- お役立ち記事
- The difference between Kanban and Picking List
月間76,176名の
製造業ご担当者様が閲覧しています*
*2025年3月31日現在のGoogle Analyticsのデータより
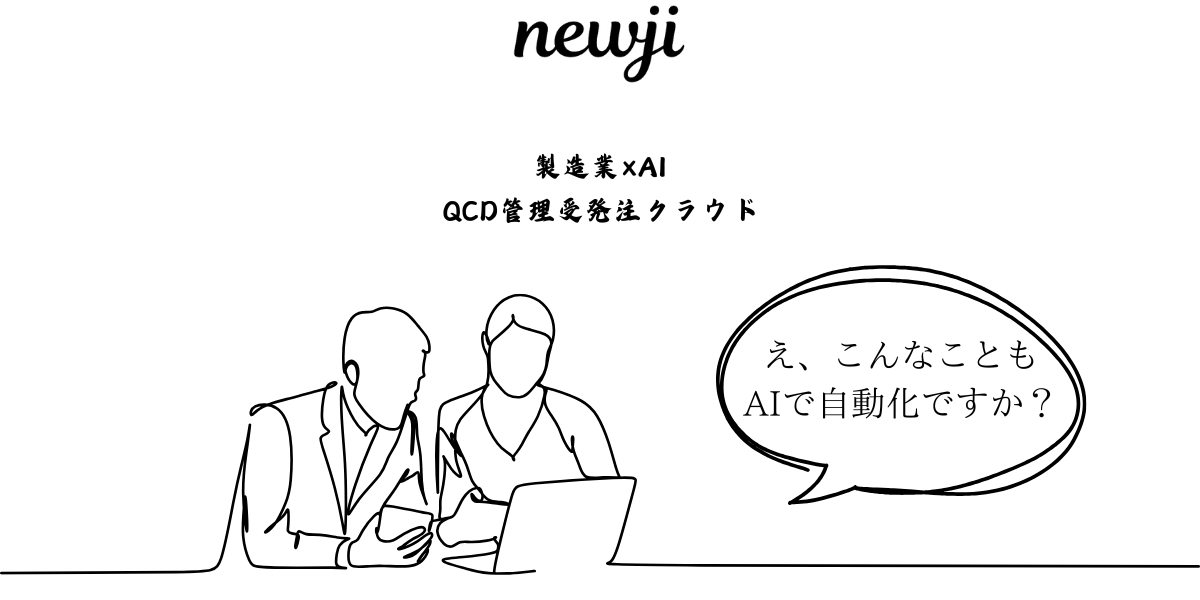
The difference between Kanban and Picking List
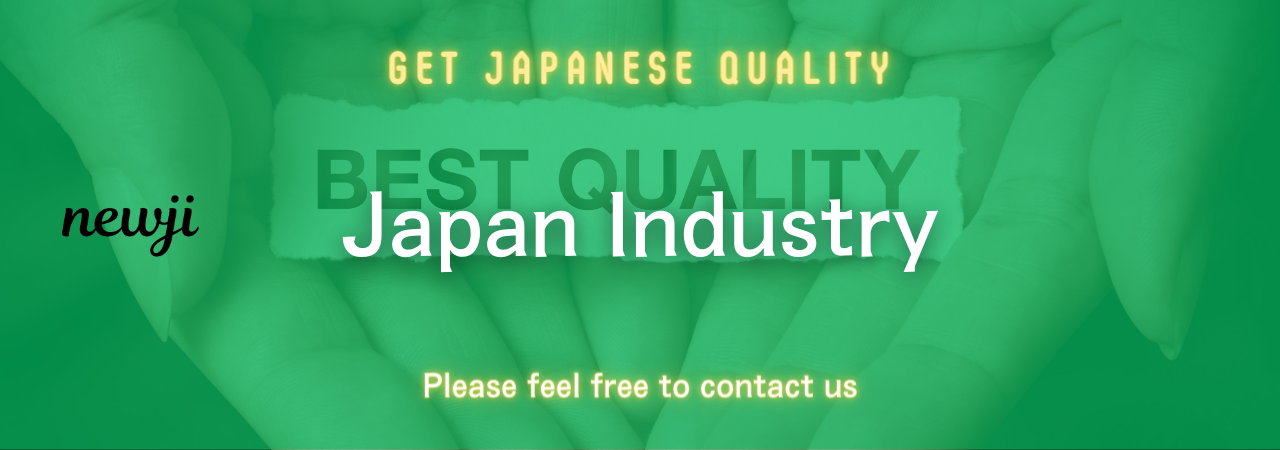
In the world of logistics and inventory management, ensuring efficient operations is critical. Two popular methods that organizations use to streamline their processes are Kanban and Picking Lists. These systems, while both important, serve distinct purposes and are used in different contexts. Understanding the difference between Kanban and Picking Lists can help businesses choose the right strategy for their needs and improve overall efficiency.
目次
What is Kanban?
Kanban is a system designed to manage workflow and inventory efficiently. Originating from Japan, the term “Kanban” means “visual signal” or “card.” It’s a method that uses visual cues to trigger actions in a production process. The primary goal of Kanban is to minimize waste by producing only what is needed, when it is needed, and in the amount needed.
