- お役立ち記事
- The difference between Laser Welding and Electron Beam Welding
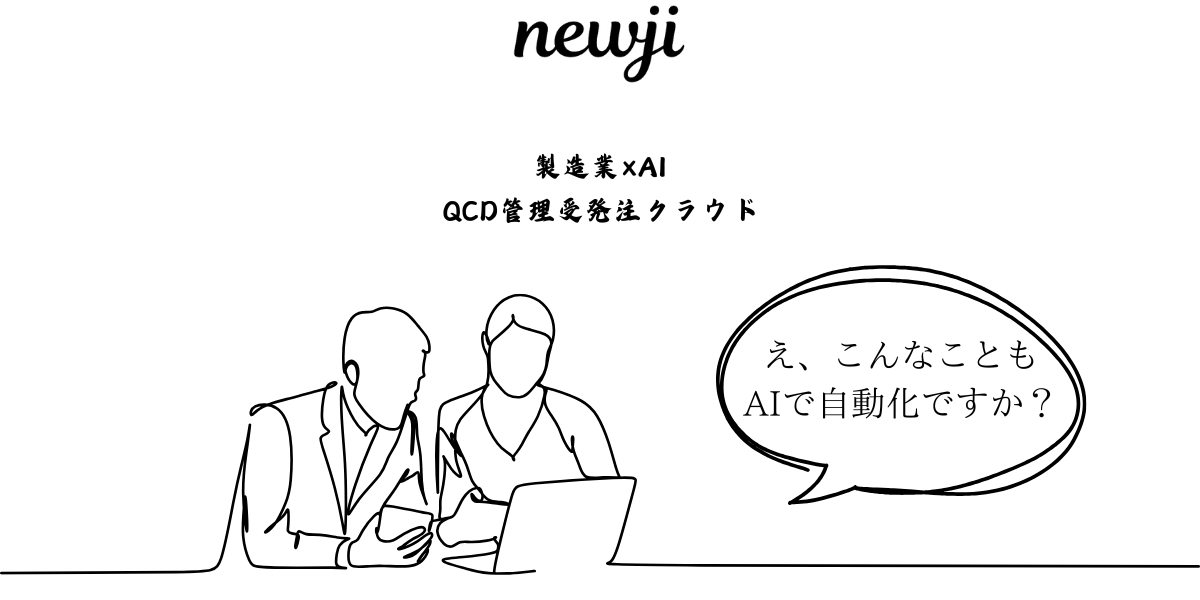
The difference between Laser Welding and Electron Beam Welding
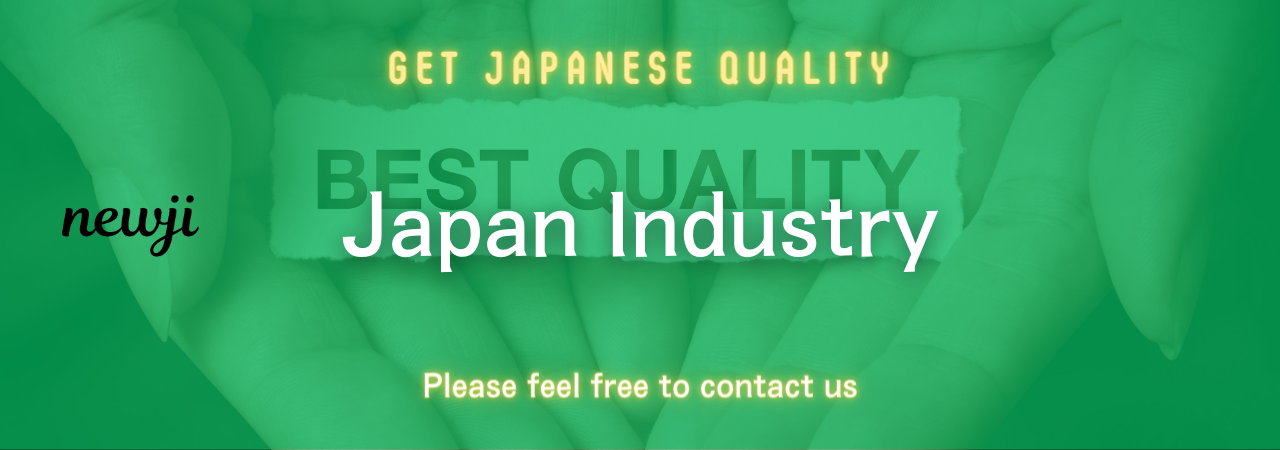
Laser welding and electron beam welding are two advanced welding technologies used in various industries.
These methods are preferred for their precision and efficiency in joining materials.
However, despite their similarities, they have distinct differences that make them suitable for specific applications.
Let’s dive into the specifics of each process and explore their unique features.
目次
Laser Welding: An Overview
Laser welding is a technique that uses a focused laser beam to join materials.
The laser produces a high-intensity light that melts the materials at the joint, allowing them to fuse together.
This process is well-suited for delicate and precision work, as it creates a small heat-affected zone.
How Laser Welding Works
The laser welding process starts with a laser generating a concentrated beam of light.
This beam is directed at the joint of the materials being welded.
