- お役立ち記事
- The difference between Maintenance Planning and Preventive Maintenance Planning
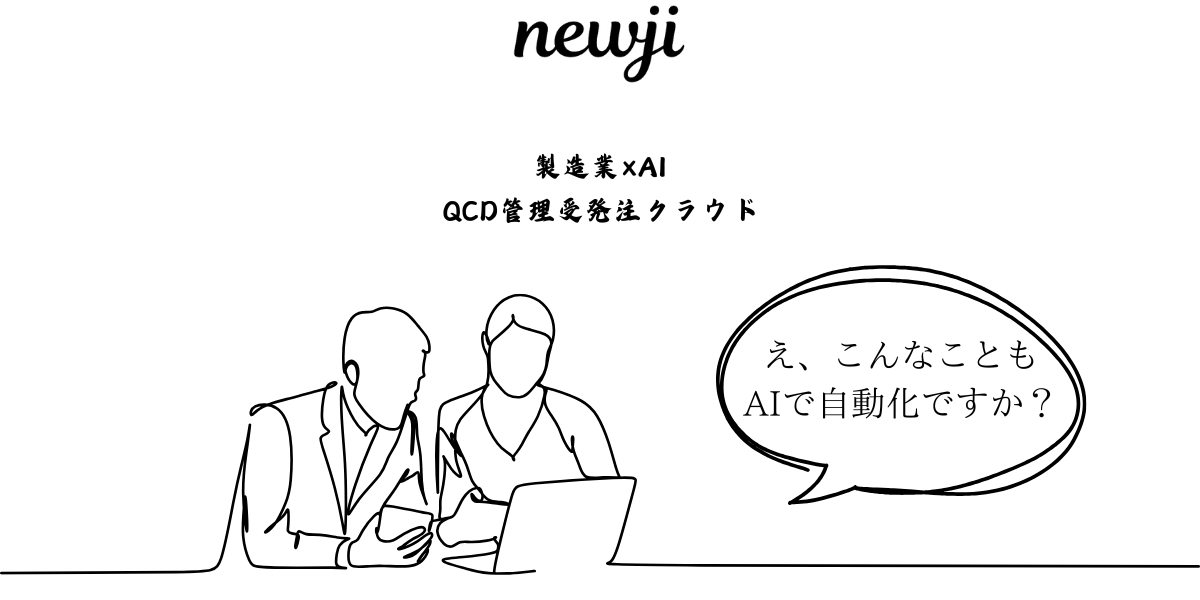
The difference between Maintenance Planning and Preventive Maintenance Planning
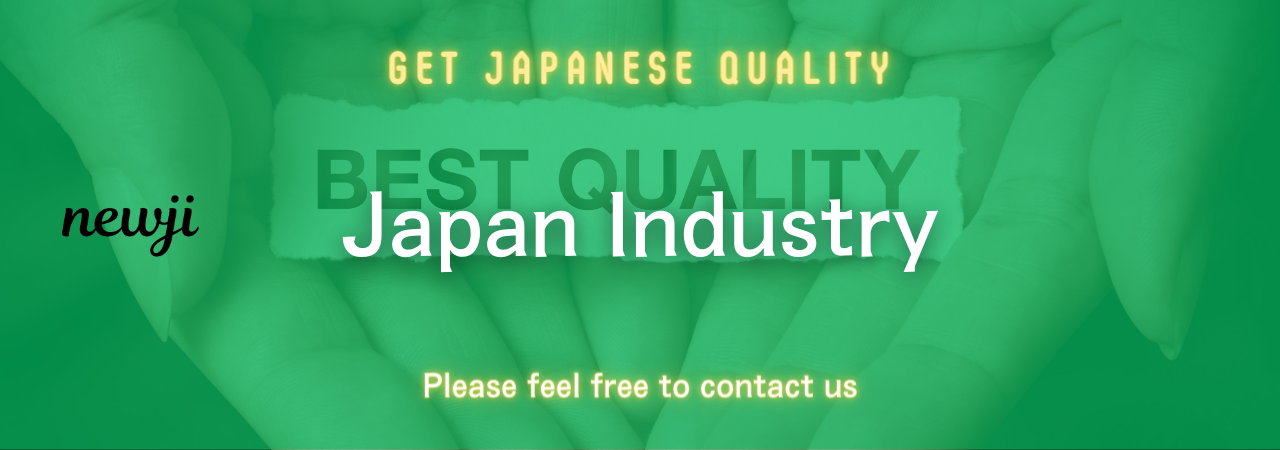
Maintenance planning and preventive maintenance planning are two essential concepts in the world of facility management and machinery upkeep.
Understanding their differences can greatly improve the efficiency and lifespan of equipment.
In this article, we will delve into what sets these two types of maintenance planning apart and why both are crucial for smooth operations.
目次
What is Maintenance Planning?
Maintenance planning involves the systematic scheduling of tasks required to keep equipment and facilities in optimal working condition.
It encompasses the identification, organization, and allocation of resources for performing maintenance activities.
This type of planning ensures that machinery and systems are repaired, serviced, and updated at the right time to prevent unexpected breakdowns.
The Importance of Maintenance Planning
Proper maintenance planning can save organizations significant amounts of money in the long run.
By scheduling regular check-ups and repairs, the potential for sudden equipment failures is minimized.
This not only reduces downtime but also enhances productivity.
