- お役立ち記事
- The difference between Manufacturing Tolerance and Design Tolerance
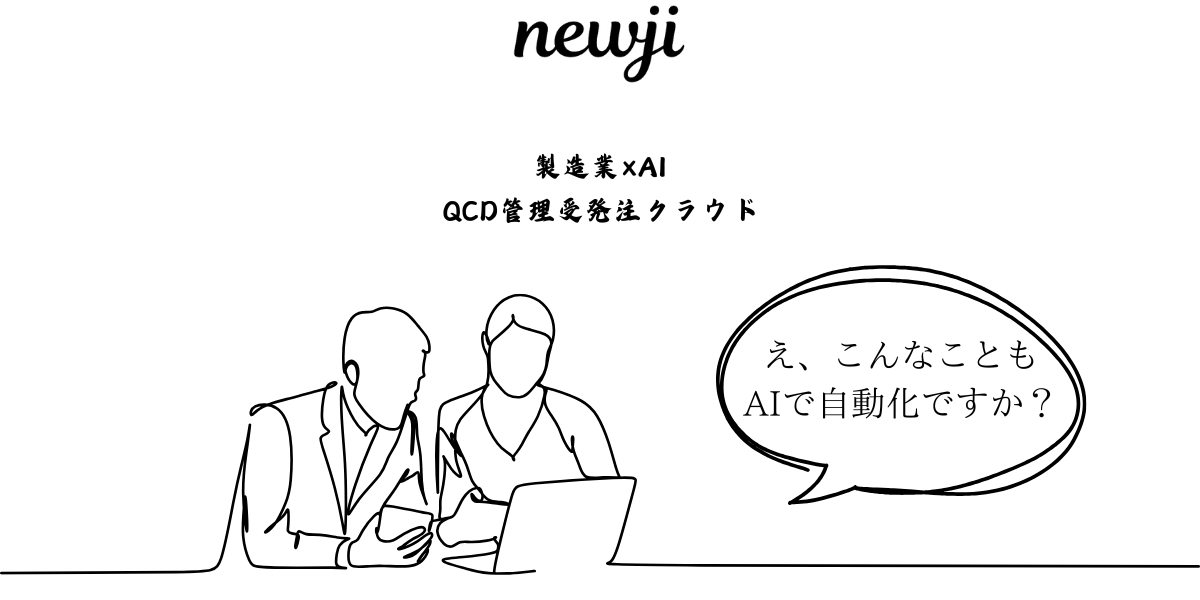
The difference between Manufacturing Tolerance and Design Tolerance
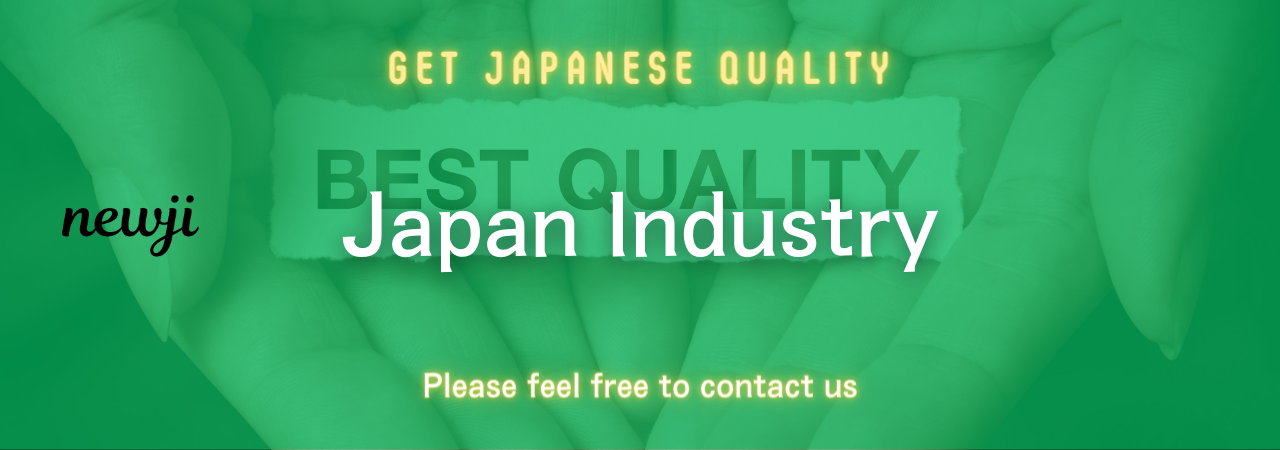
When it comes to the world of engineering, design, and manufacturing, understanding the nuances between different types of tolerances is crucial for creating high-quality products.
Two important types of tolerances are manufacturing tolerance and design tolerance.
While these terms might seem interchangeable, they serve distinct roles in the production process.
Here, we’ll dive into the differences between manufacturing tolerance and design tolerance to shed light on their significance and how they impact the manufacturing process.
目次
What is Manufacturing Tolerance?
Manufacturing tolerance refers to the allowable variation in dimensions or specifications that occur during the production process.
These variations can stem from the limitations of machinery, material properties, and human factors.
