- お役立ち記事
- The difference between Manufacturing Standardization and Process Standardization
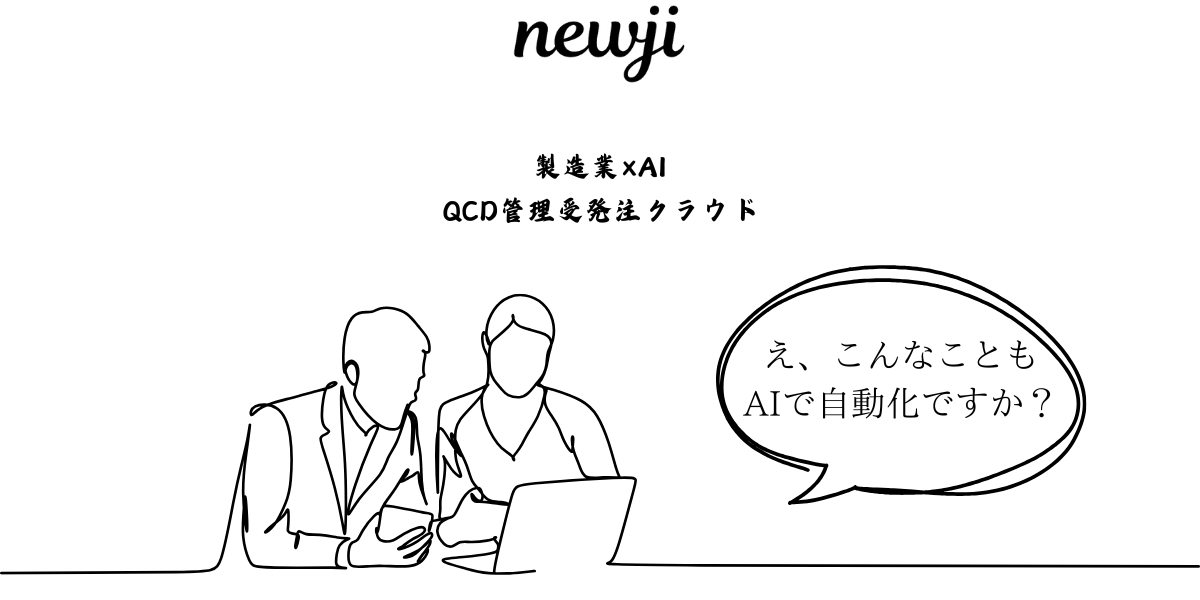
The difference between Manufacturing Standardization and Process Standardization
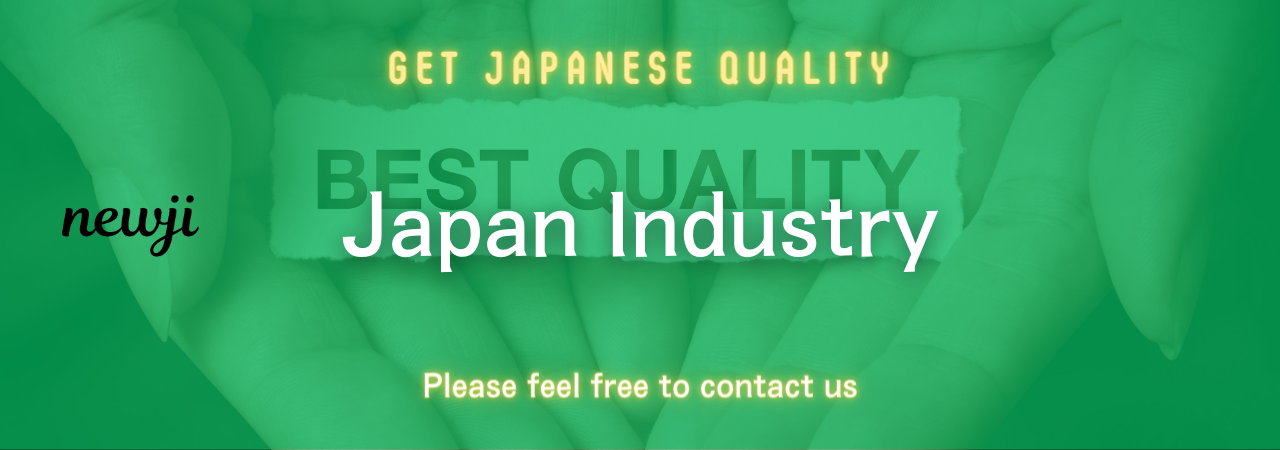
Manufacturing and process standardization are terms often used in industry to describe methods for improving efficiency and consistency.
While they may sound similar, they serve distinct purposes and have unique benefits.
In this article, we will delve deep into understanding the differences between manufacturing standardization and process standardization.
目次
Understanding Manufacturing Standardization
Manufacturing standardization refers to the uniformity of specific manufacturing methods, materials, and products.
In essence, it means creating and adhering to a fixed set of standards for manufacturing practices.
Uniformity in Products
One of the primary goals of manufacturing standardization is to achieve consistency in the products being made.
