- お役立ち記事
- The difference between Internal Quality and External Quality
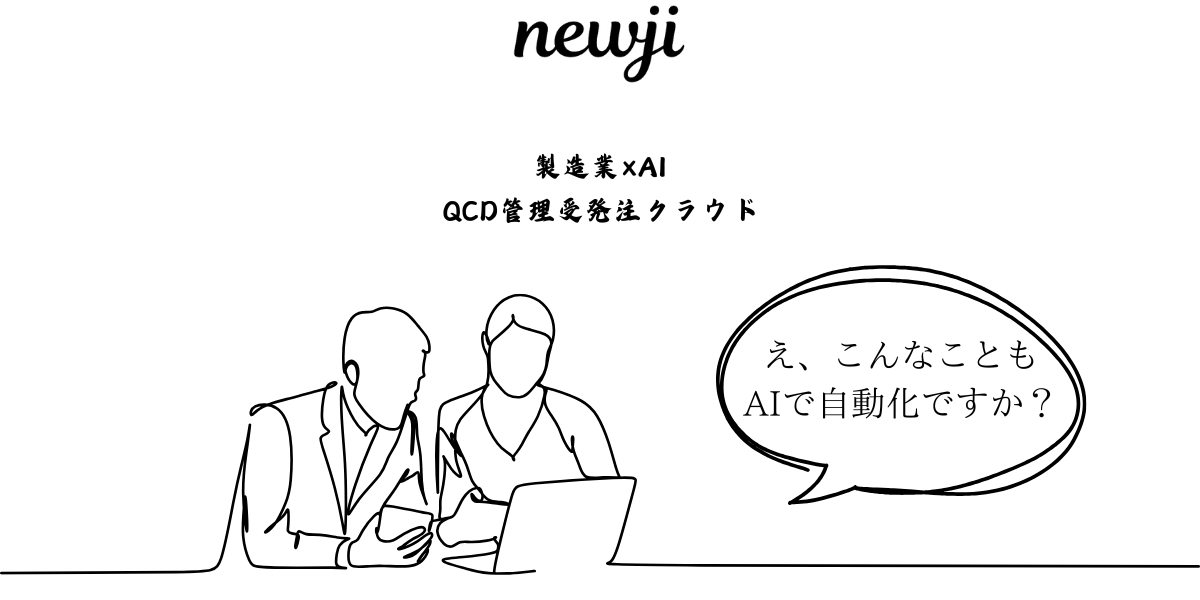
The difference between Internal Quality and External Quality
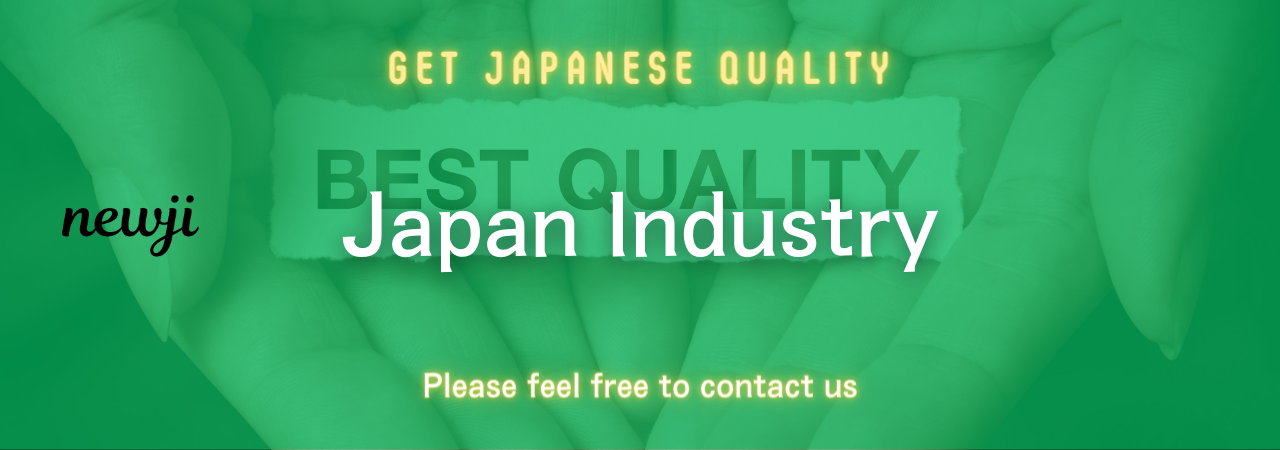
Understanding the quality of products or services is essential for businesses aiming to succeed in a competitive marketplace. Quality assessment is crucial to ensure customer satisfaction and foster long-term relationships. Two significant types of quality that companies focus on are internal quality and external quality. While these terms sound similar, they represent different aspects of a product’s or service’s overall value. Let’s dive into the differences between internal quality and external quality and why both are important for business growth.
目次
What is Internal Quality?
Internal quality refers to the measures, checks, and standards applied within the organization to ensure that a product or service meets specific criteria. These are often predefined benchmarks focused on enhancing the functionality, efficiency, and reliability of a product or service. Internal quality encompasses various aspects, including:
1. **Design Specifications**
The design phase is where internal quality begins. Proper design specifications ensure that the end product adheres to the required standards. This includes materials, dimensions, tolerances, and features that make the product viable and functional.
