- お役立ち記事
- The difference between Lot Size and Batch Size
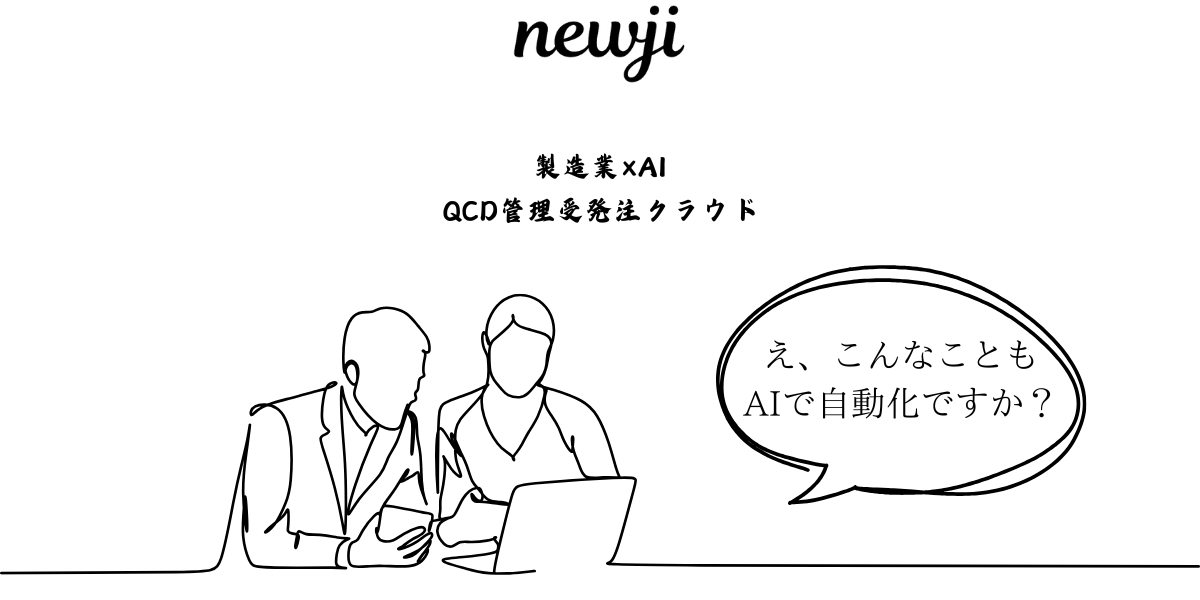
The difference between Lot Size and Batch Size
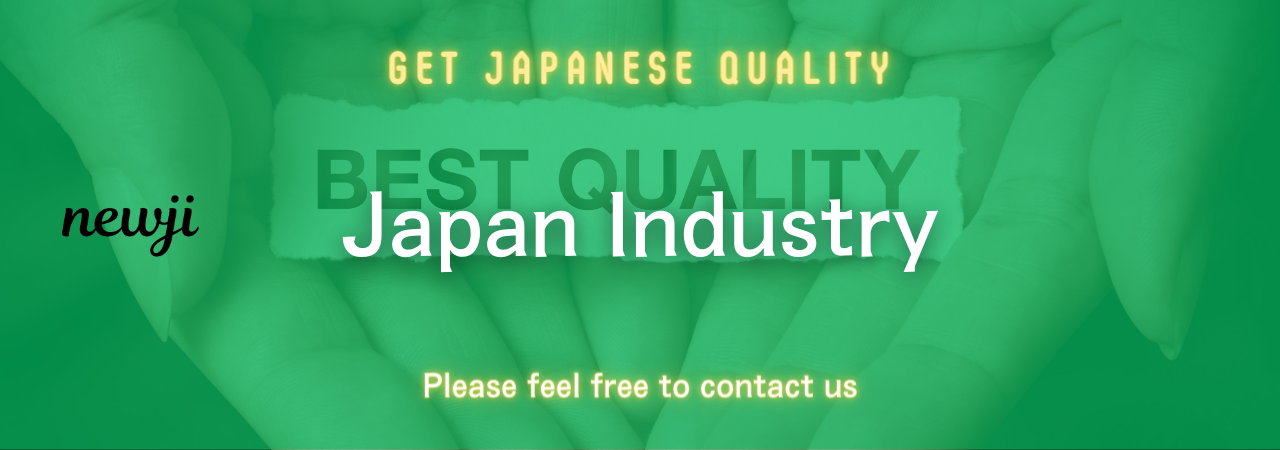
Understanding the concepts of lot size and batch size is crucial for anyone involved in manufacturing, supply chain management, or even small business operations.
Both terms often get confused because they can appear similar, especially to those who are not familiar with specific industry jargon.
However, each serves a distinct purpose and can significantly impact the efficiency and effectiveness of production processes.
This article will explain the key differences between lot size and batch size, how they affect manufacturing processes, and why they are important.
目次
What is Lot Size?
Lot size refers to the total quantity of a product that is produced or purchased in a single run.
It encompasses the entire number of units that go through the production line before stopping the process for the next product or adjusting the equipment.
For instance, if a factory decides to produce 1,000 units of a specific product before switching to another, then the lot size is 1,000 units.
The term is widely used in inventory management, purchasing, and production planning, where optimizing lot size can lead to cost savings and improved efficiency.
