- お役立ち記事
- The difference between Inventory Management and Logistics Management
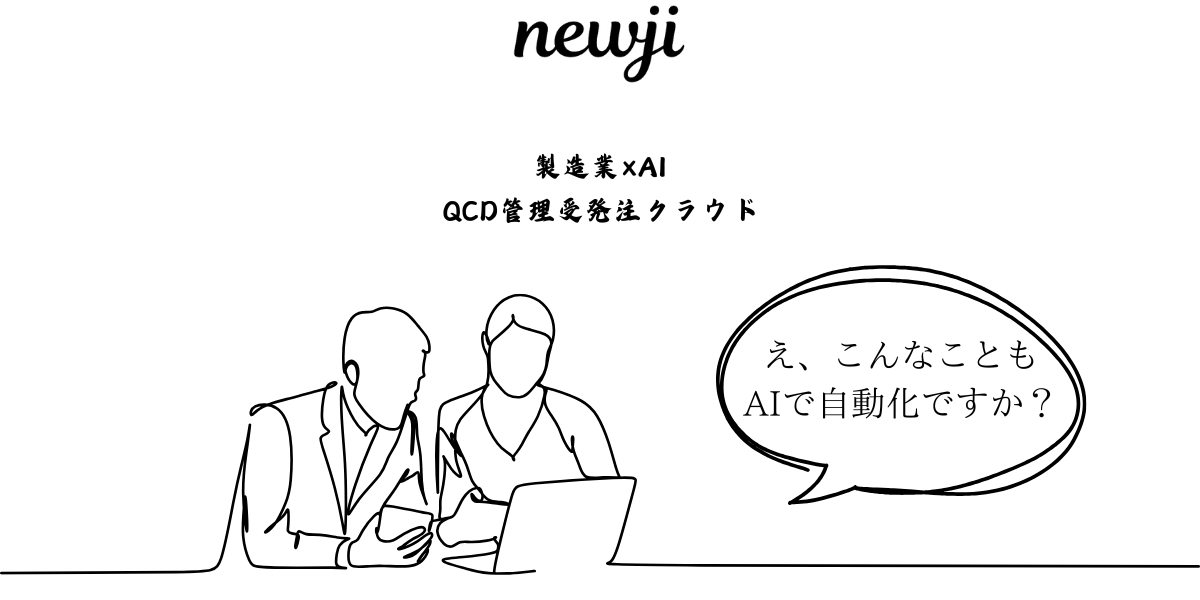
The difference between Inventory Management and Logistics Management
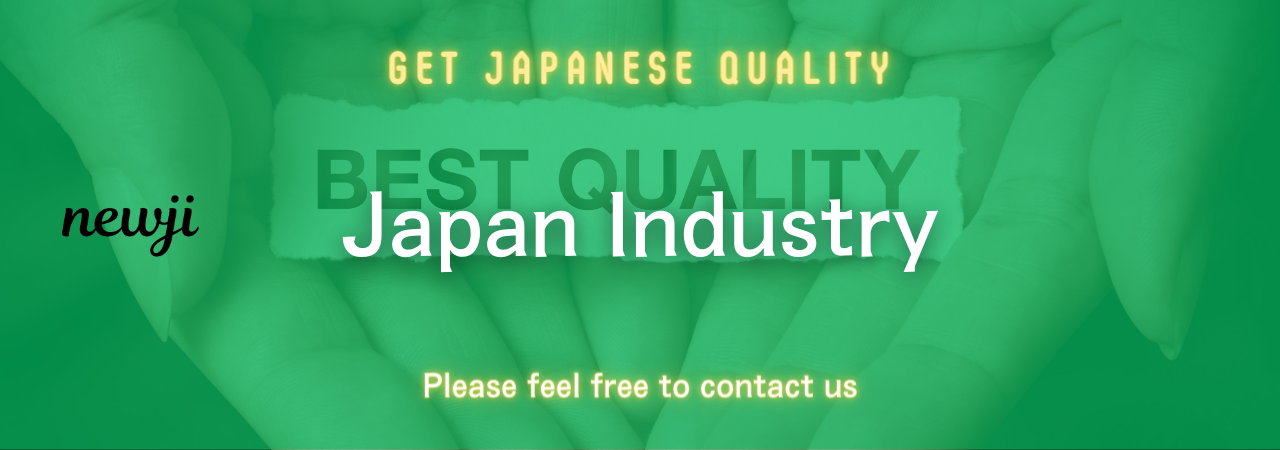
Managing a business comes with many important tasks, and understanding how to control and oversee various processes can make or break the success of your company.
Two critical aspects to focus on are inventory management and logistics management.
These two components play distinct roles in the supply chain but are often confused.
In this article, we’ll clarify the differences between inventory management and logistics management to help you streamline operations and improve your business efficiency.
目次
What is Inventory Management?
Inventory management refers to the process of ordering, storing, and using a company’s inventory.
This includes the management of raw materials, components, and finished products, as well as warehousing and processing these items.
Components of Inventory Management
Good inventory management involves several key components:
Stock Monitoring
Keeping track of items in stock is perhaps the most crucial task.
This involves regularly checking quantities, ensuring that the items are not expired, damaged, or obsolete, and maintaining accurate records of stock levels.
Ordering and Reordering
Deciding when and how much stock to reorder is another critical aspect of inventory management.
