- お役立ち記事
- The difference between Material Cost Reduction and Manufacturing Cost Reduction
月間76,176名の
製造業ご担当者様が閲覧しています*
*2025年3月31日現在のGoogle Analyticsのデータより
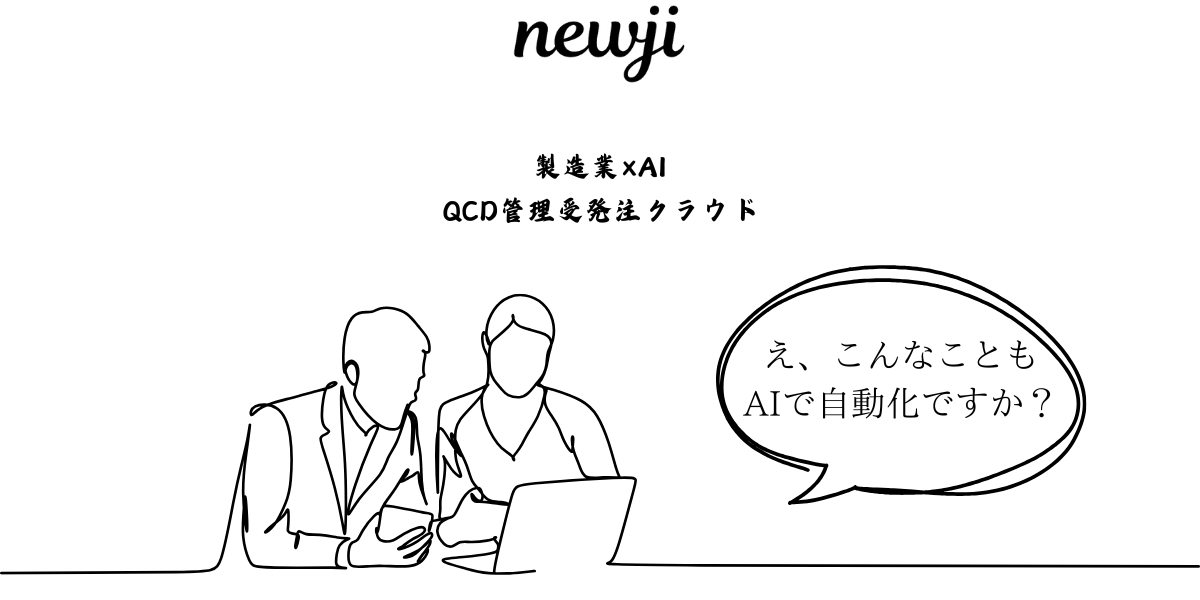
The difference between Material Cost Reduction and Manufacturing Cost Reduction
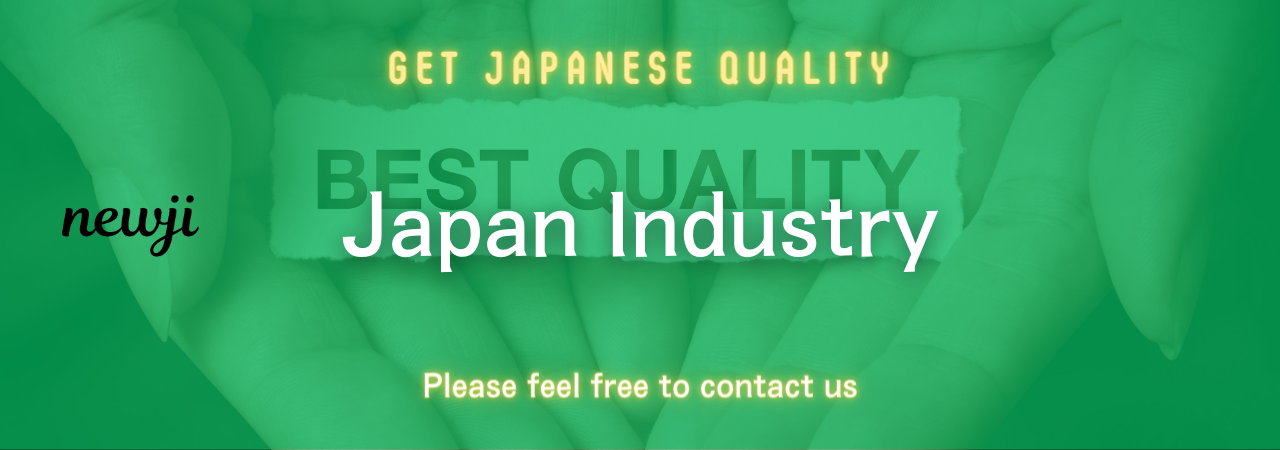
目次
Understanding Material Cost Reduction
Material cost reduction is a strategy aimed at decreasing the expenditure on raw materials used in the production process.
It can significantly impact a company’s overall profitability because materials often represent a considerable portion of total production costs.
