- お役立ち記事
- The difference between Manufacturing Work Order and Work Standard
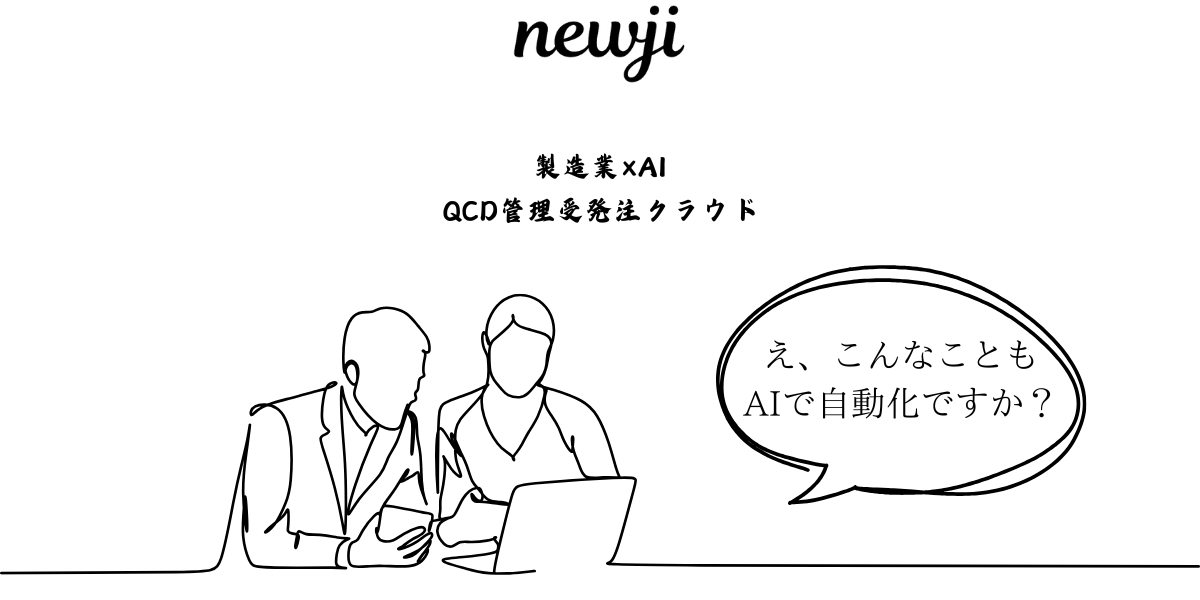
The difference between Manufacturing Work Order and Work Standard
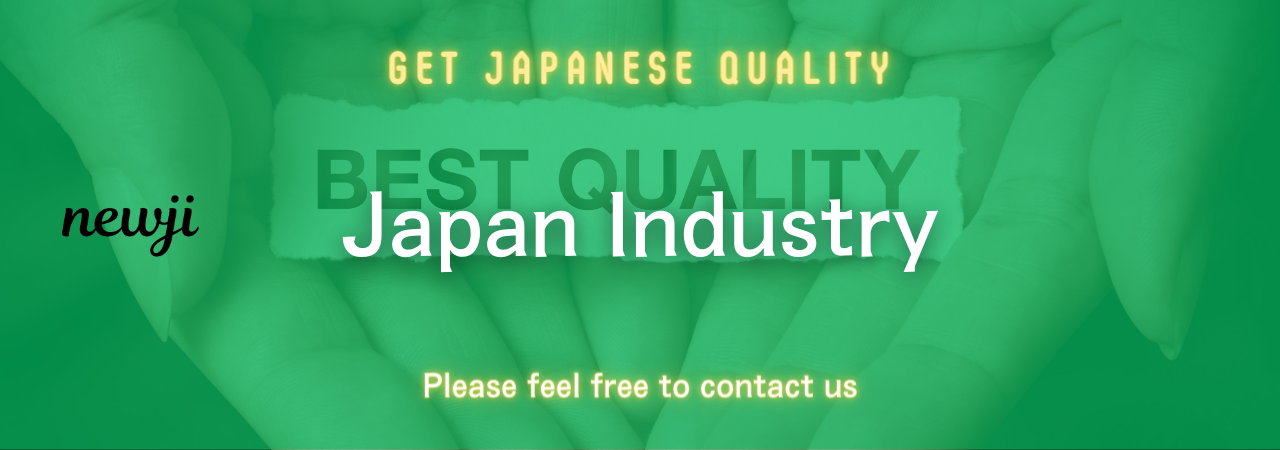
Understanding the nuances between a Manufacturing Work Order and a Work Standard is essential for anyone involved in production or manufacturing processes.
Both play crucial roles in ensuring efficient operations, maintaining quality, and boosting productivity.
Despite their interconnectedness, they serve distinct purposes and offer unique advantages.
Let’s delve deeper into this topic to clarify the differences and importance of each.
目次
What is a Manufacturing Work Order?
A Manufacturing Work Order is a detailed document or electronic record that stipulates the particular tasks, resources, and timelines needed to complete a specific item or product.
This document serves as a roadmap, guiding production teams on what needs to be done, using which materials, and by when.
Manufacturing Work Orders are integral in managing resources, scheduling, and tracking the progress of production runs.
Key Elements of a Manufacturing Work Order
Several critical components define a Manufacturing Work Order:
– **Order Number:** Unique identifier for tracking.
– **Product Details:** Specifications of the item to be produced.
