- お役立ち記事
- The difference between Material Management and Material Control
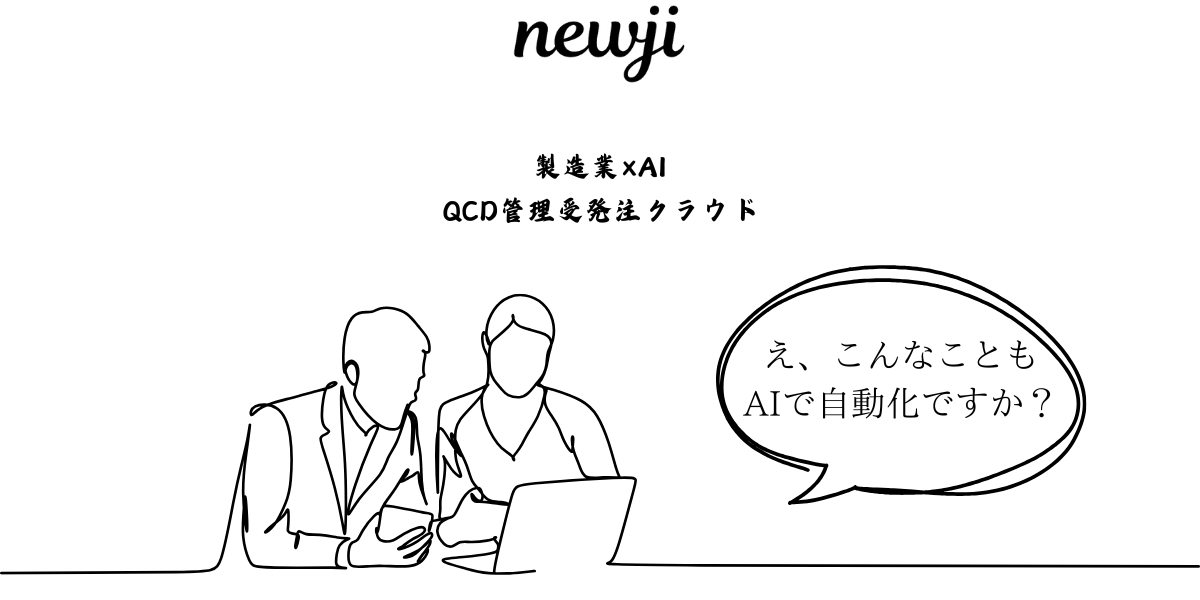
The difference between Material Management and Material Control
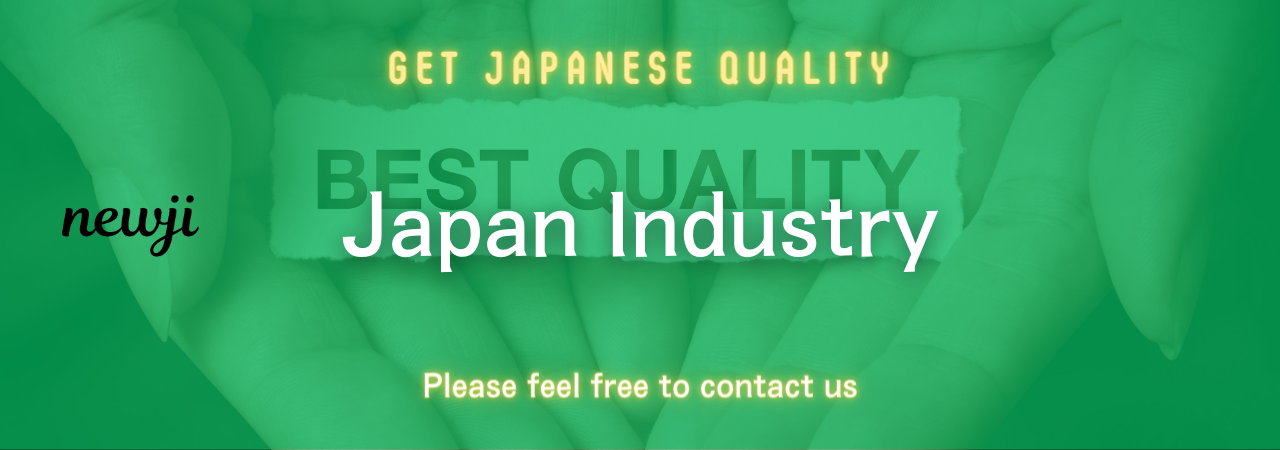
Understanding the concepts of material management and material control is crucial for anyone involved in industries such as manufacturing, construction, and logistics. Both play significant roles in ensuring seamless operations, but they serve different purposes and involve distinct processes. This article will elucidate the differences between material management and material control to help you grasp their unique functions and importance.
目次
What is Material Management?
Material management refers to the systematic approach to sourcing, storing, and utilizing raw materials in a way that meets the desired business objectives. It serves as a strategic function that ensures the right materials are available at the right time and place, reducing waste and maximizing efficiency.
Key Functions of Material Management
Sourcing and Procurement: One of the primary responsibilities of material management is to source raw materials from reliable suppliers. This often involves negotiating contracts, ensuring quality, and focusing on cost-efficiency.
