- お役立ち記事
- The difference between Lot Tracking and Serial Tracking
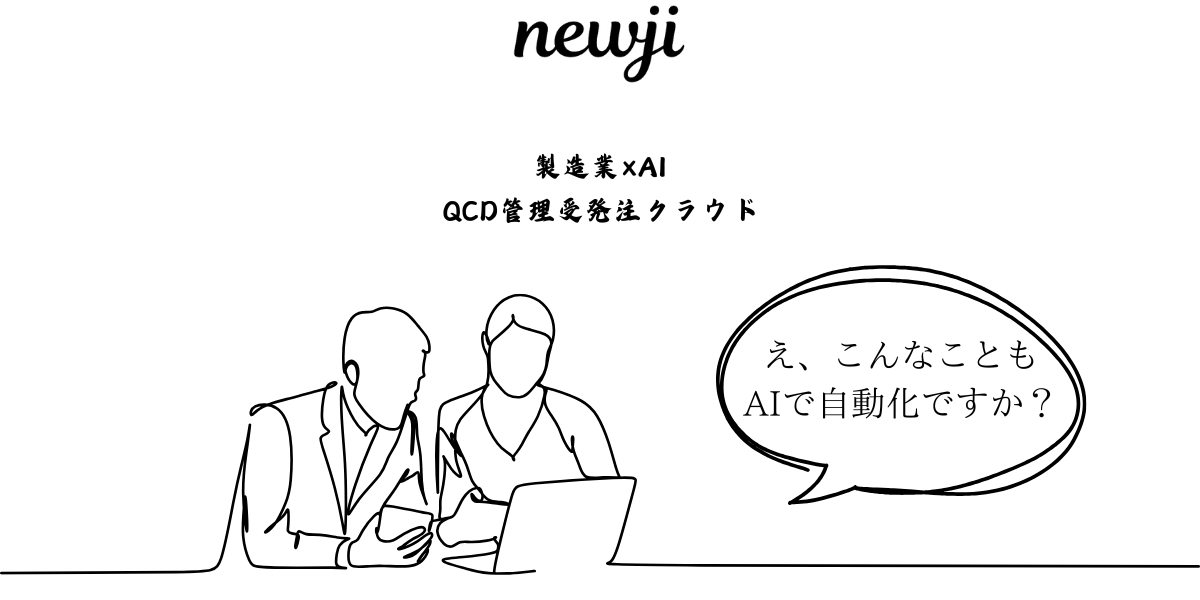
The difference between Lot Tracking and Serial Tracking
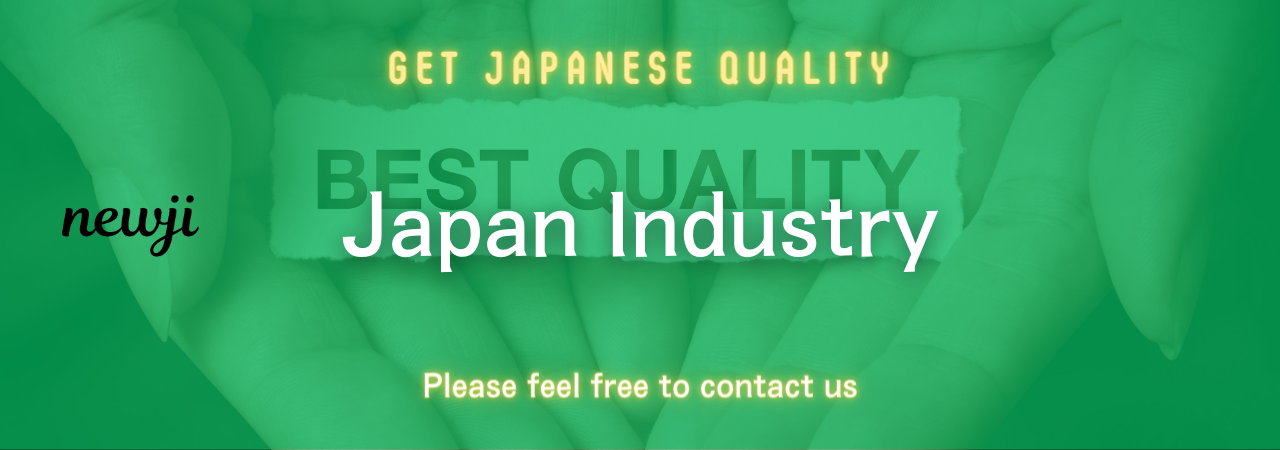
Tracking inventory accurately is essential for any business, especially one that deals in physical goods. Proper tracking ensures no item is misplaced and no expiration dates are neglected. Two of the most commonly used methods for tracking inventory are lot tracking and serial tracking. Each offers its own set of benefits and challenges. In this article, we will delve into the key differences between lot tracking and serial tracking, helping you understand which method suits your business needs.
目次
What is Lot Tracking?
Lot tracking, sometimes referred to as batch tracking, is a method of inventory control where items are grouped together into “lots.” These lots can be managed as a single unit. Each lot is assigned an identification number, making it easier to track from production to sale.
