- お役立ち記事
- The difference between Manufacturing Capacity and Production Capacity
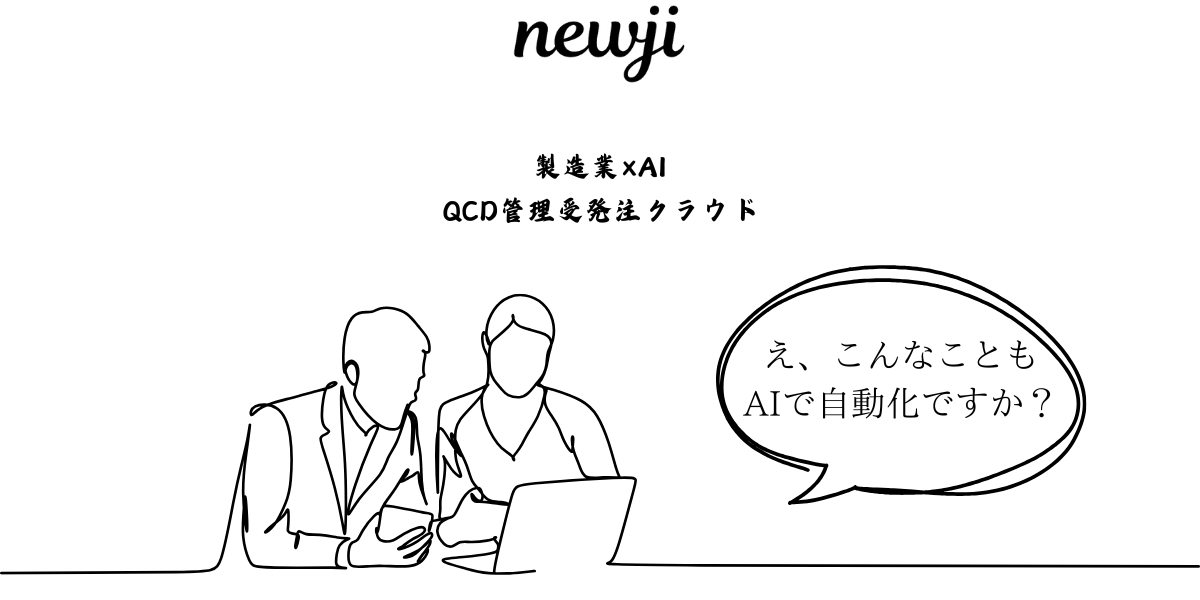
The difference between Manufacturing Capacity and Production Capacity
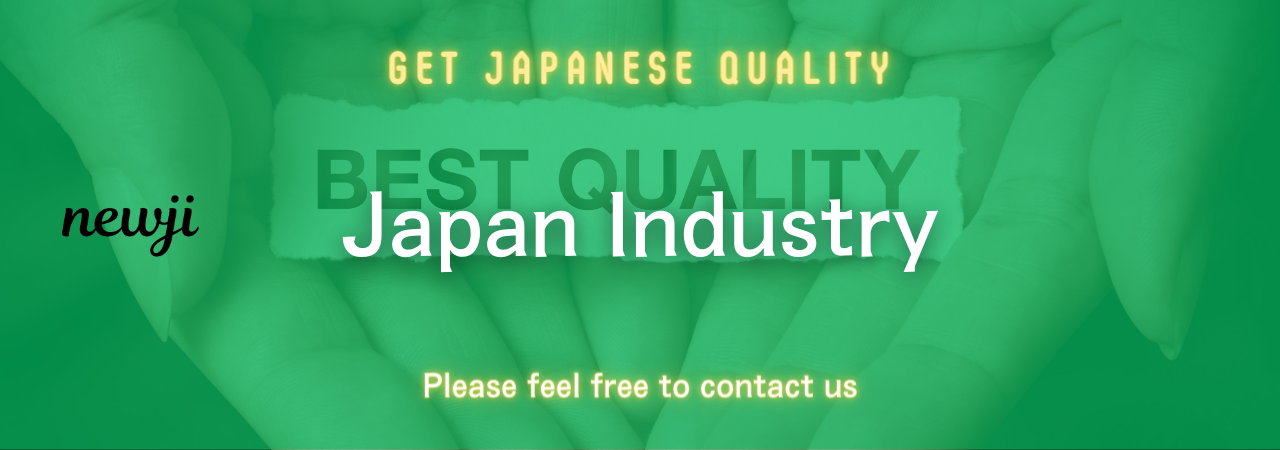
Manufacturing and production capacity might appear to be similar terms, but they represent different aspects of a company’s capabilities.
Understanding these differences can be crucial for efficient planning and optimizing operations.
This article delves into what sets manufacturing capacity apart from production capacity, and why knowing the distinction matters.
目次
Defining Manufacturing Capacity
Manufacturing capacity refers to the maximum output that a manufacturing facility can achieve under ideal conditions.