The goal is to maintain enough stock to meet customer demand while minimizing excess inventory that ties up capital.
Storage Solutions
Proper storage solutions are vital to maintaining the quality of inventory.
This includes everything from how items are stored in the warehouse to the systems used for tracking and retrieving stock efficiently.
Predictive Analytics
Modern inventory management often involves predictive analytics to forecast future demand based on historical data, market trends, and seasonal variations.
This helps in making informed decisions about stock levels.
What is Logistics Management?
Logistics management, on the other hand, involves planning, implementing, and controlling the efficient, effective flow and storage of goods, services, and related information from the point of origin to the point of consumption.
Components of Logistics Management
Effective logistics management encompasses several essential activities:
Transportation
One of the primary tasks of logistics management is ensuring that goods are transported efficiently.
This could involve various modes of transport—such as trucks, ships, and airplanes—depending on the nature of the goods and the destination.
Delivery Scheduling
Proper scheduling is crucial to ensure that deliveries are made on time.
This involves planning routes, managing delivery times, and optimizing delivery processes through various logistical software and tools.
Warehouse Operations
In logistics management, warehouse operations go beyond storage.
It includes the receipt, storage, and dispatch of goods.
A well-managed warehouse keeps an accurate record of inventory levels, manages space efficiently, and ensures the safe storage of goods.
Supply Chain Integration
Logistics management also involves integrating all components of the supply chain—from suppliers to manufacturers to end consumers.
Effective integration results in a seamless flow of goods and information, reducing delays and improving overall efficiency.
Key Differences Between Inventory Management and Logistics Management
While both inventory management and logistics management are crucial to the supply chain, they have distinct roles and responsibilities.
Understanding these differences can help businesses optimize their operations.
Scope of Work
Inventory management focuses specifically on the storage, tracking, and replenishment of stock within a company.
Logistics management has a broader scope that includes the transportation of goods, managing deliveries, and integrating various aspects of the supply chain.
Objectives
The primary objective of inventory management is to ensure that the right amount of stock is available to meet customer demand without overstocking.
Logistics management aims to deliver goods in the most efficient and cost-effective manner from the supplier to the end customer.
Responsibilities
In inventory management, responsibilities include ordering stock, monitoring inventory levels, and ensuring proper storage.
Logistics management involves planning and coordinating the transportation and delivery of goods, managing warehouses, and streamlining the entire supply chain.
Outcome Measurements
Success in inventory management is typically measured by metrics like inventory turnover rates, stockout rates, and holding costs.
In logistics management, performance is often measured by delivery times, transportation costs, and customer satisfaction.
Complementary Roles
While distinct, inventory management and logistics management often overlap and work together to achieve overall supply chain efficiency.
For instance, accurate inventory management can help optimize logistics by ensuring that stock is readily available for transportation, reducing delays.
Similarly, efficient logistics management ensures that goods are delivered on time, which in turn supports inventory management by keeping stock levels balanced.
Technology and Tools
Today’s technology plays a significant role in optimizing both inventory and logistics management.
Various software solutions and tools are available to help businesses automate and streamline these processes.
For inventory management, tools may include barcode scanners, inventory management software, and predictive analytics tools.
In logistics management, GPS tracking, route planning software, and transportation management systems (TMS) are commonly used to optimize operations.
Coordination Between Departments
Effective coordination between the inventory management and logistics management departments is essential for the smooth running of the supply chain.
Regular communication and collaboration can help identify issues early, streamline processes, and ensure that both departments work towards shared goals.
Conclusion
Understanding the differences between inventory management and logistics management is crucial for any business involved in the production, storage, and transportation of goods.
While inventory management focuses on maintaining optimal stock levels within the warehouse, logistics management ensures the efficient movement and delivery of goods.
By distinguishing between these two roles and ensuring effective coordination, businesses can achieve greater efficiency, reduce costs, and improve customer satisfaction.
Whether you are a small business owner or part of a large supply chain operation, effective management of both inventory and logistics can significantly impact your bottom line.
So, invest in the right tools, foster collaboration between teams, and stay informed about best practices to keep your supply chain running smoothly.
資料ダウンロード
QCD調達購買管理クラウド「newji」は、調達購買部門で必要なQCD管理全てを備えた、現場特化型兼クラウド型の今世紀最高の購買管理システムとなります。
ユーザー登録
調達購買業務の効率化だけでなく、システムを導入することで、コスト削減や製品・資材のステータス可視化のほか、属人化していた購買情報の共有化による内部不正防止や統制にも役立ちます。
NEWJI DX
製造業に特化したデジタルトランスフォーメーション(DX)の実現を目指す請負開発型のコンサルティングサービスです。AI、iPaaS、および先端の技術を駆使して、製造プロセスの効率化、業務効率化、チームワーク強化、コスト削減、品質向上を実現します。このサービスは、製造業の課題を深く理解し、それに対する最適なデジタルソリューションを提供することで、企業が持続的な成長とイノベーションを達成できるようサポートします。
オンライン講座
製造業、主に購買・調達部門にお勤めの方々に向けた情報を配信しております。
新任の方やベテランの方、管理職を対象とした幅広いコンテンツをご用意しております。
お問い合わせ
コストダウンが利益に直結する術だと理解していても、なかなか前に進めることができない状況。そんな時は、newjiのコストダウン自動化機能で大きく利益貢献しよう!
(Β版非公開)