- お役立ち記事
- The difference between Inventory Costs and Storage Costs
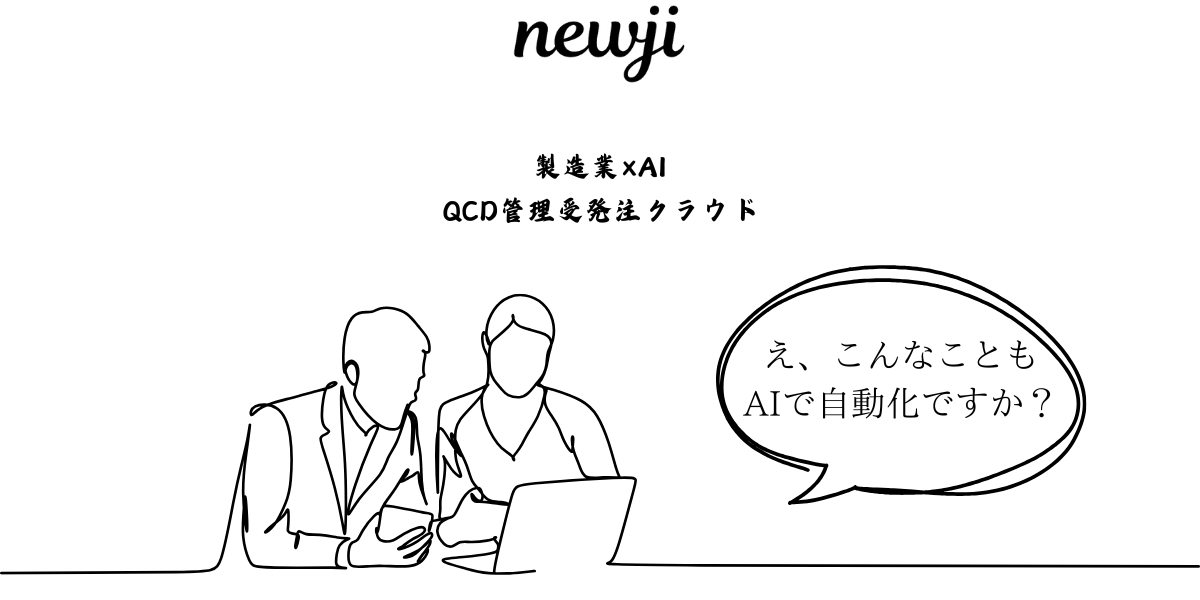
The difference between Inventory Costs and Storage Costs
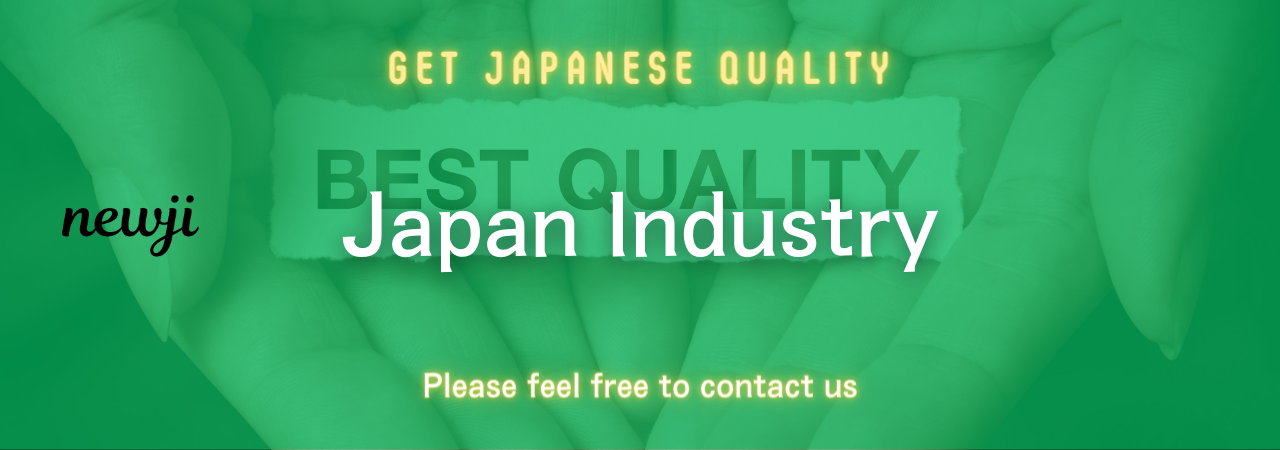
When running a business, managing expenses is crucial for profitability. Among these expenses, inventory costs and storage costs are often discussed. Understanding the difference between these two can help you manage your finances better. Let’s break down what each of these terms means and how they affect your business.
目次
What Are Inventory Costs?