Manufacturing tolerance is essential because, in reality, achieving an exact dimension every time is virtually impossible.
For example, if you’re producing metal rods that need to be 10mm in diameter, manufacturing tolerance might allow for a slight variation, say between 9.9mm to 10.1mm.
This buffer ensures that the production process remains efficient and cost-effective without compromising the functionality of the product.
What is Design Tolerance?
Design tolerance, on the other hand, is established in the design phase of a product.
It represents the permissible limits of variation in the physical dimensions or performance characteristics, ensuring that the product can perform its intended function effectively.
Design tolerance considers the product’s end use, environmental factors, and how it will interact with other components.
In essence, design tolerance is about envisioning the final product and determining how much variation can be tolerated without affecting its performance or safety.
For instance, when designing a gearbox, an engineer needs to account for the interactions between gears, bearings, and other components.
The design tolerance will dictate how much variation is allowable in the dimensions of these parts to ensure smooth operation.
The Role of Tolerances in Manufacturing
Manufacturing and design tolerances play a vital role in ensuring that products meet quality standards and function correctly.
Here are some ways these tolerances impact the manufacturing process:
1. Quality Control
Tolerances are essential for quality control.
By specifying allowable variations, manufacturers can implement control measures to keep the production process within acceptable limits.
This helps reduce defects and ensures that products meet the required specifications.
2. Cost Management
Achieving perfect dimensions in every product would be extremely costly due to the high precision required.
Manufacturing tolerance allows for slight variations, reducing the need for expensive, high-precision machinery and minimizing material waste.
3. Interchangeability
Tolerances ensure that parts can be produced by different manufacturers and still fit together correctly.
This interchangeability is essential in industries like automotive and electronics, where components must be easily replaced or assembled from different sources.
4. Product Performance
Design tolerance ensures that the product can perform its intended function despite slight variations.
By accounting for potential variations, engineers can create products that are reliable and have consistent performance.
Key Differences Between Manufacturing and Design Tolerance
While both types of tolerance are interconnected, they have distinct characteristics and applications:
1. Origin Point
Manufacturing tolerance is determined during the production phase, based on the capabilities of machines and materials.
Design tolerance, however, is set during the design phase, considering how the product will be used and its interaction with other components.
2. Purpose
Manufacturing tolerance focuses on achieving efficient production and minimizing costs by allowing for slight variations.
Design tolerance, conversely, ensures that the product can function effectively despite these variations.
3. Flexibility
Manufacturing tolerance tends to be more flexible, allowing for deviations within acceptable limits based on production constraints.
Design tolerance is generally stricter, emphasizing the end product’s performance and safety.
4. Focus
Manufacturing tolerance is concerned with the dimensions and specifications during the production process.
Design tolerance looks at the final product’s functional requirements and overall performance.
The Relationship Between Manufacturing and Design Tolerance
Though different, manufacturing and design tolerances are deeply interconnected and must work in harmony for successful product development.
When setting design tolerances, engineers must be mindful of the limitations and capabilities of the manufacturing process.
Conversely, manufacturers need to understand the design tolerances to produce parts that meet the specified requirements.
Effective communication between design and manufacturing teams is crucial.
Miscommunication or misunderstanding can lead to products that do not meet the necessary standards or fail in the field.
Therefore, maintaining a collaborative environment helps bridge the gap between design tolerances and manufacturing capabilities.
Conclusion
In the intricate quilt of engineering and manufacturing, both manufacturing and design tolerance are indispensable threads.
They ensure that high-quality, reliable, and cost-effective products reach the market.
By distinguishing between these two types of tolerance, engineers and manufacturers can work together more effectively, leading to superior end products and satisfied customers.
Understanding their roles and differences ultimately helps in crafting designs that are feasible to manufacture and perform consistently in real-world applications.
資料ダウンロード
QCD調達購買管理クラウド「newji」は、調達購買部門で必要なQCD管理全てを備えた、現場特化型兼クラウド型の今世紀最高の購買管理システムとなります。
ユーザー登録
調達購買業務の効率化だけでなく、システムを導入することで、コスト削減や製品・資材のステータス可視化のほか、属人化していた購買情報の共有化による内部不正防止や統制にも役立ちます。
NEWJI DX
製造業に特化したデジタルトランスフォーメーション(DX)の実現を目指す請負開発型のコンサルティングサービスです。AI、iPaaS、および先端の技術を駆使して、製造プロセスの効率化、業務効率化、チームワーク強化、コスト削減、品質向上を実現します。このサービスは、製造業の課題を深く理解し、それに対する最適なデジタルソリューションを提供することで、企業が持続的な成長とイノベーションを達成できるようサポートします。
オンライン講座
製造業、主に購買・調達部門にお勤めの方々に向けた情報を配信しております。
新任の方やベテランの方、管理職を対象とした幅広いコンテンツをご用意しております。
お問い合わせ
コストダウンが利益に直結する術だと理解していても、なかなか前に進めることができない状況。そんな時は、newjiのコストダウン自動化機能で大きく利益貢献しよう!
(Β版非公開)