- お役立ち記事
- The difference between Kaizen Activities and Lean Activities
月間76,176名の
製造業ご担当者様が閲覧しています*
*2025年3月31日現在のGoogle Analyticsのデータより
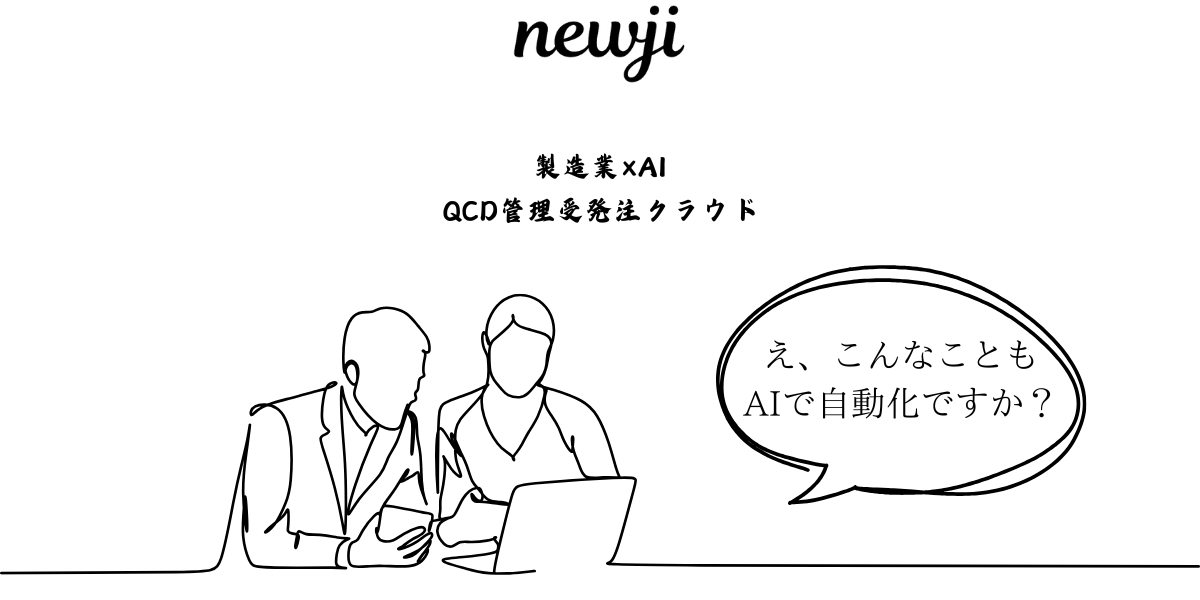
The difference between Kaizen Activities and Lean Activities
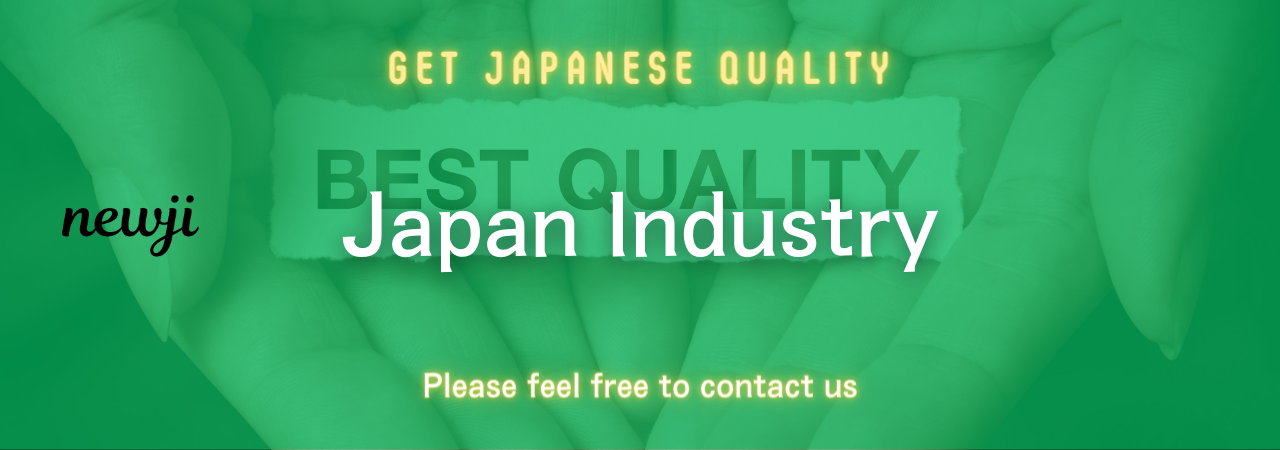
In today’s competitive business world, companies are constantly seeking ways to improve and streamline their operations.