Achieving material cost reduction requires a thorough analysis of the supply chain, negotiation with suppliers, and sometimes altering the materials sourced.
One common approach is to negotiate better prices with suppliers.
This can be achieved by securing bulk purchase discounts, establishing long-term contracts, or sourcing materials from lower-cost regions.
Another effective strategy is to seek alternative materials that provide the same quality at a reduced cost.
For example, a manufacturer might switch to a different type of plastic that is less expensive but still meets all quality standards.
Recycling and reusing materials also play a crucial role in material cost reduction.
By finding ways to repurpose waste or scrap materials, companies can effectively reduce the amount of new raw materials required.
Automation and technology integration in the procurement process help to monitor and manage material usage more efficiently, revealing further opportunities for savings.
Exploring Manufacturing Cost Reduction
Manufacturing cost reduction goes beyond just focusing on material costs.
It encompasses the entire production process, aiming to improve efficiency and reduce waste.
This holistic approach ensures that all aspects of production are optimized for cost-effectiveness.
One significant method for achieving manufacturing cost reduction is through process optimization.
Streamlining production processes, eliminating unnecessary steps, and improving workflow can lead to significant cost savings.
Lean manufacturing principles, such as reduced setup times and efficient inventory management, are commonly employed to achieve this.
Investing in advanced technologies and automation can also result in substantial manufacturing cost reductions.
Robotics, for instance, can speed up production lines, enhance precision, and reduce labor costs.
Similarly, adopting IoT (Internet of Things) solutions allows for real-time monitoring of production processes, helping identify and resolve inefficiencies promptly.
Energy consumption is another critical factor.
Implementing energy-efficient practices and using renewable energy sources can help reduce energy costs, which form a significant part of manufacturing expenses.
For example, switching to LED lighting, optimizing HVAC systems, and investing in energy-efficient machinery can lower electricity bills and overall energy consumption.
Key Differences between Material Cost Reduction and Manufacturing Cost Reduction
While both strategies aim to reduce costs and increase profitability, they focus on different aspects of the production process.
Focus Areas
Material cost reduction primarily targets the cost associated with raw materials.
It involves strategies like negotiating supplier contracts, finding alternative materials, and recycling waste.
Manufacturing cost reduction, on the other hand, takes a broader view.
It seeks to improve overall production efficiency, including labor, equipment, energy, and workflow.
Strategies Involved
The strategies for material cost reduction are often supply-chain focused.
These include supplier negotiations, bulk purchasing, and material substitution.
Manufacturing cost reduction strategies are process-focused.
They involve improving production efficiencies, integrating technologies, and optimizing energy usage.
Impact on Operations
Material cost reduction directly impacts the cost of goods sold (COGS) by decreasing the expenses related to raw materials.
Manufacturing cost reduction impacts overall operational efficiency, leading to savings across various production stages.
Optimizing manufacturing can result in reduced lead times, improved product quality, and lower labor costs.
Implementation Complexity
Material cost reduction can often be achieved through relatively direct actions such as supplier negotiation or material substitution.
However, manufacturing cost reduction usually requires a more comprehensive approach.
It may involve reengineering processes, significant capital investment in new technologies, and substantial changes in operational workflows.
In Summary
Understanding the distinction between material cost reduction and manufacturing cost reduction is essential for companies aiming to optimize their production costs.
While material cost reduction focuses on decreasing expenses related to raw materials, manufacturing cost reduction takes a holistic approach to improve efficiency and reduce waste throughout the entire production process.
Both strategies are crucial for improving profitability and should be tailored to a company’s specific needs and circumstances.
By effectively implementing these cost reduction methods, companies can achieve substantial savings, enhance their competitiveness, and ensure long-term sustainability.
資料ダウンロード
QCD管理受発注クラウド「newji」は、受発注部門で必要なQCD管理全てを備えた、現場特化型兼クラウド型の今世紀最高の受発注管理システムとなります。
ユーザー登録
受発注業務の効率化だけでなく、システムを導入することで、コスト削減や製品・資材のステータス可視化のほか、属人化していた受発注情報の共有化による内部不正防止や統制にも役立ちます。
NEWJI DX
製造業に特化したデジタルトランスフォーメーション(DX)の実現を目指す請負開発型のコンサルティングサービスです。AI、iPaaS、および先端の技術を駆使して、製造プロセスの効率化、業務効率化、チームワーク強化、コスト削減、品質向上を実現します。このサービスは、製造業の課題を深く理解し、それに対する最適なデジタルソリューションを提供することで、企業が持続的な成長とイノベーションを達成できるようサポートします。
製造業ニュース解説
製造業、主に購買・調達部門にお勤めの方々に向けた情報を配信しております。
新任の方やベテランの方、管理職を対象とした幅広いコンテンツをご用意しております。
お問い合わせ
コストダウンが利益に直結する術だと理解していても、なかなか前に進めることができない状況。そんな時は、newjiのコストダウン自動化機能で大きく利益貢献しよう!
(β版非公開)