Key Components of Maintenance Planning
– **Resource Allocation**:
Assigning the right number of technicians and procuring necessary parts ahead of time.
– **Scheduling**:
Setting up timelines for inspections, repairs, and replacements.
– **Documentation**:
Keeping records of maintenance activities for future reference.
– **Monitoring**:
Regularly reviewing the status of equipment to identify potential issues before they become major problems.
What is Preventive Maintenance Planning?
Preventive maintenance planning is a proactive approach aimed at preventing equipment failures before they occur.
It involves the systematic scheduling of specific tasks designed to reduce the likelihood of malfunction.
These tasks include regular inspections, lubrication, adjustments, cleaning, and parts replacement.
The Importance of Preventive Maintenance Planning
Preventive maintenance planning is essential for extending the lifespan of equipment.
By addressing minor issues before they become significant problems, it ensures that machinery operates efficiently.
This type of planning can lead to fewer major repairs, reduced downtime, and cost savings.
Key Components of Preventive Maintenance Planning
– **Regular Inspections**:
Scheduling frequent checks to spot potential problems early.
– **Lubrication**:
Ensuring that moving parts are well-oiled to reduce wear and tear.
– **Adjustments**:
Making necessary tweaks to equipment to maintain optimal performance.
– **Cleaning**:
Keeping machinery clean to prevent dirt and debris from causing damage.
– **Parts Replacement**:
Replacing worn-out parts before they cause failure.
Comparing Maintenance Planning and Preventive Maintenance Planning
While both maintenance planning and preventive maintenance planning aim to keep equipment in good working condition, they do so in different ways.
Understanding their differences can help you implement the right strategy for your organization.
Focus and Approach
Maintenance planning is broader and includes a variety of tasks such as repairs, updates, and general upkeep.
It involves both reactive and proactive elements.
Preventive maintenance planning, on the other hand, is entirely proactive.
It focuses specifically on tasks designed to prevent equipment failure.
Scheduling
Maintenance planning schedules all types of maintenance tasks, including emergency repairs and regular check-ups.
Preventive maintenance planning strictly schedules tasks that are intended to prevent equipment from breaking down.
Resource Allocation
In maintenance planning, resources are allocated for a wide range of activities, including troubleshooting and emergency repairs.
With preventive maintenance planning, resources are focused on preemptive measures to avoid breakdowns.
Benefits of Combining Both Types of Planning
To maximize equipment efficiency and longevity, combining both maintenance planning and preventive maintenance planning can be highly effective.
Reduces Downtime
Having a comprehensive maintenance schedule that includes preventive measures can significantly reduce unexpected downtime.
This leads to smoother operations and increased productivity.
Cost Savings
Preventing problems before they escalate into costly repairs can save significant amounts of money.
Additionally, scheduled maintenance helps avoid the high costs associated with emergency repairs.
Enhanced Equipment Lifespan
Regular maintenance and preventive measures can extend the lifespan of machinery and equipment.
This means you can get the most out of your assets before needing to replace them.
Implementing Maintenance Planning and Preventive Maintenance Planning
When implementing maintenance planning and preventive maintenance planning, consider the following steps:
Conduct a Thorough Assessment
Start by assessing your equipment and facilities.
Identify critical assets and determine what types of maintenance they require.
Develop a Comprehensive Schedule
Create a detailed maintenance schedule that includes both regular check-ups and preventive measures.
Ensure that this schedule is realistic and achievable.
Allocate Resources Wisely
Ensure you have the necessary resources to carry out the maintenance tasks.
This includes skilled technicians, tools, and spare parts.
Monitor and Adjust
Regularly review the effectiveness of your maintenance plans.
Make adjustments as needed to ensure that both reactive and preventive measures are working optimally.
Conclusion
Understanding the difference between maintenance planning and preventive maintenance planning is key to effective facility and equipment management.
While maintenance planning covers a broad range of tasks aimed at keeping machinery in good condition, preventive maintenance planning focuses on proactive measures to prevent failures.
Combining both approaches can lead to reduced downtime, cost savings, and an extended lifespan for your equipment.
Proper implementation of these plans will ensure that your operations run smoothly and efficiently.
資料ダウンロード
QCD調達購買管理クラウド「newji」は、調達購買部門で必要なQCD管理全てを備えた、現場特化型兼クラウド型の今世紀最高の購買管理システムとなります。
ユーザー登録
調達購買業務の効率化だけでなく、システムを導入することで、コスト削減や製品・資材のステータス可視化のほか、属人化していた購買情報の共有化による内部不正防止や統制にも役立ちます。
NEWJI DX
製造業に特化したデジタルトランスフォーメーション(DX)の実現を目指す請負開発型のコンサルティングサービスです。AI、iPaaS、および先端の技術を駆使して、製造プロセスの効率化、業務効率化、チームワーク強化、コスト削減、品質向上を実現します。このサービスは、製造業の課題を深く理解し、それに対する最適なデジタルソリューションを提供することで、企業が持続的な成長とイノベーションを達成できるようサポートします。
オンライン講座
製造業、主に購買・調達部門にお勤めの方々に向けた情報を配信しております。
新任の方やベテランの方、管理職を対象とした幅広いコンテンツをご用意しております。
お問い合わせ
コストダウンが利益に直結する術だと理解していても、なかなか前に進めることができない状況。そんな時は、newjiのコストダウン自動化機能で大きく利益貢献しよう!
(Β版非公開)