Two popular methodologies that help in achieving this are Kaizen and Lean activities.
While both approaches aim to enhance efficiency and eliminate waste, they differ in their philosophies and methods.
Understanding these differences can help businesses choose the right strategy for their specific needs.
目次
What is Kaizen?
Kaizen is a Japanese term that means “continuous improvement.”
It is a philosophy that encourages employees at all levels of an organization to work together proactively to achieve regular, incremental improvements in the manufacturing process.
Kaizen activities focus on small, ongoing changes rather than major, revolutionary transformations.
The Origins of Kaizen
Kaizen was popularized by Japanese companies after World War II, particularly by Toyota.
The approach was inspired by American productivity experts who introduced statistical control methods to Japan.
Over time, Kaizen evolved into a unique methodology that emphasizes employee involvement and collective problem-solving.
Principles of Kaizen
1. **Continuous Improvement:** Kaizen believes that small, consistent changes can lead to significant improvements over time.
2. **Employee Involvement:** Everyone in the company, from upper management to frontline workers, is encouraged to participate in improvement activities.
3. **Process-Oriented:** Kaizen focuses on improving processes rather than blaming individuals for problems.
4. **Standardization:** Once an improvement is made, it becomes the new standard to ensure consistency.
What is Lean?
Lean activities aim to create value for the customer by eliminating waste.
The methodology was developed from the Toyota Production System (TPS) and has evolved into a comprehensive approach for improving organizational efficiency.
Lean focuses on maximizing customer value while minimizing resources used.
The Origins of Lean
Lean manufacturing has its roots in the TPS, which was developed by Toyota in the mid-20th century.
The system was designed to improve quality, reduce costs, and enhance flexibility in the production process.
Over time, Lean principles have been adapted for use in various industries beyond manufacturing, including healthcare, software development, and service industries.
Principles of Lean
1. **Value:** Identify what the customer perceives as value and focus on creating it.
2. **Value Stream:** Map out the entire process of product creation to identify and eliminate waste.
3. **Flow:** Ensure that the production process flows smoothly without interruptions.
4. **Pull:** Produce only what is needed when it is needed to reduce excess inventory.
5. **Perfection:** Continually strive for perfection by making incremental improvements.
Key Differences Between Kaizen and Lean
While both Kaizen and Lean aim to improve efficiency and reduce waste, they differ in several key aspects.
Scope of Improvement
Kaizen focuses on small, incremental improvements that are made continuously over time.
These changes are often driven by employees at all levels and are relatively easy to implement.
In contrast, Lean focuses on more significant, systemic changes that aim to optimize the entire value stream.
Lean initiatives often require a more top-down approach and involve extensive planning and resources.
Employee Involvement
Kaizen heavily emphasizes employee involvement and empowerment.
It encourages everyone in the organization to contribute ideas for improvement, fostering a culture of collaboration and teamwork.
Lean also values employee input but tends to have a more structured approach, with specific roles and responsibilities assigned to different team members.
Focus Areas
Kaizen is more process-oriented, focusing on improving specific tasks or workflows within the organization.
