- お役立ち記事
- The difference between Inventory Analysis and Inventory Management
The difference between Inventory Analysis and Inventory Management
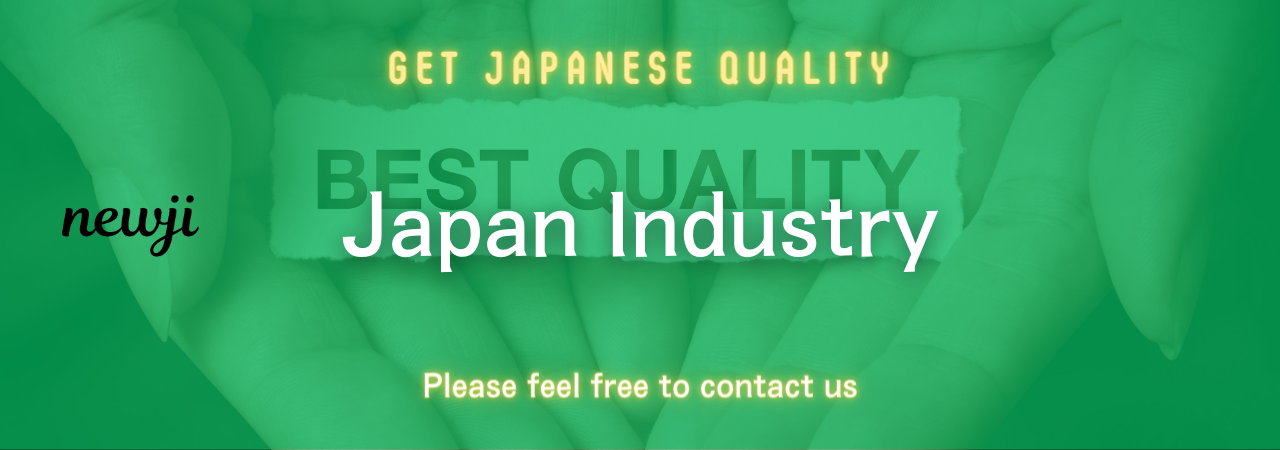
Inventory plays a crucial role in the success of any business that deals with physical products.
A well-maintained inventory ensures that the business can meet customer demands without overstocking, which can lead to higher costs.
Two key concepts in handling inventory are inventory analysis and inventory management.
Though they are closely related, they serve different purposes and involve distinct activities.
Understanding the difference between the two can help businesses operate more efficiently.
目次
What is Inventory Analysis?
Inventory analysis is the process of examining and evaluating the items in stock.
The main goal is to understand various factors related to the inventory, such as demand patterns, turnover rates, and profit margins.
This information helps businesses make informed decisions about what items to stock, how much to order, and when to reorder.
Components of Inventory Analysis
There are several components involved in inventory analysis.
The first component is demand forecasting.
This involves predicting the future demand for different products based on past sales data and market trends.
Accurate demand forecasting helps avoid stockouts and overstock situations.
Another important component is inventory turnover.
This metric measures how often inventory is sold and replaced over a specific period.
A high turnover rate indicates that products are selling quickly, while a low turnover rate may suggest overstocking or low demand.
Businesses can use this metric to identify slow-moving items and decide whether to discontinue or discount them.
The third component is cost analysis.
This involves evaluating the costs associated with holding and handling inventory, such as storage costs, insurance, and obsolescence.
By understanding these costs, businesses can identify opportunities to reduce expenses and improve profitability.
What is Inventory Management?
Inventory management, on the other hand, is the process of overseeing and controlling the ordering, storage, and use of inventory.
The main goal of inventory management is to ensure that the right products are available at the right time and in the right quantities.
This involves coordinating various activities, such as procurement, warehousing, and distribution.
Key Activities in Inventory Management
One of the key activities in inventory management is inventory control.
This involves tracking and maintaining optimal stock levels to meet customer demand without overstocking.
Various techniques, such as just-in-time (JIT) inventory and economic order quantity (EOQ), can help businesses achieve this balance.
Another important activity is order management.
This involves managing the entire process of ordering, receiving, and storing inventory.
Proper order management ensures that the business maintains a steady flow of products and avoids stockouts and delays.