How Lot Tracking Works
Lot tracking involves grouping items that share common characteristics. For instance, products manufactured on the same day or from the same batch of materials can be grouped into a lot.
Every lot is given a unique identifier. This allows businesses to track the entire batch efficiently.
This unique ID can help companies keep tabs on various stages of a product’s lifecycle, from manufacturing to distribution.
Benefits of Lot Tracking
Easier Product Recalls: If a defect is found in a single item, the whole lot can be recalled rather than individual items.
Enhanced Quality Control: With lot numbers, businesses can monitor product quality and identify any variations across different batches.
Simplified Compliance: Many industries require compliance with regulatory standards. Lot tracking makes it easier to maintain these records.
Cost-Effective: Managing inventory in bulk can often be less expensive and labor-intensive than tracking individual items.
What is Serial Tracking?
Serial tracking involves assigning a unique serial number to each individual item. Unlike lot tracking, each item is tracked on its own, rather than as part of a batch.
How Serial Tracking Works
When an individual item is manufactured or received, it is assigned a unique serial number.
This serial number is then used to track the item throughout its entire lifecycle, from storage and transport to sale and service.
Each serial number is unique to one item, providing a high level of detail and traceability.
Benefits of Serial Tracking
Detailed Traceability: Each item can be tracked individually, providing comprehensive data and history of each product.
Better Inventory Management: Knowing the exact location and history of each item can improve stock management and reduce losses.
Enhanced Customer Service: Issues related to specific items can be resolved more quickly and accurately.
Better Theft Prevention: Unique serial numbers make it easier to identify and recover stolen goods.
Key Differences Between Lot Tracking and Serial Tracking
Scope of Tracking
Lot Tracking: Monitors a group of items as a single unit using one lot number.
Serial Tracking: Tracks each item individually with a unique serial number.
Usefulness in Recall Situations
Lot Tracking: Efficient for recalling defective products in bulk.
Serial Tracking: More efficient for isolating specific defective items.
Level of Detail
Lot Tracking: Provides information about the collective group but not individual items.
Serial Tracking: Offers detailed information about each specific item.
Industries Suitable for Each Method
Lot Tracking: Often used in industries where products are manufactured in batches, such as pharmaceuticals, food, and beverages.
Serial Tracking: Commonly used in industries requiring individual item tracking, like electronics, automotive, and luxury goods.
Choosing the Right Method for Your Business
Deciding between lot tracking and serial tracking depends largely on the nature of your business and the type of products you handle. If your business deals with large quantities of goods that can be managed as groups, lot tracking could be the more efficient choice. Conversely, if individual tracking offers more value to your operations, serial tracking is the better option.
Factors to Consider
Product Type: Consider the nature of the products. Are they more effectively tracked as groups or individually?
Regulatory Requirements: Some industries mandate a specific form of tracking.
Resource Availability: Assess the manpower and technology you have available for managing inventory.
Cost Implications: Determine which method aligns better with your budget constraints.
Implementing Tracking Systems
Once you’ve decided which tracking method suits your business, the next step is implementation. This involves choosing the right tools and software, training your staff, and setting up processes to ensure effective tracking.
Choosing the Right Tools
Research software solutions that offer lot tracking or serial tracking capabilities. Many inventory management systems come equipped with these features.
Ensure the software integrates well with your existing systems and processes.
Training Employees
Proper training ensures that your staff understands how to use the new tracking system efficiently.
Offer ongoing support and resources for any questions or issues that arise.
Conclusion
Both lot tracking and serial tracking offer unique advantages and cater to different business needs. Understanding their differences and benefits allows you to make an informed decision that best suits your operational requirements. Select the method that aligns with your business goals, regulatory needs, and customer service expectations. Whether you opt for lot tracking or serial tracking, enhancing your inventory management should always be the ultimate goal.
資料ダウンロード
QCD調達購買管理クラウド「newji」は、調達購買部門で必要なQCD管理全てを備えた、現場特化型兼クラウド型の今世紀最高の購買管理システムとなります。
ユーザー登録
調達購買業務の効率化だけでなく、システムを導入することで、コスト削減や製品・資材のステータス可視化のほか、属人化していた購買情報の共有化による内部不正防止や統制にも役立ちます。
NEWJI DX
製造業に特化したデジタルトランスフォーメーション(DX)の実現を目指す請負開発型のコンサルティングサービスです。AI、iPaaS、および先端の技術を駆使して、製造プロセスの効率化、業務効率化、チームワーク強化、コスト削減、品質向上を実現します。このサービスは、製造業の課題を深く理解し、それに対する最適なデジタルソリューションを提供することで、企業が持続的な成長とイノベーションを達成できるようサポートします。
オンライン講座
製造業、主に購買・調達部門にお勤めの方々に向けた情報を配信しております。
新任の方やベテランの方、管理職を対象とした幅広いコンテンツをご用意しております。
お問い合わせ
コストダウンが利益に直結する術だと理解していても、なかなか前に進めることができない状況。そんな時は、newjiのコストダウン自動化機能で大きく利益貢献しよう!
(Β版非公開)