It aims to standardize these improvements to ensure long-term consistency.
Lean, on the other hand, takes a broader view by looking at the entire value stream.
It seeks to eliminate waste at all stages of the production process, from raw materials to the finished product.
Implementation Speed
Kaizen activities are generally easier and quicker to implement because they involve small, incremental changes.
These activities can be rolled out without significant disruption to ongoing operations.
Lean initiatives, however, often require substantial time and resources to plan and execute, particularly if they involve major process re-engineering or technology upgrades.
Benefits of Kaizen and Lean
Both Kaizen and Lean offer numerous benefits that can help organizations become more efficient and competitive.
Benefits of Kaizen
1. **Improved Productivity:** Regular, small improvements can lead to significant gains in productivity over time.
2. **Employee Engagement:** Involvement in Kaizen activities boosts employee morale and encourages a sense of ownership and accountability.
3. **Higher Quality:** Continuous improvement activities can help identify and eliminate defects, leading to higher-quality products and services.
4. **Cost Savings:** Reducing waste and improving efficiency can result in significant cost savings.
Benefits of Lean
1. **Enhanced Customer Value:** By focusing on what the customer values, Lean helps organizations deliver better products and services.
2. **Reduced Waste:** Lean methodologies aim to eliminate waste in all forms, including excess inventory, unnecessary steps, and idle time.
3. **Increased Flexibility:** Lean practices improve the ability to respond quickly to changes in customer demand or market conditions.
4. **Cost Reduction:** Efficient processes and waste elimination can lead to lower operating costs and higher profitability.
Which Approach is Right for Your Organization?
Choosing between Kaizen and Lean depends on your organization’s goals, resources, and existing processes.
If you are looking for a method that encourages widespread employee involvement and focuses on small, continuous improvements, Kaizen may be the right choice.
It is particularly effective for organizations that want to foster a collaborative culture and achieve incremental gains over time.
If your organization seeks to make more significant, systemic changes aimed at optimizing the entire value stream, Lean may be a better fit.
Lean requires more planning and resources but can result in substantial improvements in efficiency and customer value.
In many cases, organizations find that a combination of both approaches works best.
By integrating the continuous improvement philosophy of Kaizen with the waste-elimination focus of Lean, businesses can achieve sustainable long-term success.
Understanding the differences between Kaizen and Lean activities can help you make informed decisions about which methodologies to implement.
Both approaches offer valuable tools for improving efficiency, reducing waste, and enhancing customer satisfaction.
By leveraging the strengths of each method, your organization can create a culture of continuous improvement and achieve its strategic goals.
資料ダウンロード
QCD管理受発注クラウド「newji」は、受発注部門で必要なQCD管理全てを備えた、現場特化型兼クラウド型の今世紀最高の受発注管理システムとなります。
ユーザー登録
受発注業務の効率化だけでなく、システムを導入することで、コスト削減や製品・資材のステータス可視化のほか、属人化していた受発注情報の共有化による内部不正防止や統制にも役立ちます。
NEWJI DX
製造業に特化したデジタルトランスフォーメーション(DX)の実現を目指す請負開発型のコンサルティングサービスです。AI、iPaaS、および先端の技術を駆使して、製造プロセスの効率化、業務効率化、チームワーク強化、コスト削減、品質向上を実現します。このサービスは、製造業の課題を深く理解し、それに対する最適なデジタルソリューションを提供することで、企業が持続的な成長とイノベーションを達成できるようサポートします。
製造業ニュース解説
製造業、主に購買・調達部門にお勤めの方々に向けた情報を配信しております。
新任の方やベテランの方、管理職を対象とした幅広いコンテンツをご用意しております。
お問い合わせ
コストダウンが利益に直結する術だと理解していても、なかなか前に進めることができない状況。そんな時は、newjiのコストダウン自動化機能で大きく利益貢献しよう!
(β版非公開)