– **Bill of Materials (BOM):** List of raw materials and components required.
– **Labor Requirements:** Information on workforce and skills needed.
– **Scheduling:** Start and end dates for production.
– **Quality Assurance:** Parameters and benchmarks to meet quality standards.
Manufacturing Work Orders are essential for ensuring that production runs smoothly and meets customer requirements and deadlines.
Benefits of Using Manufacturing Work Orders
Using Manufacturing Work Orders offers several advantages:
– **Efficiency:** Streamlines the production process by providing clear instructions and timelines.
– **Traceability:** Facilitates tracking and accountability through unique order numbers.
– **Resource Management:** Helps in managing inventory and labor effectively.
– **Quality Control:** Ensures that all necessary quality checks and standards are adhered to.
This document acts as the backbone of manufacturing operations, optimizing resources and minimizing waste.
What is a Work Standard?
A Work Standard, also referred to as a Standard Operating Procedure (SOP), is a set of detailed guidelines that describe how to perform a specific job or task within the manufacturing process.
Unlike Manufacturing Work Orders, Work Standards are not tied to individual production runs but serve as ongoing protocols for maintaining consistency and quality.
Key Elements of a Work Standard
Here are some fundamental aspects of a Work Standard:
– **Task Description:** Detailed steps for completing a particular task.
– **Tools and Equipment:** List of required tools and machinery.
– **Quality Criteria:** Benchmarks and tolerances to be maintained.
– **Safety Guidelines:** Instructions for ensuring workplace safety.
– **Training Requirements:** Skills and knowledge needed to perform the task.
Work Standards ensure that every team member knows how to perform their duties correctly and consistently.
Benefits of Implementing Work Standards
The advantages of adhering to Work Standards are manifold:
– **Consistency:** Ensures uniformity in how tasks are performed, leading to consistent quality.
– **Training Aid:** Serves as a training guide for new employees.
– **Safety:** Reduces the risk of accidents by providing clear safety instructions.
– **Efficiency:** Standardizes tasks, thereby reducing variability and improving efficiency.
Work Standards are essential for maintaining quality and operational efficiency in the long term.
Comparing Manufacturing Work Orders and Work Standards
While both Manufacturing Work Orders and Work Standards are vital to manufacturing, it’s essential to understand their differences.
Purpose
A Manufacturing Work Order focuses on the specifics of a particular production run.
It is a dynamic document that changes with each order.
In contrast, a Work Standard is a static set of guidelines to be followed consistently over time.
Scope
Manufacturing Work Orders are narrow in scope, concentrating on specific tasks for a given production run.
Work Standards are broader, providing protocols that apply to all instances of a given task.
Flexibility
Manufacturing Work Orders can be tailored to the unique requirements of each order.
Work Standards, however, are generally fixed and only updated when procedural changes are required.
Role in Quality Control
While both documents contribute to quality control, they do so differently.
Manufacturing Work Orders ensure that each production run meets specific quality benchmarks.
Meanwhile, Work Standards ensure that the methods and processes employed produce consistent quality over time.
Implementing Both for Optimal Results
For a manufacturing setup to achieve operational excellence, it is crucial to implement both Manufacturing Work Orders and Work Standards effectively.
Together, they provide a comprehensive framework for managing production, ensuring quality, and improving efficiency.
Real-World Application
In practice, Manufacturing Work Orders guide the day-to-day activities of production teams, dictating what needs to be done for each order.
Work Standards, on the other hand, serve as foundational protocols to ensure that each step is carried out correctly and consistently.
Together, they create a robust system that ensures high-quality output and operational efficiency.
Conclusion
Understanding the difference between a Manufacturing Work Order and a Work Standard is essential for anyone involved in production and manufacturing.
While a Manufacturing Work Order focuses on the specifics of a particular job, a Work Standard provides consistent guidelines for performing tasks.
Both are crucial for ensuring efficient, high-quality production.
By implementing both effectively, manufacturing operations can achieve optimal results, enhancing productivity and maintaining quality.
Whether you’re a seasoned professional or new to the field, grasping these concepts will undoubtedly contribute to your success in manufacturing.
資料ダウンロード
QCD調達購買管理クラウド「newji」は、調達購買部門で必要なQCD管理全てを備えた、現場特化型兼クラウド型の今世紀最高の購買管理システムとなります。
ユーザー登録
調達購買業務の効率化だけでなく、システムを導入することで、コスト削減や製品・資材のステータス可視化のほか、属人化していた購買情報の共有化による内部不正防止や統制にも役立ちます。
NEWJI DX
製造業に特化したデジタルトランスフォーメーション(DX)の実現を目指す請負開発型のコンサルティングサービスです。AI、iPaaS、および先端の技術を駆使して、製造プロセスの効率化、業務効率化、チームワーク強化、コスト削減、品質向上を実現します。このサービスは、製造業の課題を深く理解し、それに対する最適なデジタルソリューションを提供することで、企業が持続的な成長とイノベーションを達成できるようサポートします。
オンライン講座
製造業、主に購買・調達部門にお勤めの方々に向けた情報を配信しております。
新任の方やベテランの方、管理職を対象とした幅広いコンテンツをご用意しております。
お問い合わせ
コストダウンが利益に直結する術だと理解していても、なかなか前に進めることができない状況。そんな時は、newjiのコストダウン自動化機能で大きく利益貢献しよう!
(Β版非公開)