2. **Manufacturing Processes**
During production, internal quality checks are crucial. These checks monitor machinery performance, worker skills, and production techniques to produce a consistent and reliable outcome. Quality assurance teams play a vital role in assessing and improving these processes.
3. **Testing and Inspection**
Before a product reaches the market, it undergoes various testing and inspection stages. Internal quality involves rigorous testing to identify any defects or issues. This step helps ensure that only products meeting the set standards move forward.
Why is Internal Quality Important?
Internal quality is essential for several reasons:
1. **Cost Efficiency**
By identifying and addressing issues early in the production process, companies can reduce waste and avoid the high costs associated with product recalls and repairs.
2. **Employee Satisfaction**
High internal quality often translates into a smoother production process, which can lead to increased job satisfaction among employees. Teams can work more efficiently when the systems in place support their tasks.
3. **Reputation Management**
A company known for internal quality is perceived as reliable and trustworthy. Consistent internal quality can protect a company’s reputation in the long run.
What is External Quality?
External quality refers to how customers perceive the quality of a product or service. This encompasses all customer-facing aspects, such as usability, aesthetics, and performance. External quality is often judged based on the following factors:
1. **User Experience and Satisfaction**
External quality is heavily influenced by the user’s experience. This includes the ease of use, functionality, and satisfaction derived from the product. Positive user experience leads to higher customer satisfaction levels.
2. **Aesthetic Appeal**
For many products, how it looks can be as important as how it works. Aesthetic appeal includes design, color schemes, and packaging, all of which contribute to the perceived quality.
3. **Performance and Reliability**
Customers assess a product based on its performance and reliability. If a product performs well over time and meets their needs consistently, it is deemed to have high external quality.
Why is External Quality Important?
External quality holds a direct impact on a company’s success:
1. **Customer Loyalty**
High external quality fosters customer loyalty and repeat business. Satisfied customers are more likely to return and recommend the product to others.
2. **Brand Image**
A strong perception of quality enhances your brand image. Quality products build trust and credibility, which are crucial for brand loyalty and expansion.
3. **Market Competitiveness**
In a crowded market, external quality can be the deciding factor for consumers. Offering high-quality products that meet customer needs helps gain a competitive edge.
Key Differences Between Internal and External Quality
While both internal and external quality are essential, they differ in focus and measurement:
1. **Focus Area**
Internal quality focuses on processes within the organization, such as design, manufacturing, and testing. External quality centers on the customer’s experience, perception, and satisfaction.
2. **Measurability**
Internal quality can be measured through objective criteria, like defect rates and consistency in production. External quality is often subjective, measured through customer reviews, feedback, and overall satisfaction.
3. **Stakeholders Involved**
Internal quality involves employees, quality assurance teams, and management. External quality involves the customers, end-users, and sometimes third-party reviewers.
Balancing Internal and External Quality
Balancing both types of quality is necessary for holistic growth:
1. **Integrated Quality Management Systems (QMS)**
A robust QMS can help integrate internal and external quality standards. Regular audits and updates ensure that the products meet internal benchmarks while also satisfying customer expectations.
2. **Feedback Loops**
Regularly collecting and acting on customer feedback can help improve both internal and external quality. Understanding what customers value allows for better alignment between production processes and market needs.
3. **Employee Training**
Employees should be trained not only in technical skills but also in understanding customer needs. This can help bridge the gap between internal processes and external expectations.
Conclusion
Understanding the difference between internal quality and external quality can greatly benefit a business. Internal quality focuses on the consistency and reliability of the production processes. It ensures that the product meets predetermined standards. On the other hand, external quality emphasizes customer satisfaction, usability, and overall user experience. Balancing both types of quality through integrated systems, continuous feedback, and employee training can establish a strong foundation for success. By excelling in both internal and external quality, a business can enhance its reputation, build customer loyalty, and thrive in a competitive market.
資料ダウンロード
QCD調達購買管理クラウド「newji」は、調達購買部門で必要なQCD管理全てを備えた、現場特化型兼クラウド型の今世紀最高の購買管理システムとなります。
ユーザー登録
調達購買業務の効率化だけでなく、システムを導入することで、コスト削減や製品・資材のステータス可視化のほか、属人化していた購買情報の共有化による内部不正防止や統制にも役立ちます。
NEWJI DX
製造業に特化したデジタルトランスフォーメーション(DX)の実現を目指す請負開発型のコンサルティングサービスです。AI、iPaaS、および先端の技術を駆使して、製造プロセスの効率化、業務効率化、チームワーク強化、コスト削減、品質向上を実現します。このサービスは、製造業の課題を深く理解し、それに対する最適なデジタルソリューションを提供することで、企業が持続的な成長とイノベーションを達成できるようサポートします。
オンライン講座
製造業、主に購買・調達部門にお勤めの方々に向けた情報を配信しております。
新任の方やベテランの方、管理職を対象とした幅広いコンテンツをご用意しております。
お問い合わせ
コストダウンが利益に直結する術だと理解していても、なかなか前に進めることができない状況。そんな時は、newjiのコストダウン自動化機能で大きく利益貢献しよう!
(Β版非公開)