This takes into consideration various factors such as machinery, labor, and materials.
It’s essentially the maximum volume of products that can be produced within a given timeframe.
When we talk about manufacturing capacity, we’re focusing on the ability of the physical machinery and systems.
For example, if a factory has three production lines and each can produce 100 units per hour, the manufacturing capacity is 300 units per hour.
Factors Affecting Manufacturing Capacity
Several factors impact manufacturing capacity:
1. Equipment Efficiency
The efficiency and performance of machinery significantly affect manufacturing output.
Older or poorly maintained equipment may run slower or break down more often, reducing capacity.
2. Labor Availability
Skilled labor is essential to run machines efficiently.
Lack of training or insufficient workforce can limit the total output.
3. Material Availability
Consistent supply of raw materials is crucial to maintain continuous production.
Delays or shortages can halt manufacturing processes.
Defining Production Capacity
Production capacity, on the other hand, is a broader term that encompasses the maximum output that a process can achieve under real-world conditions.
This not only includes the capabilities of the manufacturing components but also other aspects like supply chain efficiency, logistics, and market demand.
When discussing production capacity, we’re considering the entire production line, including planning, scheduling, and delivery.
For instance, even if a factory can manufacture 300 units per hour, its production capacity might be lower due to bottlenecks in supply chain processes or limited market demand.
Factors Affecting Production Capacity
Here are some key factors influencing production capacity:
1. Market Demand
No matter how much a facility can produce, actual production will be aligned with market demand.
Producing beyond demand can result in surplus that needs storage and financial resources.
2. Supply Chain Efficiency
Even with high manufacturing capacity, inefficiencies in transportation, warehousing, and inventory management can lower actual production output.
3. Regulatory Constraints
Compliance with governmental or industry regulations can impact the speed and volume of production, influencing overall capacity.
Why Knowing the Difference Matters
Understanding the distinction between manufacturing and production capacity is vital for several reasons:
1. Optimizing Resources
Knowing the limitations of both types of capacity helps in allocating resources more efficiently.
For example, if manufacturing capacity is high but production capacity is low, efforts should focus on improving the supply chain rather than investing in new machinery.
2. Effective Planning
Realistic production planning requires a comprehensive understanding of both capacities.
This ensures that schedules are achievable and that resources are not overextended.
3. Cost Management
Balancing manufacturing and production capacities can aid in cost management.
For instance, producing at maximum manufacturing capacity when demand is low can lead to unnecessary expenses in storage and overproduction.
Improving Manufacturing and Production Capacities
Enhancing both types of capacities involves distinct strategies:
For Manufacturing Capacity:
1. Upgrade Machinery
Investing in modern equipment can boost manufacturing efficiency and reduce downtime.
2. Staff Training
Regular training sessions can improve labor efficiency, leading to higher output.
3. Maintenance Management
Scheduled maintenance can prevent unexpected breakdowns and maintain optimal machine performance.
For Production Capacity:
1. Streamline Supply Chains
Improving logistics and inventory management can enhance overall production capacity.
2. Enhance Demand Forecasting
Using advanced analytics can predict market demand more accurately, aligning production schedules accordingly.
3. Regulatory Compliance
Staying updated with regulations and integrating them into production planning can help avoid legal bottlenecks.
Conclusion
Understanding the difference between manufacturing capacity and production capacity is essential for effective business management.
While manufacturing capacity focuses on the potential output under optimal conditions, production capacity considers the broader scope of real-world constraints and efficiencies.
Efficiently balancing and optimizing both capacities can lead to better resource utilization, cost savings, and more flexible and responsive operational planning.
資料ダウンロード
QCD調達購買管理クラウド「newji」は、調達購買部門で必要なQCD管理全てを備えた、現場特化型兼クラウド型の今世紀最高の購買管理システムとなります。
ユーザー登録
調達購買業務の効率化だけでなく、システムを導入することで、コスト削減や製品・資材のステータス可視化のほか、属人化していた購買情報の共有化による内部不正防止や統制にも役立ちます。
NEWJI DX
製造業に特化したデジタルトランスフォーメーション(DX)の実現を目指す請負開発型のコンサルティングサービスです。AI、iPaaS、および先端の技術を駆使して、製造プロセスの効率化、業務効率化、チームワーク強化、コスト削減、品質向上を実現します。このサービスは、製造業の課題を深く理解し、それに対する最適なデジタルソリューションを提供することで、企業が持続的な成長とイノベーションを達成できるようサポートします。
オンライン講座
製造業、主に購買・調達部門にお勤めの方々に向けた情報を配信しております。
新任の方やベテランの方、管理職を対象とした幅広いコンテンツをご用意しております。
お問い合わせ
コストダウンが利益に直結する術だと理解していても、なかなか前に進めることができない状況。そんな時は、newjiのコストダウン自動化機能で大きく利益貢献しよう!
(Β版非公開)