Warehouse management is also a crucial part of inventory management.
It involves organizing and managing the storage of inventory in a way that maximizes efficiency and minimizes costs.
This includes optimizing warehouse layouts, implementing inventory tracking systems, and ensuring proper handling and storage of products.
Key Differences Between Inventory Analysis and Inventory Management
While inventory analysis and inventory management are closely related, they serve different purposes and involve distinct activities.
Understanding the key differences between the two can help businesses optimize their inventory processes.
Focus and Objectives
Inventory analysis focuses on examining and evaluating inventory data to gain insights and make informed decisions.
The main objectives are to understand demand patterns, turnover rates, and cost factors to optimize stock levels and improve profitability.
In contrast, inventory management focuses on overseeing and controlling the entire inventory process.
The main objectives are to ensure that the right products are available at the right time and in the right quantities to meet customer demand and minimize costs.
Activities and Techniques
Inventory analysis involves activities such as demand forecasting, inventory turnover analysis, and cost analysis.
These activities help businesses understand their inventory performance and identify opportunities for improvement.
Inventory management, on the other hand, involves activities such as inventory control, order management, and warehouse management.
These activities ensure that the business maintains optimal stock levels, manages orders efficiently, and organizes warehouse space effectively.
How They Work Together
Inventory analysis and inventory management are complementary processes that work together to optimize inventory operations.
By conducting thorough inventory analysis, businesses can gain valuable insights that inform their inventory management strategies.
For example, demand forecasting can help businesses plan their procurement and ordering processes more effectively.
On the other hand, effective inventory management ensures that the business can implement the insights gained from inventory analysis.
For instance, if inventory analysis reveals that certain products have high turnover rates, inventory management can ensure that these products are restocked promptly to meet customer demand.
Benefits of Understanding the Difference
Understanding the difference between inventory analysis and inventory management can provide several benefits for businesses.
Firstly, it allows businesses to allocate resources more effectively.
By knowing which activities are part of inventory analysis and which are part of inventory management, businesses can assign staff and resources to the appropriate tasks.
Secondly, it helps businesses identify areas for improvement.
By separating the two processes, businesses can conduct a more focused evaluation of their inventory operations and identify specific areas that need enhancement.
Finally, understanding the difference can lead to better decision-making.
When businesses have a clear understanding of their inventory data through analysis, they can make more informed decisions about their inventory management processes.
This can result in improved efficiency, reduced costs, and higher customer satisfaction.
In conclusion, while inventory analysis and inventory management are closely related, they serve different purposes and involve distinct activities.
Inventory analysis focuses on examining and evaluating inventory data to gain insights and make informed decisions.
Inventory management focuses on overseeing and controlling the entire inventory process to ensure that the right products are available at the right time and in the right quantities.
By understanding the difference between the two, businesses can optimize their inventory operations and achieve greater success.
資料ダウンロード
QCD調達購買管理クラウド「newji」は、調達購買部門で必要なQCD管理全てを備えた、現場特化型兼クラウド型の今世紀最高の購買管理システムとなります。
ユーザー登録
調達購買業務の効率化だけでなく、システムを導入することで、コスト削減や製品・資材のステータス可視化のほか、属人化していた購買情報の共有化による内部不正防止や統制にも役立ちます。
NEWJI DX
製造業に特化したデジタルトランスフォーメーション(DX)の実現を目指す請負開発型のコンサルティングサービスです。AI、iPaaS、および先端の技術を駆使して、製造プロセスの効率化、業務効率化、チームワーク強化、コスト削減、品質向上を実現します。このサービスは、製造業の課題を深く理解し、それに対する最適なデジタルソリューションを提供することで、企業が持続的な成長とイノベーションを達成できるようサポートします。
オンライン講座
製造業、主に購買・調達部門にお勤めの方々に向けた情報を配信しております。
新任の方やベテランの方、管理職を対象とした幅広いコンテンツをご用意しております。
お問い合わせ
コストダウンが利益に直結する術だと理解していても、なかなか前に進めることができない状況。そんな時は、newjiのコストダウン自動化機能で大きく利益貢献しよう!
(Β版非公開)