Inventory costs are the costs associated with obtaining and holding the goods that your business sells. They include several types of expenses:
Purchasing Costs
Purchasing costs are the expenses you incur when buying products from suppliers. These costs can vary depending on the quantity purchased and the supplier’s pricing.
Carrying Costs
Carrying costs are the expenses related to holding inventory over a period of time. These include costs like insurance, taxes, and warehousing. The longer you hold inventory, the higher these costs will be.
Order Costs
Order costs are the expenses incurred every time you place an order for new inventory. These include administrative expenses like paperwork and processing fees.
Shortage Costs
Shortage costs occur when you run out of inventory. Running out of stock can lead to lost sales and dissatisfied customers. These costs represent the lost opportunity and potential damage to your reputation.
What Are Storage Costs?
Storage costs are a subset of inventory costs specifically related to storing your products. Let’s take a look at the different aspects of storage costs:
Warehouse Rent or Lease
This is the cost of renting or leasing a space where you store your inventory. The size and location of the warehouse will greatly affect this cost.
Utilities and Maintenance
Utilities such as electricity, water, and heating are required to maintain the warehouse and ensure proper storage conditions. Additionally, maintenance costs are needed to keep the storage facility in good condition.
Labor Costs
These include wages paid to employees responsible for organizing, handling, and managing the inventory within the storage facility. Efficient labor management can help reduce these costs.
Security
Security costs include measures taken to protect the stored goods from theft or damage. This can involve surveillance systems, security personnel, and insurance.
The Relationship Between Inventory Costs and Storage Costs
Understanding the relationship between inventory and storage costs is essential for effective cost management. Storage costs are a component of overall inventory costs, but each has distinct elements. Properly managing both can help optimize your business operations.
Balancing Inventory Levels
Maintaining an appropriate inventory level is crucial. Overstocking can lead to high carrying and storage costs while understocking can lead to shortage costs. Finding the right balance can minimize these expenses.
Efficient Use of Space
Using storage space efficiently can help reduce storage costs. Implementing organizational systems and warehouse management software can maximize space utilization, reducing the need for additional storage.
Reducing Inventory and Storage Costs
Reducing these costs can significantly improve your bottom line. Here are some strategies to consider:
Just-In-Time Inventory
The Just-In-Time (JIT) inventory system is a strategy where materials and products are ordered only when needed. This approach can minimize carrying and storage costs by reducing the amount of inventory held.
Vendor Managed Inventory (VMI)
VMI is a practice where the supplier is responsible for managing the inventory levels. This can help reduce order and carrying costs as the supplier ensures the supply meets the demand.
Inventory Turnover Improvement
Increasing your inventory turnover ratio means that you sell and replace inventory more frequently. Higher turnover can reduce carrying costs by shortening the time products spend in storage.
Warehouse Automation
Implementing automated systems in your warehouse can reduce labor costs and improve efficiency. Automated storage and retrieval systems (AS/RS) can streamline operations and reduce the need for manual labor.
Leasing vs. Owning Storage Facilities
Choosing between leasing and owning your storage facility can impact your storage costs. Leasing offers flexibility and may be less expensive in the short term. Owning may offer long-term savings, but requires significant upfront investment.
Conclusion
In summary, inventory costs and storage costs are distinct but interrelated expenses that businesses must manage. Understanding the difference between the two can help you develop strategies to minimize these costs, ultimately improving your company’s profitability.
By balancing inventory levels, using storage space efficiently, and implementing cost-reducing strategies, you can effectively manage both inventory and storage costs. This will not only save money, but also ensure smoother business operations.
Careful cost management is a key factor in the success of any business. By focusing on inventory and storage costs, you can streamline your operations and maintain a healthy bottom line.
資料ダウンロード
QCD調達購買管理クラウド「newji」は、調達購買部門で必要なQCD管理全てを備えた、現場特化型兼クラウド型の今世紀最高の購買管理システムとなります。
ユーザー登録
調達購買業務の効率化だけでなく、システムを導入することで、コスト削減や製品・資材のステータス可視化のほか、属人化していた購買情報の共有化による内部不正防止や統制にも役立ちます。
NEWJI DX
製造業に特化したデジタルトランスフォーメーション(DX)の実現を目指す請負開発型のコンサルティングサービスです。AI、iPaaS、および先端の技術を駆使して、製造プロセスの効率化、業務効率化、チームワーク強化、コスト削減、品質向上を実現します。このサービスは、製造業の課題を深く理解し、それに対する最適なデジタルソリューションを提供することで、企業が持続的な成長とイノベーションを達成できるようサポートします。
オンライン講座
製造業、主に購買・調達部門にお勤めの方々に向けた情報を配信しております。
新任の方やベテランの方、管理職を対象とした幅広いコンテンツをご用意しております。
お問い合わせ
コストダウンが利益に直結する術だと理解していても、なかなか前に進めることができない状況。そんな時は、newjiのコストダウン自動化機能で大きく利益貢献しよう!
(Β版非公開)