- お役立ち記事
- The difference between Labor Cost and Material Cost
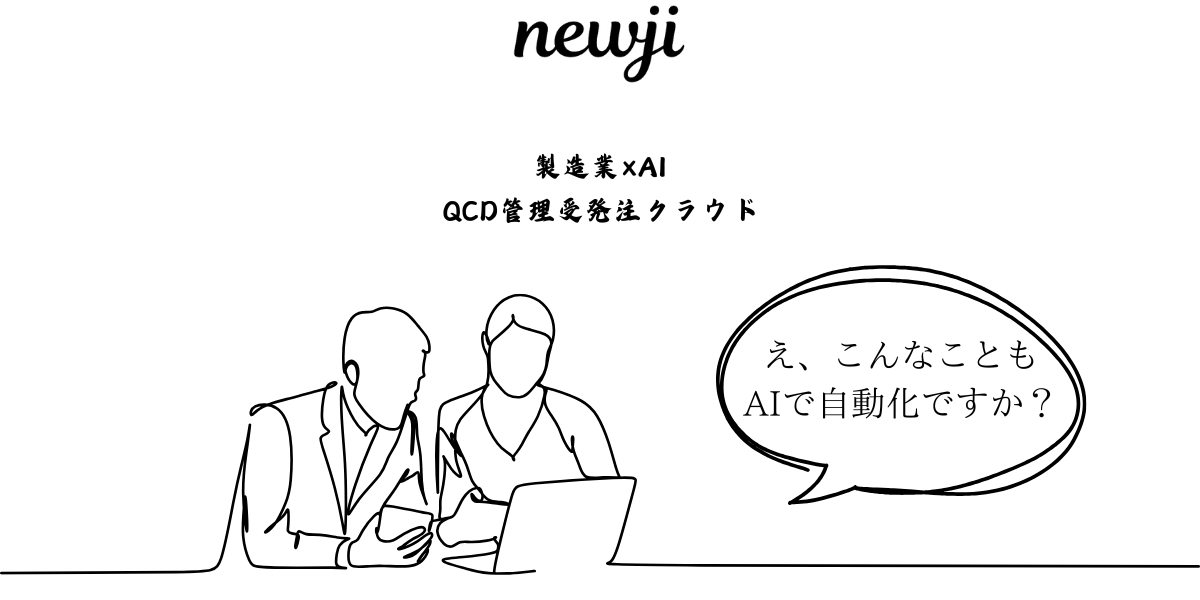
The difference between Labor Cost and Material Cost
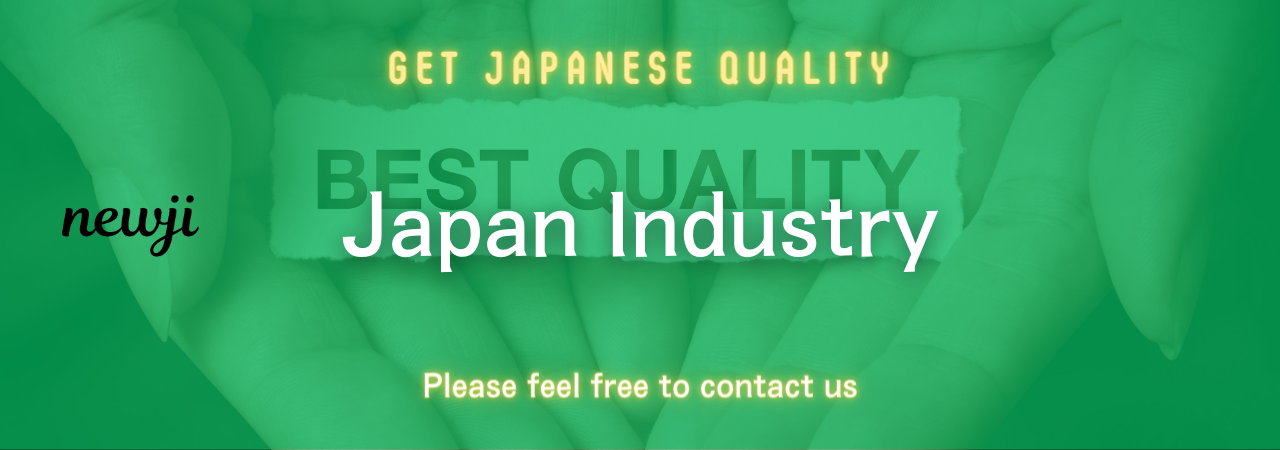
In managing the finances of a business, understanding the various types of costs is crucial.
Two key types of costs that frequently come into play are labor costs and material costs.
While they may seem similar at first glance, they serve quite different roles in the overall expenses of a business.
In this article, we will explore the differences between labor cost and material cost to help you better manage your business finances.