How Kanban Works
Kanban operates on a just-in-time (JIT) production philosophy. This means that items are produced only when there is a demand for them. The system uses cards or visual indicators attached to inventory bins. When a bin is emptied, the Kanban card is moved to signal that more items need to be produced or ordered. This triggers the next step in the production process without the need for complex scheduling systems or detailed inventory tracking.
Benefits of Kanban
Kanban offers several advantages, including:
• Reduced inventory levels: By producing only what is needed, companies can minimize excess inventory and reduce storage costs.
• Improved workflow: Visual cues make it easy for workers to understand what needs to be done next, leading to more efficient processes.
• Increased flexibility: Kanban allows for quick adjustments to changing demand, reducing the risk of overproduction or stockouts.
What is a Picking List?
A Picking List, on the other hand, is a document used in order fulfillment processes. It contains a list of items to be picked from inventory to complete a customer order. Picking Lists are widely used in warehouses and distribution centers to streamline the picking process and ensure accurate order fulfillment.
How Picking Lists Work
Picking Lists are typically generated by an inventory management system or an enterprise resource planning (ERP) system. When a customer places an order, the system creates a Picking List detailing the items that need to be picked, their quantities, and their locations within the warehouse. Warehouse workers use these lists to locate and pick the necessary items, which are then packed and shipped to fulfill the customer order.
Types of Picking Lists
There are several types of Picking Lists, including:
• Single-order Picking List: This list is used to pick items for a single customer order. It’s straightforward and ideal for small-scale operations.
• Batch Picking List: This combines multiple orders into a single list, allowing workers to pick items for several orders in one go. This method can improve efficiency in larger warehouses with high order volumes.
• Zone Picking List: This method divides the warehouse into zones, with each worker responsible for a specific area. The Picking List is divided accordingly, and items are picked zone by zone.
Benefits of Picking Lists
Using Picking Lists offers several benefits:
• Increased accuracy: Picking Lists provide clear instructions, reducing errors in order fulfillment.
• Enhanced efficiency: Workers can quickly locate and pick items, saving time and effort.
• Better organization: Picking Lists help maintain order in the warehouse, making it easier to manage inventory.
Comparing Kanban and Picking Lists
While both Kanban and Picking Lists are essential tools in inventory management, they serve different functions and are used in distinct contexts. Here are some key differences between the two:
Purpose
• Kanban: The primary purpose of Kanban is to manage and optimize production processes, ensuring that inventory is produced just in time to meet demand. It focuses on maintaining optimal inventory levels and improving workflow efficiency.
• Picking List: The main purpose of a Picking List is to facilitate order fulfillment by providing clear instructions for picking items from inventory. It focuses on ensuring accurate and efficient order processing.
Usage
• Kanban: Kanban is used primarily in manufacturing and production environments, where it helps streamline the production process and reduce waste.
• Picking List: Picking Lists are used in warehouses and distribution centers to organize and expedite the picking and packing of orders.
Flexibility
• Kanban: Kanban offers high flexibility, allowing for quick adjustments to changes in demand. This makes it ideal for environments with fluctuating production needs.
• Picking List: While Picking Lists can be adapted to different picking methods, they are less flexible than Kanban in terms of responding to sudden changes in demand.
Visual Management
• Kanban: The visual nature of Kanban makes it easy for workers to understand what needs to be done next. This can lead to improved operational efficiency and quick decision-making.
• Picking List: Picking Lists provide detailed written instructions, which are effective for order fulfillment but may not offer the same level of intuitive understanding as Kanban’s visual cues.
Conclusion
Both Kanban and Picking Lists play important roles in inventory management and order fulfillment. Kanban is ideal for managing production processes and reducing waste, while Picking Lists are essential for accurately and efficiently picking and packing customer orders.
Choosing the right system depends on the specific needs of your organization and the nature of your operations. By understanding the differences between Kanban and Picking Lists, businesses can make informed decisions to optimize their processes and achieve greater efficiency.
資料ダウンロード
QCD管理受発注クラウド「newji」は、受発注部門で必要なQCD管理全てを備えた、現場特化型兼クラウド型の今世紀最高の受発注管理システムとなります。
ユーザー登録
受発注業務の効率化だけでなく、システムを導入することで、コスト削減や製品・資材のステータス可視化のほか、属人化していた受発注情報の共有化による内部不正防止や統制にも役立ちます。
NEWJI DX
製造業に特化したデジタルトランスフォーメーション(DX)の実現を目指す請負開発型のコンサルティングサービスです。AI、iPaaS、および先端の技術を駆使して、製造プロセスの効率化、業務効率化、チームワーク強化、コスト削減、品質向上を実現します。このサービスは、製造業の課題を深く理解し、それに対する最適なデジタルソリューションを提供することで、企業が持続的な成長とイノベーションを達成できるようサポートします。
製造業ニュース解説
製造業、主に購買・調達部門にお勤めの方々に向けた情報を配信しております。
新任の方やベテランの方、管理職を対象とした幅広いコンテンツをご用意しております。
お問い合わせ
コストダウンが利益に直結する術だと理解していても、なかなか前に進めることができない状況。そんな時は、newjiのコストダウン自動化機能で大きく利益貢献しよう!
(β版非公開)