- お役立ち記事
- The difference between Just-in-time and Kanban System
月間76,176名の
製造業ご担当者様が閲覧しています*
*2025年3月31日現在のGoogle Analyticsのデータより
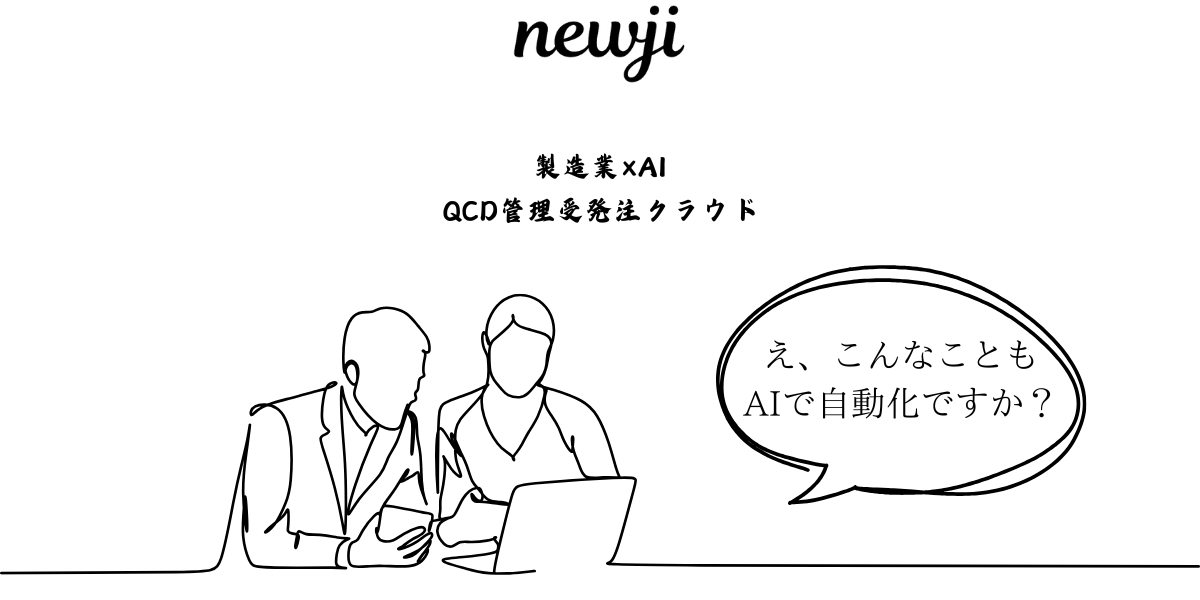
The difference between Just-in-time and Kanban System
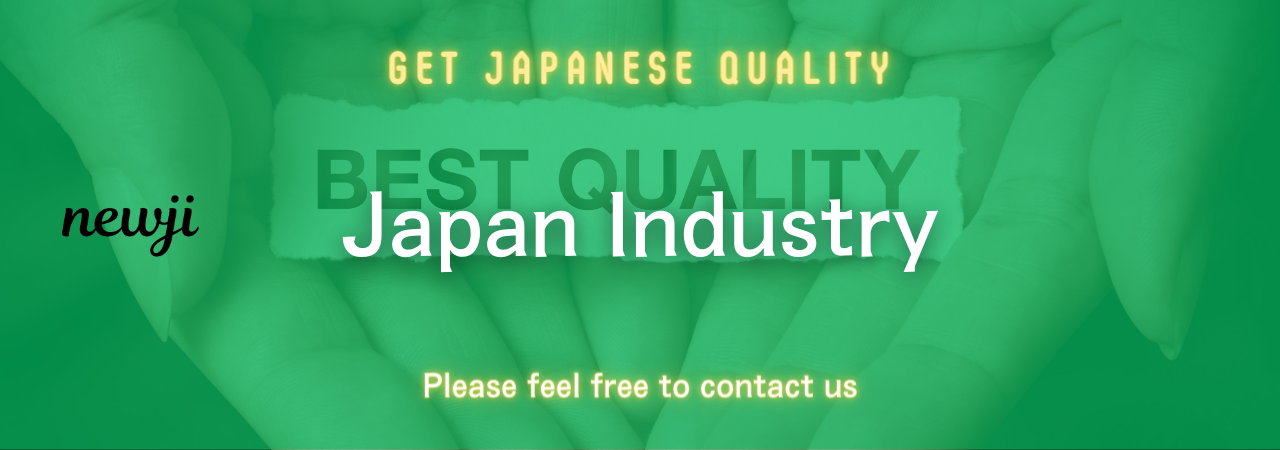
Just-in-time (JIT) and Kanban are two important methodologies used in manufacturing and inventory management.
Both aim to enhance efficiency and reduce waste, but they approach these goals in different ways.
Understanding the differences between the Just-in-time system and the Kanban system can help businesses choose the right strategy for their operations.
目次
What is Just-in-time (JIT)?
Just-in-time is a production strategy where materials and products are produced or acquired only as they are needed for immediate use.
This method minimizes inventory costs and reduces waste.
The concept was popularized by Toyota in the 1970s and has since been widely adopted in various industries.
How JIT Works
In a JIT system, a company keeps minimal inventory.
When an order is received, the production process begins.
Suppliers deliver materials only when required, and production is tightly scheduled to meet demand without surplus.
This requires precise forecasting and a reliable supply chain to ensure materials arrive on time.
Benefits of JIT
1. **Reduced Inventory Costs:** By holding less inventory, companies save on storage and handling costs.