目次
What is Labor Cost?
Labor cost represents the amount of money a company spends on its employees.
It includes wages, salaries, bonuses, and benefits.
These costs are essential for running the business as labor plays a critical role in producing goods and services.
Components of Labor Cost
1. **Wages and Salaries**: The most straightforward part of labor cost is the pay that employees receive per hour or as a monthly salary.
2. **Benefits**: These include health insurance, retirement plans, and other perks.
3. **Bonuses and Incentives**: Extra payments made to employees for achieving certain targets.
4. **Payroll Taxes**: Taxes that the company must pay based on the employee’s salary.
Understanding these components helps businesses allocate resources effectively.
What is Material Cost?
Material cost is the expense incurred in purchasing the raw materials needed for production.
These materials are transformed into final products that are sold to customers.
Components of Material Cost
1. **Raw Materials**: Basic substances that are used in the creation of a product.
2. **Components and Parts**: Sub-assemblies or parts purchased from suppliers that are used to create the final product.
3. **Packaging**: Materials used to package the final product for sale.
These elements are fundamental to the manufacturing process and a key component of the overall production cost.
Key Differences Between Labor Cost and Material Cost
Understanding the distinction between labor cost and material cost can help in various aspects of business management.
Nature of Costs
Labor cost is typically more variable than material cost.
While raw material prices might fluctuate, labor costs are often more influenced by market conditions, labor laws, and contractual agreements.
Control Over Costs
Businesses generally have more control over material costs than labor costs.
Material costs can be managed through negotiating better rates or bulk purchasing.
Labor costs, on the other hand, are more influenced by external factors such as labor market conditions and government regulations.
Impact on Productivity
High labor costs could either positively or negatively impact productivity.
An investment in skilled labor can lead to higher productivity and better quality products.
In contrast, high material costs directly impact the cost of goods sold, thereby affecting profitability.
Measurement and Tracking
Labor cost is usually measured through payroll and HR systems, making it easier to track.
Material cost requires sophisticated inventory and supply chain management systems to accurately measure and control.
How to Manage Labor Costs Effectively
Effective management of labor costs involves various strategies:
Efficiency and Training
Invest in workforce training to increase productivity.
Well-trained employees can perform tasks more efficiently, reducing the need for overtime and additional labor.
Outsourcing
If it’s more cost-effective, consider outsourcing non-core activities.
This allows the business to focus on its primary operations while keeping labor costs in check.
Use of Technology
Implement automation where possible.
Technology can replace manual labor for repetitive tasks, thereby reducing labor costs in the long run.
How to Manage Material Costs Effectively
Effective management of material costs can significantly improve the profitability of a business.
Bulk Purchasing
Buying materials in bulk can often reduce per-unit costs.
Negotiate with suppliers for bulk discounts or long-term contracts.
Supplier Relationships
Develop strong relationships with suppliers.
Reliable suppliers offer better prices, quality, and turnaround times.
Inventory Management
Implement inventory management systems to avoid over-ordering or stockouts.
Effective inventory management ensures that you have the right amount of materials when needed, reducing waste and unnecessary expenses.
Conclusion
Understanding the differences between labor cost and material cost is essential for effective business management.
Labor cost is more variable and often harder to control, but it is crucial for maintaining productivity.
Material cost, on the other hand, is easier to manage through strategic purchasing and inventory control.
By effectively managing both types of costs, businesses can improve their overall profitability and operational efficiency.
資料ダウンロード
QCD調達購買管理クラウド「newji」は、調達購買部門で必要なQCD管理全てを備えた、現場特化型兼クラウド型の今世紀最高の購買管理システムとなります。
ユーザー登録
調達購買業務の効率化だけでなく、システムを導入することで、コスト削減や製品・資材のステータス可視化のほか、属人化していた購買情報の共有化による内部不正防止や統制にも役立ちます。
NEWJI DX
製造業に特化したデジタルトランスフォーメーション(DX)の実現を目指す請負開発型のコンサルティングサービスです。AI、iPaaS、および先端の技術を駆使して、製造プロセスの効率化、業務効率化、チームワーク強化、コスト削減、品質向上を実現します。このサービスは、製造業の課題を深く理解し、それに対する最適なデジタルソリューションを提供することで、企業が持続的な成長とイノベーションを達成できるようサポートします。
オンライン講座
製造業、主に購買・調達部門にお勤めの方々に向けた情報を配信しております。
新任の方やベテランの方、管理職を対象とした幅広いコンテンツをご用意しております。
お問い合わせ
コストダウンが利益に直結する術だと理解していても、なかなか前に進めることができない状況。そんな時は、newjiのコストダウン自動化機能で大きく利益貢献しよう!
(Β版非公開)