Storage and Inventory Management: Proper storage and inventory management are essential to maintain the quality and availability of materials. This includes organizing warehouses, managing stock levels, and using software tools to monitor inventory in real-time.
Logistics and Transportation: Effective logistics and transportation play a vital role in ensuring that materials are moved efficiently between locations. This encompasses planning routes, choosing the right transportation modes, and ensuring timely deliveries.
Demand Forecasting: Predicting the future requirement for materials helps in avoiding overstocking or understocking. Demand forecasting utilizes historical data, market trends, and analytical tools to predict future needs accurately.
Benefits of Effective Material Management
Cost Savings: Efficient material management can lead to significant cost savings by reducing waste, minimizing holding costs, and optimizing procurement.
Operational Efficiency: With the right materials in stock, operations can proceed without interruptions, ensuring timely project completion.
Improved Supplier Relationships: Effective material management fosters better relationships with suppliers through timely payments, repeat business, and mutually beneficial contracts.
Quality Assurance: Proper storage and handling ensure materials maintain their quality, contributing to the overall excellence of the final product.
What is Material Control?
Material control, on the other hand, is a subset of material management that focuses specifically on the monitoring and regulation of materials as they move through different stages of production. It ensures that materials are used efficiently and that waste is minimized.
Key Functions of Material Control
Monitoring: Keeping track of materials as they move from storage to the production line and through various stages of manufacturing. This ensures that materials are where they need to be when they are needed.
Regulating Usage: Ensuring that materials are used as intended and not wasted. This involves setting guidelines for material consumption and monitoring adherence to those guidelines.
Reporting: Generating reports on material usage, wastage, and inventory levels to inform decision-makers and help in planning future material requirements.
Quality Control: Ensuring that only the highest quality materials are used in the production process. This involves inspecting materials and rejecting any that do not meet quality standards.
Benefits of Effective Material Control
Reduced Waste: By monitoring and regulating the use of materials, waste can be significantly reduced, leading to cost savings and more efficient production processes.
Inventory Accuracy: Accurate tracking of materials ensures that inventory levels are always up to date, which helps in planning and decision-making.
Enhanced Product Quality: By ensuring that only high-quality materials are used, material control contributes to the production of superior products.
Improved Compliance: Adhering to guidelines and regulations in material usage ensures compliance with industry standards and legal requirements.
Key Differences Between Material Management and Material Control
While material management and material control are closely related, they serve distinct functions within an organization:
Focus: Material management has a broader focus, encompassing sourcing, storage, logistics, and inventory management. Material control, however, is more narrowly focused on monitoring and regulating the use of materials.
Scope: Material management involves long-term planning and strategic decision-making. Material control is more concerned with day-to-day operations and tactical execution.
Objectives: The primary objective of material management is to ensure that materials are available when needed, while the primary objective of material control is to ensure that materials are used efficiently with minimal waste.
Tools and Techniques: Material management often involves the use of sophisticated software for demand forecasting, procurement, and inventory management. Material control relies more on monitoring tools and techniques for tracking and regulating material usage.
Interdependence Between the Two
While material management and material control have different focuses and objectives, they are interdependent and work together to ensure the smooth operation of an organization.
Effective material management provides the foundation for material control by ensuring that the right materials are available when needed.
Conversely, effective material control ensures that the materials provided through material management are used efficiently and with minimal waste.
Together, they help an organization achieve its operational goals, improve efficiency, and reduce costs.
Conclusion
Understanding the differences between material management and material control is essential for optimizing operations, reducing costs, and improving efficiency in any industry reliant on raw materials.
While material management focuses on sourcing, storage, and logistics, material control zeroes in on the monitoring and regulation of materials through the production process.
Both are crucial and interdependent, working together to ensure seamless operations and the achievement of organizational goals.
By grasping these concepts, businesses can better manage their resources, enhance their productivity, and maintain a competitive edge in the market.
資料ダウンロード
QCD調達購買管理クラウド「newji」は、調達購買部門で必要なQCD管理全てを備えた、現場特化型兼クラウド型の今世紀最高の購買管理システムとなります。
ユーザー登録
調達購買業務の効率化だけでなく、システムを導入することで、コスト削減や製品・資材のステータス可視化のほか、属人化していた購買情報の共有化による内部不正防止や統制にも役立ちます。
NEWJI DX
製造業に特化したデジタルトランスフォーメーション(DX)の実現を目指す請負開発型のコンサルティングサービスです。AI、iPaaS、および先端の技術を駆使して、製造プロセスの効率化、業務効率化、チームワーク強化、コスト削減、品質向上を実現します。このサービスは、製造業の課題を深く理解し、それに対する最適なデジタルソリューションを提供することで、企業が持続的な成長とイノベーションを達成できるようサポートします。
オンライン講座
製造業、主に購買・調達部門にお勤めの方々に向けた情報を配信しております。
新任の方やベテランの方、管理職を対象とした幅広いコンテンツをご用意しております。
お問い合わせ
コストダウンが利益に直結する術だと理解していても、なかなか前に進めることができない状況。そんな時は、newjiのコストダウン自動化機能で大きく利益貢献しよう!
(Β版非公開)