- お役立ち記事
- The difference between Laser Cutting and Plasma Cutting
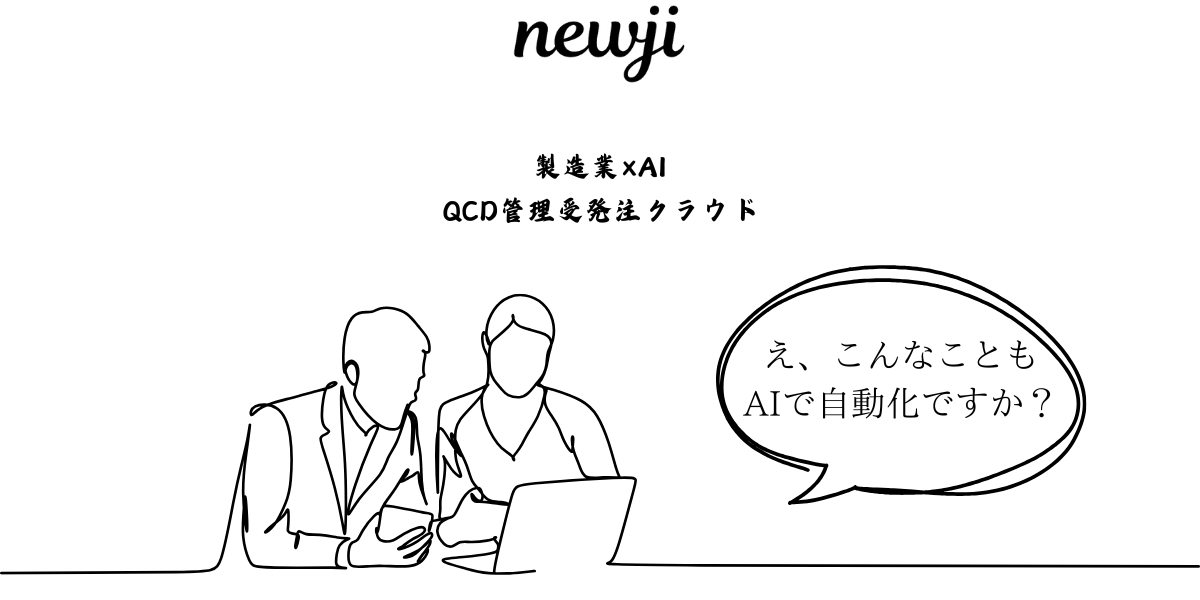
The difference between Laser Cutting and Plasma Cutting
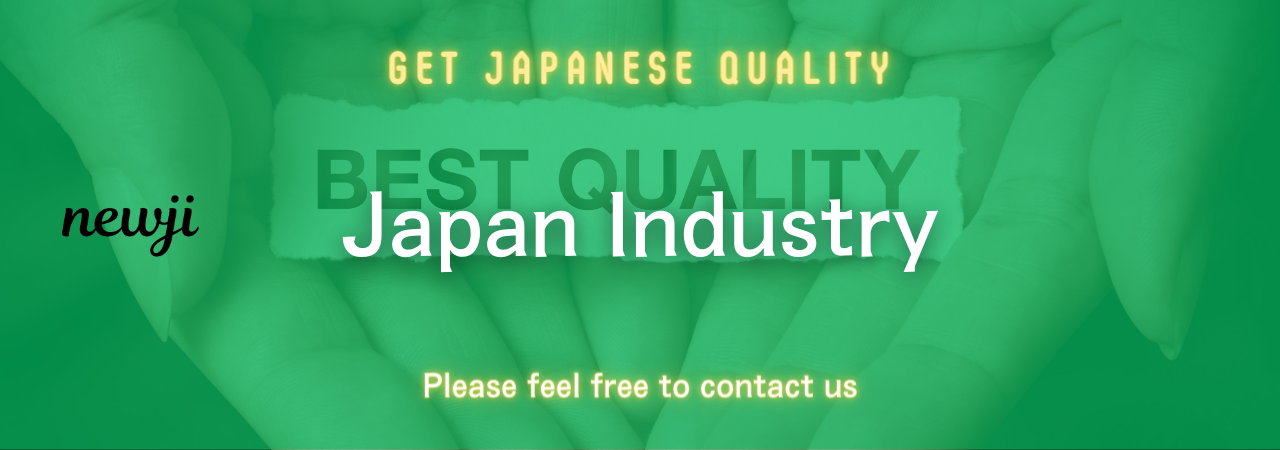
Cutting technology has come a long way, making manufacturing processes faster and more precise.
Two popular methods of cutting different materials are laser cutting and plasma cutting.
If you’re trying to decide between the two, it helps to understand their differences and benefits.
Let’s explore how laser cutting and plasma cutting work, their uses, and some key factors that differentiate them.
目次
What is Laser Cutting?
Laser cutting uses a high-powered laser beam to cut through materials.
This process involves focusing a laser beam onto a material surface, which then melts, burns, or vaporizes away, leaving a clean edge.
Laser cutting is highly accurate, making it a preferred choice for intricate designs and detailed cuts.
How Does Laser Cutting Work?
The process begins by generating a laser in a laser resonator.
Once the laser is created, it reflects off several mirrors, directing the beam through the center of a machine’s cutting head.
The beam is then focused onto the material, cutting through it with pinpoint precision.