The energy of the laser is sufficient to melt the workpieces at the point of contact, creating a weld.
Advantages of Laser Welding
Laser welding offers several benefits:
– **Precision**: The high-intensity laser can target small areas, making it ideal for intricate and delicate jobs.
– **Speed**: The process is quick, reducing production time.
– **Minimal Distortion**: The focused heat source limits the heat-affected zone, minimizing distortion in the materials.
– **Versatility**: Laser welding can be used on various materials, including metals, plastics, and dissimilar materials.
Applications of Laser Welding
Laser welding is employed in various industries, such as:
– **Aerospace**: For precision parts and assemblies.
– **Automotive**: For welding car bodies and components.
– **Medical Devices**: For creating small, intricate parts.
– **Electronics**: For joining tiny components and circuits.
Electron Beam Welding: An Overview
Electron beam welding (EBW) is another high-precision welding process.
It uses a beam of high-velocity electrons to fuse materials together.
This method is known for its ability to penetrate deeply into materials, making it suitable for thick joints.
How Electron Beam Welding Works
In electron beam welding, an electron gun generates a stream of high-velocity electrons.
These electrons are accelerated and focused into a narrow beam directed at the materials’ joint.
The kinetic energy of the electrons converts to heat upon impact, melting and fusing the materials.
Advantages of Electron Beam Welding
Electron beam welding has several key advantages:
– **Deep Penetration**: EBW can weld thicker materials in a single pass.
– **Precision**: Despite its deep penetration capabilities, EBW can also perform intricate welds.
– **Controlled Environment**: The process typically occurs in a vacuum, preventing contamination.
– **High Strength**: The resulting welds are strong and reliable.
Applications of Electron Beam Welding
Electron beam welding is used in industries such as:
– **Aerospace**: For creating critical, high-strength joints.
– **Automotive**: For welding heavy-duty components.
– **Nuclear Industry**: For fabricating reactor parts.
– **Medical Devices**: For producing metal implants and components.
Key Differences Between Laser Welding and Electron Beam Welding
While both laser and electron beam welding are advanced, high-precision techniques, they have several key differences:
Energy Source
– **Laser Welding**: Uses a concentrated laser beam (light).
– **Electron Beam Welding**: Utilizes high-velocity electrons (particle beam).
Heat-Affected Zone
– **Laser Welding**: Creates a smaller heat-affected zone, making it ideal for delicate tasks.
– **Electron Beam Welding**: Can result in a larger heat-affected zone due to deeper penetration.
Operating Environment
– **Laser Welding**: Can typically operate in normal atmospheric conditions.
– **Electron Beam Welding**: Requires a vacuum environment to prevent electron scattering.
Material Thickness
– **Laser Welding**: Best for thin to moderate material thicknesses.
– **Electron Beam Welding**: Suitable for thicker materials due to deeper penetration ability.
Cost and Equipment Complexity
– **Laser Welding**: Generally has lower initial equipment costs and simpler setup.
– **Electron Beam Welding**: Involves higher equipment costs and greater complexity due to the need for a vacuum chamber.
Choosing Between Laser Welding and Electron Beam Welding
The choice between laser welding and electron beam welding depends on several factors, including the specific application, material type, thickness, and desired outcomes.
Considerations for Laser Welding
Laser welding is ideal when:
– Precision and minimal distortion are required.
– The materials involved are thin or delicate.
– The process needs to be very fast.
Considerations for Electron Beam Welding
Electron beam welding is preferred when:
– Deep penetration is necessary.
– The materials are thick or require strong, reliable welds.
– The welding must occur in a highly controlled, contamination-free environment.
Conclusion
Both laser welding and electron beam welding are innovative technologies that offer unique advantages for various industries.
Understanding the differences between these two methods can help in selecting the appropriate technique for your specific welding needs.
Whether you prioritize precision, depth, or operating environment, there is a welding solution that fits your requirements perfectly.
資料ダウンロード
QCD調達購買管理クラウド「newji」は、調達購買部門で必要なQCD管理全てを備えた、現場特化型兼クラウド型の今世紀最高の購買管理システムとなります。
ユーザー登録
調達購買業務の効率化だけでなく、システムを導入することで、コスト削減や製品・資材のステータス可視化のほか、属人化していた購買情報の共有化による内部不正防止や統制にも役立ちます。
NEWJI DX
製造業に特化したデジタルトランスフォーメーション(DX)の実現を目指す請負開発型のコンサルティングサービスです。AI、iPaaS、および先端の技術を駆使して、製造プロセスの効率化、業務効率化、チームワーク強化、コスト削減、品質向上を実現します。このサービスは、製造業の課題を深く理解し、それに対する最適なデジタルソリューションを提供することで、企業が持続的な成長とイノベーションを達成できるようサポートします。
オンライン講座
製造業、主に購買・調達部門にお勤めの方々に向けた情報を配信しております。
新任の方やベテランの方、管理職を対象とした幅広いコンテンツをご用意しております。
お問い合わせ
コストダウンが利益に直結する術だと理解していても、なかなか前に進めることができない状況。そんな時は、newjiのコストダウン自動化機能で大きく利益貢献しよう!
(Β版非公開)