This means that every item produced should meet predetermined quality and performance specifications.
By using the same materials, methodologies, and machinery, manufacturers can rest assured that their products will be uniform.
Reducing Variability
Variability can be a major challenge in the manufacturing process, resulting in defects and inefficiencies.
Standardization significantly reduces variability by enforcing strict guidelines and quality checks.
This not only improves the overall quality of the product but also minimizes waste and cost.
Global Compatibility
With today’s global market, products often need to meet international standards.
Manufacturing standardization ensures that products are compatible across different regions and markets.
This not only expands the product’s market reach but also facilitates smoother trade and compliance with international regulations.
Understanding Process Standardization
Process standardization, on the other hand, focuses on the procedures and workflows within an organization.
It aims to create a consistent and efficient workflow by standardizing operational procedures.
Consistency in Operations
Process standardization ensures that every task within the organization is performed in a consistent manner.
Whether it’s onboarding new employees, manufacturing a product, or servicing customers, standardized processes ensure a uniform approach.
This leads to fewer errors, improved productivity, and a more cohesive workplace environment.
Streamlining Workflows
Efficient workflows are crucial for any organization aiming to optimize productivity.
Process standardization helps streamline operations by eliminating unnecessary steps and reducing waste.
This not only saves time but also makes it easier to scale operations without compromising quality.
Training and Onboarding
Training new employees can be time-consuming and costly.
With process standardization, the onboarding process becomes much simpler.
New recruits can quickly learn the ropes by following standardized procedures, making the transition smoother and reducing the learning curve.
The Key Differences
While both manufacturing and process standardization aim to improve efficiency and quality, they do so in different ways.
Focus on Products vs. Processes
Manufacturing standardization is primarily concerned with the end product.
Its main aim is to ensure that each unit produced meets specific quality standards.
In contrast, process standardization focuses on the methods and workflows used to achieve a goal.
It aims to create a uniform approach to tasks within the organization.
Impact on Quality
Both types of standardization impact quality, but in different ways.
Manufacturing standardization directly affects the quality of the product, ensuring uniformity and compliance with standards.
Process standardization, however, improves the quality of operations and workflows, leading to better overall organizational efficiency.
Implementation
Implementing manufacturing standardization often involves investing in specialized machinery, training personnel, and adhering to strict guidelines.
It can be a resource-intensive process.
On the other hand, process standardization is more about revising and optimizing existing workflows.
It requires less capital investment but a greater focus on documenting and refining procedures.
Benefits and Challenges
Each type of standardization has its own set of benefits and challenges.
Benefits of Manufacturing Standardization
1. **Consistent Quality** – Ensures that every product meets the desired quality standards.
2. **Reduced Waste** – Minimizes material and production waste.
3. **Enhanced Market Reach** – Meets international standards, making it easier to enter global markets.
Challenges of Manufacturing Standardization
1. **High Initial Cost** – Requires significant investment in machinery and training.
2. **Rigidity** – Can make it difficult to adapt to new technologies or methods.
Benefits of Process Standardization
1. **Improved Efficiency** – Streamlines operations and reduces inefficiencies.
2. **Simplified Training** – Makes it easier and quicker to train new employees.
3. **Scalability** – Facilitates scaling operations without compromising quality.
Challenges of Process Standardization
1. **Initial Resistance** – Employees may resist changes in established processes.
2. **Continuous Improvement** – Requires regular updates and improvements to remain effective.
Conclusion
While manufacturing standardization and process standardization may seem similar, they have distinct roles and benefits within an organization.
Manufacturing standardization focuses on creating uniform products that meet quality standards, while process standardization aims to streamline and improve operational workflows.
Both types of standardization are essential for achieving efficient, high-quality, and competitive operations in today’s demanding market.
Understanding the differences and benefits of each can help organizations implement effective strategies for long-term success.
資料ダウンロード
QCD調達購買管理クラウド「newji」は、調達購買部門で必要なQCD管理全てを備えた、現場特化型兼クラウド型の今世紀最高の購買管理システムとなります。
ユーザー登録
調達購買業務の効率化だけでなく、システムを導入することで、コスト削減や製品・資材のステータス可視化のほか、属人化していた購買情報の共有化による内部不正防止や統制にも役立ちます。
NEWJI DX
製造業に特化したデジタルトランスフォーメーション(DX)の実現を目指す請負開発型のコンサルティングサービスです。AI、iPaaS、および先端の技術を駆使して、製造プロセスの効率化、業務効率化、チームワーク強化、コスト削減、品質向上を実現します。このサービスは、製造業の課題を深く理解し、それに対する最適なデジタルソリューションを提供することで、企業が持続的な成長とイノベーションを達成できるようサポートします。
オンライン講座
製造業、主に購買・調達部門にお勤めの方々に向けた情報を配信しております。
新任の方やベテランの方、管理職を対象とした幅広いコンテンツをご用意しております。
お問い合わせ
コストダウンが利益に直結する術だと理解していても、なかなか前に進めることができない状況。そんな時は、newjiのコストダウン自動化機能で大きく利益貢献しよう!
(Β版非公開)