conditions.
Conclusion
Both impact extrusion and cold extrusion are valuable processes in metal forming, each with its unique benefits and limitations.
Impact extrusion is favored for its speed and efficiency in producing components from softer metals.
In contrast, cold extrusion offers better mechanical properties, dimensional accuracy, and can be used with a broader range of metals.
Choosing between these two methods depends on the specific requirements of your project, including the type of metal, desired mechanical properties, production volume, and budget considerations.
By understanding the differences between impact extrusion and cold extrusion, manufacturers can make informed decisions to ensure high-quality, cost-effective production.
資料ダウンロード
QCD調達購買管理クラウド「newji」は、調達購買部門で必要なQCD管理全てを備えた、現場特化型兼クラウド型の今世紀最高の購買管理システムとなります。
ユーザー登録
調達購買業務の効率化だけでなく、システムを導入することで、コスト削減や製品・資材のステータス可視化のほか、属人化していた購買情報の共有化による内部不正防止や統制にも役立ちます。
NEWJI DX
製造業に特化したデジタルトランスフォーメーション(DX)の実現を目指す請負開発型のコンサルティングサービスです。AI、iPaaS、および先端の技術を駆使して、製造プロセスの効率化、業務効率化、チームワーク強化、コスト削減、品質向上を実現します。このサービスは、製造業の課題を深く理解し、それに対する最適なデジタルソリューションを提供することで、企業が持続的な成長とイノベーションを達成できるようサポートします。
オンライン講座
製造業、主に購買・調達部門にお勤めの方々に向けた情報を配信しております。
新任の方やベテランの方、管理職を対象とした幅広いコンテンツをご用意しております。
お問い合わせ
コストダウンが利益に直結する術だと理解していても、なかなか前に進めることができない状況。そんな時は、newjiのコストダウン自動化機能で大きく利益貢献しよう!
(Β版非公開)