2. **Less Waste:** Producing only what is needed reduces the risk of overproduction and obsolescence.
3. **Improved Cash Flow:** With fewer funds tied up in inventory, companies have more cash available for other operations.
4. **Increased Efficiency:** Streamlined production processes lead to faster turnaround times and better responsiveness to market changes.
What is Kanban?
Kanban is a scheduling system that helps manage workflow and inventory.
Originating in the Toyota Production System, Kanban uses visual signals, such as cards or electronic boards, to control production and inventory levels.
It aims to create a balanced and efficient production process by controlling the flow of work.
How Kanban Works
In a Kanban system, work is divided into small, manageable tasks.
These tasks are represented by Kanban cards, which move through various stages of the production process.
Each stage has a defined capacity, preventing work from piling up and ensuring a smooth production flow.
Kanban boards, either physical or digital, are used to visualize work-in-progress and identify bottlenecks.
Benefits of Kanban
1. **Improved Visibility:** Kanban boards provide a clear view of the production process, making it easier to track progress and identify issues.
2. **Flexibility:** Kanban systems are adaptable and can accommodate changes in demand or production requirements quickly.
3. **Enhanced Collaboration:** Teams can see what others are working on, fostering better communication and coordination.
4. **Continuous Improvement:** By regularly reviewing the workflow, teams can identify areas for improvement and implement changes.
Key Differences Between Just-in-time and Kanban
While both JIT and Kanban aim to streamline production and reduce waste, they differ in their approach and implementation.
Inventory Management
JIT focuses on minimizing inventory by producing goods only when needed.
This approach reduces storage costs and minimizes waste.
Kanban, on the other hand, uses visual signals to manage inventory levels.
It doesn’t necessarily eliminate inventory but ensures that materials are available when needed, preventing stockouts and overproduction.
Production Scheduling
In a JIT system, production is tightly scheduled based on demand forecasts.
This requires accurate forecasting and a reliable supply chain.
Kanban uses a pull system, where production is driven by actual demand rather than forecasts.
Work is triggered by Kanban signals, ensuring that production aligns with real-time needs.
Implementation Complexity
JIT systems can be complex to implement, requiring significant changes to production processes, supply chain management, and forecasting methods.
Companies need to work closely with suppliers to ensure timely delivery of materials.
Kanban is generally easier to implement and can be integrated into existing workflows with minimal disruption.
It relies on visual management tools to control production and inventory.
Choosing the Right System for Your Business
The choice between Just-in-time and Kanban depends on various factors, including the nature of your business, production processes, and market conditions.
When to Use Just-in-time
JIT is ideal for businesses with predictable demand and reliable supply chains.
If you can accurately forecast demand and ensure timely delivery of materials, JIT can help minimize inventory costs and reduce waste.
Industries like automotive manufacturing, where precision and efficiency are critical, often benefit from JIT systems.
When to Use Kanban
Kanban is suitable for businesses with variable demand and production processes.
If your workflow involves multiple stages or teams, Kanban can help manage tasks and improve collaboration.
Industries such as software development, where projects are dynamic and require flexibility, often find Kanban beneficial.
It allows for quick adjustments and continuous improvement.
Combining Just-in-time and Kanban
Many businesses use a combination of JIT and Kanban to optimize their operations.
JIT can be used to manage the overall production strategy, while Kanban can control the flow of work within the production process.
By integrating both systems, companies can achieve greater efficiency and responsiveness to market demands.
Implementing JIT and Kanban
1. **Assessment:** Evaluate your current production processes and identify areas for improvement.
Determine which system aligns best with your business goals and operational needs.
2. **Planning:** Develop a detailed implementation plan, including timelines, resources, and key performance indicators.
3. **Training:** Train your team on the principles and practices of the chosen system.
Ensure everyone understands their roles and responsibilities.
4. **Integration:** Gradually integrate the new system into your existing workflow.
Monitor progress and make adjustments as needed.
5. **Review:** Regularly review the system’s performance and identify opportunities for continuous improvement.
By understanding the differences between Just-in-time and Kanban, businesses can make informed decisions and choose the right strategy for their operations.
Both systems offer unique benefits and, when implemented effectively, can lead to significant improvements in efficiency, productivity, and overall success.
資料ダウンロード
QCD管理受発注クラウド「newji」は、受発注部門で必要なQCD管理全てを備えた、現場特化型兼クラウド型の今世紀最高の受発注管理システムとなります。
ユーザー登録
受発注業務の効率化だけでなく、システムを導入することで、コスト削減や製品・資材のステータス可視化のほか、属人化していた受発注情報の共有化による内部不正防止や統制にも役立ちます。
NEWJI DX
製造業に特化したデジタルトランスフォーメーション(DX)の実現を目指す請負開発型のコンサルティングサービスです。AI、iPaaS、および先端の技術を駆使して、製造プロセスの効率化、業務効率化、チームワーク強化、コスト削減、品質向上を実現します。このサービスは、製造業の課題を深く理解し、それに対する最適なデジタルソリューションを提供することで、企業が持続的な成長とイノベーションを達成できるようサポートします。
製造業ニュース解説
製造業、主に購買・調達部門にお勤めの方々に向けた情報を配信しております。
新任の方やベテランの方、管理職を対象とした幅広いコンテンツをご用意しております。
お問い合わせ
コストダウンが利益に直結する術だと理解していても、なかなか前に進めることができない状況。そんな時は、newjiのコストダウン自動化機能で大きく利益貢献しよう!
(β版非公開)