Factors Influencing Lot Size
Several factors come into play when deciding the appropriate lot size:
– **Demand Forecast:** Understanding consumer demand is essential.
Underestimating could lead to stockouts, while overestimating could result in unnecessary inventory costs.
– **Cost Considerations:** Producing larger lot sizes can offer economies of scale, reducing the cost per unit.
However, it can also increase holding costs.
– **Production Capacity:** The capacity of the production line and the availability of raw materials can limit the lot size.
– **Lead Times:** The time taken to set up machinery, procure materials, and complete production must be considered.
What is Batch Size?
Batch size, on the other hand, refers to the quantity of items that go through a particular stage of production at one time.
It is a subset of the lot size and signifies smaller segments within the lot size that are processed together.
In simple terms, if your lot size is the entire cake, your batch size is one slice of that cake.
For example, if a total of 1,000 units (lot size) need to be produced and you decide to process them in groups of 200 units, then each operational run of 200 units is termed a batch.
This can be incredibly useful for quality control and testing, as well as meeting specific equipment or process requirements.
Factors Influencing Batch Size
When determining batch size, various considerations must be taken into account:
– **Machine Capacity:** Equipment limitations can dictate the maximum number of units that can be processed at one time.
– **Process Efficiency:** Smaller batch sizes allow for easier quality control and faster detection of issues.
However, smaller batches could mean more frequent changeovers, impacting efficiency.
– **Quality Assurance:** Smaller batches offer better control over quality and defect rates can be more easily managed.
– **Speed and Flexibility:** Smaller batches enable quicker adjustments based on quality control feedback or changes in demand, enhancing production flexibility.
Key Differences Between Lot Size and Batch Size
While lot size and batch size might seem similar, they have distinct roles in the manufacturing process.
Scope of Quantity
– **Lot Size:** Refers to the total number of units produced or purchased in one go.
Think of it as the master plan for the quantity to be handled in one production run.
– **Batch Size:** Refers to smaller segments of units within the lot size that are handled together through a specific stage of manufacturing.
It provides a focused approach to production in bits and pieces, rather than all at once.
Impact on Production
– **Lot Size:** Affects overarching production planning, inventory management, and cost efficiencies.
A larger lot size can optimize production runs and minimize setup times, but may increase holding costs.
– **Batch Size:** Impacts the day-to-day operational efficiency and quality control.
Smaller batch sizes allow for better scrutiny and flexibility but might require more frequent machine setup and changeover times.
Cost Implications
– **Lot Size:** Primarily concerned with reducing overall production costs per unit through economies of scale.
However, improper sizing can lead to increased inventory costs.
– **Batch Size:** Balances the cost by optimizing process efficiency and quality control.
While it could increase operational costs due to frequent resets, it often results in lower waste and defect rates.
Why Understanding the Difference Matters
Grasping the distinction between lot size and batch size is crucial for improving production efficiency and product quality.
It can help in streamlining resources, reducing waste, and meeting customer demands more effectively.
Inventory Management
By understanding these concepts, businesses can better manage their inventories.
Optimal lot sizes reduce holding costs while still meeting demand, and appropriate batch sizes can ensure quality products reach consumers.
Cost Savings
With the right balance, companies can achieve significant cost savings.
Minimizing changeover times, reducing waste, and improving quality control are all possible with an informed approach to lot size and batch size.
Product Quality
Effective batch sizing can lead to better quality control.
Smaller batches facilitate more frequent inspections and quicker rectification of any detected issues, ensuring high-quality output.
Conclusion
Understanding the difference between lot size and batch size can greatly impact the efficiency, cost-effectiveness, and quality of production processes.
Lot size pertains to the total quantity produced in one run, while batch size refers to smaller groups of units processed together within that run.
Each has unique implications for production planning, cost considerations, and quality control.
By paying attention to these factors, businesses can optimize their operations, reduce costs, and deliver high-quality products to their customers.
資料ダウンロード
QCD調達購買管理クラウド「newji」は、調達購買部門で必要なQCD管理全てを備えた、現場特化型兼クラウド型の今世紀最高の購買管理システムとなります。
ユーザー登録
調達購買業務の効率化だけでなく、システムを導入することで、コスト削減や製品・資材のステータス可視化のほか、属人化していた購買情報の共有化による内部不正防止や統制にも役立ちます。
NEWJI DX
製造業に特化したデジタルトランスフォーメーション(DX)の実現を目指す請負開発型のコンサルティングサービスです。AI、iPaaS、および先端の技術を駆使して、製造プロセスの効率化、業務効率化、チームワーク強化、コスト削減、品質向上を実現します。このサービスは、製造業の課題を深く理解し、それに対する最適なデジタルソリューションを提供することで、企業が持続的な成長とイノベーションを達成できるようサポートします。
オンライン講座
製造業、主に購買・調達部門にお勤めの方々に向けた情報を配信しております。
新任の方やベテランの方、管理職を対象とした幅広いコンテンツをご用意しております。
お問い合わせ
コストダウンが利益に直結する術だと理解していても、なかなか前に進めることができない状況。そんな時は、newjiのコストダウン自動化機能で大きく利益貢献しよう!
(Β版非公開)