Often, a jet of gas, such as nitrogen or oxygen, blows away molten material, ensuring a clean cut.
Applications of Laser Cutting
Laser cutting is versatile and used across many industries.
It’s ideal for cutting metals, plastics, wood, and even paper.
Here are some common applications:
– Manufacturing: Making machine parts and components.
– Automotive: Cutting intricate parts and panels.
– Electronics: Creating circuit boards and electronic devices.
– Art and Craft: Crafting decorative items and intricate patterns.
– Aerospace: Fabricating precision parts for aircraft.
What is Plasma Cutting?
Plasma cutting uses electrically conductive gas to cut through materials.
It generates an electrical arc between an electrode and the material, turning the gas into plasma, which then cuts through the material.
How Does Plasma Cutting Work?
This method starts by creating an electrical arc with an electrode.
The arc ionizes gas (such as compressed air or nitrogen) blowing through a nozzle at high speed.
This process forms plasma, a superheated and electrically conductive gas.
The plasma melts the material, and the force of the gas blows away the molten metal, creating a cut.
Applications of Plasma Cutting
Plasma cutting is particularly effective for cutting thick metals and conductive materials.
Common uses include:
– Fabrication: Cutting thick steel and aluminum plates.
– Automotive: Repairing and customizing car bodies and frames.
– Construction: Cutting beams and metal structures on-site.
– HVAC: Cutting metal sheets for heating, ventilation, and air conditioning systems.
– Salvage and Recycling: Dismantling metal structures for recycling.
Key Differences Between Laser Cutting and Plasma Cutting
Understanding the differences between laser and plasma cutting helps in choosing the right method for your needs.
Precision and Accuracy
Laser cutting is known for its high precision and accuracy.
It produces clean, sharp edges with minimal kerf (material removed during cutting).
This makes it suitable for intricate designs and fine details.
Plasma cutting, while less precise than laser cutting, is highly effective for thicker materials.
It can handle cuts that need less precision but require more power.
Material Thickness
Laser cutting is excellent for thin to moderately thick materials, generally up to 0.5 inches.
It struggles with very thick materials due to the laser’s limited penetrating power.
Plasma cutting excels with thick metals and is efficient for cuts up to 2 inches or more, depending on the machine’s power.
Speed
Plasma cutting is typically faster, especially for thicker materials.
It can cut through thick metal plates more quickly than a laser cutter.
Laser cutting, while slower for thick materials, is fast for thin materials and offers high-speed operations for detailed designs.
Cost
Laser cutting machines are generally more expensive than plasma cutting machines.
They require higher initial investments and running costs, including maintenance and gas consumption.
Plasma cutting machines are more cost-effective for cutting thicker materials.
They require less investment for the same power output and operational capability.
Versatility
Laser cutting is versatile and can cut various materials, including metals, plastics, wood, and glass.
It’s particularly useful for materials that require precision and smooth edges.
Plasma cutting is limited to conductive metals and is best suited for thick materials.
It’s less versatile in terms of material range but highly effective for specific applications.
Choosing the Right Cutting Method
Choosing between laser cutting and plasma cutting depends on several factors, including material type, thickness, required precision, and budget.
Consider the Material
If you need to cut non-metal materials or thin metals with high precision, laser cutting is the way to go.
For cutting thick conductive metals, plasma cutting is more efficient and cost-effective.
Evaluate Costs
Consider your budget for both initial investment and operating costs.
Laser cutting machines are pricier but offer precise results, while plasma cutters are more affordable and better for thick materials.
Precision Requirements
For projects requiring detailed and clean cuts, laser cutting is ideal.
If precision is less of a concern, and you’re working with thick materials, plasma cutting is suitable.
Conclusion
Both laser cutting and plasma cutting have their distinct advantages and applications.
By understanding the differences in precision, material compatibility, speed, cost, and versatility, you can choose the right cutting method for your specific needs.
Whether you opt for the detailed, precision-focused approach of laser cutting or the robust, thick-metal efficiency of plasma cutting, both methods offer valuable solutions for various cutting requirements.
資料ダウンロード
QCD調達購買管理クラウド「newji」は、調達購買部門で必要なQCD管理全てを備えた、現場特化型兼クラウド型の今世紀最高の購買管理システムとなります。
ユーザー登録
調達購買業務の効率化だけでなく、システムを導入することで、コスト削減や製品・資材のステータス可視化のほか、属人化していた購買情報の共有化による内部不正防止や統制にも役立ちます。
NEWJI DX
製造業に特化したデジタルトランスフォーメーション(DX)の実現を目指す請負開発型のコンサルティングサービスです。AI、iPaaS、および先端の技術を駆使して、製造プロセスの効率化、業務効率化、チームワーク強化、コスト削減、品質向上を実現します。このサービスは、製造業の課題を深く理解し、それに対する最適なデジタルソリューションを提供することで、企業が持続的な成長とイノベーションを達成できるようサポートします。
オンライン講座
製造業、主に購買・調達部門にお勤めの方々に向けた情報を配信しております。
新任の方やベテランの方、管理職を対象とした幅広いコンテンツをご用意しております。
お問い合わせ
コストダウンが利益に直結する術だと理解していても、なかなか前に進めることができない状況。そんな時は、newjiのコストダウン自動化機能で大きく利益貢献しよう!
(Β版非公開)